President
- FMA
- The Fabricator
- FABTECH
- Canadian Metalworking
Categories
- Additive Manufacturing
- Aluminum Welding
- Arc Welding
- Assembly and Joining
- Automation and Robotics
- Bending and Forming
- Consumables
- Cutting and Weld Prep
- Electric Vehicles
- En Español
- Finishing
- Hydroforming
- Laser Cutting
- Laser Welding
- Machining
- Manufacturing Software
- Materials Handling
- Metals/Materials
- Oxyfuel Cutting
- Plasma Cutting
- Power Tools
- Punching and Other Holemaking
- Roll Forming
- Safety
- Sawing
- Shearing
- Shop Management
- Testing and Measuring
- Tube and Pipe Fabrication
- Tube and Pipe Production
- Waterjet Cutting
Industry Directory
Webcasts
Podcasts
FAB 40
Advertise
Subscribe
Account Login
Search
The case for mechanical beveling
Fabricators can improve productivity and quality with these portable and benchtop tools
- By Phil Heck
- January 29, 2021
- Article
- Cutting and Weld Prep
Portable beveling machines are designed to mill a bevel edge along the plate edge. Photos courtesy of Heck Industries.
No one likes to grind metal for weld prep for an entire shift. It’s difficult to maintain consistency as the hours pass because of the physical nature of the job.
Welders have their own opinions as well. They’d be quick to tell you that they’d rather work with a clean, consistent bevel than something with inconsistent depths of cut and bevel widths.
That’s where mechanical beveling machines can make a difference. They work faster than someone manually grinding a bevel. They provide more consistent cut depths and bevel widths. They produce bevels that look like they came off a machining center.
These devices also are going to produce metal chips, not the dust that results from manual grinding. Dust is not only a respiratory hazard, it also poses a slipping danger. Chips rather than dust is a safety benefit that not a lot of people consider.
What’s Available in Beveling Technology
Most fabricators might consider hand-held beveling technologies for their weld prep needs. They are flexible enough to tackle projects of various sizes, and they don’t cost much more than the hand-held grinders the weld prep team uses.
These devices fall into two categories, straight and shape bevelers. Straight bevelers are meant to be used to bevel plate edges. The operator sets the bevel angle, lines the beveling device up on the plate edge, and guides it down the line as the bevel is created. The operator doesn’t need to force the action like he might have to do with a grinding tool.
Shape bevelers are used to bevel contours, although they can work on straight edges as well, even if they may not be specifically designed to. (They’d likely be a bit slower in tackling those straight-side bevels.)
These tools particularly shine when beveling small holes or slots. Typically, a manual grinder would be the tool of choice for this type of a job. The unfortunate result in many instances is that the person trying to grind that small hole with an abrasive wheel or disc leaves the hole in worse condition than it was originally. A shape beveler can be used to create a uniform bevel around the hole and leave a finish that looks like a Bridgeport mill produced it, except for the fact that the operator didn’t have to program a machine or clamp the part into a fixture.
These bevelers come in various sizes. One of the smallest is a device that fits into an operator’s palm, weighing around 5 ounces. This type of equipment can produce a 1/16-in. radius on small holes. (They can be powerful as well. Pneumatic versions of this small power tool can reach 22,000 RPM.)
Shape bevelers also are capable of creating a radius, as wide as ¼ in. A tool operator guides the tool over the metal, sometimes over a weld bead, to create the round shape. Shape bevelers often are used for decorative purposes, such as handrails and gun safes. In many instances, a final cleaning with a low-grit abrasive is needed for the newly created radius to really shine.
This shape beveler provides radius shaping for applications such as edge rounding. This particular unit has an adjustable cut depth up to 3/16 in.
Larger units can deliver bevels as deep as 7/8 in. and change the angle of the bevel from 15 to 45 degrees. Even though the units are larger, the operator is not faced with the risk of severe fatigue from operating the equipment because the tools sit on the plate as the bevel is being created. Some units can reach speeds as high as 3 FPM.
Larger units are designed to work with standard carbide cutting inserts, which can be changed out quickly by loosening a couple of screws. (Smaller beveling units typically require special cutting tools because of their size.)
Benchtop beveling units also are available for metal fabricators that work with small to medium-sized workpieces. Some sort of guidance mechanism leads the workpiece between two guide plates, where the milling cutter is found. The operator adjusts the angle and depth of penetration by setting the guide plates and tool position.
More often than not, benchtop units are used for deburring and cleaning up an edge. It’s not unusual to see such a machine next to a machining center so that the operator can clean the part edge off before putting the workpiece into the mill for the precise cutting.
Powerfeed bevelers are for shops that perform a lot of beveling. When these units are placed on wheels, they can be affixed to a long piece of plate, and the beveler creates the desired edge shape while also moving down the plate’s edge. Think of it as an electric can opener, if you are old enough to recall how those work.
Powerfeed units do not require an operator to watch over them as they are cutting. Once they are engaged in beveling, an operator can walk away from the unit to do something else. When the beveler reaches the plate’s end, it disengages from the metal and remains stationary until the operator moves it to its next job.
These portable bevel units also can be used to tackle pipe projects with the addition of a rolling mechanism. The beveler attaches to the end of the pipe and the roller guides it along its circular path.
This type of accessory is useful for shops that have the occasional pipe job. Obviously, if a shop is looking to do an extensive amount of pipe work, a dedicated machine might make more sense.
Getting the Most out of the Beveler
Like most cutting activities, lubricants help to optimize the cutting process and extend the life of the cutting consumables. Vegetable oil-based lubricants tend to do the trick for most beveling jobs. It’s got a high heat threshold and doesn’t produce offensive odors when in use.
The lubricant helps to extend the cutting consumable life two to three times compared to a consumable used in dry cutting applications. It also produces a surface finish that looks like it was done in a mill after the lubricant has been cleaned from the beveled edge.
Unlike petroleum-based lubricants, vegetable oil lubricants can be welded through. A technician still should clean the vegetable oil lubricants from the surface after cutting, but if some remains, it won’t affect the overall quality of the weld. Petroleum-based lubricants have to be thoroughly cleaned from the surface because they pose a greater threat to weld quality.
Phil Heck is owner of Heck Industries Inc., 1498 Old U.S. 23, Howell, MI 48353, 810-632-5400, www.heckind.net.
About the Author
Phil Heck
1498 Old U.S. 23
Howell, MI 48353
(810)632-5400
Related Companies
subscribe now
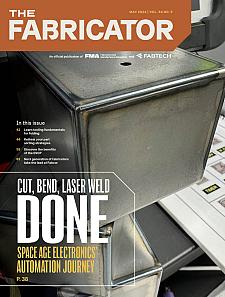
The Fabricator is North America's leading magazine for the metal forming and fabricating industry. The magazine delivers the news, technical articles, and case histories that enable fabricators to do their jobs more efficiently. The Fabricator has served the industry since 1970.
start your free subscription- Stay connected from anywhere
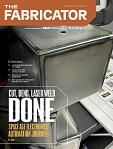
Easily access valuable industry resources now with full access to the digital edition of The Fabricator.
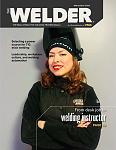
Easily access valuable industry resources now with full access to the digital edition of The Welder.
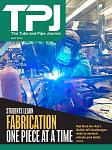
Easily access valuable industry resources now with full access to the digital edition of The Tube and Pipe Journal.
- Podcasting
- Podcast:
- The Fabricator Podcast
- Published:
- 04/16/2024
- Running Time:
- 63:29
In this episode of The Fabricator Podcast, Caleb Chamberlain, co-founder and CEO of OSH Cut, discusses his company’s...
- Trending Articles
Tips for creating sheet metal tubes with perforations
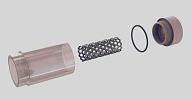
JM Steel triples capacity for solar energy projects at Pennsylvania facility
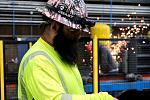
Are two heads better than one in fiber laser cutting?
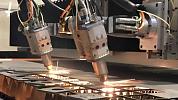
Supporting the metal fabricating industry through FMA
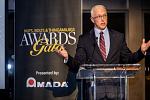
Omco Solar opens second Alabama manufacturing facility
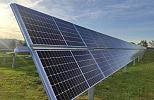
- Industry Events
16th Annual Safety Conference
- April 30 - May 1, 2024
- Elgin,
Pipe and Tube Conference
- May 21 - 22, 2024
- Omaha, NE
World-Class Roll Forming Workshop
- June 5 - 6, 2024
- Louisville, KY
Advanced Laser Application Workshop
- June 25 - 27, 2024
- Novi, MI