Editor-in-Chief
- FMA
- The Fabricator
- FABTECH
- Canadian Metalworking
Categories
- Additive Manufacturing
- Aluminum Welding
- Arc Welding
- Assembly and Joining
- Automation and Robotics
- Bending and Forming
- Consumables
- Cutting and Weld Prep
- Electric Vehicles
- En Español
- Finishing
- Hydroforming
- Laser Cutting
- Laser Welding
- Machining
- Manufacturing Software
- Materials Handling
- Metals/Materials
- Oxyfuel Cutting
- Plasma Cutting
- Power Tools
- Punching and Other Holemaking
- Roll Forming
- Safety
- Sawing
- Shearing
- Shop Management
- Testing and Measuring
- Tube and Pipe Fabrication
- Tube and Pipe Production
- Waterjet Cutting
Industry Directory
Webcasts
Podcasts
FAB 40
Advertise
Subscribe
Account Login
Search
Fab shop turns to automated deburring
California-based Tink Inc. ditches manual deburring of parts for its heavy-duty industrial products
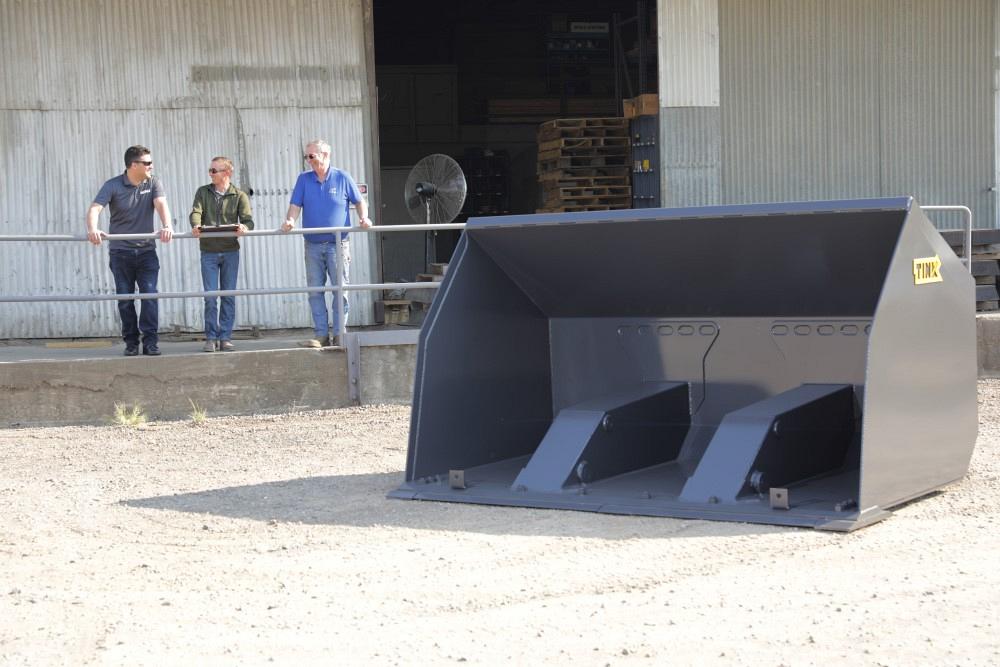
Tink Inc.’s roll-out buckets are designed to add dump height and reach to any wheel loading machine. With this type of bucket, the loader can reach over the 13-ft., 6-in. sides typical of most high-side trailers. (From left) Nathan Brown, ARKU sales engineer), Hank DuBose (Tink vice president), and Allen Kinyon (Tink operations manager) talk about the company’s buckets. ARKU Inc.
Working with heavy-duty materials is hard work—for both man and machine.
Tink Inc., Durham, Calif., lives that experience each day. The company’s fabricators and welders work with abrasion-resistant plate like AR 400 to build front-loader buckets and mobile home material handling equipment that are able to do the tasks they were designed to do while also standing up to the rigors of the job. The minimum steel thickness that the fabricating company works with is 0.25 in., and some of the parts reach 3 in. thick. These buckets and mobile home lifts are robust by design and heavy-duty performers in action.
“Our customers don’t want any low-quality clamps, buckets, or lifts. They want longer-lasting products that allow them to carry out the demanding tasks for as long as possible,” said Hank DuBose, the company owner.
Tink Inc. plasma-cuts the thick and dense material and welds the parts to create the buckets and lift products for its customers. The products then are painted before being sent to the customer.
Grinding is a key element of this production process. The parts need to have burrs and slag removed before welding. Also, rounded edges on the parts help the paint adhere to the metal surface better.
DuBose said the company needed to “ramp up” its grinding efforts because it was not nearly as efficient as other parts of the manufacturing process. At any one time, the company could have five to 10 people manually grinding parts.
“We were having a hard time filling those positions and keeping guys there,” DuBose said. “It’s an entry-level position, so we had a high turnover rate. It’s also physically demanding. It’s a pretty grueling process.”
He added that because a lot of the people involved in deburring parts are new to metal fabricating and they are engaging in a physically demanding activity over an entire shift, they run a greater risk of injury than their more experienced colleagues. Manually deburring the dense material with a 6-in. grinder is a tedious task to begin with, but over several hours a person might let their guard down, resulting in an injury. DuBose said most of the company’s foreign-object injuries, related to sparks or pieces of metal coming off during the grinding process, occur in this department.
DuBose knew that automated deburring could greatly help the situation—boosting output and being able to deliver more consistent results, grind after grind. He just didn’t know exactly where to start.
How It All Started
Before DuBose’s father and uncle started Tink Inc., they ran a construction equipment rental company in the 1970s. One day a customer came to the business looking to rent an attachment for his skid steer loader and commented that he’d actually consider buying one if manufacturers produced better attachments for loaders. The two business owners recognized that OEMs were failing to meet customer demands, so they decided to make bucket attachments with customer specifications not available in the market at the time. That led to DuBose’s uncle and father founding Tink Inc. and designing its first high-dump bucket for skid steer loaders. The customer bought it, and others soon followed.
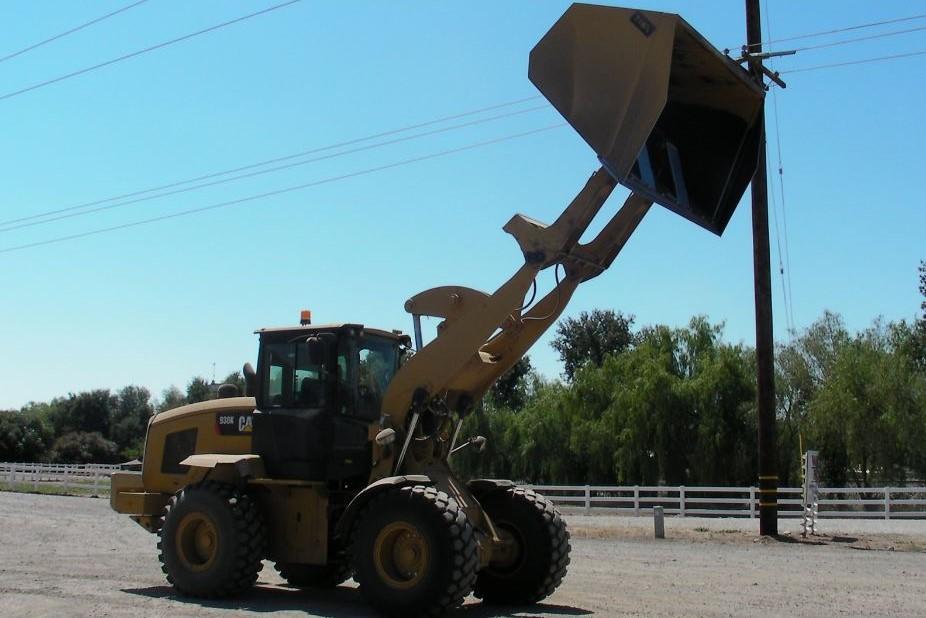
Tink Inc. cuts a lot of plate in the manufacture of its roll-out buckets and mobile home lifting devices. Tink Inc.
That success was followed later by a request from another customer looking to improve the design and fabrication of his Translift mobile home moving equipment. Familiar with the material and fabricating skills used to create heavy-duty construction equipment, Tink Inc. applied the same thinking to the redesigned Translift product. The result was a product embraced by the mobile home industry, which was looking for a device that could carry modular sections or entire mobile homes and operate properly while supporting the tremendous weights.
Today other companies, including one of the largest names in the industrial equipment space, have their own versions of high-side dump buckets. There also are other manufacturers of mobile home moving devices. But Tink Inc. remains a vibrant player in the space, employing 75 people, 25 of whom are welders, at its Northern California shop. DuBose said that he has been passionate about metal fabrication from a very early age and that he is constantly looking for ways to keep up with customers’ changing priorities. The search for some sort of automated grinding technology was just the latest challenge.
Looking for a Better Way
DuBose found his answer attending a metal fabricating tradeshow in late 2018. Perusing through an industry magazine, he came across an advertisement for ARKU promoting its automated deburring equipment. He noticed the company had a location in the Midwest, so he made a mental note to follow up with a visit to see the deburring technology in person.
The subsequent visit to ARKU’s Cincinnati headquarters took place in February 2019. DuBose didn’t have to check his test parts for the trip there; they were sent in advance to see how ARKU’s Edgebreaker 4000 would handle them.
The actual demonstration proved that the machine was going to be the right fit for Tink Inc. It removed any burrs and slag and rounded off the edges of the plasma- and oxyfuel-cut parts from both sides in just a single pass.
“After seeing the results, it was obvious that the machine could handle heavy-duty plates and parts as well as regular sheet metal easily and reliably,” DuBose said.
The Edgebreaker’s deburring capabilities result from a large drum to which abrasive material is attached. The drum rotates in a counterclockwise movement and oscillates as the metal parts are conveyed underneath it. Once the parts make contact with the grinding drum, the abrasive-lined drum digs into the metal surface and conforms to the material’s edges. The drum’s grinding action can be adjusted to remove anything from thin mill scale to difficult-to-remove burrs or slag.
After the grinding drum, blocks of abrasive brushes attached to a belt handle the edge rounding. Each brush block is made up of abrasive pads that are joined on one vertical end. Each belt is made of several of these blocks. Two belts, one above and one below the material, rotate clockwise. As the material makes contact with the rotating blocks, they start to break down the sharp edges and produce a rounded edge.
Instead of outfitting the machine with just edge-rounding blocks, a fabricator can use blocks with different types of abrasives for more aggressive grinding action. This provides simultaneous deburring of both the top and bottom of the metal surface.
After returning home, DuBose consulted with his team and shared some videos of the Edgebreaker in action. “The team was convinced that the machine was a perfect match for us, so we ordered right away,” he said.
Tink got its machine later in the fall. It came with infeed and exit conveyors and a wet dust extraction system that helps to keep the air free from dust that the deburring process generates.
DuBose said that operations training took place over several hours. He added that controls were “intuitive” and operators of nearby plasma and CNC mills quickly caught on. In fact, the operator only needs to input the thickness of the material into the control interface and ensure that the appropriate abrasives installed in the unit match the intended job. (The height of the material does not take into account any peaks associated with existing burrs; it’s the true material thickness.)
“We can now deliver consistent deburring quality and can keep our customers’ deadlines even better than before,” DuBose said.
Tink has gone from multiple people tackling the grinding job to one person operating the Edgebreaker, which processes about 90% of the parts that the company produces. (The machine can handle parts up to 4 in. thick and just under 51 in. wide.)
“It does a good job of getting everything off there,” DuBose said. “We can adjust the settings so that we can just get the mill scale off the surface, which is more for the welding process than anything. Then there are other parts that we need a more polished finish, and other parts where we want to be a little more aggressive. We have the ability to do all of that with this machine.”
The edge rounding of those plate parts also helps with the painting process, according to ARKU officials. Sharp edges don’t make for an ideal surface onto which paint can adhere. The rounded edges are more conducive to a coat of paint that is going to last, at least until the buckets or mobile home lifts start being used on a regular basis.
DuBose added that maintenance of the deburring machine is relatively simple. Machine sensors notify the operator when consumables are running low and might need to be replaced to ensure proper performance. Changeout of the belts or blocks occurs in a few minutes.
By opening some access doors, an operator can get into the interior of the machine and clean up any loose dirt that escaped the wet dust extraction system. DuBose said the operator typically cleans the unit every day.
DuBose added that the deburring machine has enabled Tink to deploy workers elsewhere in the facility. Grinding has gone from a labor headache to a process DuBose doesn’t have to worry about. The deburring machine keeps up with the current workload without it being used for the full shift each day.
“I think we’ve got our problems solved with this machine,” he said.
About the Author
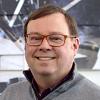
Dan Davis
2135 Point Blvd.
Elgin, IL 60123
815-227-8281
Dan Davis is editor-in-chief of The Fabricator, the industry's most widely circulated metal fabricating magazine, and its sister publications, The Tube & Pipe Journal and The Welder. He has been with the publications since April 2002.
Related Companies
subscribe now
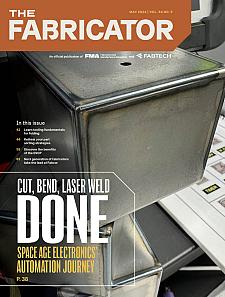
The Fabricator is North America's leading magazine for the metal forming and fabricating industry. The magazine delivers the news, technical articles, and case histories that enable fabricators to do their jobs more efficiently. The Fabricator has served the industry since 1970.
start your free subscription- Stay connected from anywhere
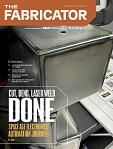
Easily access valuable industry resources now with full access to the digital edition of The Fabricator.
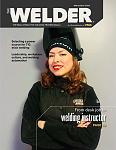
Easily access valuable industry resources now with full access to the digital edition of The Welder.
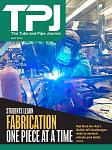
Easily access valuable industry resources now with full access to the digital edition of The Tube and Pipe Journal.
- Podcasting
- Podcast:
- The Fabricator Podcast
- Published:
- 04/16/2024
- Running Time:
- 63:29
In this episode of The Fabricator Podcast, Caleb Chamberlain, co-founder and CEO of OSH Cut, discusses his company’s...
- Trending Articles
Tips for creating sheet metal tubes with perforations
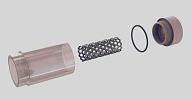
Supporting the metal fabricating industry through FMA
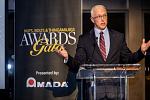
JM Steel triples capacity for solar energy projects at Pennsylvania facility
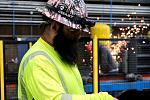
Are two heads better than one in fiber laser cutting?
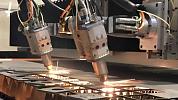
Fabricating favorite childhood memories
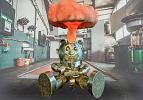
- Industry Events
16th Annual Safety Conference
- April 30 - May 1, 2024
- Elgin,
Pipe and Tube Conference
- May 21 - 22, 2024
- Omaha, NE
World-Class Roll Forming Workshop
- June 5 - 6, 2024
- Louisville, KY
Advanced Laser Application Workshop
- June 25 - 27, 2024
- Novi, MI