- FMA
- The Fabricator
- FABTECH
- Canadian Metalworking
Categories
- Additive Manufacturing
- Aluminum Welding
- Arc Welding
- Assembly and Joining
- Automation and Robotics
- Bending and Forming
- Consumables
- Cutting and Weld Prep
- Electric Vehicles
- En Español
- Finishing
- Hydroforming
- Laser Cutting
- Laser Welding
- Machining
- Manufacturing Software
- Materials Handling
- Metals/Materials
- Oxyfuel Cutting
- Plasma Cutting
- Power Tools
- Punching and Other Holemaking
- Roll Forming
- Safety
- Sawing
- Shearing
- Shop Management
- Testing and Measuring
- Tube and Pipe Fabrication
- Tube and Pipe Production
- Waterjet Cutting
Industry Directory
Webcasts
Podcasts
FAB 40
Advertise
Subscribe
Account Login
Search
How to avoid post-pandemic manufacturing supply chain pitfalls
Using manufacturing ERP software to rise above the disruptions
- June 10, 2022
- Article
- Manufacturing Software
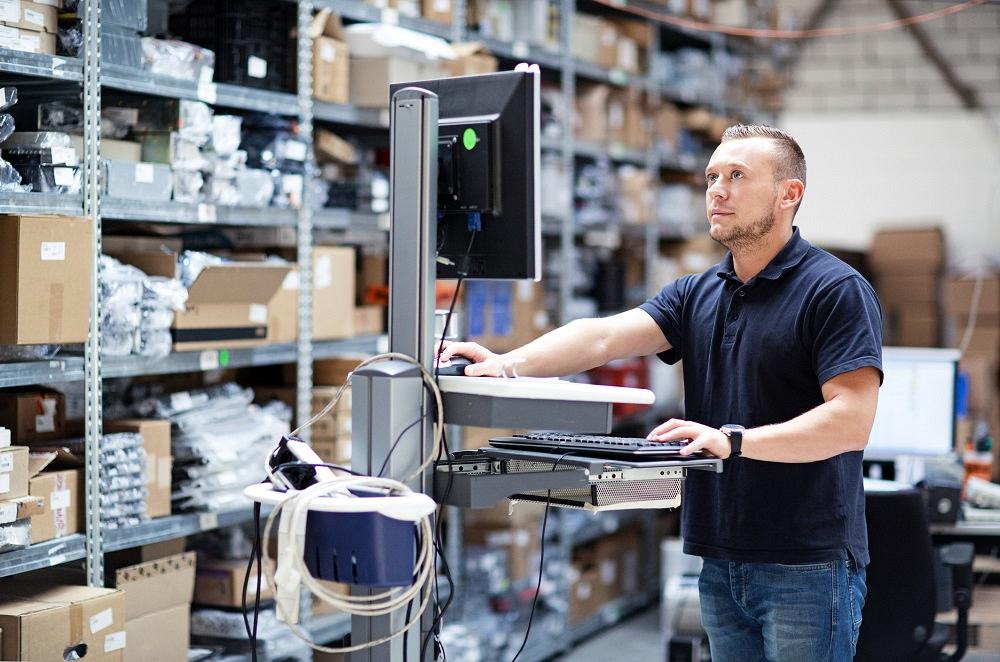
Without an automated ERP option, manufacturers can pay too much, procure too much or too little, or order too soon or too late.
The COVID-19 pandemic may be considered the most disruptive event in modern supply chain history, causing 4,200 disruptions in the first nine months of 2020, according to Resilinc’s Eventwatch risk monitoring system. Disruptions resulted from the combination of viral outbreaks among workers and subsequent labor shortages, layoffs, furloughs, turnover, factory shutdowns, and production cuts in the supply chain. Now, mid-2022, the global supply chain is still reeling from the cascading effects of the massive disruption with scarcities in raw materials, extended manufacturing lead times, rationing, shipping delays, and retail outages.
Building in resilience is key to sustainable supply chain continuity going forward. McKinsey research reveals that companies now can expect disruptions lasting a month or longer to occur every 3.7 years on average. That may be a conservative projection, as some of the major causes of supply chain disruptions including natural disasters, political uncertainty, and cyberattacks appear to be increasingly likely. While the pandemic is still impacting the supply chain, it is imperative that manufacturers strengthen and automate their supply chains and inventory management practices.
Manufacturers must avoid the major supply chain management pitfalls. Fortunately there are best practices for doing so using innovative manufacturing enterprise resource planning (ERP) software.
PITFALL NO. 1: Manual Purchasing
Manual purchasing is compromised, flawed purchasing. Without an automated ERP option, manufacturers can pay too much, procure too much or too little, or order too soon or too late. Poor visibility into suppliers’ inventory and lack of supplier diversification are leading causes of low supply chain resilience.
These weaknesses are revealed when disruptions occur. A company can rely on too few suppliers, including some that are short-staffed or use a limited number of raw materials suppliers themselves. When suppliers don’t have contingency plans, their problems become manufacturers’ problems. But manufacturers can do something to prevent that failure from occurring.
The solution: Purchasing activity monitoring, alerts. A manufacturing ERP system improves the accuracy of demand forecasting based on historical trends. It keeps a manufacturing business organized as it integrates more suppliers and diversifies its supply base for improved resilience. One of the keys is in sourcing and working with local suppliers. Less distance between a business and its suppliers decreases risks during disruptions.
Working with a geographically dispersed group of diverse suppliers and carriers provides flexibility when any supplier is affected. Intelligent software applications either automate or streamline the selection of the right suppliers at the right times, steering clear of unnecessary risks. Is a supplier in a pandemic hot spot, a war zone, or near a natural disaster? If yes, divert automatically to a supplier that isn’t at risk.
Many ERP systems also enable data monitoring and collection of the history of conditions that affect specific suppliers. When an event, such as a snowstorm, adversely impacts a supplier, the right ERP system can provide timely alerts to switch suppliers. This improves supply forecasting accuracy and helps determine which suppliers and carriers can best meet budgets and deadlines.
Visibility and insights into suppliers’ performance over time provides continual, incremental improvement, which is the main key to reducing the impact of disruptions and increasing supply chain resilience.
Similarly, ERP systems monitor and integrate changes to a job directly with suppliers so that if job specifications change, it’s easy to get the best choices for the right suppliers and switch on the fly.
PITFALL NO. 2: Wasteful Inventory Stocking
Many manufacturers and job shops tie up cash with wasteful inventory stocking, while some do not carry enough and get caught shorthanded in production. Seat-of-the-pants replenishment is just as common as overstocking. This means reacting to inventory depletion by reordering to meet expected demand. Because this is not a data-driven inventory management practice using inventory management software, it is not cost-effective and often leads to production disruptions.
Wasteful inventory practices also include inventory record inaccuracies stemming from physical counts and disconnected systems. For example, parts stocked on fleet trucks are often documented inaccurately. Inefficient storage and receipt processes are another cause of costly mistakes, including trouble accessing products and over-ordering.
Finally, stock disorganization and poor labeling and picking practices also are culprits for costly inventory management mistakes. In cost-effective inventory operations, items are always documented, available when needed (and not too soon), and are accessible quickly.
The solution: Inventory management software. These challenges all can be addressed with inventory management software that standardizes just-in-time (JIT) practices and inventory operations documentation. As part of an ERP system, this software offers real-time inventory data that populates across inventory and all business modules. When an item is used, that information is immediately accessible to everyone in the operation.
Inventory management software includes multibin and multilocation tracking, cycle counting, and supply and demand analysis tools. JIT forecasting tools are built in for raw materials as well as purchased and manufactured parts, so that the fabricator doesn’t tie up cash unnecessarily. These systems include multilevel bill of materials (BOM) assembly system and material requirements planning (MRP) tools. Multilevel BOM systems include SKUs, part descriptions, quantities, costs, and other specifications for complex builds. MRP enables manufacturers to cost-effectively plan, schedule, and manage all inventory throughout the manufacturing process.
PITFALL NO. 3: Inefficient Physical Inventory Audits
A recent warehouse management survey found that 82% of respondents complete scheduled physical inventory counts, 46% do spot checking, 22% do cycle counting of specific products on a rotating basis, and 19% do full physical counts when a problem is discovered.
Without software that provides efficient physical inventory audit processes and documentation, all of that time-consuming, expensive work must be performed more often to maintain accuracy. Physical counts can’t be trusted without reliable methods for keeping them up to date. Disconnected spreadsheets and poorly designed picking and labeling systems cause confusion about where parts and supplies are stored.
The solution: Stock visibility. ERP systems with inventory management software reduce operating costs caused by inefficient manual processes, including physical inventory audits. Manufacturers that start using this software see immediate results in terms of maximized warehouse space and accurate inventory counts. Accurate labeling and real-time tracking on inventory levels, schedules, demand, and forecasting integrates with every aspect of the business’ supply chain management practices and ensures efficiency through transparency.
PITFALL NO. 4: Lack of Cross-departmental Visibility and Integration
Planning in silos, even when best practices are implemented in each department, results in disparate data systems, inaccurate information, and miscommunications. For example, when an e-commerce platform doesn’t communicate with inventory management software, a customer may expect to receive an order by a certain date but instead receives an email saying the item is out of stock and will have to be backordered, when it actually is available.
Cross-departmental integration and visibility are also essential to documentation for regulatory and compliance records in many manufacturing sectors.
The solution: Software that provides a single source of data. ERP software is one integrated source of real-time data that provides a consolidated view of the supply chain and transparency across the business. ERP delivers cost-effective, efficient planning and scheduling based on accurate, real-time data. Streamlined invoicing and workflows with full data visibility ensure strong supply chain management, regardless of external disruptive forces. The most effective leaders across manufacturing sectors depend on a single source of data with powerful reporting functions and dashboard monitoring to steer their ships clear of any potential trouble ahead.
Manufacturing-specific ERP software takes these potential pitfalls and turns them into opportunities with efficient purchase management, better inventory tracking, less manual work, and increased visibility. With ERP software, leaders are equipped to make the right decisions at the right times to increase productivity, profitability, and customer satisfaction.
ECI Software Solutions Inc., 4400 Alliance Gateway Freeway, Suite 154, Fort Worth, TX 76177
subscribe now
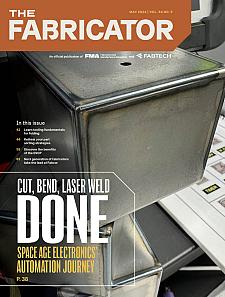
The Fabricator is North America's leading magazine for the metal forming and fabricating industry. The magazine delivers the news, technical articles, and case histories that enable fabricators to do their jobs more efficiently. The Fabricator has served the industry since 1970.
start your free subscription- Stay connected from anywhere
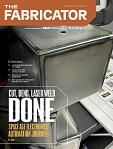
Easily access valuable industry resources now with full access to the digital edition of The Fabricator.
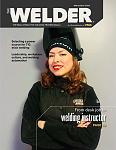
Easily access valuable industry resources now with full access to the digital edition of The Welder.
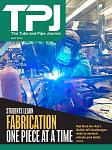
Easily access valuable industry resources now with full access to the digital edition of The Tube and Pipe Journal.
- Podcasting
- Podcast:
- The Fabricator Podcast
- Published:
- 04/16/2024
- Running Time:
- 63:29
In this episode of The Fabricator Podcast, Caleb Chamberlain, co-founder and CEO of OSH Cut, discusses his company’s...
- Trending Articles
Tips for creating sheet metal tubes with perforations
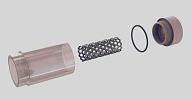
JM Steel triples capacity for solar energy projects at Pennsylvania facility
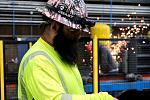
Are two heads better than one in fiber laser cutting?
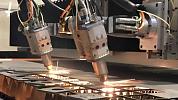
Supporting the metal fabricating industry through FMA
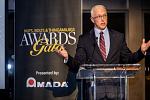
Omco Solar opens second Alabama manufacturing facility
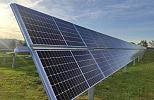
- Industry Events
16th Annual Safety Conference
- April 30 - May 1, 2024
- Elgin,
Pipe and Tube Conference
- May 21 - 22, 2024
- Omaha, NE
World-Class Roll Forming Workshop
- June 5 - 6, 2024
- Louisville, KY
Advanced Laser Application Workshop
- June 25 - 27, 2024
- Novi, MI