President
- FMA
- The Fabricator
- FABTECH
- Canadian Metalworking
Categories
- Additive Manufacturing
- Aluminum Welding
- Arc Welding
- Assembly and Joining
- Automation and Robotics
- Bending and Forming
- Consumables
- Cutting and Weld Prep
- Electric Vehicles
- En Español
- Finishing
- Hydroforming
- Laser Cutting
- Laser Welding
- Machining
- Manufacturing Software
- Materials Handling
- Metals/Materials
- Oxyfuel Cutting
- Plasma Cutting
- Power Tools
- Punching and Other Holemaking
- Roll Forming
- Safety
- Sawing
- Shearing
- Shop Management
- Testing and Measuring
- Tube and Pipe Fabrication
- Tube and Pipe Production
- Waterjet Cutting
Industry Directory
Webcasts
Podcasts
FAB 40
Advertise
Subscribe
Account Login
Search
Reducing downtime with condition-based maintenance
Predictive method help personnel fix equipment before it fails
- By Bill Frahm
- May 10, 2022
- Article
- Manufacturing Software
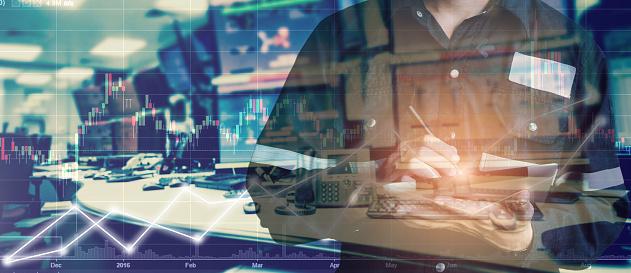
Conditions-based monitoring can be a useful tool for keeping tabs on production conditions and maintaining performance while reducing unscheduled downtime. Goodvibes Photo/iStock/Getty Images Plus
As sheet metal forming becomes more complex, it’s critical to deploy tools to help staff monitor ongoing production conditions. This allows for faster response, improved overall equipment effectiveness, and a safer plant.
One of those tools is condition-based maintenance (CBM), which allows operators and maintenance teams to predict and prevent equipment failures before they interfere with production. It involves scheduling repair and maintenance tasks when equipment shows an operating condition that indicates reduced performance.
Smart operators and maintenance personnel will understand when these performance thresholds are met, realize how much time remains before the equipment will fail, and address the problems before failure becomes imminent.
To do that, they typically use sensors and tools such as lubrication contaminant and viscosity monitors, vibration analysis, temperature monitors, and cycle time analysis. Vibration, oil, and temperature sensors placed on equipment provide continuing tests to identify changes in monitored conditions. When changes happen, the sensors and supporting software send alerts to operators and maintenance staff so that they can manage conditions.
Predictive Vs. Preventive Maintenance
Because CBM is predictive, it is more efficient that traditional, scheduled preventive maintenance procedures.
In automotive terms, preventive maintenance is the same as replacing the oil in your car every 3,000 miles because your shop tells you to. However, today’s vehicles are manufactured with machined tolerances less likely to contaminate or break down oil in such a short period of time, so they can go for 5,000 miles or more between oil changes. In a modern car, sensors measure contaminant levels in the oil and warn the driver when an oil change is needed. That’s CBM.
CBM Plus IoT
The objective of CBM is to maximize the service life of a device by allowing normal operation until changes are detected in a device’s status that indicate a functional failure will occur and corrected action is required.
In addition to direct condition monitoring, manufacturers can use the internet of things (IoT) to collect a history of events so they can accurately predict service life, mean time between failures, and time to failure. Given this information, staff can schedule maintenance tasks to address the most critical and immediate concerns before they become production issues. They also can determine the amount of time, or cycles, between potential failure and functional failure, when corrective action should be taken.
Analysis and Measurements
Some of the most commonly used CBM practices are vibration analysis, lubricant properties monitoring, and temperature measurement.
Vibration analysis supports machine diagnostics by measuring the vibration signals on a machine housing to determine its operating condition. Performed periodically, it can measure changes in a machine’s vibration signature over time. These changes can indicate defects in moving components to warn operators and maintenance personnel of potential failure.
Lubricant properties are critical both to the proper functioning of equipment and to minimize friction between the blank and die components. Lubrication analysis tests fluids to determine if their properties remain within the necessary specifications. Lubrication tests can show contaminants and particulates, viscosity changes, and water contamination.
The act of forming components generates a fair amount of friction and heat, and sometimes sheet metal blanks are purposefully heated for warm and hot forming. Thermography can be used to capture the heat of production assets and blanks. Variations in temperature can indicate issues with oven regulators, lubrication, or worn parts.
CBM can be a useful tool for monitoring production conditions and maintaining performance while reducing unscheduled downtime. Timely alerts of equipment issues can greatly assist maintenance planning and help operators and maintenance personnel diagnose and resolve problems before they lead to equipment failure. Over time, collected machine performance history also can help predict failure intervals.
About the Author
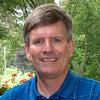
Bill Frahm
P.O. Box 71191
Rochester Hills, MI 48307
248-506-5873
subscribe now
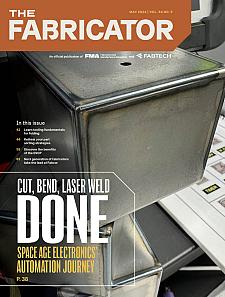
The Fabricator is North America's leading magazine for the metal forming and fabricating industry. The magazine delivers the news, technical articles, and case histories that enable fabricators to do their jobs more efficiently. The Fabricator has served the industry since 1970.
start your free subscription- Stay connected from anywhere
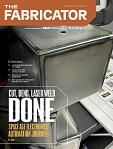
Easily access valuable industry resources now with full access to the digital edition of The Fabricator.
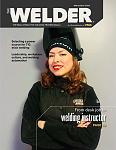
Easily access valuable industry resources now with full access to the digital edition of The Welder.
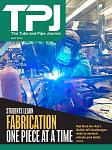
Easily access valuable industry resources now with full access to the digital edition of The Tube and Pipe Journal.
- Podcasting
- Podcast:
- The Fabricator Podcast
- Published:
- 04/16/2024
- Running Time:
- 63:29
In this episode of The Fabricator Podcast, Caleb Chamberlain, co-founder and CEO of OSH Cut, discusses his company’s...
- Trending Articles
Tips for creating sheet metal tubes with perforations
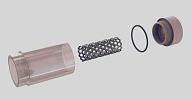
JM Steel triples capacity for solar energy projects at Pennsylvania facility
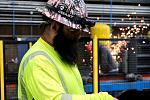
Are two heads better than one in fiber laser cutting?
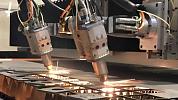
Supporting the metal fabricating industry through FMA
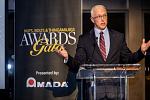
Omco Solar opens second Alabama manufacturing facility
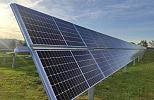
- Industry Events
16th Annual Safety Conference
- April 30 - May 1, 2024
- Elgin,
Pipe and Tube Conference
- May 21 - 22, 2024
- Omaha, NE
World-Class Roll Forming Workshop
- June 5 - 6, 2024
- Louisville, KY
Advanced Laser Application Workshop
- June 25 - 27, 2024
- Novi, MI