Contributing Writer
- FMA
- The Fabricator
- FABTECH
- Canadian Metalworking
Categories
- Additive Manufacturing
- Aluminum Welding
- Arc Welding
- Assembly and Joining
- Automation and Robotics
- Bending and Forming
- Consumables
- Cutting and Weld Prep
- Electric Vehicles
- En Español
- Finishing
- Hydroforming
- Laser Cutting
- Laser Welding
- Machining
- Manufacturing Software
- Materials Handling
- Metals/Materials
- Oxyfuel Cutting
- Plasma Cutting
- Power Tools
- Punching and Other Holemaking
- Roll Forming
- Safety
- Sawing
- Shearing
- Shop Management
- Testing and Measuring
- Tube and Pipe Fabrication
- Tube and Pipe Production
- Waterjet Cutting
Industry Directory
Webcasts
Podcasts
FAB 40
Advertise
Subscribe
Account Login
Search
Paint precision in a manufacturing shop gets a boost with Toronto tech
Mazlite brings AI to the paint booth with monitoring system
- By Rob Colman
- June 20, 2023
- Article
- Finishing
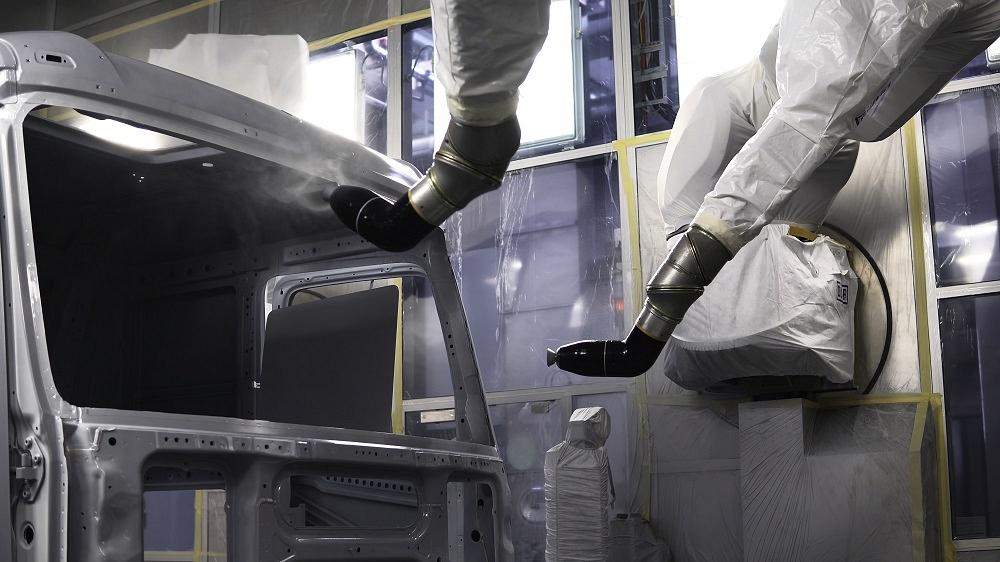
Mazlite's technology, deployed in a paint booth, tests the spray profile of a spray gun. Media Whalestock/iStock/Getty Images Plus
Paint finishes are a critical part of many fabrication processes; if the application or color is at all off, it can mean wasteful rework or scrapped parts. This is of particular concern in high-volume applications like automotive parts manufacturing.
The problem is that all quality control in the paint process has traditionally involved postprocess checks of finished parts. To help address this, Toronto-based Mazlite has designed a monitoring system that uses sensors to check spray profiles throughout the day during the process. The sensors also monitor paint materials continually to avoid defects due to changes in color or poor finishes.
Spray Research
Mazlite was founded in 2107 by Cameron Dallas and Amirreza Amighi.
“Amirreza and I met at the University of Toronto when I was working on my master’s and he was working towards his PhD,” Dallas said. “He was working in spray-related research connected to fuel-injection systems for airplanes—research related to how efficient the engine can burn—while I was studying aerodynamics and high-performance computing. As the concept for developing spray monitoring technology developed, I saw how my computing and physics background could help with algorithm development. That’s how I got involved.”
Spray consistency is an issue in a variety of different fields, as Dallas pointed out.
“Automotive companies struggle with consistency in spray painting,” he said. “In fact, the process is so intricate that the defect rate is significant, with some estimates as high as 25%. It can be a very wasteful process and could be much more efficient. In similar ways, pharmaceutical companies have issues with their processes as well. For instance, with inhalers, when you are trying to deposit some sort of drug in the body, droplet size really matters.”
Addressing Changing Needs
Mazlite’s technology captures the spray profile of a spray gun, comparing the way in which the paint or other liquid presents itself as it is atomized in droplets, particles, and bubbles.
“We had an inkling that there was some sort of industry problem in this area because as we developed our technology, companies kept coming to us with similar problems they were trying to address,” Dallas said. “This led to us giving presentations to a variety of OEMs and Tier 1 and Tier 2 automotive suppliers, and eventually to beta testing of the technology in their facilities.”
Like many industries, Dallas sees Mazlite’s technology replacing some of the legacy knowledge that is disappearing as older skilled workers retire.
“You’ve got some people who have worked in the industry for 40 years and they can just look at a spray and tell if it’s good or bad,” he noted. “Between a change in the labor force and greater automation, it has become more difficult to track that. That’s why our lab exists. There are a lot of different complicated mathematical and physical processes at work in spray profiles that few people really understand.”
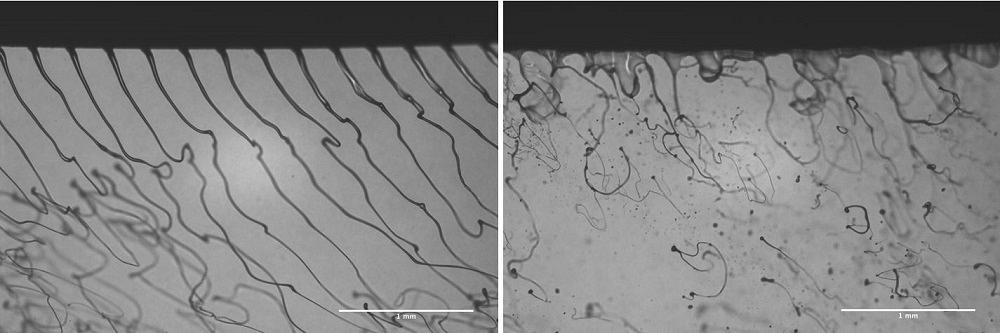
FIGURE 1. These images, collected using the monitoring system, compare a baseline image (left) to one that indicates a clogged nozzle.
Implementation Basics
The structure of the monitoring system is unremarkable to look at—a towel-rack-like stainless steel structure with a gap in the front of the rack where the sensor captures its data. But of course, given the environment in which it needs to function, it’s built to last.
“The systems have to operate in extreme and hazardous environments (including Class 1 Division 1 or Zone 1 hazardous locations) within many industries, including automotive, coating, agriculture, pharmaceutical, food, or aerospace,” Dallas said. “Everything needs to be explosion proof, and you need to get the strictest certifications on the sensor to be able to even put it into the location. It took a great deal of development to make the design compact, flexible, robust, and reliable.”
Implementation has been unique in every facility Mazlite has entered.
“Every plant is different,” Dallas said. “Some just want to use the technology for R&D purposes, so they take one monitor and place it in a test booth to use. In other instances, you might put multiple sensors within a paint line, and multiple robots will be able to reach the same sensor to run a check on their spray every 30 minutes or every couple of hours, depending on a facility’s requirements.”
Examining All Factors
Companies are looking for more information than just whether the spray nozzle is working correctly, however.
“Automotive suppliers are interested in color, primarily—how nicely a car ‘shines,’” Dallas noted. “But they are also interested in defects where they have ripples on the surface, or craters where perhaps a really big droplet of paint created an anomaly on the part surface. So there are many different failure modes.”
Mazlite has developed indicators to a number of failure modes based on what its sensors capture on film. For example, Figure 1 compares a base line image to one that indicates a clogged nozzle.
“When we receive the data from their booths, we can predict whether the spray will be effective, and if not, what the issue that needs to be fixed likely is,” Dallas said.
But data flow isn’t a one-way street in this tech’s development. The handful of companies Mazlite is currently working with also are providing the monitoring company with data about the temperature, humidity, paint batches, and other details that may affect spray performance.
“Sprays are extremely sensitive to temperature and humidity, so changes can occur as seasons change, and even between day and night shifts,” Dallas said. “Companies are always fine-tuning their processes because of this, and we can help them catch changes to clarify what is happening in their paint processes.”
So, as much as Mazlite has provided a selection of OEMs and Tier 1 and Tier 2 automotive suppliers with a valuable technology, Dallas thinks of the relationship as very much a collaboration towards solving a real challenge for the industry as a whole.
“This is why we want to work closely with these companies, because every time we go into a new plant and every time we start a new project, we learn something and they learn something,” he noted.
Research Support
Developing its systems has involved thousands of hours of research, and to keep the knowledge flow primed, Mazlite has taken advantage of the cutting-edge expertise of student researchers hired through Mitacs, a Canadian innovation organization that helps solve business challenges with research support from academic institutions.
Mitacs’ internships are critical to keeping Mazlite’s momentum going, Dallas said, by allowing the company to hire the niche expertise it needs to solve its most technical challenges.
“Our business is not just using AI and statistical models and throwing them at a problem and seeing what comes out of it,” said Dallas. “The core of our business is deep scientific knowledge. You need to understand the science of this to actually do any good work here. It’s great to be able to tap into that level of knowledge to grow our abilities as a company. Having an organization like Mitacs to be able to fund this has just been wonderful and very helpful.”
Mitacs intern Khalil Sidawi, a University of Toronto post-doc, for example, is currently applying his specialized knowledge of automotive paints.
“He’s a superstar,” said Dallas, adding that as a startup, it would be difficult to afford Sidawi and other interns’ expertise without the support of a paid internship. “With Mitacs’ support, for example, we’ve brought Khalil in to work on innovation challenges directly related to commercialization. It has been extremely helpful in innovating and speeding up the commercialization process.”
Moving Forward
Mazlite is currently a team of about 10 people, but they are busy enough that they could definitely expand soon. Co-founder and CEO Amirreza Amighi wasn’t available for an interview because he was busy arranging shipments of monitoring systems.
“Companies see the value of what we bring to the table,” Dallas said. “We are helping the paint shop to be more environmentally friendly, and we’re increasing quality. As we develop our technology further, even more will be possible.”
Editor’s Note: This article originally appeared in the May 2023 issue of Canadian Fabricating & Welding.
About the Author
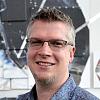
Rob Colman
subscribe now
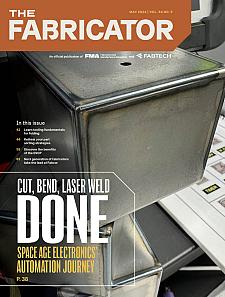
The Fabricator is North America's leading magazine for the metal forming and fabricating industry. The magazine delivers the news, technical articles, and case histories that enable fabricators to do their jobs more efficiently. The Fabricator has served the industry since 1970.
start your free subscription- Stay connected from anywhere
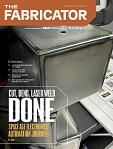
Easily access valuable industry resources now with full access to the digital edition of The Fabricator.
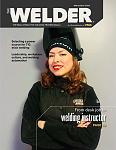
Easily access valuable industry resources now with full access to the digital edition of The Welder.
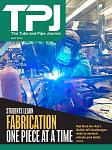
Easily access valuable industry resources now with full access to the digital edition of The Tube and Pipe Journal.
- Podcasting
- Podcast:
- The Fabricator Podcast
- Published:
- 04/16/2024
- Running Time:
- 63:29
In this episode of The Fabricator Podcast, Caleb Chamberlain, co-founder and CEO of OSH Cut, discusses his company’s...
- Trending Articles
Tips for creating sheet metal tubes with perforations
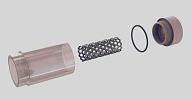
JM Steel triples capacity for solar energy projects at Pennsylvania facility
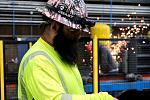
Are two heads better than one in fiber laser cutting?
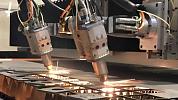
Supporting the metal fabricating industry through FMA
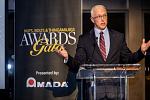
Omco Solar opens second Alabama manufacturing facility
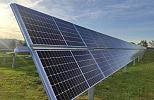
- Industry Events
16th Annual Safety Conference
- April 30 - May 1, 2024
- Elgin,
Pipe and Tube Conference
- May 21 - 22, 2024
- Omaha, NE
World-Class Roll Forming Workshop
- June 5 - 6, 2024
- Louisville, KY
Advanced Laser Application Workshop
- June 25 - 27, 2024
- Novi, MI