Senior Editor
- FMA
- The Fabricator
- FABTECH
- Canadian Metalworking
Categories
- Additive Manufacturing
- Aluminum Welding
- Arc Welding
- Assembly and Joining
- Automation and Robotics
- Bending and Forming
- Consumables
- Cutting and Weld Prep
- Electric Vehicles
- En Español
- Finishing
- Hydroforming
- Laser Cutting
- Laser Welding
- Machining
- Manufacturing Software
- Materials Handling
- Metals/Materials
- Oxyfuel Cutting
- Plasma Cutting
- Power Tools
- Punching and Other Holemaking
- Roll Forming
- Safety
- Sawing
- Shearing
- Shop Management
- Testing and Measuring
- Tube and Pipe Fabrication
- Tube and Pipe Production
- Waterjet Cutting
Industry Directory
Webcasts
Podcasts
FAB 40
Advertise
Subscribe
Account Login
Search
New York manufacturer starts its Industrial Internet of Things (IIoT) journey
Uncovering the true value of machine data for a diversified contract manufacturer
- By Tim Heston
- October 18, 2022
- Article
- Manufacturing Software
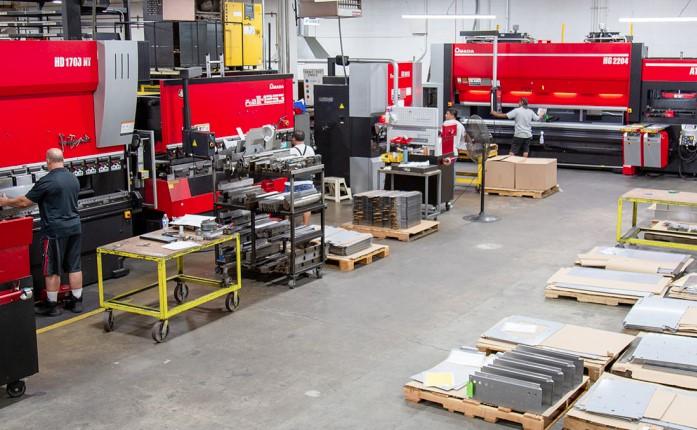
Allen Machine Products’ forming department recently added an automatic tool change (ATC) press brake. The flexibility of automated tool change might be a harbinger of what will be possible in the connected shop.
Walk the shop floor at Allen Machine Products (AMP) and you’ll see the gamut of metal manufacturing automation. Material moves from a cassette in a storage tower, onto a 4-kW laser cutting system, then delivers a cut nest of disparate parts out to an offloading station.
A press brake changes its tools automatically, and the operator is ready to run the next job within minutes. Walk up the street to the machine shop and you’ll see a 10-pallet machining center processing a multitude of tombstones, each fixtured with a variety of parts. The whole place shows just how flexible automation has become.
“We’re always looking for new equipment, innovative equipment, equipment that will produce the same results time and time again, which is so important. In doing so, we want to remove cost and wasted movement. For us, automation isn’t about eliminating anybody. It’s about retooling that person for another job so they can be more productive for the company and more successful for themselves.”
So said Eric Lazarus, managing director at AMP, a diverse contract manufacturer in Hauppauge, N.Y. For the past decade, the 70-plus-employee operation has embraced machine automation, with major customers in medical equipment, transportation, food service, homeland security, semiconductor, emerging technologies, and a variety of other industries. Now, Lazarus, along with Rich Pettenato, AMP’s vice president of operations, and other company leaders are ready to take automation to the next step, tapping directly into machines to mine data, schedule strategically, optimize quoting, and better serve a growing customer base. In other words, they’re looking to build a connected shop.
The Little Things
Workers arrive on a Saturday to finish a job only to find they were out of gas—specifically, cutting and welding gases. “All our industrial gases are in huge tanks outside,” Lazarus said. “And on occasion, we’d have a crew show up on Saturday, and all of sudden we find that someone runs out of gas. What happened? Someone forgot to order. The gas delivery’s coming in on Monday!”
Today, AMP automates its gas delivery; telemetry on the gas cylinders themselves communicate with the suppliers to replenish. “We don’t have to worry about it now.”
That improvement was an early step in the “data journey” that AMP has traveled over the past decade, analyzing the workflow over the entire shop, from initial quote to final shipment. Someone leaves his or her workstation to find a tool. Two minutes gone. Someone loses an email about a last-minute customer request. The scrambling ensues. An emailed quote falls into a customer’s spam folder, and the shop never wins the job. Opportunity lost.
Each incident in isolation doesn’t ring alarm bells. So what if an operator left his machine for a minute or two? Someone missed an email? That happens all the time, so what’s the big deal? It’s to be expected in a company juggling thousands of different part numbers for dozens of customers across various industries. It’s the nature of the custom metal fabrication beast.
But does it have to be? That, Lazarus said, is what AMP sought to find out several years ago when it started scrutinizing and enhancing the way information flowed throughout the organization.
Turn on a Dime
Lazarus pointed to one of the company’s most recent purchases, an AMADA automatic tool change (ATC) press brake. “Some of our more complex jobs used to take hours to set up, and because those setups took so long, we wanted to run as many pieces as we could. Often, that would be a year’s worth of product for a customer. The ATC changed that.”
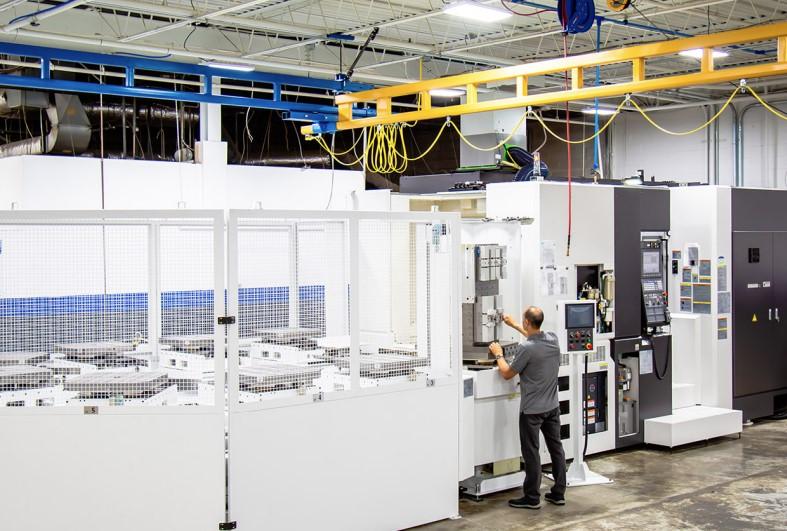
The company’s 10-pallet machining center can be set up to run kit-based production, with multiple families of parts being machined and then transported to assembly at just the right time.
AMP is still a high-mix, low-volume operation, so a year’s worth of product didn’t represent a massive number of parts. Still, customers didn’t want to hold inventory; they wanted everything just-in-time. And with the ATC, AMP now can align its production with customer demand. “Even with these complicated setups, it’s good to go within minutes,” Lazarus said. “And if we have some kind of variation, such as in material thickness, it has a [digital caliper] that connects right to the controller. The operator measures the part, and the machine makes adjustments.”
Lazarus and his team effectively want to take this kind of flexibility—change direction on a dime and produce quickly—to the entire organization. “We need data in real-time, especially in today’s market when you’re trying to decide how much material should come in, and when we will be ready for it. We want to reduce inventories as much as possible, but at the same time never put our customers in jeopardy by not providing what they need when they need it.”
The fabricator’s data transformation has three pieces: enterprise resource planning (ERP), streamlined quoting, and connected machinery. The first two pieces are in place, and the last is just over the horizon.
Quoting and ERP
A formed part arrives at the hardware insertion press. The operator reads the traveler, then looks for the hardware—and finds it missing. Lazarus shook his head and laughed, proclaiming as he raised his hands, “How can you not have the right hardware? Well someone thought it was ordered for the job, but it wasn’t.”
He added that delays caused by that missing hardware (and any missing component that should have been ordered earlier) can be just as serious as delays from a down machine or lengthy machine setup. A laser might have stellar green-light-on time, but customers couldn’t care less about machine uptime if their parts are still delivered late.
Today, because of streamlined quoting and an expansive ERP platform, that kind of delay doesn’t happen anymore at AMP. Before beginning the job, the insertion operator scans a bag of hardware, which sends information directly to the shop’s ECI JobBOSS ERP platform. In fact, the company’s quoting platform, Paperless Parts, integrates with ERP, communicating that, yes, the job requires a certain number of specific hardware, and ensures the hardware is ordered and available.
The quoting platform also uses current material pricing and updates quotes as necessary (a necessity in today’s volatile material pricing environment). It also sends notifications once customers open and view a quote online, avoiding those lost opportunities from email caught in spam.
Quality is another area AMP streamlined. The shop connects its Unipoint quality software (which QA techs use to input inspection reports) with its JobBOSS ERP. The ERP also integrates material certifications for the jobs that require it and allows operators to add notes about the idiosyncrasies of specific setups. “Everything is right there for everyone to see,” Lazarus said, “the drawings, images of parts we made previously, and notes about stumbling blocks to avoid.
“What drives me crazy,” Lazarus continued, “isn’t that a mistake is made. Mistakes are going to happen. It’s when the mistake is repeated. When we bring all the data right to the operator on the floor, he knows how to prevent the mistake from happening again.”
Connecting Machinery
At this writing, AMP has connected its quoting and quality platforms to its ERP. Now it’s looking to connect the machines themselves. Note that the company’s current ERP platform has a job tracking function, but it relies on workers manually clocking in and out of jobs. The company is looking to automate this function and, most critically, tie in the tracking with the actual movements of the machine, be it the moving ram of a press brake or the rotating spindle of a machining center.
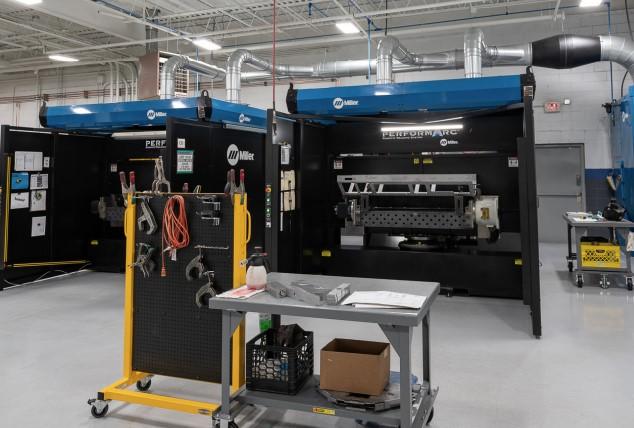
Two welding cells sit adjacent to mobile carts, with tools needed to simplify and streamline job changeovers.
The idea is to detect those minor stoppages that pass under the radar. Operators might need to retrieve a tool for a certain job, so they walk to the other side of the plant to get it. They return, process the work, then clock out of the job to notify the material handler that it’s ready to be sent downstream. The operator actually finished the job in less than the time allotted, so all is well—right? Not necessarily.
In fact, that minor stoppage might contribute to lost opportunity. What if the tool could be moved closer to the work cell? Would it be worth it to buy another tool? Could the job be processed anywhere else more efficiently? The idea is to track not only machine-on time but also setup time, and also to relate that data to specific jobs. Knowing how setup times vary—from operator to operator and job to job—helps reveal operational variabilities and areas for improvement.
Lazarus emphasized that the goal isn’t to push employees harder. “We want them to work at a sustainable, steady pace,” he said. “That’s the best way to get quality parts.”
He added that getting data directly from the machine also could reveal problems that operators might just see as part of the job. “For instance, say a machine runs for two hours, but then for the final two hours, the cycle times slow.”
That’s natural, of course; operators get tired, especially if they’re manually lifting and processing work. But seeing when operators slow down, and during which jobs, could give valuable insight into resource management. Does that operator need to work with that machine four hours straight? Could he alternate with another operator? What jobs are particularly challenging, and why? Machine data could reveal ways to make an operator’s life on the floor easier.
He added that machine data is arguably more important in a high-product-mix operation like AMP. A high-volume environment can learn a lot from time studies and worker observation, considering just how repetitive their jobs are. People at AMP do make common-sense improvements, of course, but it’s also difficult to see the true implications of minor stoppages in a shop that’s producing thousands of different parts. The work isn’t repetitive, patterns are more difficult to see, and improvements might be less intuitive. Machine data could reveal those hidden inefficiencies.
Data right from the machine also could help optimize scheduling and sequencing, especially in an environment as diverse as AMP, where a good portion of products involve both machining and sheet metal. Lazarus described how the company uses its 10-pallet horizontal machining center (HMC) to run broad families of parts.
“Because we have 10 pallets, we could have 10 tombstones set up, each with different fixtures to run families of parts. So, when we assemble products, we ensure that we give assemblers all the parts they need quickly. If we have a 75-piece run of a six-part assembly, we don’t want to run batches of 75 for each part.” The automated HMC allows the company to run kit-based production, so units flow to assembly at just the right time. The same holds true on the sheet metal side of the business. A variety of parts can flow through the AMADA laser and press brakes, including the ATC, all sequenced to arrive in assembly at just the right time.
With granular data directly from the machine, managers could fine-tune this flow. A change on the machining side would be known immediately on the sheet metal side, and adjustments could be made accordingly, all in a quest for better flow and minimal work-in-process (WIP).
“We want as many inventory turns as possible,” Lazarus said. “We want to minimize our carrying costs and our WIP, while at the same time have enough stock for our customers.”
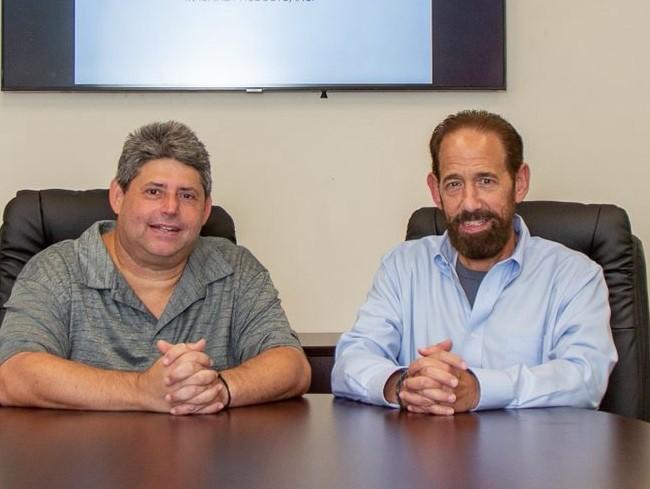
(From Left) AMP President Rich Pettenato and Eric Lazarus began investing IIoT technologies earlier this year. Their journey has just begun.
The Importance of Connection
AMP has started down the road toward the Industrial Internet of Things (IIoT). The essence of this (admittedly overused) buzzword is connection—connected machines, ERP, quoting, and quality. Further down the road, Lazarus and his team have ideas about connecting suppliers, outside service providers, and customers.
For now, the company is working out the details, uncovering how machine data collection can connect to machines of different brands and ages, and how it all can connect with the company’s ERP platform. “We’re walking through the important questions,” Lazarus said. “What kind of data can we get from different machines? Is it just green-light-on time, or is the data actually telling you what parts are running and how many parts are coming off the machine? The better data we get, them more efficiently we can run our operations.”
Lazarus pointed again to the ATC press brake. The operator was in the middle of a setup, and racks of punches and dies were moving swiftly into place. He was loading a job that hadn’t been run before, but it had been programmed and simulated offline. The operator ran a batch of a few dozen, then jumped to yet another job. The sequence allowed jobs to flow downstream so they reached assembly in the exact order they were needed, with no excess inventory.
Before the ATC and offline bend simulation, such a changeover would have been impossible. Lazarus carried the same concept to machine data and IIoT. Without data, just imagine trying to optimize disparate operations—laser cutting, bending, welding, machining—for every one of the thousands of jobs that flow through the shop. The transformation won’t happen overnight, but eventually, IIoT could make it happen.
About the Author
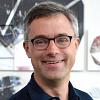
Tim Heston
2135 Point Blvd
Elgin, IL 60123
815-381-1314
Tim Heston, The Fabricator's senior editor, has covered the metal fabrication industry since 1998, starting his career at the American Welding Society's Welding Journal. Since then he has covered the full range of metal fabrication processes, from stamping, bending, and cutting to grinding and polishing. He joined The Fabricator's staff in October 2007.
subscribe now
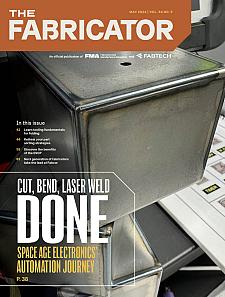
The Fabricator is North America's leading magazine for the metal forming and fabricating industry. The magazine delivers the news, technical articles, and case histories that enable fabricators to do their jobs more efficiently. The Fabricator has served the industry since 1970.
start your free subscription- Stay connected from anywhere
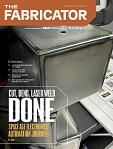
Easily access valuable industry resources now with full access to the digital edition of The Fabricator.
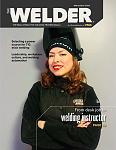
Easily access valuable industry resources now with full access to the digital edition of The Welder.
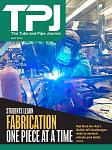
Easily access valuable industry resources now with full access to the digital edition of The Tube and Pipe Journal.
- Podcasting
- Podcast:
- The Fabricator Podcast
- Published:
- 04/16/2024
- Running Time:
- 63:29
In this episode of The Fabricator Podcast, Caleb Chamberlain, co-founder and CEO of OSH Cut, discusses his company’s...
- Trending Articles
Tips for creating sheet metal tubes with perforations
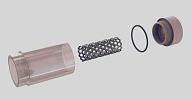
JM Steel triples capacity for solar energy projects at Pennsylvania facility
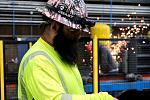
Are two heads better than one in fiber laser cutting?
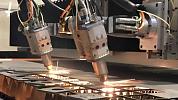
Supporting the metal fabricating industry through FMA
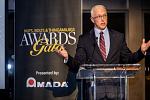
Omco Solar opens second Alabama manufacturing facility
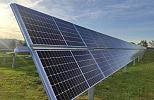
- Industry Events
16th Annual Safety Conference
- April 30 - May 1, 2024
- Elgin,
Pipe and Tube Conference
- May 21 - 22, 2024
- Omaha, NE
World-Class Roll Forming Workshop
- June 5 - 6, 2024
- Louisville, KY
Advanced Laser Application Workshop
- June 25 - 27, 2024
- Novi, MI