Senior Editor
- FMA
- The Fabricator
- FABTECH
- Canadian Metalworking
Categories
- Additive Manufacturing
- Aluminum Welding
- Arc Welding
- Assembly and Joining
- Automation and Robotics
- Bending and Forming
- Consumables
- Cutting and Weld Prep
- Electric Vehicles
- En Español
- Finishing
- Hydroforming
- Laser Cutting
- Laser Welding
- Machining
- Manufacturing Software
- Materials Handling
- Metals/Materials
- Oxyfuel Cutting
- Plasma Cutting
- Power Tools
- Punching and Other Holemaking
- Roll Forming
- Safety
- Sawing
- Shearing
- Shop Management
- Testing and Measuring
- Tube and Pipe Fabrication
- Tube and Pipe Production
- Waterjet Cutting
Industry Directory
Webcasts
Podcasts
FAB 40
Advertise
Subscribe
Account Login
Search
Amada opens manufacturing plant in North Carolina
Production begins for press brakes and laser automation
- By Tim Heston
- December 23, 2019
- Article
- Laser Cutting
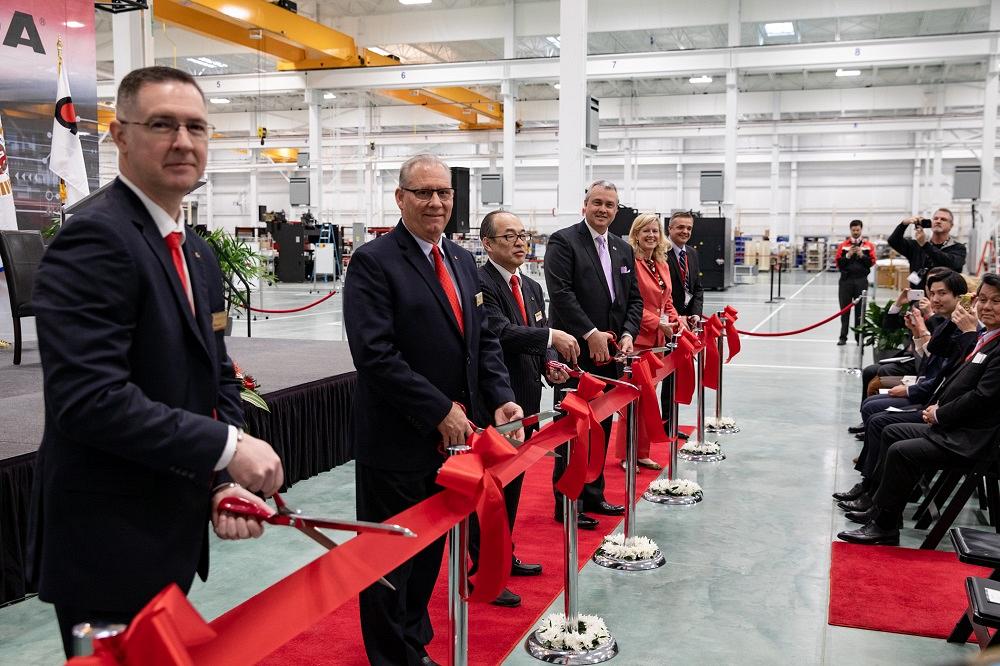
From left, Amada CMO Patrick Medlin, COO Mike Guerin, CEO Yukihiro Fukui; High Point Mayor Jay Wagner; High Point Economic Development Corp. Executive VP Sandy Dunbeck; and Gray Construction VP Brett Goode prepare to cut the ribbon, officially opening Amada’s North Carolina manufacturing plant.
In early December came more evidence that the U.S. is becoming one of the strongest, most important sheet metal fabrication markets in the world. Seventeen months after breaking ground, Amada America officially opened its 190,000-square-foot Carolina Manufacturing Center in High Point, N.C. Another building on the campus, the 62,000-sq.-ft. Carolina Technical Center, will open in 2020.
The North Carolina campus has Amada’s third manufacturing facility in the U.S. The opening follows another manufacturing expansion earlier in 2019, when Amada Tool America completed a 19,000-sq.-ft. addition to its existing plant in Batavia, N.Y. In 2013 the company opened a laser cutting machine manufacturing plant in Brea, Calif.
“Including the buildings here in North Carolina, Amada now has more than 1 million square feet of covered real estate in the United States,” said Mike Guerin, COO, Amada North America, during the official ribbon cutting Dec. 6.
Also on hand were Patrick Medlin, chief manufacturing officer of Amada America; Jay Wagner, mayor of the High Point; Brett Goode, senior vice president of Gray Construction Corp. (which completed the facility on time despite significant weather delays); Sandy Dunbeck, executive vice president of the High Point Economic Development Corp.; and Yukihiro Fukui, CEO of Amada North America.
Fukui in particular gained special praise from speakers. The executive has spearheaded Amada’s global manufacturing strategy. “He’s been the one with the foresight to build factories in China, Japan, and now in the U.S.,” Guerin said.
Medlin added similar praise. “Without his vision and influence, Amada would not be manufacturing press brakes and [laser] automation in North Carolina.”
During his subsequent speech, Medlin gave some perspective, not only about what the new campus means for the sheet metal fabrication business in the U.S., but also what it means to High Point and the broader Greensboro metro area. High Point has long been known as the “international city,” thanks to the large number of foreign companies that have set up U.S. operations in the area.
“It’s also known as the furniture capital of the world,” Medlin said. “And we’ve seen many changes over the years. Many furniture and textile jobs were offshored, and for nearly three decades we watched a skilled workforce struggle … But today the future is much brighter. High Point has become high tech, and the opportunities here are endless.
“Upon completion of this campus, Amada will add about 200 good-paying jobs,” Medlin continued. “This is what bringing jobs back to the United States looks like.”
The plant now employs a little more than 50 people, and the company expects employment to rise as it ramps up production of its HRB, short for Hybrid Retrofittable Bending machine. The plant will produce both stand-alone HRB press brakes as well as an HRB with an automatic tool changer (ATC). Both HRB models have options, like special gauging or sheet followers, that fabricators can add at the time of purchase or choose to add later.
Amada COO Mike Guerin, CMO Patrick Medlin; and High Point Mayor Jay Wagner push a button to initiate the cycle of the company’s two-column bridge mill, which machines beams and side plates for press brakes.
Produced on a line adjacent to the press brake, the loading/unloading laser machine automation also has modular attributes. Designed to keep pace with the company’s fastest fiber lasers, the automation can be sold with a new machine or retrofitted to an old one.
The machines are designed for flexibility and, in many respects, so is the new manufacturing plant. Assembly cells down the central aisles are equipped with wheeled carts holding kits of parts and tools, and everything can be wheeled to other locations as needed.
Most critically, the plant’s largest equipment, including a double-column bridge mill, paint booths, and blasting booth, has excess space and capacity. The blast booth alone, an automated system with a massive turntable, has the capacity to fit a complete laser machine frame on it. In the future, should laser machine production expand beyond Amada’s Brea plant, the North Carolina plant is designed to be able to absorb the demand and tool up for laser machine production.
All welding cells are set up with local fume extraction, and one welding cell has a massive, 12,000-pound-capacity positioner, similar to one used at Amada’s plant in Japan. Thanks to quick positioning, employees can weld an entire press brake side plate within a few hours.
Both prepaint blast and cleaning booths have reclamation systems that significantly reduce waste. About 95% of cleaning solution is filtered and used again. The blast booth has an automated reclamation system with an elevator that carries blast media back to the storage hopper. All this not only produces less waste from an environmental perspective, but also frees more available production capacity for future expansion.
After the ribbon cutting, Medlin, Guerin, and High Point Mayor Jay Wagner pushed a button to initiate the first cycle on the plant’s bridge mill, a massive machine with automated material handling—and for good reason. Machining time for plates vary between three and 14 hours depending on the part. And the part mix requires numerous tools; the machine can hold 80 in its magazine. The mill is designed to run two attended shifts and one unattended shift throughout the night, when finished plates can be transported, staged, and ready for when employees arrive in the morning.
Such lights-out capability build capacity that will be critical for future expansion and adaptation, two attributes that (not coincidentally) form the foundation for many a custom fabricator.
“It’s been a great road,” Guerin said as he concluded the event. “Some great things will come out of this facility, now and in the near future. We hope everyone prospers with us, and that we all share a success story for a long time to come.”
About the Author
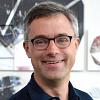
Tim Heston
2135 Point Blvd
Elgin, IL 60123
815-381-1314
Tim Heston, The Fabricator's senior editor, has covered the metal fabrication industry since 1998, starting his career at the American Welding Society's Welding Journal. Since then he has covered the full range of metal fabrication processes, from stamping, bending, and cutting to grinding and polishing. He joined The Fabricator's staff in October 2007.
Related Companies
subscribe now
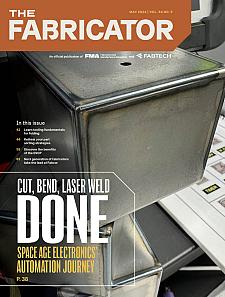
The Fabricator is North America's leading magazine for the metal forming and fabricating industry. The magazine delivers the news, technical articles, and case histories that enable fabricators to do their jobs more efficiently. The Fabricator has served the industry since 1970.
start your free subscription- Stay connected from anywhere
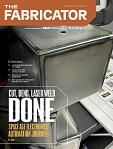
Easily access valuable industry resources now with full access to the digital edition of The Fabricator.
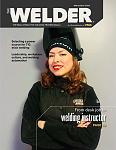
Easily access valuable industry resources now with full access to the digital edition of The Welder.
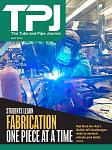
Easily access valuable industry resources now with full access to the digital edition of The Tube and Pipe Journal.
- Podcasting
- Podcast:
- The Fabricator Podcast
- Published:
- 04/16/2024
- Running Time:
- 63:29
In this episode of The Fabricator Podcast, Caleb Chamberlain, co-founder and CEO of OSH Cut, discusses his company’s...
- Trending Articles
Tips for creating sheet metal tubes with perforations
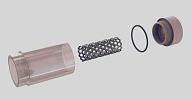
JM Steel triples capacity for solar energy projects at Pennsylvania facility
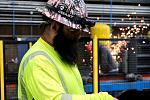
Are two heads better than one in fiber laser cutting?
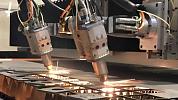
Supporting the metal fabricating industry through FMA
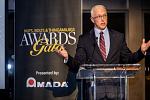
Omco Solar opens second Alabama manufacturing facility
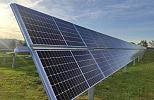
- Industry Events
16th Annual Safety Conference
- April 30 - May 1, 2024
- Elgin,
Pipe and Tube Conference
- May 21 - 22, 2024
- Omaha, NE
World-Class Roll Forming Workshop
- June 5 - 6, 2024
- Louisville, KY
Advanced Laser Application Workshop
- June 25 - 27, 2024
- Novi, MI