- FMA
- The Fabricator
- FABTECH
- Canadian Metalworking
Categories
- Additive Manufacturing
- Aluminum Welding
- Arc Welding
- Assembly and Joining
- Automation and Robotics
- Bending and Forming
- Consumables
- Cutting and Weld Prep
- Electric Vehicles
- En Español
- Finishing
- Hydroforming
- Laser Cutting
- Laser Welding
- Machining
- Manufacturing Software
- Materials Handling
- Metals/Materials
- Oxyfuel Cutting
- Plasma Cutting
- Power Tools
- Punching and Other Holemaking
- Roll Forming
- Safety
- Sawing
- Shearing
- Shop Management
- Testing and Measuring
- Tube and Pipe Fabrication
- Tube and Pipe Production
- Waterjet Cutting
Industry Directory
Webcasts
Podcasts
FAB 40
Advertise
Subscribe
Account Login
Search
Belco Industries cuts component cutting time with high-powered fiber laser
Fiber laser cutting machine replaces two older cutting tables, accelerates production
- By Sue Roberts
- June 14, 2019
- Article
- Laser Cutting
Shops involved with metal finishing and aluminum extrusion deserve, and may need, equipment built specifically to enhance each of their unique production environments. Sixty years ago Belco Industries, Belding, Mich., saw how it could help finishing and extrusion companies increase production by engineering, building, and installing systems that are still anything but one-size-fits-all.
Custom washers, ovens, spray paint booths, and air makeup units are included in the custom finishing lines. Billet and log heaters, furnaces, handling systems, log saws, pullers, air quench systems, and die and age ovens are part of the aluminum extrusion lines.
To produce the components that comprise the custom-designed systems, Belco’s own shop floor needs to provide a variety of part sizes and shapes, manage several material types and thicknesses, and frequently meet tight deadlines.
"We are an OEM, but it’s not like we run the same parts over and over. Once a sale is made, we design the system and produce parts that are unique to that system,” said Chris Stewart, manufacturing engineer. “And we don’t just cut components for our own products and in-house use. Since new equipment cuts so much faster, we have more idle time than ever before, so we outsource that available machine time to other manufacturers.”
Equipment Specs: More Production, Flexibility
Sheets of aluminum, mild steel, and stainless steel up to 1 inch thick that become components for the systems make their first stop at a cutting table. Until recently they went to either a 20-year-old, 2.5-kW CO2 laser Stewart described as “long in the tooth” or a plasma table that was used primarily to cut thin, aluminized material for ductwork because of its cut quality. Problems that prompted the investment in new equipment included difficulties in finding replacement parts for the two tables and the laser becoming, according to Stewart, a bit temperamental and often the culprit in creating shop bottlenecks.
Once the decision was made to purchase a new cutting table, Stewart served as the point man to research laser technologies and coordinate the purchase and installation processes.
“Prior to my current job of programming, I ran our old laser so I’m familiar with what an operator wants to see in a machine. And I understand the company’s expectations of wanting a machine that will last for the next 20 years. From the programmer standpoint, I wanted flexibility and quick production.”
A stop at FABTECH® in Chicago in 2017 was part of the search for a laser to meet the company’s specific criteria. That search ended with the purchase of a Mazak 8-kW Optiplex 4020 Fiber. Although Stewart began by looking at a 6-kW, he liked the heavy chassis that came along with the additional 2 kW of power in the 8-kW model.
“We saw that the cutting speed of an 8-kW would let us replace the two older cutting tables with one fiber laser,” he said.
“The capability to cut thicker material was important. We wanted to be able to cut up to 1 in. thick in all our materials. We rarely cut 1-in. aluminum, but we wanted to have that capability. With the older machines we were basically limited to processing 5/8-in. mild steel and ½-in. stainless. We could cut thicker materials, but it was at a crawling speed.”
Another consideration was table size.
“We didn’t want to deal with the size limitations that we had for years with the old CO2 laser. It was important to have a work table where we could cut up to 6- by 12-ft. material.
“The old laser’s 5- by 10-ft. table didn’t allow us to do a full trim on a 5-ft.-wide sheet. It would come up short. And there were some parts we had to split because they wouldn’t fit on a 10-ft. sheet. Producing those parts in two sections added processing time and created downstream work that we wanted to eliminate. For cutting smaller components, the larger work area lets us put more parts on a sheet. That keeps the machine cutting and saves us a lot of time.”
Equipment Location Critical to Smooth Operations
Moving the new fiber laser into its position in the 70,000-sq.-ft. facility was a bit of a trick. The laser had to be maneuvered through a shop door with about 1 ft. of clearance on each side then make an immediate 90-degree turn. “We wanted to position the new laser in the space vacated by the one it was replacing so we could utilize the same sheet storage system; maintain its proximity to the bulk nitrogen supply; and certainly keep it close to the press brake, which is an integral component to the production cell. This allows us to transfer the laser-cut parts that need to be formed directly to the press brake, which is just a few feet away.”
The importance of proximity to material and ease of loading with the two-pallet material handling system helped to boost laser cutting productivity. Faster production, of course, means more loading and unloading to keep part production going.
“In the past we had one person on the laser. He was able to operate the machine and handle loading and unloading,” Stewart said. “Now production has increased so much that we have two. One person runs the laser and one person is dedicated to getting the material on and the parts off. He is definitely busy, especially when we run thin parts like those for our ductwork or the large ovens. When an entire sheet can be cut in a minute and a half, there is not much time for sitting around.”
When cutting ¼ in. and thinner, Stewart said they use nitrogen rather than oxygen as the assist gas. Less heat is generated during the cut so more power can be used to increase the cutting speed.
“The process is ridiculously fast; we’re talking upwards of 3,000 IPM in the thin material,” he said.
Although he is still developing actual time comparisons between the old cutting tables and the fiber laser, Stewart estimated that the cutting of parts for a system that would have taken a couple of weeks has been reduced to a couple of days.“There is one part we produce for in-house use. It’s a hook that is usually cut from 14-gauge material. The hook is used to suspend components as they go through our paint line,” he said. “To get the end of the hook sharp enough to keep the parts on, we used to need to do a corner loop during the cutting process—actually go past the point and loop back around it. We used to have to build in some dwells to prevent heat buildup. None of that is necessary with the new machine. We just toss the material on the table and tell it to go. The old laser would cut one hook in about 10 to 15 seconds. With the new machine, it’s down to two or three seconds.”
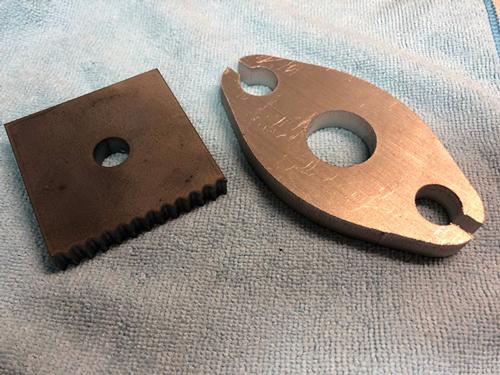
A ½-in. mild steel part with a tooth profile on the left and ½-in. aluminum part on the right were cut to demonstrate the new laser’s capabilities.
Etching Saves Time, Increases Accuracy
In the past part numbers and directions for downstream processes were written on each part with a paint stick as it was unloaded from the CO2 laser and plasma tables. It took time, and transposing numbers or ending up with difficult-to-read notations was always a possibility.
With the fiber laser, critical information is pulled directly from the part programs and etched on components as part of the cutting process. The etching is faster than handwriting and much more accurate.
“With the machine being so fast, we have time to etch information on the parts while they are still on the machine. Each part is labeled and has a notation added if it needs to go to another process. This saves time downstream, and there is really no room for error because the information is embedded in the part program,” Stewart said. “This may slow the cutting process down a little but, in the long run, it speeds everything up.”
On the software side, nothing changed for the company with the switch to the fiber laser. SigmaNEST was used with their older equipment and new post files carry the programs over to the new machine.
“From my programming side, everything is the same except I have more parts to do because of the capabilities of the new machine.”Work Lifter Eases Loading
Available space didn’t accommodate load/unload automation for now, but the machine’s modular design will allow it to be added if floor space becomes available. A workpiece lifter, an integral part of an automated load/unload system, is an automation option that Belco included on the laser to assist with manual loading and unloading.
“The workpiece lifter is located just below the work table. Fingers with ball bearings on the tips rise up and support the material so it can be squared and moved into place a little easier,” Stewart said.
“Upgrading our laser cutting equipment has allowed us to produce more parts and cut thicker materials without laminating. The speed and fast turnaround let us do more jobs, more quickly. Customers get exactly what they want sooner.”
Belco Industries, www.belcoind.com
Mazak Optonics Corp., www.mazakoptonics.com
About the Author
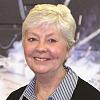
Related Companies
subscribe now
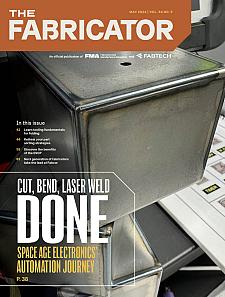
The Fabricator is North America's leading magazine for the metal forming and fabricating industry. The magazine delivers the news, technical articles, and case histories that enable fabricators to do their jobs more efficiently. The Fabricator has served the industry since 1970.
start your free subscription- Stay connected from anywhere
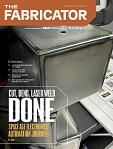
Easily access valuable industry resources now with full access to the digital edition of The Fabricator.
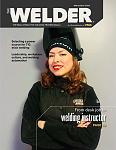
Easily access valuable industry resources now with full access to the digital edition of The Welder.
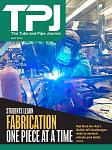
Easily access valuable industry resources now with full access to the digital edition of The Tube and Pipe Journal.
- Podcasting
- Podcast:
- The Fabricator Podcast
- Published:
- 04/16/2024
- Running Time:
- 63:29
In this episode of The Fabricator Podcast, Caleb Chamberlain, co-founder and CEO of OSH Cut, discusses his company’s...
- Trending Articles
Tips for creating sheet metal tubes with perforations
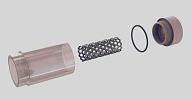
Are two heads better than one in fiber laser cutting?
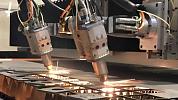
Supporting the metal fabricating industry through FMA
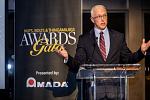
JM Steel triples capacity for solar energy projects at Pennsylvania facility
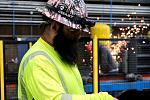
Omco Solar opens second Alabama manufacturing facility
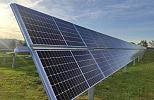
- Industry Events
16th Annual Safety Conference
- April 30 - May 1, 2024
- Elgin,
Pipe and Tube Conference
- May 21 - 22, 2024
- Omaha, NE
World-Class Roll Forming Workshop
- June 5 - 6, 2024
- Louisville, KY
Advanced Laser Application Workshop
- June 25 - 27, 2024
- Novi, MI