Contributing Writer
- FMA
- The Fabricator
- FABTECH
- Canadian Metalworking
Categories
- Additive Manufacturing
- Aluminum Welding
- Arc Welding
- Assembly and Joining
- Automation and Robotics
- Bending and Forming
- Consumables
- Cutting and Weld Prep
- Electric Vehicles
- En Español
- Finishing
- Hydroforming
- Laser Cutting
- Laser Welding
- Machining
- Manufacturing Software
- Materials Handling
- Metals/Materials
- Oxyfuel Cutting
- Plasma Cutting
- Power Tools
- Punching and Other Holemaking
- Roll Forming
- Safety
- Sawing
- Shearing
- Shop Management
- Testing and Measuring
- Tube and Pipe Fabrication
- Tube and Pipe Production
- Waterjet Cutting
Industry Directory
Webcasts
Podcasts
FAB 40
Advertise
Subscribe
Account Login
Search
New dimension, familiar direction
H.W. Metals invests in a laser cutter for jobs where plasma doesn’t cut it
- By Michael Bishop
- February 10, 2009
- Article
- Laser Cutting

H.W. Metals processes high-strength steel for many different applications, including transportation equipment manufacturing.
H.W. Metals, Tualatin, Ore., processes high-strength steel for transportation equipment manufacturers and other applications. The company began operating in 1979 as the fabrication division of a local service center, which would provide materials and contract out work. Jack Suter and Howard Wolfe both were with the company in October of '79 when it shipped its first product: a 48-foot-long, grade-70 truck trailer frame.
When the service center closed the fabrication division, Suter and Wolfe took over a back bay, where they operated a large press brake that was two tandem 24-ft., 750-ton machines. Since then H.W. Metals has expanded its offerings with punching, shearing, and arc welding. The company also added high-definition plasma cutting with the purchase of an 80-ft.-long by 10-ft. wide, two-torch system and standard plasma cutting with the acquisition of two four-torch systems—one measuring 80 ft. by 12 ft. and the other 90 ft. by 12 ft. And it acquired press brakes in 14-ft., 350-ton; 20-ft., 350-ton; and 60-ft., 2,500-ton models for additional forming capacity.
Suter now owns the company, along with Wolfe and both of their sons: Vice President/Sales Manager Josh Suter and Vice President/General Manager Brian Wolfe.
H.W., which historically has maintained a work force of about 75, currently employs 65 in a 140,000-sq.-ft. facility. It runs two shifts per day, with the exception of certain machines that run all the time. Even though its large number of machines and its variety of operations keep it reasonably busy, the company found that there was more and more work it couldn't do for its customers because some jobs required laser-cut parts. The company didn't have laser technology, which automatically excluded it from these jobs.
Taking those customers into account, as well as new work and the evolution of the way steel is cut, the company decided to purchase a laser. Managers didn't want to go into new markets, but they wanted to expand capabilities in their current markets by offering an alternative to plasma cutting, Suter said.
"It was a direction we had to go to ensure our future," he said.
First in North America
In October 2008 the company installed a Prima Maximo laser cutting system, the first of this model to be installed in North America, according to Suter. The system allows the company to cut a 60-ft. part in a single section. It also cuts small parts as quickly and efficiently as a small laser. As a result, the company didn't need to purchase both a large and a small laser, so it bought one machine with a small footprint.
"I think that we're the only job shop that can plasma, high-def plasma, laser-cut, form, and weld a 60-foot piece in a single section," Suter said. "We don't cut 60-foot parts that often, but we have the ability to do so."
At first Suter worried about bringing a laser into a carbon steel, heavy-industry shop environment because he didn't know if the laser would be affected by carbon dust and vibration. Visits to shops in Italy that work under similar conditions convinced him that H.W. could install and use the laser without problems.
Preparing for the installation required work on the foundation, plumbing, and gas lines. The foundation had to be isolated from the rest of the shop floor to eliminate the possibility of vibration and shock problems. The gas lines needed to be run from bulk tanks to the laser, a project that the company contracted out. H.W. Metals didn't have to rearrange the shop at all; the company just had to figure out the right place to put the machine and clear enough floor space. To assuage the worries about carbon dust and vibration, technicians installed it away from high-traffic areas and the main work flow of the shop.
The introduction of the business's first laser required significant training to prepare workers to operate the machine, Suter said.
"None of our people here had run a laser, so we had to hire an operator who was experienced in operating a fairly large laser," he said. "We trained a couple of our plasma operators as well. And we trained two people internally in the programming aspect."
Streamlining the Operation
Early operations have met the company's expectations since the installation. The first item the shop processed on the laser was 3/16-in. DOMEX®, 110,000-minimum-yield, 53-ft.-long, as-rolled steel for agricultural trailer rails. The company also cut 1/2-in., abrasion-resistant track pad, which is heat-treated, 4-ft.-long plate for mining applications. The pads required holes that plasma couldn't cut correctly. So before the company installed the laser, this was a two-stage operation in which operators would plasma-cut the part and then punch or drill holes. The process since has been consolidated into a single operation—operators now laser-cut the perimeter and the holes. The laser also has helped eliminate the need for customers to have to prepare cut edges for welding.
"Handling the material is always a crucial issue, and the fewer times you have to move product from machine to machine, the more time you save, and then you can allocate manpower more efficiently," Suter said.
Anecdotal Engineering
H.W. Metals isn't known for making just one product. According to its Web site, applications for its fabricated parts include marine, railcar, truck trailer, dump truck body, motor home, transit bus, crane boom, military vehicle, and mining equipment. The company also fabricates poles for light structures and components for bridges, buildings, conveyors, signs, and tanks.
The company, which also uses the laser for some in-house art projects, continues to train plasma operators on how to run the machine. Suter believes the company eventually will purchase another laser. But because H.W. is a job shop, customer needs will dictate goals for the future, he said. One goal for the new laser is to provide new services to current customers. Now, for example, a customer that previously requested plasma-cut parts from H.W. but had to seek laser-cut parts from another job shop can turn to H.W. for both.
In addition to its work with transportation equipment manufacturers, the company has gotten involved with the military in parts for armament, cutting components with both plasma and the laser. The company also has been involved, to a certain extent, in architectural and building applications and expects the laser to open up new markets in these areas. This will prove especially important because H.W. depends on manufacturers more than any industry segment for business, and its work with manufacturers cycles in ways that business with fabricators and the construction industry doesn't, Suter explained. Because of this, expanding into new markets with the help of the laser may be able to prepare the company to work through slowdowns in the manufacturing industry.
"We don't make a product; we are an extension of our customer's shop and consider ourselves a local outsource option," he said. "We don't have an engineering staff. We work off of customer drawings and consider ourselves anecdotal engineers."
About the Author
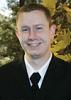
Related Companies
subscribe now
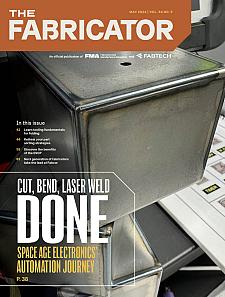
The Fabricator is North America's leading magazine for the metal forming and fabricating industry. The magazine delivers the news, technical articles, and case histories that enable fabricators to do their jobs more efficiently. The Fabricator has served the industry since 1970.
start your free subscription- Stay connected from anywhere
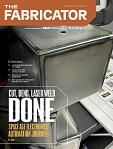
Easily access valuable industry resources now with full access to the digital edition of The Fabricator.
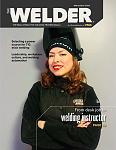
Easily access valuable industry resources now with full access to the digital edition of The Welder.
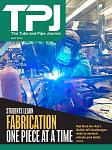
Easily access valuable industry resources now with full access to the digital edition of The Tube and Pipe Journal.
- Podcasting
- Podcast:
- The Fabricator Podcast
- Published:
- 04/16/2024
- Running Time:
- 63:29
In this episode of The Fabricator Podcast, Caleb Chamberlain, co-founder and CEO of OSH Cut, discusses his company’s...
- Industry Events
16th Annual Safety Conference
- April 30 - May 1, 2024
- Elgin,
Pipe and Tube Conference
- May 21 - 22, 2024
- Omaha, NE
World-Class Roll Forming Workshop
- June 5 - 6, 2024
- Louisville, KY
Advanced Laser Application Workshop
- June 25 - 27, 2024
- Novi, MI