Editor-in-Chief
- FMA
- The Fabricator
- FABTECH
- Canadian Metalworking
Categories
- Additive Manufacturing
- Aluminum Welding
- Arc Welding
- Assembly and Joining
- Automation and Robotics
- Bending and Forming
- Consumables
- Cutting and Weld Prep
- Electric Vehicles
- En Español
- Finishing
- Hydroforming
- Laser Cutting
- Laser Welding
- Machining
- Manufacturing Software
- Materials Handling
- Metals/Materials
- Oxyfuel Cutting
- Plasma Cutting
- Power Tools
- Punching and Other Holemaking
- Roll Forming
- Safety
- Sawing
- Shearing
- Shop Management
- Testing and Measuring
- Tube and Pipe Fabrication
- Tube and Pipe Production
- Waterjet Cutting
Industry Directory
Webcasts
Podcasts
FAB 40
Advertise
Subscribe
Account Login
Search
CUTCO Corp. uses engineered abrasives to create a new finish
Knife manufacturer finds a more modern way to produce a high-end finish on its high-end cutlery
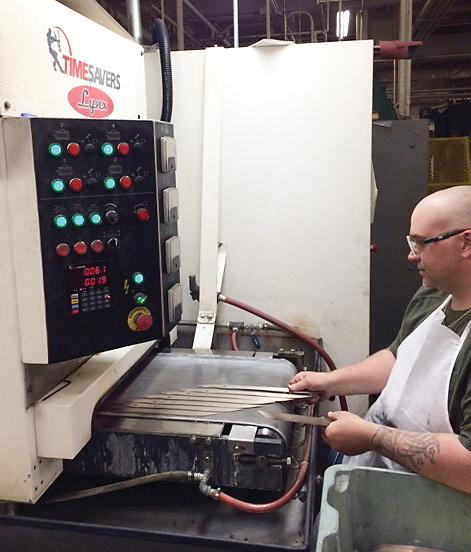
Figure 1
The adoption of the Timesavers flat-surface finishing machine
and the Trizact abrasive technology has allowed
CUTCO Corp. to eliminate a majority of the labor costs associated
with making “cut-down” rolls that the older finishing
machines needed to do the job. The current equipment
setup removes enough stock material and leaves a surface
ready for final buffing.
Photos courtesy of CUTCO Corp.
CUTCO® Corp., the only U.S. manufacturer of high-end kitchen cutlery, follows a knife production process that has more than 30 steps, but in the end it all comes down to the finish. The end of the manufacturing process is crucial because that cutlery is not leaving the factory in Olean, N.Y., unless it looks worthy of a product with a lifetime performance guarantee.
With that in mind, you might understand why the manufacturer held onto a prefinishing process, comprised of old “cut-down” equipment and a labor-intensive method to create the rolls used to remove that metal, for more than 50 years. The finishing steps taken before final polishing worked: The knives looked like high-end cutlery, especially when compared to global competitors’ knives.
That doesn’t mean equipment wasn’t looked at or new production steps tried over the last five decades. It just means that nothing really did the job like the process that was already in place.
Well, that changed about a year ago. New technology finally trumped tradition.
The End of an Era
“Our objective is to polish our cutlery blades to a mirror finish,” said Paul Eade, process engineering manager, CUTCO Corp. “Due to the typical manufacturing problems that we have with polishing steel, we have to take off so much stock from our blades before we’ll be able to produce a mirror finish without any imperfections.”
The company looks to take about 0.003 to 0.004 inch off of the metal surface, where imperfections are easy to see with the naked eye. The top layer also happens to be hardened as a result of the metal- making process; it represents the hardest layer of the metal to cut through. Getting rid of that material is important, however, because it allows the final buffing rolls to apply that pristine, mirrorlike finish that customers want in their cutlery.
CUTCO had a unique way of getting rid of that metal stock before blades were sent to the final polishing rolls.
“These machines [used for prefinishing] required us to build and maintain buffing rolls with a liquid abrasive head on them that you cured to a hard finish,” Eade said.
A one-sentence description of the prefinishing process hardly is apt considering what actually took place. The equipment didn’t look that unusual. Machines with reciprocating heads used for buffing are actually a common sight in the metal- and woodworking industries. The process to prepare the buffing rolls was an entirely different story.
The rolls began as cotton buffs pressed onto a shaft. Next glue was applied and allowed to cure. Then a layer of abrasive mix was applied and allowed to cure. This process was repeated three more times for each 36-in.-long by 8-in.-diameter buffing roll.
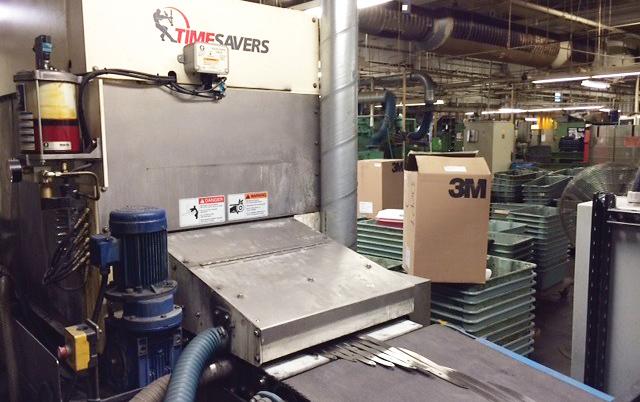
Figure 2
A magnetized table holds the blades stationary and flat while inside the flat-surface finishing machines. A demagnetizer is built into the exit so that the parts don’t pick up metal dust.
Two of these rolls fit into one of CUTCO’s older surface finishing machines. The machine itself could accommodate 25 blanks at a time. During the finishing process, a liquid compound was sprayed onto the rolls to reduce frictional heat and enhance the rolls’ cutting capabilities.
With each pass through the machine, the rolls removed 0.001 to 0.002 in. of material per side and delivered a surface finish of about 15 Ra, Eade said. The process worked, but not that efficiently.
“With the labor involved with making these rolls; the low production rate because you could usually get only 25 parts in a fixture; and the long cycle times of more than 3 minutes, the process was always something we wanted to eliminate,” Eade said.
Over the years CUTCO had looked at different flap wheels and abrasive belts to replace its old abrasive buffing rolls, but discovered that they couldn’t improve on the process. Also, alternative methods were cost-prohibitive; either the abrasives required slower production speeds to be effective, or they would wear out much too quickly, requiring almost constant replacement.
Around 2010, however, the surface finishing equipment and abrasive technology finally aligned, and CUTCO found the right combination that would allow it to cut loose those old buffing rolls.
Try This
The answer came in the form of 3M™ Trizact™ 363FC abrasive. These abrasive products were introduced in the 1990s and have a surface structure that maintains sharpness longer than traditional abrasives. As a result, they are able to remove material consistently during use.
Brian Janovec, a 3M technical service specialist, said Trizact abrasives are manufactured using 3M patented “microreplication” technology. These engineered abrasives consist of precisely shaped 3-D structures distributed uniformly over a cloth or film backing. The uniform configuration of the abrasives helps to deliver more consistent performance and eliminates belt to belt variation; traditional abrasives, which are constructed from randomly spaced and irregular-shaped
mineral, don’t deliver the same consistency, according to Janovec.
“On a traditional abrasive product, you literally have one layer of mineral grit. When that conventional abrasive belt is new, the abrasive is much sharper, but throughout the belt’s life, the cut starts to drop off as the mineral dulls,” Janovec said. “The finish and the stock removal change throughout the life of the belt. Trizact belts start sharp and stay sharp, resulting in more predictable finishes and improved, consistent part quality.”
The first generation of these abrasives had pyramid-shaped structures. Over time 3M engineers found that the shape of the structures could be optimized for a variety of applications. Working with that premise, engineers have developed new variations with much larger engineered shapes. These newer “macroreplicated” abrasives are used in many flat finishing, centerless finishing, and tube polishing applications.
The initial CUTCO development work was done on a Timesavers™ machine at 3M’s Customer Abrasive Methods (CAM) Center.
“During these trials we produced blades with a variety of different finishes using various Trizact abrasive sequences. The finished blades were returned to CUTCO for final buffing and analysis. That got the whole thing kicked off,” Janovec recalled.
“Before CUTCO moved forward with the machine purchase, a small production trial run was completed at the 3M CAM Center, witnessed by key stakeholders from CUTCO and Timesavers,” he added.
CUTCO ultimately elected to use Timesavers flat finishing machines for its prefinishing process (see Figure 1). Tim Mueller, Timesavers regional sales manager, said the microreplicated abrasive has changed the way its machinery can be used to tackle difficult finishing jobs.
“With the advent of these belts, what used to take six or seven abrasive steps now takes four. It makes the machine more affordable for the customer,” he said.
Getting to the Finish
CUTCO purchased the first flat-surface finishing machine in 2011. Based on the success with it, the company purchased another machine in 2013.
Mueller said that they learned a lot once that first four-head finishing machine was installed. On the original machine, the four belts were all run at the same speed. After operating the machine for several weeks, operators fine-tuned the belt and feed speeds to deliver a finish closer to what CUTCO desired.
Once the first machine was operating at an acceptable level, Timesavers implemented what they had learned and took it a step farther.
On the second machine they increased the abrasive belt speed on the first two heads and increased the drum hardness on all four heads. The combination of harder drums on a couple of heads and faster belt speeds on the other two created a process that removed stock even faster than the first machine, but still maintained an acceptable abrasive belt life.
“You don’t want to sacrifice abrasive belt life for stock removal. Belts are designed to remove a certain amount of stock, and once you move past that, the life can be negatively affected and will increase the cost per part. But making the speed and hardness changes we did kept the belt life up to where it was meant to be,” Mueller said.
Today CUTCO runs the two four-head machines as a flow-through process. An operator feeds the blanks into the first machine, where a magnetized table holds them down to ensure flatness during the finishing process (see Figure 2). An operator picks up the blanks as they exit the first machine, inspects the parts, flips them over, and feeds them into the second machine where the process is repeated for the other side. A person at the end of the second machine grabs the parts, after they go through a demagnetizer to prevent any metallic dust or remnants from hanging on, and stacks them for the next operation, which is polishing.
Eade said that CUTCO is using a grade A160, which is similar to a 120-grit conventional belt. The Trizact belts last about a shift and a half before they have to be changed out, he added.
“As you probably know, change in any manufacturing facility, especially at our site where most of us have been here 20-plus years, is difficult,” Eade said. “But this wasn’t a tough sell because the improvement was obvious and easily shows.”
Eade estimated that the new prefinishing setup triples the production output of the older method over a shift. He also said they are regularly getting surface finishes of 7 to 15 Ra, which makes it much easier to polish the part during the final blade finishing stage. These consistent surface finishes and resulting flat surface also improve other downstream processes, such as handle assembly and handle polishing, Gaps between the riveted handle and blade tang have been eliminated, producing more of a sealed handle assembly.
The cut-down machines are also a thing of the past—for the most part. Two people used to spend an entire eight-hour shift working to create these buffing rolls. Now just one person, on a part-time basis, builds the labor-intensive cut-down rolls because they are still used in final processing.
“The new process is also a safety project,” Eade said, “in that it’s easier for an operator to run a flat finisher than our older machines. We’ve decreased our incidents of hazards due to smoke and potential fires.”
Eade said that the joke around the .facility is that once this surface finishing process is figured out, he could finally retire. But there is still work to be done. The manufacturing team is conducting small-scale tests in which one of the surface finishing machines is used just for material removal and the other for cosmetic finishing. They also are looking at new approaches to final buffing operations.
In the end, there is always something to look at and new technology developments to consider.
About the Author
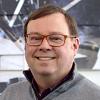
Dan Davis
2135 Point Blvd.
Elgin, IL 60123
815-227-8281
Dan Davis is editor-in-chief of The Fabricator, the industry's most widely circulated metal fabricating magazine, and its sister publications, The Tube & Pipe Journal and The Welder. He has been with the publications since April 2002.
subscribe now
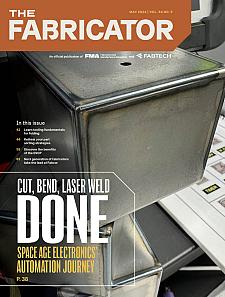
The Fabricator is North America's leading magazine for the metal forming and fabricating industry. The magazine delivers the news, technical articles, and case histories that enable fabricators to do their jobs more efficiently. The Fabricator has served the industry since 1970.
start your free subscription- Stay connected from anywhere
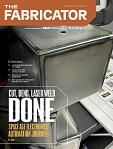
Easily access valuable industry resources now with full access to the digital edition of The Fabricator.
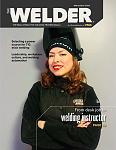
Easily access valuable industry resources now with full access to the digital edition of The Welder.
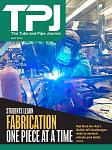
Easily access valuable industry resources now with full access to the digital edition of The Tube and Pipe Journal.
- Podcasting
- Podcast:
- The Fabricator Podcast
- Published:
- 04/16/2024
- Running Time:
- 63:29
In this episode of The Fabricator Podcast, Caleb Chamberlain, co-founder and CEO of OSH Cut, discusses his company’s...
- Trending Articles
Tips for creating sheet metal tubes with perforations
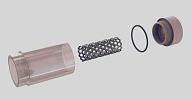
JM Steel triples capacity for solar energy projects at Pennsylvania facility
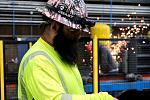
Are two heads better than one in fiber laser cutting?
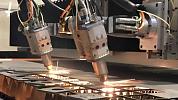
Supporting the metal fabricating industry through FMA
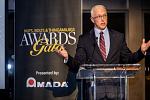
Omco Solar opens second Alabama manufacturing facility
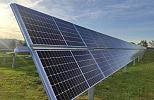
- Industry Events
16th Annual Safety Conference
- April 30 - May 1, 2024
- Elgin,
Pipe and Tube Conference
- May 21 - 22, 2024
- Omaha, NE
World-Class Roll Forming Workshop
- June 5 - 6, 2024
- Louisville, KY
Advanced Laser Application Workshop
- June 25 - 27, 2024
- Novi, MI