Editor-in-Chief
- FMA
- The Fabricator
- FABTECH
- Canadian Metalworking
Categories
- Additive Manufacturing
- Aluminum Welding
- Arc Welding
- Assembly and Joining
- Automation and Robotics
- Bending and Forming
- Consumables
- Cutting and Weld Prep
- Electric Vehicles
- En Español
- Finishing
- Hydroforming
- Laser Cutting
- Laser Welding
- Machining
- Manufacturing Software
- Materials Handling
- Metals/Materials
- Oxyfuel Cutting
- Plasma Cutting
- Power Tools
- Punching and Other Holemaking
- Roll Forming
- Safety
- Sawing
- Shearing
- Shop Management
- Testing and Measuring
- Tube and Pipe Fabrication
- Tube and Pipe Production
- Waterjet Cutting
Industry Directory
Webcasts
Podcasts
FAB 40
Advertise
Subscribe
Account Login
Search
Holy fabrication work!
Creating metal elements for a Catholic church is no simple cut and bend job
- By Dan Davis
- February 10, 2015
- Article
- Laser Cutting
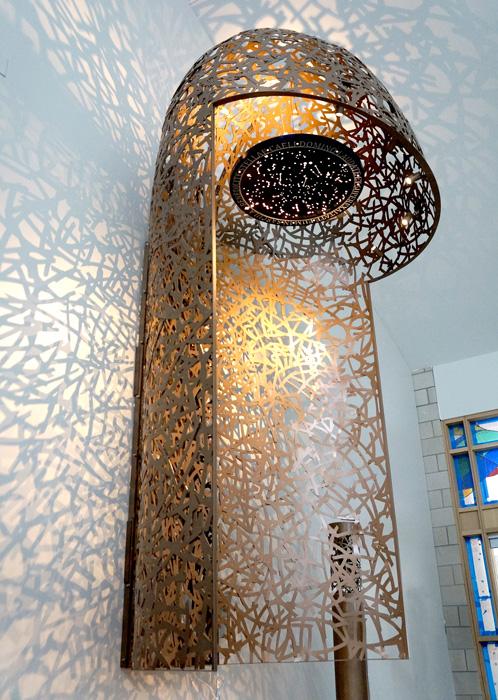
Figure 1
A baldachin is a ceremonial canopy found in a church.
Design Fugitives, Milwaukee, fabricated this particular
baldachin with a CNC plasma table with a Hypertherm
Powermax85 to cut the sections out; a manual roller to
form the cylindrical shapes; and a gas metal arc welding
power source to join the parts together. It was later sandblasted
and painted to get the final bronze appearance.
A company that goes by the name Design Fugitives probably isn’t a metal fabricator in the sense that it can deliver 5,000 metal widgets by the start of business the next day.
In reality, the Milwaukee company is a design firm that can both envision and make the vision a reality. It started in 2009 as a collection of three individuals with backgrounds in architecture who wanted to do more than just sit in front of their computers all day. They wanted to be involved in the actual creations of the designs, which today include furniture, lighting fixtures, and even pavilions.
The company also has the latest tools to showcase the principals’ craftsmanship. It uses the latest CNC plasma and routing technology, for example, to create these special fabrications.
“The way we talk about ourselves is we are ‘figure-outers,’” said Paul Mattek, one of the founding partners.
With the design talent and the fabricating muscle to tackle their own work, Design Fugitives inevitably finds itself taking on challenging work—something almost any metal fabricator can identify with. In one of its more interesting undertakings recently, the company designed and fabricated ecclesiastical elements for St. Mary Magdalen Parish in Grand Rapids, Mich. (see Figure 1).
Design Fugitives was approached after having worked with a Jesuit priest working at the University of Detroit Mercy (UDM), who later recommended the firm to the parishioners of St. Mary Magdalen. They wanted to somehow find a way to demonstrate the “shield of the spirit,” as Mattek described it, around the Eucharistic celebration.
Like most any successful design project, the winning idea began with a simple sketch. Instead of off-the-shelf wire mesh architectural elements that were originally in the worship space, Design Fugitives came up with the idea to create a sense of movement on the church walls, like wheat being blown by the wind.
“It was something immaterial registering itself on something material and then creating a new composition—a new life to it,” Mattek said. “The visible and the invisible merged.”
Mattek and his partners met with the UDM liturgical design consultant and even chatted briefly with a Vatican astronomer. That input helped them deliver a rendering of a lighted baldachin (from the Italian word baldacchino) to share with parishioners. That rendering revealed not only an obvious pattern in the metal, but also another one evident on the nearby wall (see Figure 2). The light was cast around the worship space.
After the design firm received buy-in from the church, it had to fabricate the pieces. It used Rhinoceros 3-D design software to re-create the renderings in a digital format and a software plug-in to write a script that allowed for manipulation of the design, such as adjusting the density of the pattern in areas or deciding just how much rotation to introduce as the design was wrapped around a cylinder. When the final tweaks were done, the software flattened out the design, and the CNC instructions were created for the plasma cutting table. The smaller parts were later welded together, and final finishing steps led to the creation of the new ecclesiastical elements.
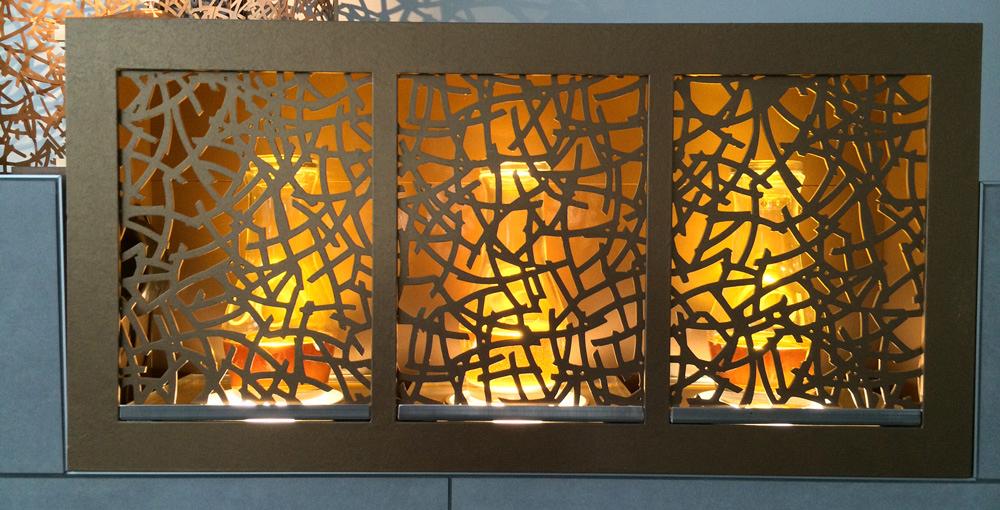
Figure 2
The light emanating from the metal fabrications is
meant to evoke the presence of the Holy Spirit watching
over Mass. Some parishioners also see shapes that
remind them of the crown of thorns that adorned Jesus’
head when he died on the cross.
Design Fugitives designed and fabricated the baldachin, a sanctuary lamp (see Figure 3), an ambry for holding oils, Stations of the Cross panels, water font holders, a decorative wall pattern, and four intricate door carvings. Only the latter was made of wood.
Looking back at this project, Mattek said he believes that his company accomplished the main goal of delivering what the customer had in mind, but had no idea of how to create. This project, however, also met personal expectations as well.
“Our primary desire is to design and make cool stuff,” he said.
Amen.
About the Author
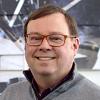
Dan Davis
2135 Point Blvd.
Elgin, IL 60123
815-227-8281
Dan Davis is editor-in-chief of The Fabricator, the industry's most widely circulated metal fabricating magazine, and its sister publications, The Tube & Pipe Journal and The Welder. He has been with the publications since April 2002.
subscribe now
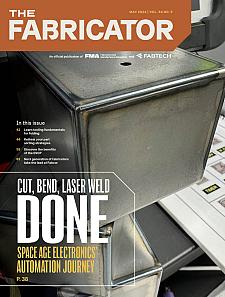
The Fabricator is North America's leading magazine for the metal forming and fabricating industry. The magazine delivers the news, technical articles, and case histories that enable fabricators to do their jobs more efficiently. The Fabricator has served the industry since 1970.
start your free subscription- Stay connected from anywhere
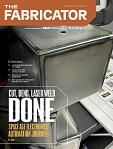
Easily access valuable industry resources now with full access to the digital edition of The Fabricator.
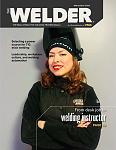
Easily access valuable industry resources now with full access to the digital edition of The Welder.
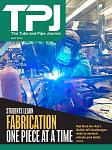
Easily access valuable industry resources now with full access to the digital edition of The Tube and Pipe Journal.
- Podcasting
- Podcast:
- The Fabricator Podcast
- Published:
- 04/16/2024
- Running Time:
- 63:29
In this episode of The Fabricator Podcast, Caleb Chamberlain, co-founder and CEO of OSH Cut, discusses his company’s...
- Trending Articles
Tips for creating sheet metal tubes with perforations
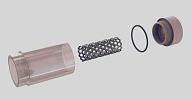
Are two heads better than one in fiber laser cutting?
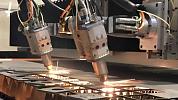
Supporting the metal fabricating industry through FMA
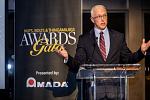
JM Steel triples capacity for solar energy projects at Pennsylvania facility
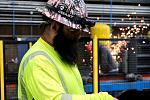
Omco Solar opens second Alabama manufacturing facility
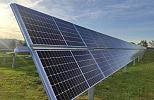
- Industry Events
16th Annual Safety Conference
- April 30 - May 1, 2024
- Elgin,
Pipe and Tube Conference
- May 21 - 22, 2024
- Omaha, NE
World-Class Roll Forming Workshop
- June 5 - 6, 2024
- Louisville, KY
Advanced Laser Application Workshop
- June 25 - 27, 2024
- Novi, MI