Editor-in-Chief
- FMA
- The Fabricator
- FABTECH
- Canadian Metalworking
Categories
- Additive Manufacturing
- Aluminum Welding
- Arc Welding
- Assembly and Joining
- Automation and Robotics
- Bending and Forming
- Consumables
- Cutting and Weld Prep
- Electric Vehicles
- En Español
- Finishing
- Hydroforming
- Laser Cutting
- Laser Welding
- Machining
- Manufacturing Software
- Materials Handling
- Metals/Materials
- Oxyfuel Cutting
- Plasma Cutting
- Power Tools
- Punching and Other Holemaking
- Roll Forming
- Safety
- Sawing
- Shearing
- Shop Management
- Testing and Measuring
- Tube and Pipe Fabrication
- Tube and Pipe Production
- Waterjet Cutting
Industry Directory
Webcasts
Podcasts
FAB 40
Advertise
Subscribe
Account Login
Search
Laser cutting systems demonstrate practical evolution
PRC Laser introduces two products influenced by real-world fabricating concerns
- By Dan Davis
- November 23, 2020
- Article
- Laser Cutting
The PRC Laser team enjoyed the 2019 FABTECH tradeshow in Chicago. Not only did North America’s largest sheet metal fabricating technology event provide an opportunity to meet new customers, it gave the company the platform to tell everyone about its new manufacturing facility in Ladson, S.C. The company that once was synonymous with CO2 laser resonator manufacturing is now a full-fledged laser cutting machine builder, as well as a seller of machine components, such as its own machine controller.
One year later, PRC Laser is still enjoying the latest benefit of attending that trade show. It’s introducing two new laser cutting machines, the Falcon 5x13 and the Apex 4x4, which were directly influenced by conversations had at FABTECH.
“Many people walking around FABTECH don’t realize that they are the experts,” said Alain Porro, PRC Laser’s director of sales. “They go to work every day; then they have the chance to go to FABTECH and see some cool stuff. When you meet them, they can say the most interesting things. Some observations are genius.”
It takes smart people to recognize other smart people. Today PRC Laser is owned by three parties: Walter Wilson, current president and a longtime executive with the company; partner Guy Bauwens, general manager and head of PRC European operations; and machine designer Jan Muys, who is now chief technology officer. The trio purchased the company from Coherent in April 2018. It’s now dedicated not only to building the CO2 laser resonators at its Charleston, S.C.-area facility, but also laser cutting systems that can have PRC’s own CO2 power sources or fiber lasers ranging from 1 to 12 kW. PRC Laser’s first machine tool was a 5- by 10-ft. model. The input gained from the 2019 FABTECH event helped to influence its next class of machines.
The first product tweak came in the form of a different cutting bed size. Porro said the idea to increase the length of the bed came from a conversation with a Midwest metal fabricator.
“The fabricator said, ‘I go out and see these expensive 6- by 12-ft. or 2- by 4-m machines, and you always see this beautiful 1-ft. strip of clean slats all the way down the machine because no one is using 6-ft. sheets. Everybody buys 4- to 5-ft.-wide sheets,’” Porro recounted.
In essence, the fabricator asked why he should pay for something he wasn’t going to use. Porro said the feedback resonated with the PRC Laser leadership team.
As a result, it has introduced its Falcon 5x13 laser cutting machine, joining its machine with a 5- by 10-ft. bed. (The machine designers decided to go with a 13-ft. bed instead of a 12-ft. bed so that it would be closer to 4 m, making it more appealing for customers around the world.) With its front-load capability, the Falcon maintains a smaller footprint, even with the 13-ft.-long bed, than other end-loading laser cutting machines. “The footprint is particularly attractive to shops with limited square footage,” Porro said.
The larger Falcon still features the original machine’s motion system with a centered overhead carriage. “It’s not a cantilever or rear-driven system. The gantry is firmly balanced under the X axis,” Porro said. “It’s truly a flying optic.”
Porro added, “If you were able to look at the motion system without the top of the enclosure being in the way, you would see a design reminiscent of a bird’s wings. The Falcon name was an ideal fit after a suggestion from Mr. Wilson.”
This cabinet-style laser cutting machine from PRC Laser is called the Apex. It has a tilt table that raises up so that the machine operator can place the sheet metal vertically onto the table, like a painting being placed on an easel. The table then returns to its original position when laser cutting commences. The procedure can be repeated for subsequent cutting jobs.
At the same FABTECH, PRC Laser had its shuttle table near the aisle, so it limited table cycling for safety reasons. Because of that, staff personnel had to manually load the sheet metal onto the cutting bed. That led to a conversation about a material handling feature that would assist fabricators who have to manually load their material into their laser cutting machines.
“Walter [Wilson] suggested that we design a tilt table,” Porro said. “Jan Muys envisioned the idea and marketing it with the words ‘We have your back.’”
That tilt table is now part of the design for the Apex 4x4, a cabinet-style laser cutting machine with a 48- by 48-in. working area. If a laser operator wants to load a sheet, he hits a button and the table raises into position, like an easel used to support a painting. The operator gets a sheet from the teepee rack and grabs it vertically at the material’s apex. (“That’s why we named the machine Apex,” Porro said.) The operator then places the sheet metal on a lip on the bottom of the tilted table. If he needs to move it into position, he can shimmy it on rollers on the table’s lip, so the material isn’t being dragged along a solid bottom. When the material is in place, the operator hits a button and the table returns to its original horizontal position.
The Apex is designed to appeal to a niche market of metal fabricators. Likely candidates for this machine, according to Porro, are shops that may be focused on waterjet or plasma cutting now and want to jump into fiber laser cutting without a $1 million investment or shops that don’t have a lot of room.
Porro said that being good listeners paid off almost immediately for PRC Laser. The metal fabricator who suggested the longer cutting bed took possession of a Falcon 5x13 in late September.
About the Author
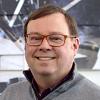
Dan Davis
2135 Point Blvd.
Elgin, IL 60123
815-227-8281
Dan Davis is editor-in-chief of The Fabricator, the industry's most widely circulated metal fabricating magazine, and its sister publications, The Tube & Pipe Journal and The Welder. He has been with the publications since April 2002.
subscribe now
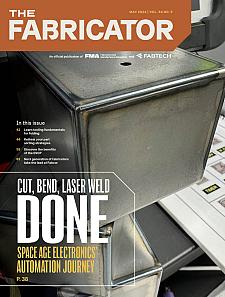
The Fabricator is North America's leading magazine for the metal forming and fabricating industry. The magazine delivers the news, technical articles, and case histories that enable fabricators to do their jobs more efficiently. The Fabricator has served the industry since 1970.
start your free subscription- Stay connected from anywhere
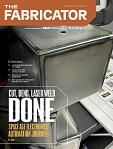
Easily access valuable industry resources now with full access to the digital edition of The Fabricator.
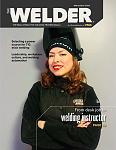
Easily access valuable industry resources now with full access to the digital edition of The Welder.
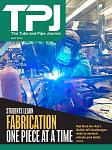
Easily access valuable industry resources now with full access to the digital edition of The Tube and Pipe Journal.
- Podcasting
- Podcast:
- The Fabricator Podcast
- Published:
- 04/16/2024
- Running Time:
- 63:29
In this episode of The Fabricator Podcast, Caleb Chamberlain, co-founder and CEO of OSH Cut, discusses his company’s...
- Trending Articles
Tips for creating sheet metal tubes with perforations
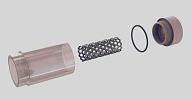
Supporting the metal fabricating industry through FMA
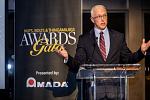
JM Steel triples capacity for solar energy projects at Pennsylvania facility
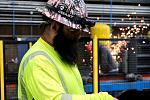
Are two heads better than one in fiber laser cutting?
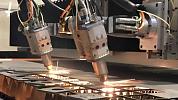
Fabricating favorite childhood memories
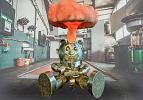
- Industry Events
16th Annual Safety Conference
- April 30 - May 1, 2024
- Elgin,
Pipe and Tube Conference
- May 21 - 22, 2024
- Omaha, NE
World-Class Roll Forming Workshop
- June 5 - 6, 2024
- Louisville, KY
Advanced Laser Application Workshop
- June 25 - 27, 2024
- Novi, MI