Contributing editor
- FMA
- The Fabricator
- FABTECH
- Canadian Metalworking
Categories
- Additive Manufacturing
- Aluminum Welding
- Arc Welding
- Assembly and Joining
- Automation and Robotics
- Bending and Forming
- Consumables
- Cutting and Weld Prep
- Electric Vehicles
- En Español
- Finishing
- Hydroforming
- Laser Cutting
- Laser Welding
- Machining
- Manufacturing Software
- Materials Handling
- Metals/Materials
- Oxyfuel Cutting
- Plasma Cutting
- Power Tools
- Punching and Other Holemaking
- Roll Forming
- Safety
- Sawing
- Shearing
- Shop Management
- Testing and Measuring
- Tube and Pipe Fabrication
- Tube and Pipe Production
- Waterjet Cutting
Industry Directory
Webcasts
Podcasts
FAB 40
Advertise
Subscribe
Account Login
Search
Detroit-area metal stamper adds servo transfer press to sustain its rhythm supplying automotive industry
Motor City Stamping adds capacity, capabilities, workforce with machine installation
- By Kate Bachman
- August 11, 2022
- Article
- Electric Vehicles
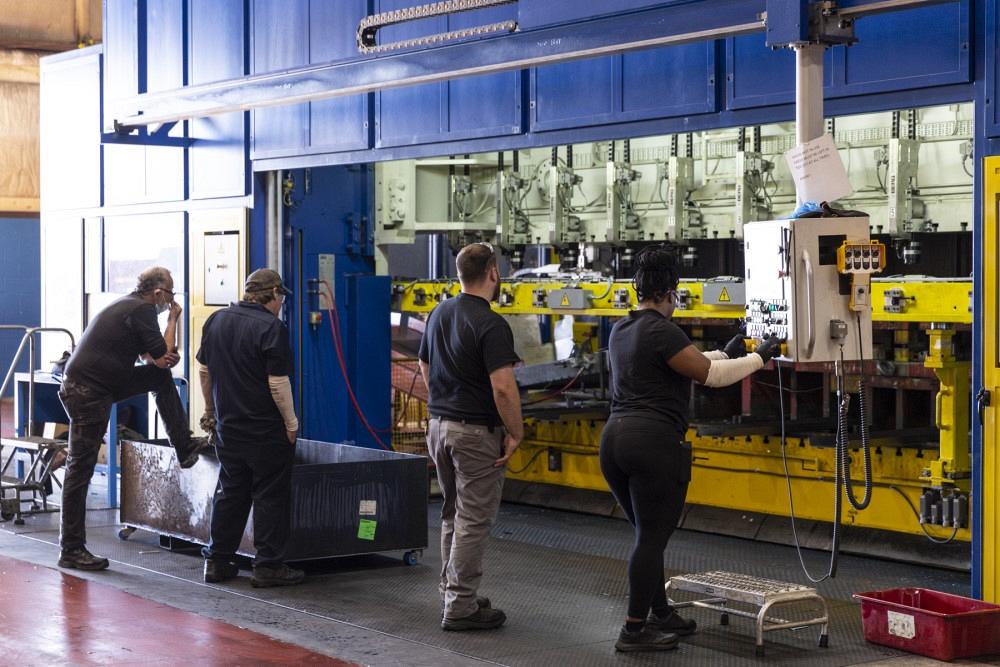
Motor City Stamping personnel inspect the new servo transfer press and ready it for production. At first, they ran only reliable, large progressive dies in the transfer press to debug the press and coil system. Employees are a precious resource at Motor City. The company has 360 employees in Chesterfield, Mich., and is looking to hire 40 more.
On a busy street in Chesterfield, Mich., two modest-looking, tan brick buildings with a narrow lane between them and small, arched windows sit close to the road. They could be mistaken for a quick-print shop or a local insurance agency. The inconspicuous buildings belie their actual size—360,000 sq. ft.—the robust stamping manufacturing activity within them, and the continuous expansion of the company there, including the recent installation of a new 1,690-ton servo transfer press and a 28,000-sq.-ft. addition.
Parts on Every GM
Motor City Stamping has stamped parts for every GM vehicle made in the past 50 years. It has been a Tier 1 stamping supplier of single-piece and assembled automotive structural components to GM since its inception in 1969.
The family-owned, Certified Woman Owned Business is still under the watchful eye of the original founder and owner, CEO Judith Kucway, and her husband, Roger. Their son, Patrick Kucway, is president, and several other family members now help manage the operations.
“We locked in some direct work with General Motors from the beginning, and our company has been built on supplying to it,” Patrick Kucway said.
The company ships globally from its only location in Chesterfield, Mich., north of Detroit. Recently, the stamper has become a Tier 1 supplier to both Honda NA and Ford Motor Co. It also serves a number of Tier 1 suppliers such as Kautex Textron, Webasto, Inalfa, Navistar, Thyssenkrupp, and Shape Corp.
“We have been blessed with continuous moderate growth,” Kucway said. Based on booked sales and forecasting, company management assessed current and future capacity as well as future demand.
“We have found the need to expand our manufacturing capacity and building space. We need additional press capabilities and overall capacity to allow Motor City Stamping to be open for new opportunities. That could not be done with our current press configuration, building size, and staff size,” Kucway added.
Sizing Up the Current, Future Situation
Motor City Stamping produces about 40 million parts a year for GM. It ships roughly 6 million parts a month for all of its customers. “We've been running 24/7 for about the last year. We were struggling to keep up with orders,” said Accounts Manager Ray Davis.
Motor City Stamping’s press fleet included 10 progressive die presses ranging from 300 to 1,000 tons, but only one 1,200-ton transfer press, which was running constantly and beyond its capacity limits because of high demand.
“The existing transfer press was running about 130% over capacity, and our other press lines were mostly legacy mechanical presses,” Davis said. Not only did the company want to meet current demand, it wanted to have more capability and capacity for future growth.
“We began the hunt for either a pre-owned or new servo transfer press,” Davis said.
Why Servo Transfer Press?
Davis explained why the company wanted that specific type of press.
Servo. Although the manufacturer doesn’t stamp a lot of really deep drawn parts, it does stamp some large parts like heat shields, inner fender components, and side components. “With mechanical presses, you're kind of stuck with a fixed stroke and press opening. A servo press allows us more flexibility to manage the length of the stroke and motion profiles so that we can use the minimum stroke required. That way we can get more parts out of the press,” Davis said.
He continued, “Let's say you have a 22-in. window in a mechanical press, but you only need a 12-in. opening. You have to wait for that press to go its full draw, 22 in. up and down. A servo press will allow you to program it so that it doesn't use the whole stroke. So, you can literally short stroke a tool and get a higher stroke per minute rate because you're not using the full 22 in. of stroke.”
The torque range can be changed more readily on a servo press than a mechanical press too. “So, a servo press would give us the control we wanted.”
Transfer. Another transfer press would provide more capability to do a wider product range, not only for GM, but also for new OEM business, Davis said.
The difference between a progressive die and a transfer die press is primarily how the part is moved from station to station, Davis explained. Instead of having carrier tabs that carry the part all the way to the end of the progressive die and then are cut off at the end, the blank is formed as it goes through the tools. Finger tools pick it up and move it.
“Typically, the coil comes in and a blank is cut off in the very first station. Then, the transfer fingers that are mounted on a transfer bar come in and actually pick up that blank and move it through the stamping stations to form the part.”
The stamper was seeking the advantages that a transfer system offers over progressive die systems, he said. “You can reduce your blank size. You don’t get a lot of scrap. Also, you can transfer much bigger parts because you can use the entire coil width. In fact, you can press parts that are larger than the coil width by running them on a diagonal.”
In addition, a transfer system allows for the forming of complex parts because they can be pressed from more than one direction, Davis maintained.
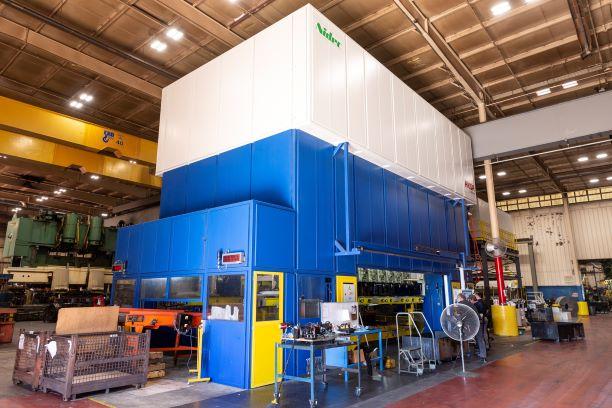
A new 1,690-ton Nidec Arisa High Dynamic Transfer servo transfer press system was installed at Motor City Stamping to expand press capacity and meet high current and future demand. Images: Brad Ziegler for STAMPING Journal
Acquiring the Press
The plans to expand the business began over two years ago, but were then delayed due to the pandemic, Davis relayed. “We were fortunate to finally find a new Nidec Press & Automation Arisa servo transfer press, which was built for another company that could no longer take possession.”
The press system includes some unique technology, according to Nidec Press & Automation North American Automotive Market Segment Director Joel Wuebker.
“This system included a Nidec Arisa press, high dynamic transfer, and moving bolster with Nidec CHS thread table, straightener, feed, and coil car—all of which are uniquely integrated as a total OEM system.
“Many helpful features in this system like the antivibration technology, the moving bolster transfer technology, and the common HMI were designed with the operator in mind to create an efficient experience and simplified functionality,” said Wuebker.
Coil Handling. The Nidec CHS HDX coil line comprises a thread table, straightener, feed, and coil car. Its capacity is up to 72 in. wide and handles up to 8-mm material thickness for increased material flexibility. “So, it gives us the capability to do very large and also very thick or high-strength parts,” Davis said.
Moving Bolster. One unique aspect about the press system is that the die cart function is replaced with a moving bolster that is integrated with the press and is operated from a common HMI. “It is actually part of the lower bolster rather than a separate unit that has to be moved out once the die is in place. It goes into the press and stays in there during the operation,” Davis said. The moving bolster moves the die in and out on a steel rail that’s embedded in the floor.
Scrap. Because the press was installed in an existing building, there were no underground conveyor pits for scrap, so side scrap ejection trays were installed instead. Scrap drops off and down a shoot and out of the back of the press.
Installation Logistics
The transfer press installation was not without complications. A door had to be moved for the press to fit through, and an overhead crane had to be installed. In addition, the excavation and concrete pour for the foundation had to wait for the ground to defrost. Michigan has very strict frost laws that limit the movement of heavy equipment in the winter months. “To be able to get the heavy crane out here, we had to make sure that we were clear of the frost,” Davis said.
Very large pillars were driven all the way down into the bedrock. Hundreds of tons of concrete were poured. The pit is 15 ft. deep. Sump pumps are in position below to pump water out.
Of course, all of the installation had to occur without disrupting current operations.
Up and Running
The new press has been up and running and producing parts. In June, the company initiated production, running only reliable, large progressive dies in the transfer press to debug the press and coil system. The initial transfer job beginning July 1 was a hood reinforcement part for GM.
Some of the parts the company is stamping on the press are new, and some are in a “sundowning phase,” Davis said. “We have more than 400 GM part numbers alone that are in production today. Since we’ve been supplying to GM for over 50 years, we have literally thousands of active part numbers. You know, you continue to make service parts for 15 years. We still have a tool here that makes parts for the Chevy S-10 pickup and a van that they've been making since the 70s.”
One part and its variations that Motor City Stamping now produces that it anticipates “sundowning” is heat shields. “That’s $7 million worth of business that we're potentially going to lose in the next few years because of electrification,” Davis said. Another part is a thick, heavy bracket that holds up a diesel fuel tank.
“We’re losing some vehicle content because of the move to electrification, but we do quite a few parts for the automakers that are a part of the new electrified business, Davis said.
For example, Motor City Stamping stamps parts for the new electrified Hummer being produced at GM’s Factory Zero in Hamtramck, Mich., he said. The company also is stamping a number of parts for the new GM Chevy Silverado EV and several part numbers for the Mustang Mach-E. Some go directly onto the skateboard battery system, he said.
“We’re fortunate to have parts on the skateboard. We started out quoting maybe a 100,000; 150,000 parts per year. Well, there are multiples of them that go onto the skateboard. And now we're shipping 500,000 that all go on the Mustang Mach-E.”
Building Expansion
To meet space constrictions due to growing demand, the company enclosed the space between two buildings that had been outdoor transportation and docking space. The new construction added 28,000 sq. ft.
Davis pointed to resources needed beyond equipment.
“Good people are a precious commodity today. There's a significant percentage of the human resources here—our operators, our skilled trades—that have been with the company for a long time. Many years of experience … 10, 15, 20 years. As a matter of fact, we still have the very first employee who was hired here,” Davis said.
Davis relayed it has been hard to get new hires for general manufacturing-type work and then retain them. “Salaried guys like me have been coming in here on weekends because we've been having so many labor issues. I ran two presses from 8 o'clock Saturday night until three in the morning,” Davis said. Motor City Stamping employs approximately 360 people and is looking to hire an additional 40 employees.
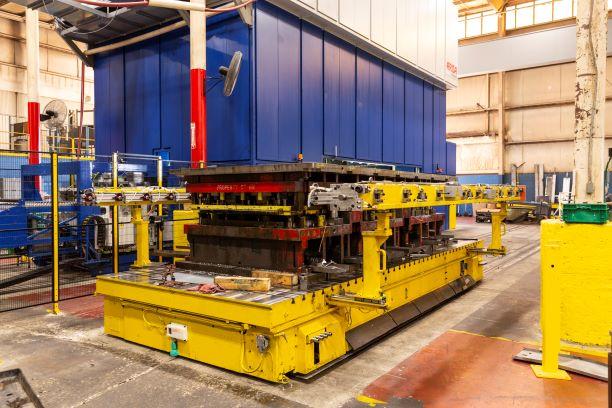
The moving bolster is integrated with the lower die and remains in the press during the operation, then is moved out by rail.
Making Longevity Attainable
So, what is the secret to Motor City Stamping’s longevity and enviable position as a Tier 1 supplier to GM, and now to Ford and Honda?
Hard work, transparency, and good financial management, Kucway said. “We don't have a ton of overhead. We've never been a company to outgrow itself. A lot of companies expand into other states, open other endeavors, and they really over-leverage themselves. We have very little debt. We're proud to say this company actually owns nearly everything in here.”
Davis added, “We, as a management team, make very smart decisions as to our growth. We pull back when we feel like we need to pull back, and then we surge forward when we feel we should; for instance, to buy this press. So, I think that is really why the company's had such longevity. It’s just good, old-fashioned business horse sense.
“Plus, there's a good corporate culture,” he added. “There’s respect for everybody. Like a family, you have your good days and bad days, but, when push comes to shove, everybody pulls together.”
About the Author
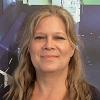
Kate Bachman
815-381-1302
Kate Bachman is a contributing editor for The FABRICATOR editor. Bachman has more than 20 years of experience as a writer and editor in the manufacturing and other industries.
Related Companies
subscribe now
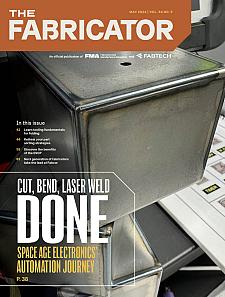
The Fabricator is North America's leading magazine for the metal forming and fabricating industry. The magazine delivers the news, technical articles, and case histories that enable fabricators to do their jobs more efficiently. The Fabricator has served the industry since 1970.
start your free subscription- Stay connected from anywhere
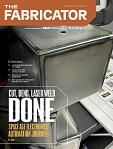
Easily access valuable industry resources now with full access to the digital edition of The Fabricator.
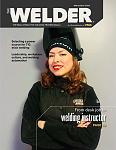
Easily access valuable industry resources now with full access to the digital edition of The Welder.
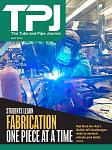
Easily access valuable industry resources now with full access to the digital edition of The Tube and Pipe Journal.
- Podcasting
- Podcast:
- The Fabricator Podcast
- Published:
- 04/30/2024
- Running Time:
- 53:00
Seth Feldman of Iowa-based Wertzbaugher Services joins The Fabricator Podcast to offer his take as a Gen Zer...
- Industry Events
Pipe and Tube Conference
- May 21 - 22, 2024
- Omaha, NE
World-Class Roll Forming Workshop
- June 5 - 6, 2024
- Louisville, KY
Advanced Laser Application Workshop
- June 25 - 27, 2024
- Novi, MI
Precision Press Brake Certificate Course
- July 31 - August 1, 2024
- Elgin,