Account Manager for TruLaser Tube
- FMA
- The Fabricator
- FABTECH
- Canadian Metalworking
Categories
- Additive Manufacturing
- Aluminum Welding
- Arc Welding
- Assembly and Joining
- Automation and Robotics
- Bending and Forming
- Consumables
- Cutting and Weld Prep
- Electric Vehicles
- En Español
- Finishing
- Hydroforming
- Laser Cutting
- Laser Welding
- Machining
- Manufacturing Software
- Materials Handling
- Metals/Materials
- Oxyfuel Cutting
- Plasma Cutting
- Power Tools
- Punching and Other Holemaking
- Roll Forming
- Safety
- Sawing
- Shearing
- Shop Management
- Testing and Measuring
- Tube and Pipe Fabrication
- Tube and Pipe Production
- Waterjet Cutting
Industry Directory
Webcasts
Podcasts
FAB 40
Advertise
Subscribe
Account Login
Search
A new dimension in lasers
Tilt laser beam technology combines 2-D, 3-D laser cutting
- By Thomas Burdel, Pieter Schwarzenbach, and Dr. Per Stenius
- January 17, 2007
- Article
- Laser Cutting
Laser cutting has become widely used in manufacturing over the past 30 years. During its evolution, laser cutting has been used for just-in-time (JIT) production with minimized parts stocking, as well as sheet metal processing.
High-speed laser cutting is the modern-day result of increased laser power and high acceleration motion technology, which have improved cutting speeds, some as high as 60 feet per minute. High-speed cutting requires a dynamic, stable machine and a modern CNC with high resolution. With nitrogen assist gas, the speed-limiting oxidation process encountered when using oxygen assist gas can be overcome. This process demands higher laser power (more than 3 kilowatts) even on thin mild steel thicker than 16-gauge, as well as higher assist gas consumption—1,000 standard cubic feet per hour (SCFH).
Between 85 and 90 percent of all laser cutting applications today involve flat sheet metal cutting in which the laser beam is perpendicular to the metal surface. Additional exchange tables, automatic loading and unloading systems, and pallet towers can increase automation and productivity for these applications.
Three-dimensional applications account for the other 10 to 15 percent of laser cutting, used mainly—but not exclusively—by the automotive industry, which uses big systems that cut large parts, such as whole car bodies. Because 3-D laser processing systems are large and restricted in their movement, high-speed cutting isn't available or necessary. The systems normally are equipped with laser powers below 3 kW, which is sufficient for thin sheet metal cutting.
Historically, programming these large 3-D systems using the teach-in method has been costly because the machine isn't productive during the programming time. However, software that allows for offline programming of 3-D machines directly from CAD files offers new opportunities in 3-D cutting.
2-D and 3-D Cutting
Traditional fabrication job shops currently use lasers to cut flat sheet metal parts before the part is formed. In the past cutting the part after it was formed has proved complicated because the equipment was too expensive and programming was difficult and required the machine to be offline. For those reasons, 3-D or five- or six-axis lasers have been used almost exclusively in the automotive industry for prototyping or low-volume production.
Today's new laser systems are designed for both flat sheet and 3-D cutting.
In a multiple-operation job that requires cutting, bending, and possibly machining, the bending operation will distort the hole if it was flat-cut with a laser. With a 3-D laser cutting system, the sheet metal can be bent first and the parts cut out after the forming process. This eliminates the machining and bending.
As a tip for job shops, it's important to look for a 3-D laser system that also is designed to handle flat cutting and offers high cutting and positioning speeds for increased productivity, short changeover times, and automatic material handling. The system also should be easy to program and run.
New Opportunities With Tilt Beam
Tilt beam 2-D and 3-D systems offer the following, especially for laser job shops:
- Laser cutting of small, 3-D parts
- Bevel cutting on 2-D sheet metal and 3-D parts
- 3-D trimming of small deep-drawn parts
- Processing of holes and cutouts in hydroformed parts
With an optional rotary axis, such a system can cut tubes and profiles and make bevel cuts in tubes.
The automotive industry, which demands efficient processing of hydroformed parts, can use these hybrid systems for several applications. With a 3-D cutting head, a modern six-axis CNC with fast processors, and increased speed of the laser along the Z axis, a flat-sheet laser cutter also can cut the trim off 3-D hydroformed parts.
In flat sheet metal applications, these systems with a 3-D head can perform bevel cutting, especially on thick parts that need to be prepared for welding. Bevel cuts are necessary in heavy military and construction equipment production, in shipyards, and in machine construction.
Bevel cutting normally starts with vertical piercing. The laser head subsequently is tilted to realize the necessary bevel angle. The X and Y axes have to move a different trajectory because of the offset between the Z axis and the focal point. This offset is a function of the bevel angle. The trajectory calculation is a simple tool correction offset evaluation.
The tilt beam also can be used to produce other complex parts, such as slanted teeth for a helical gear, or simple beveled holes for countersunk screws.
Market for 3-D Laser Cutting
In addition to the automotive industry, which already uses 3-D laser cutting, the following markets are expected to begin implementing tilt beam technology:
- Agriculture
- Construction
- Military
- Lighting
The 3-D/2-D laser cutting systems, especially those with an optional rotary axis for profile processing, should also prove attractive to job shops looking for flexibility in the metal fabrications they can produce.
About the Authors
Pieter Schwarzenbach
Vice President of Laser Technology
711 E. Main St.
Chicopee, MA 01020
413-598-5200
Related Companies
subscribe now
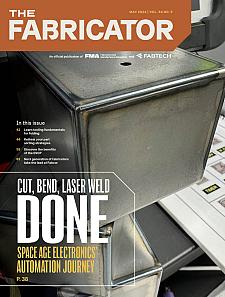
The Fabricator is North America's leading magazine for the metal forming and fabricating industry. The magazine delivers the news, technical articles, and case histories that enable fabricators to do their jobs more efficiently. The Fabricator has served the industry since 1970.
start your free subscription- Stay connected from anywhere
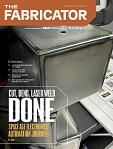
Easily access valuable industry resources now with full access to the digital edition of The Fabricator.
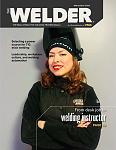
Easily access valuable industry resources now with full access to the digital edition of The Welder.
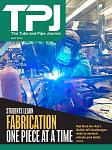
Easily access valuable industry resources now with full access to the digital edition of The Tube and Pipe Journal.
- Podcasting
- Podcast:
- The Fabricator Podcast
- Published:
- 04/30/2024
- Running Time:
- 53:00
Seth Feldman of Iowa-based Wertzbaugher Services joins The Fabricator Podcast to offer his take as a Gen Zer...
- Industry Events
Pipe and Tube Conference
- May 21 - 22, 2024
- Omaha, NE
World-Class Roll Forming Workshop
- June 5 - 6, 2024
- Louisville, KY
Advanced Laser Application Workshop
- June 25 - 27, 2024
- Novi, MI
Precision Press Brake Certificate Course
- July 31 - August 1, 2024
- Elgin,