Senior Editor
- FMA
- The Fabricator
- FABTECH
- Canadian Metalworking
Categories
- Additive Manufacturing
- Aluminum Welding
- Arc Welding
- Assembly and Joining
- Automation and Robotics
- Bending and Forming
- Consumables
- Cutting and Weld Prep
- Electric Vehicles
- En Español
- Finishing
- Hydroforming
- Laser Cutting
- Laser Welding
- Machining
- Manufacturing Software
- Materials Handling
- Metals/Materials
- Oxyfuel Cutting
- Plasma Cutting
- Power Tools
- Punching and Other Holemaking
- Roll Forming
- Safety
- Sawing
- Shearing
- Shop Management
- Testing and Measuring
- Tube and Pipe Fabrication
- Tube and Pipe Production
- Waterjet Cutting
Industry Directory
Webcasts
Podcasts
FAB 40
Advertise
Subscribe
Account Login
Search
Shortage of steel detailers shines light on their importance
Detailing the steel detailer’s rise to prominence in the modern metalworking industry
- By Tim Heston
- December 21, 2021
- Article
- Manufacturing Software
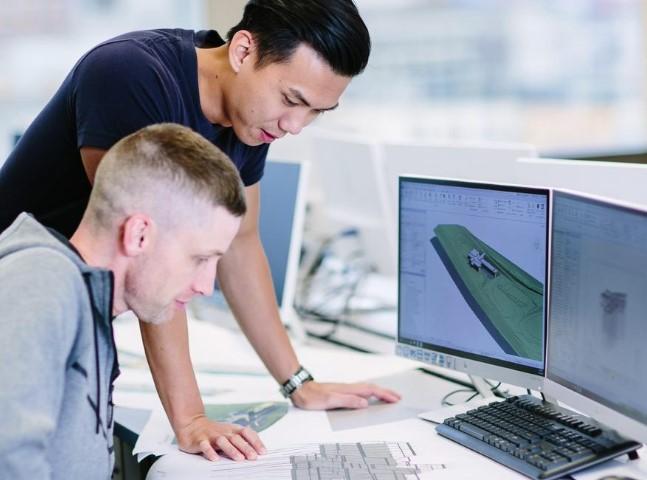
Before the pandemic, Ron Palma of VCC’s steel detailing program guides a student through a construction drawing.
A few years ago Ron Palma of Vancouver Community College took his students on a field trip to the new Amazon facility in downtown Vancouver, B.C., being built on top of a former industrial building. They weren’t there to discuss tech jobs or even economic development, but instead the nuts and bolts of construction. That’s in a literal sense.
As a steel construction modeling technician instructor, Palma heads VCC’s steel detailing program. “We tend to get tunnel vision, a worker in front of a monitor, and we forget how big a scale we’re working on. It’s an eye-opening experience seeing large steel structures and pieces of steel being welded and bolted together.”
VCC recently renamed its certificate program to “steel construction modeling,” a move that shows just how little people outside the construction trade know about steel detailing. “They think it’s about washing cars,” Palma said. “So we changed the name to steel construction modeling to better reflect what we’re doing.”
Palma emphasized that he wasn’t pointing blame at the broader public. Their misunderstanding points to a communication problem that plagues various aspects of the structural metal fabrication trades and, for that matter, metalworking overall.
“There is a severe shortage of steel detailers right now,” Palma said, adding that this shortage has driven enrollment in VCC’s certificate program. Since the pandemic, in fact, the school has offered remote learning opportunities for aspiring steel detailers from all over the world. “We’ve had students from South Korea, Hong Kong, and from other parts of Canada.”
The steel detailer shortage has far-reaching implications, considering the steel detailer’s role in the construction supply chain. Steel detailers might work at a structural fabricator, be a subcontractor to one, or contract directly with the general contractor. Whoever employs them, detailers work at the intersection of information flow, marrying construction standards with best fabrication practices and best sequencing for erection. They go through drawings with a fine-toothed comb (hence the term detailing) to ensure compliance with various industry standards. Without good detailing, structural fabrication falls apart, figuratively and (even worse) literally.
Palma takes his detailing students on construction site and fabricator visits for a reason: They can’t learn the entire trade only by working with software, though software has become more critical than ever. They need to see the big picture. After all, the mouse clicks they make can affect how fabricators or erectors perform their work.
A Welder Turned Detailer
As a welder, Lindsay Meikle remembers looking at a mistake on a drawing, not just a wrong welding symbol, but a larger error that reached the shop floor and, even worse, caused a larger structure not to fit. Rework ensued, either on the floor or (even more expensive) on the job site during erection.
Meikle chuckled quietly. “As a welder, I had the impression that steel detailing was really easy. I took all the good things they did for granted and blew the mistakes way out of proportion, thinking, ‘What were those guys thinking?’”
As a steel detailer at Victoria, British Columbia-based Exact Detailing, Meikle now knows just how much detailers juggle, from managing changeovers to writing RFI (request for information) after RFI to the engineer of record. That said, his years in the fab shop has made him aware of just how important the fabrication details are.
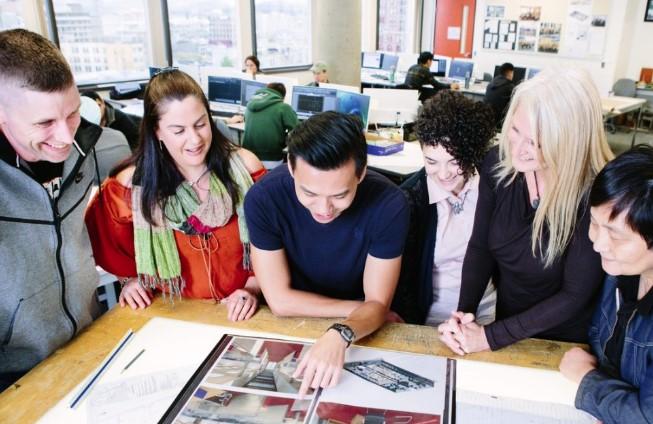
Ron Palma’s students view images of solid models in the classroom. Pre-pandemic, they also ventured outside the classroom to visit construction sites and fabricators.
“With my years in welding, I can spot things that won’t work in fabrication, like weld access issues, as well as issues during the erection stage,” Meikle said.
He added that such issues often involve weld distortion, recalling a recent handrail job for a catwalk in an aircraft hangar. “We have a bunch of vertical pickets, all of them welded top and bottom. Several hundred of these welds would have been placed on the main top rail. I saw that and realized they’d get shrinkage if they put that many welds, so they’d lose a few mils on the overall length.”
The plan was to weld the handrail in the shop and then bolt everything in place on-site. Meikle knew that fastening bolt holes, especially those with threads, would be difficult if not impossible to locate accurately after the assembly had been welded in the shop. “So we decided to go with on-site welding rather than mechanical fasteners, just to nip that problem in the bud.”
Such a change goes against the common practice to minimize on-site welding in favor of mechanical fastening. On-site welding is expensive, but it’s less expensive than mechanical fastening followed by hours or even days of rework.
Steel Detailing
Meikle spent several years in the structural fab shop before a sports injury ended his welding career, so he turned to detailing. But unlike most steel detailers working in industry today, Meikle received specialized training and enrolled in VCC’s 10-month certificate program, graduating in July 2020.
Attaining a certificate is unusual, Palma said, adding that most get into steel detailing with only informal training. Whether they are architectural or civil technicians of some sort or managers in steel fabrication, nearly all new detailers learn on the job.
When detailers start, they often lack some of the fundamentals. And considering the speed of fabrication these days—and the need to adapt and change materials thanks to unpredictable supply chains—a steel detailer lacking fundamental knowledge of steel fabrication and erection can put a construction project in a tough spot.
“At VCC, we try to instill the fundamentals,” Palma said. “We read through the fabrication and construction industry standards.”
Being in Vancouver, the school is careful to cover standards that span all of North America, including those from the Canadian Institute of Steel Construction (CISC), the American Institute of Steel Construction (AISC), the Canadian Welding Bureau (CWB), and the American Welding Society (AWS).
Fundamentals have become even more important as modeling software has permeated the industry. “As powerful as the software is, if you don’t know what you’re doing, you can make some bad choices and cause problems in the model, which will be reflected on the drawings,” Palma said. “If detailers aren’t sure about what they’re doing, their decisions can affect a lot of people.”
Technology at the Forefront of Construction
Palma himself graduated from VCC’s certificate program in 1997, a time of transition both for the detailing program at VCC and the industry overall. The program has roots as deep as VCC’s founding in 1949, when drafting was one of its first academic departments. After decades of having students sit at drafting boards with pencils and papers, the program Palma studied in the late 1990s had four stations of AutoCAD. By the time Palma took over the program in 2018, it was fully entrenched in Tekla.
Today Trimble has donated its Tekla software to VCC for the past 13 years. “[Trimble] has been extremely supportive,” Palma said. “Tekla is so fundamental to what we do. We wouldn’t be a steel detailing program without it.”
“Technology is becoming the forefront of construction. Whether it’s laser scanning in the field, AR/VR with the Hololens, or 3D models used for pricing jobs, all the way through the process, the detailers who have been embracing it and keeping current will be at the forefront of the industry.”
So said Matt Arnott, director of administration at Exact, which since its founding in 2008 has expanded its services to include not just detailing, but also surveying and connection engineering. “We’re all about solving problems ahead of time.”
Most of Exact’s survey work involves renovations of heritage buildings, where it’s important all fabrications mate precisely with the existing structure. The company uses Trimble’s TX7 laser scanner. “The point cloud data we get, if utilized across all parts of the project, can be extremely valuable. We can see exactly what issues we could have before any fabricator starts cutting or welding, before any crane arrives on-site, and well before construction starts.”
For connection engineering, Exact makes use of Qnect to optimize connections. The cloud-based software undergoes numerous iterations to optimize connection design for an entire structure. One fewer bolt hole can save hours or days of erection time. The software even color-codes members to help connection engineers identify the number of required workstations in the fab shop. For instance, one color might signify members that need only go to the punch and drill line, while another color shows components that go through a beam line plus the weld line.
The number of stations a beam goes through affects the cost of the job, where the estimating function comes into play—services that Exact is increasingly being called upon for assistance.
“We do use Tekla EPM [estimating and production management] and provide a preliminary model for a client,” Arnott said. “When we are brought in during the bidding stage, we work with the fabricator, general contractor, and design team to develop an intelligent model and material lists, [so] they can price a job the most effectively.” He added these services also include transportation challenges, the laydown areas for steel, and the sequencing certain space constraints require.
All this has helped Exact and its structural fabrication clients navigate an industry that, like nearly everywhere else, continues to suffer from supply chain challenges. “At this point everyone is becoming proactive,” Arnott said, adding that software has allowed his company to provide information to clients, allowing them to make quick decisions as different materials become available. “We build a smart model well before construction. We do the preliminary connection engineering and detailing, all during the estimation stage. We can price out different components and uncover scheduling scenarios. We fully utilize our software tools to allow our clients to make the best decision for the project.”
All this happens well before any steel is cut, welded, or erected. As VCC’s Palma described, such predictive software tools have changed steel detailing’s prominence.
Still, a detailer’s world shouldn’t be confined to the computer screen. Before the pandemic, Palma led a class field trip to Dynamic Attractions, the amusement park ride firm specializing in design, engineering, and fabrication that has a facility near downtown Vancouver. There, students saw not only engineers and detailers in action, but also the numerous fabricators on the shop floor.
Palma’s message: The model you design in software has a direct impact on everything that happens in fabrication and erection. “For a long time, steel detailing was at the bottom of the ladder, under the radar. Even in construction, people didn’t know what steel detailing was. And as the years are going on, I think one of the biggest reasons detailers have risen to such high profiles is because of software. We have powerful tools that we can extract information from and share so quickly, it has made the detailer that much more vital.”
About the Author
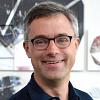
Tim Heston
2135 Point Blvd
Elgin, IL 60123
815-381-1314
Tim Heston, The Fabricator's senior editor, has covered the metal fabrication industry since 1998, starting his career at the American Welding Society's Welding Journal. Since then he has covered the full range of metal fabrication processes, from stamping, bending, and cutting to grinding and polishing. He joined The Fabricator's staff in October 2007.
subscribe now
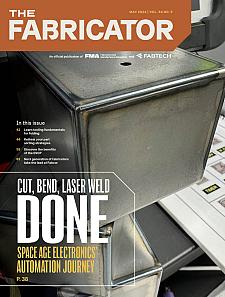
The Fabricator is North America's leading magazine for the metal forming and fabricating industry. The magazine delivers the news, technical articles, and case histories that enable fabricators to do their jobs more efficiently. The Fabricator has served the industry since 1970.
start your free subscription- Stay connected from anywhere
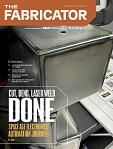
Easily access valuable industry resources now with full access to the digital edition of The Fabricator.
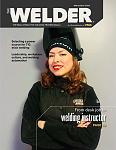
Easily access valuable industry resources now with full access to the digital edition of The Welder.
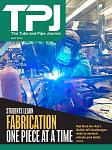
Easily access valuable industry resources now with full access to the digital edition of The Tube and Pipe Journal.
- Podcasting
- Podcast:
- The Fabricator Podcast
- Published:
- 04/16/2024
- Running Time:
- 63:29
In this episode of The Fabricator Podcast, Caleb Chamberlain, co-founder and CEO of OSH Cut, discusses his company’s...
- Industry Events
16th Annual Safety Conference
- April 30 - May 1, 2024
- Elgin,
Pipe and Tube Conference
- May 21 - 22, 2024
- Omaha, NE
World-Class Roll Forming Workshop
- June 5 - 6, 2024
- Louisville, KY
Advanced Laser Application Workshop
- June 25 - 27, 2024
- Novi, MI