Editor-in-Chief
- FMA
- The Fabricator
- FABTECH
- Canadian Metalworking
Categories
- Additive Manufacturing
- Aluminum Welding
- Arc Welding
- Assembly and Joining
- Automation and Robotics
- Bending and Forming
- Consumables
- Cutting and Weld Prep
- Electric Vehicles
- En Español
- Finishing
- Hydroforming
- Laser Cutting
- Laser Welding
- Machining
- Manufacturing Software
- Materials Handling
- Metals/Materials
- Oxyfuel Cutting
- Plasma Cutting
- Power Tools
- Punching and Other Holemaking
- Roll Forming
- Safety
- Sawing
- Shearing
- Shop Management
- Testing and Measuring
- Tube and Pipe Fabrication
- Tube and Pipe Production
- Waterjet Cutting
Industry Directory
Webcasts
Podcasts
FAB 40
Advertise
Subscribe
Account Login
Search
A new dimension in beveling abrasives
A re-engineered abrasive material delivers a new level of material removal in fabricating applications
The abrasive belt on the left beveled 18 forklift components before it was too worn to be used again. The new 3M 984FX Pro belt beveled 62 similar parts.
A new and effective tool holds the potential to really transform a process. Precision Bevel, Burlington, Ky., believes it has one, with the introduction of a new abrasive belt from 3M Abrasives.
Precision Bevel, founded by Iwan Antonow in late 2019, offers beveling as a service. Customers seek the company out to produce bevels on plate and steel components, primarily as a prelude to welding.
At the heart of the beveling enterprise is a Gerima FasRapid LGA 3000 II machine. Antonow describes it as a “high-performance” grinding beveler, relying on cloth belts with ceramic grains as the abrasive to remove the material in several precise passes across the material. The beveler can accommodate up to 4-in. plate and lengths of up to 12 ft. (Longer parts can be processed by indexing them through the machine.) The machine can produce up to 4-in.-wide bevels and has an angle range of 0 degrees to 80 degrees.
“You set the machine up, and the grinding unit goes back and forth, removing material with each pass,” Antonow said. “You can set it to cut a little deeper into the material with each pass, if needed. You can regulate that depth.”
On the Gerima machine, Precision Bevel uses industrial abrasive belts from various vendors. According to Antonow, these conventional abrasive belts have served the company well in its beveling applications.
A New Tool
Earlier this year, 3M Abrasives approached Precision Bevel to try out the new generation of abrasive belts, the Cubitron II 984FX Pro. The ceramic grains are designed so that when they break off during metal removal, other sharp forms remain, allowing for consistent performance even as the belt wears down. According to 3M officials, the new generation of abrasives, when crushed during use, leave sharper and “precision-shaped” grains, resulting in better performance when compared to the previous generation of belts. The belts also have been designed to improve heat dissipation while in use.
According to Alejandro Naumann von Rennenkampf, the 3M coated abrasives product manager for U.S. and Canada, the new generation of Cubitron abrasives has been available to manufacturers for about six months. It is only available in 36 grit right now, but he said that 3M is looking to expand upon that in the near future.
Intrigued by the opportunity, Antonow set up a beveling trial for the new abrasive. This is what he found out.
Testing Abrasive Performance
Antonow set up the test on the Gerima beveling machine. The trial involved 1-in.-thick and 22-in.-wide plate used in a forklift application. The part required a 65-degree bevel on its long edge. To produce such a part, the abrasive belt, oscillating as it engaged with the metal to ensure uniform usage across the belt wide, required multiple passes. The belt rotates at about 1,800 RPM.
Stage 1 of the trial tested the durability of a conventional, current-generation abrasive belt. It managed to bevel 18 parts successfully with one belt. (The Gerima machine can accommodate six parts per clamping. It needed three clampings to process all 18 parts.)
3M’s new Cubitron II 984FX Pro belt is applied to plate on a beveling trial at Precision Bevel in Burlington, Ky.
By the end of this trial, Antonow said that the belt showed extensive wear and the belt’s joint revealed signs of potential fraying. The risk of rupture was too high to continue with the belt. Additionally, part discoloration, a sign of excessive heat and friction, was evident on some of the plate beveled late in the exercise.
Stage 2 of the trial involved the new 984FX Pro. Antonow said he ran 18 parts again over three clampings. However, when he examined the belt afterward, he said he discovered only “slight” wear marks.
He also noticed that the 984FX Pro removed more material per pass than the conventional abrasive belt.
“Where with the conventional belt, you might take 1 mm off per pass,” Antonow said, “the new belt would allow you to remove 1.5 mm per pass and still go at the same speed, not generating more heat.”
Stage 3 included the beveling of yet another 18 parts. Antonow said that the wear marks had increased, but the belt’s integrity didn’t seem to be diminished.
Antonow didn’t want to stop there, so he continued the trial by processing another 18 parts. Upon completion of this Stage 4, he identified more wear around the center line and the beginning of fraying around the belt seam. He said he figured he could process a few more parts.
After beveling another eight parts, Antonow said the new generation abrasive belt had reached the end of its useful life. The belt beveled 62 pieces total, compared to 18 parts for the previous generation of abrasive technology.
Antonow said the trial with the forklift parts was probably one of the toughest beveling jobs that his company tackles on a regular basis. He added that he looked forward to trying the new abrasive on other materials, such as stainless steel and armor-grade steel.
About the Author
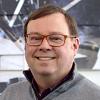
Dan Davis
2135 Point Blvd.
Elgin, IL 60123
815-227-8281
Dan Davis is editor-in-chief of The Fabricator, the industry's most widely circulated metal fabricating magazine, and its sister publications, The Tube & Pipe Journal and The Welder. He has been with the publications since April 2002.
Related Companies
subscribe now
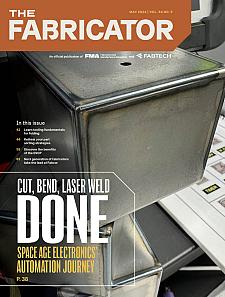
The Fabricator is North America's leading magazine for the metal forming and fabricating industry. The magazine delivers the news, technical articles, and case histories that enable fabricators to do their jobs more efficiently. The Fabricator has served the industry since 1970.
start your free subscription- Stay connected from anywhere
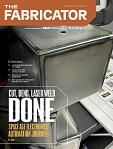
Easily access valuable industry resources now with full access to the digital edition of The Fabricator.
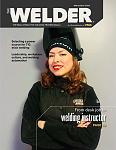
Easily access valuable industry resources now with full access to the digital edition of The Welder.
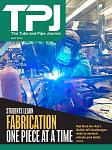
Easily access valuable industry resources now with full access to the digital edition of The Tube and Pipe Journal.
- Podcasting
- Podcast:
- The Fabricator Podcast
- Published:
- 04/16/2024
- Running Time:
- 63:29
In this episode of The Fabricator Podcast, Caleb Chamberlain, co-founder and CEO of OSH Cut, discusses his company’s...
- Trending Articles
Tips for creating sheet metal tubes with perforations
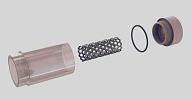
JM Steel triples capacity for solar energy projects at Pennsylvania facility
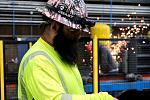
Are two heads better than one in fiber laser cutting?
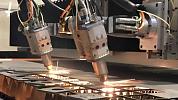
Supporting the metal fabricating industry through FMA
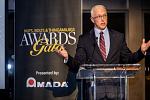
Omco Solar opens second Alabama manufacturing facility
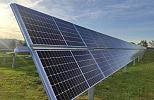
- Industry Events
16th Annual Safety Conference
- April 30 - May 1, 2024
- Elgin,
Pipe and Tube Conference
- May 21 - 22, 2024
- Omaha, NE
World-Class Roll Forming Workshop
- June 5 - 6, 2024
- Louisville, KY
Advanced Laser Application Workshop
- June 25 - 27, 2024
- Novi, MI