- FMA
- The Fabricator
- FABTECH
- Canadian Metalworking
Categories
- Additive Manufacturing
- Aluminum Welding
- Arc Welding
- Assembly and Joining
- Automation and Robotics
- Bending and Forming
- Consumables
- Cutting and Weld Prep
- Electric Vehicles
- En Español
- Finishing
- Hydroforming
- Laser Cutting
- Laser Welding
- Machining
- Manufacturing Software
- Materials Handling
- Metals/Materials
- Oxyfuel Cutting
- Plasma Cutting
- Power Tools
- Punching and Other Holemaking
- Roll Forming
- Safety
- Sawing
- Shearing
- Shop Management
- Testing and Measuring
- Tube and Pipe Fabrication
- Tube and Pipe Production
- Waterjet Cutting
Industry Directory
Webcasts
Podcasts
FAB 40
Advertise
Subscribe
Account Login
Search
Laser welding and structural adhesive bonding for BIW welding
Competing or complementary joining methods?
- By Johnny Larsson
- Updated October 26, 2023
- May 8, 2007
- Article
- Laser Welding
Selecting the best joining method for state-of-the-art body-in-white (BIW) engineering and manufacturing is a delicate task. Considering that, in principle, a car body engineer has only three parameters to combine for an optimal solution—the geometric shape, material, and the joining method—it is essential to choose the appropriate joining technique. This explains why new assembly technologies have received a lot of attention lately and are gaining ground steadily at the expense of more traditional welding methods.
Considering the palette of available joining methods (see Figure 1), it is easy to understand how problematic it can be for a design engineer to select the most suitable joining method for each application. Therefore, it may be useful to review what a BIW joint's purpose is.
Simply put, joining's main objective is to attach separate components to a functional structure. Furthermore, the joint must balance the properties of the materials it connects so that the assembly becomes as strong as possible, thereby reducing vehicle weight and optimizing fuel efficiency.
Case Example of Laser Welding: Volvo C70 Convertible
The Volvo C70 convertible, built on the P1 platform and launched in the autumn of 2005, features a variety of laser applications3(see image at top of page). Laser welding is the preferred joining method for the floor sill; it also is necessary for attaching the A-pillar cover to the A-pillar, because the A-pillar is a hydroformed, kneaded tube, and therefore allows only single-sided access for assembly. The connection between the upper portion of the A-pillar and the front header is laser-brazed. The smooth brazed surface satisfies the stringent visual requirements for this high-quality auto.
The laser brazing, along with other laser welding operations, takes place in a stand-alone cell in the main body shop line. The cell has a 4-kW, lamp-pumped Nd:YAG laser source with fiber-guided beam transmission (see Figure 3). The same laser head that is used to weld the A-pillar is also used for the brazing operations. In practice, this means that the pressure finger device needed for welding operations is flipped aside and substituted with the braze wire (CuSi3) feeder. When the A-pillar/front header connection is laser-brazed, the wire itself serves as a mechanical guiding device.
Furthermore, the combined brazing and welding tool is equipped with swiveling optics, cover glass monitoring, a heavy-duty crossjet, and water-cooled nozzles. Typical brazing speed is around 5.28 feet per minute (1.6 meters per minute), and the preheated wire is fed at a rate of 4.29 FPM (1.3 MPM).
Making recommendations about which joining method to use for different car body components and assemblies is a challenging task. Throughout the years, attempts have been made to create general rules. For example, for the 1999-2000 vehicle releases, Volvo Cars was using traditional spot welding as the reference standard from which to evaluate the positives or negatives of alternative joining methods on various body properties and attributes.
Which Technologies Are Best Suited for BIW Welding?
Two joining methods that are being used with increasing frequency are laser beam welding and structural adhesive bonding. They both offer long, continuous bonding lines and therefore can be considered competing methods.
Understanding the pros and cons of these two technologies makes it possible to decide which body-in-white applications are more suitable for laser welding or adhesive bonding, resulting in design guidelines and recommendations for the engineer.
Assembling car body parts using either laser welding or structural adhesive bonding provides some advantages. Because they generate a continuous bond line, they create a larger area for load transfer between parts. This larger load transfer results in better crash performance, increased durability, and improved torsion and bending stiffness. That, in turn, makes it possible to down-gauge material thickness and reduce weight, while maintaining good car body performance.
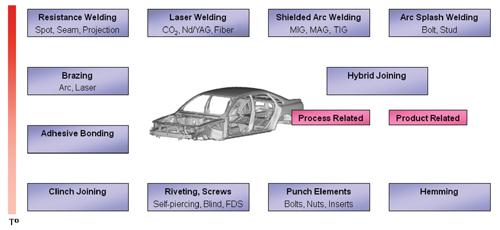
Figure 1 Joining methods currently used in the body-in-white assembly process are numerous and varied.
In the case of traditional unitized car body structures, using both laser welding and adhesive bonding can contribute to the weight savings realized with the use of high-strength steel (HSS).
Laser Welding
Today most car bodies made by automakers around the world have at least a couple of laser welded components (see Automakers Using Laser Welding).
Laser Welding Advantages
Single-sided Access. One of the main benefits of laser welding is that it requires only single-sided access to the joining location, as opposed to classic resistance spot welding (RSW), which operates with upper and lower electrodes. This opens up possibilities for completely new design solutions; however, to really utilize these new design solutions for laser welding also requires an open-minded design approach.2 For example, laser welding a typical RSW flange does not make sense, because that type of layout is optimized for spot weld gun access and does not benefit from the possibility of narrow laser welds. Single-sided welding must take into consideration the necessity to reach fixture arrangements, such as pressure devices and fixed clampings, to create the smallest weld gap between sheet components in an overlap configuration.
Invisible Joints. By positioning the laser weld on the sheet edge, or by using laser brazing technology in combination with some type of beam trap configuration (see Figure 2), it is possible to create nearly invisible joints. This gives the impression of craftsmanship in areas such as door, trunk lid, and tailgate apertures.
Material Reduction. Another advantage of laser welding is that it requires smaller flanges than spot welding requires for apertures such as side door openings. A reduction from 16 mm to 6 mm—a 10-mm reduction—is feasible with the correct flange design. Not only do such narrow weld flanges reduce weight and improve visibility, they also allow for increased volume for pillar, cantrail, and sill sections in confined spaces, which increase stiffness and strength. The latter, of course, is also a result of the continuous weld line, which, in this respect, is superior to intermittent RSW spacing. This, in turn, enables sheet components to be down-gauged while maintaining comparable performance to heavier spot welds.
From a manufacturing perspective, the high process speed is favorable because it improves productivity, reduces cycle time, and can be used to reduce costly floor space in the body shop. But the high process speed also results in less heat input and lower part distortion, which, in turn, help improve accuracy and quality of the final product.
Laser Welding Disadvantages
High Investment Cost. Although it may sound as though laser welding could be the ultimate tool for BIW assembly, some drawbacks exist. One obvious drawback is the high investment cost of installing fully equipped laser welding cells. Therefore, it is important that the body design is such that the enhanced properties and performance can justify the higher investment costs.
Tight Tolerances. It is also important to bear in mind that laser welding puts more stringent requirements on parts and positioning tolerances to ensure a successful result. Overlooking this in early automotive laser history resulted in many failures.
Specific Repair Methods. Finally, because laser welding is a relatively new joining method, repair techniques specifically designed for laser welding must be used.
Structural Adhesive Bonding
Adhesive bonding seems to be the topic of the day among European automotive manufacturers. In reality, they are addressing the subject of welding/bonding, in which the adhesive application is followed by spot welding to position and fixture the parts together accurately before the heat-curing adhesives harden to full strength during the paint process.

Figure 3 Adhesive trap designs (left to right—flat, right-angle, inclined) prevent the risk of adhesive washoff during the cleaning steps preceding the paint and curing processes.
Automakers Using Laser Welding
Although European automakers were the first to use laser welding, Asian manufacturers like Nissan, Toyota, and Hyundai, as well as North American automakers GM, Ford Motor Co., and DaimlerChrysler, have incorporated it now as well.
For example, roof laser welding recently was used on the Ford 500® models and Freestyle®. Right now Ford is considering laser welding for the assembly of the new F-150® pickup truck, with an estimated annual volume of 850,000.
It is difficult to ignore the impressive investments in laser facilities by European automaker Volkswagen (VW) group.1 The company was late to accept laser technology relative to competitors like Volvo Cars and BMW. As a result, VW bypassed CO2 laser welding and incorporated Nd:YAG technology, which was introduced around 1990.
When VW introduced its fifth-generation version of the Golf®, it was nothing less than a paradigmatic shift for car body assembly within the company. The new Golf model contains about 231 feet (70 meters) of laser welds. To be able to manage this large-scale usage, 250 lamp-pumped, 4-kW Nd:YAG lasers were installed in the Wolfsburg and Mosel, Germany, and Brussels, Belgium, plants. In the Wolfsburg factory alone, 89 miles (140 km) of laser welding on 2,000 car bodies is performed daily in a three-shift operation.
The laser applications primarily are on the underbody and body sides, in the framing, and in a number of subsequent respot welding stations. In addition, VW uses laser brazing to attach the roof to body sides; for the drain channel in the trunk lid opening; and for the split skin panel of the trunk lid.
Today the most commonly used adhesives are epoxy-based, but as environmental concerns become more pronounced, intensive R&D is ongoing to try to develop more environmentally friendly, rubber-based alternatives. The presence of about 132 to 231 feet (40 to 70 meters) of epoxy adhesive in a modern car body structure is considered more or less "state-of-the-art." Current examples include the Audi A4® and A6® models, the BMW 5- and 7-Reihe®, and the Mercedes E-, S- and CLK-Klasse®.
Structural Adhesive Bonding Advantages
Preventing Cracks. Adhesive bonding is a well-known complement to help resolve problems with cracks around spot welds occurring as a result of fatigue loads. Distributing the stress forces over a larger area reduces the stress concentration on the spot welds. Therefore, it is possible to reduce sheet component thickness without risking fatigue performance, and to reduce the number of spot welds. This, in turn, will require fewer welding robots in the body shop, resulting in a substantial cost reduction—both in terms of investment in new automation equipment and utilities such as electricity and cooling water.
NVH. Replacing otherwise necessary sealant materials with adhesive automatically achieves a double functionality. Doing so not only seals out water, it also improves noise, vibration, and harshness (NVH). Here, the adhesive not only dampens airborne noise distribution, it also can help minimize body vibrations for critical frequencies because of its stiffness.
Performance. Tailor-made adhesives are being developed that could be attractive from an engineering standpoint, for example, to improve fatigue and crash performance.
Structural Adhesive Bonding Disadvantages
Environmental Impact. The drawbacks of adhesive usage today are mainly linked to the working environment, because the hazardous long-term effects of adhesives, which initially raised a number of questions, seem to have been validated. One concern about using epoxy adhesives is that they can cause skin allergies. Environmentally conscious automakers have fully robotized the application of structural adhesives. Through an exact extrusion, excessive amounts of adhesives that could contaminate equipment and personnel can be avoided. Postheating operations, such as repair welding, in areas where adhesives are present should be avoided.
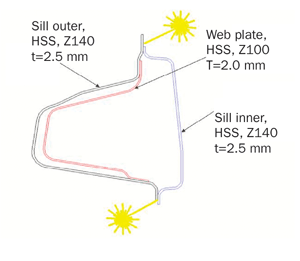
Figure 5 Section height within a restricted space can be gained by using minimum flange length and laser fillet welding.
Washoff. Another disadvantage is the risk of so-called washoff of the adhesives during the various cleaning steps preceding the paint and curing processes. As the adhesive has not cured at this state, it is important to trap it in place to maintain the intended product improvements. This can be done either by smart adhesive trap designs (see Figure 3) or, for especially critical applications, by placing the adhesive-joined parts in pregel ovens in the body shop.
Conclusions and Recommendations
Taking into consideration the advantages and disadvantages of laser welding and adhesive bonding that have been outlined, some obvious recommendations can be given as to when to use each method. However, in some situations the choice is not so clear-cut, especially with complex loading and when counteracting product properties exist, such as the cross section of structural members.
Case Example of Adhesive Bonding: Volvo S80® Luxury Sedan
When Volvo Cars launched its new S80 luxury sedan in the spring of 2006, it was the first time that the company used adhesive bonding extensively, and specifically to improve car body properties. About 82.5 feet (25 meters) of the heat-curing, epoxy-based, single-component adhesive BetaMate XW-1496V is used in the vehicle. It is applied primarily in the underbody structure, where the adhesive contributes to a global torsion stiffness of 22.0 kNm/deg.
But the main reason for introducing adhesive bonding on a larger scale than before was to improve the crashworthiness of the car without encountering high weight penalties in the form of add-on reinforcements. The S80 has received an 8-star ranking in the European Union New Car Assessment Program (EU-NCAP) testing, and a 5-star ranking in the corresponding U.S. New Car Assessment Program (US-NCAP). It provides the best side-impact protection, according to the International Institute for Highway Safety (IIHS), and Allianz insurance classified it as a "vk24." Comparable performance would have been possible without adhesive bonding, but at the expense of an 8-kg weight increase (see Figure 4).4
The introduction of adhesive technology in the Torslanda, Sweden, plant where the Volvo S80 is manufactured has created the need for a factory expansion to accommodate a completely new underbody line. The investment cost for this expansion is about 3.5 million euros.
Great emphasis has been placed on the working environment, quality assurance, and process monitoring. Both nondestructive testing (ultrasonic techniques and camera inspection) and periodic destructive testing (peel tests) are performed to ensure bond quality.
In addition, the education of specially trained "adhesive operators" has been an important component of introducing adhesive bonding into the manufacture of the S80 model.
So far there has not been evidence of improvements from a continuous laser weld for dynamic crash loads. Where loads are parallel to the weld seam—which is the case in the axial compression of front side members at frontal (head-on) or offset (40 percent overlapping of the impacting car's front) accidents, for example—this is easy to understand. The forces are concentrated at the very small weld width at the start or end of the laser weld, so the risk that the narrow weld may just unzip is obvious.
[image8]However, not even using spot welds to decrease stress concentration at the ends of the laser weld has improved crash performance.5 The only remaining alternative, then, is to configure the laser weld pattern by using a remote welding technique,6 so that the crash loads can be absorbed in a more optimized and controlled manner. However, further research has to be conducted before these assumptions can be relied on.
What is a little more difficult to explain is the laser weld's poor behavior compared with adhesively bonded flanges in four-point dynamic bending (see Figure 4). The "single-hat" beams used in this study had a 17-mm, flat flange, which is the standard for a spot-welded flange. They also were wide enough to be joined securely with an adhesive application 10 mm wide.
Looking at the laser-welded components only showed that continuous laser welds behave better than intermittent stitch welds, and a fully penetrated overlap weld performs better than a fillet weld. What is perplexing, however, is that the spot-welded component (with 40-mm spacing) is almost as strong as the continuous laser-welded version. Equally perplexing is that the adhesively bonded beams perform better in this loading situation, even when the bond width is only 50 percent of the value that has been stipulated.
It can be concluded that for structural beams or members with equal cross sections, adhesive bonding achieves a larger load distribution area, so it will always be superior to laser welding in terms of durability and crashworthiness.
[image9]However, as indicated earlier in this article, the geometric shape is another way to improve the body performance. A larger cross section of a structural member will always provide better stiffness, fatigue, and energy absorption than a continuous joint. This has been successfully achieved by laser welding the assembly of the floor sill of the Volvo C70® convertible (see Figure 5). With laser fillet welding, the upper and lower weld flanges have been minimized, so it is possible to increase the height of the sill section without interfering with surrounding exterior design areas. This has contributed to the superior global torsion stiffness—12.7 kilonewton meters (kNm)/deg.—of this vehicle.
Joining Selection Rules of Thumb
To summarize the recommendations for using either laser welding or adhesive bonding, the following rules of thumb can be given:
- Flange Width Reduction <-- Laser Welding
- New Single-sided-access Designs <-- Laser Welding
- Invisible Joints <-- Laser Brazing
- Torsion Stiffness <-- Adhesive Bonding
- Fatigue Improvement <-- Adhesive Bonding
- Better Crash Properties <-- Adhesive Bonding
The rules can be simplified even more:
- Underbody <-- Adhesive Bonding
- Upper Structure <-- Laser Welding
The latter, of course, depends on the assembly sequences in the body shop—and perhaps to some extent is application-specific.
On one hand, as adhesive bonding always requires a certain flange width to secure a strong connection, it should be used for underbody applications where the flange width reduction is of minor concern. Too, limiting the use of adhesives to the underbody flanges prevents operators and equipment from getting contaminated from uncured adhesives being squeezed out, as they could from upper body flanges.
On the other hand, the ability to laser weld narrow flanges offers the strongest benefits in the upper structure, where visibility and access ergonomics are of prime interest. Also, concentrating the laser welding operations on the upper structure limits the number of laser stations needed, which can help contain laser investment costs.
Notes:
- J.K. Larsson, "Laser Welding as a Competitive Joining Method in Body-in-White Assembly – An Automotive State-of-the-Art Report With Complementary Future Challenges," in proceedings from 10th Nordic Laser Manufacturing Processes (NOLAMP) Conference, Pite, August 2005.
- J.K. Larsson, "The JKL Design Guide Book for Successful Laser Welding," Annual Assembly of the Swedish Welding Commission, Lule, Sweden, May 2006.
- J.K. Larsson and N. Palmquist, "Extensive Laser Processing on the New Volvo C70 Convertible," in proceedings from Automotive Laser Applications Workshop (ALAW), Plymouth, Mich., March 2006.
- J.K. Larsson, "How to Meet Assembly Issues in Lightweight and Mixed Materials Scenarios – The Diversified Palette of Joining Methods for the Car Bodies of Today and Tomorrow," in proceedings from TRANSFAC'06, San Sebastian, Spain, October 2006.
- R. Khezri, "Fatigue Properties of Laser Welds With Alternative Start and Stop," KIMAB, Stockholm, Sweden (Corrosion and Metals Research Institute) report to be published in March 2008.
- J.K. Larsson, "Load Adapted Laser Weld Patterns Part 2: Crashworthiness Performance," in proceedings from 10th Nordic Laser Manufacturing Processes (NOLAMP) Conference, Pite, Sweden, August 2005.
About the Author
Johnny Larsson
Advanced Body Concepts, Volvo Car Corp.
subscribe now
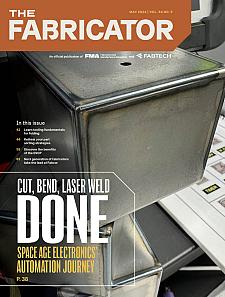
The Fabricator is North America's leading magazine for the metal forming and fabricating industry. The magazine delivers the news, technical articles, and case histories that enable fabricators to do their jobs more efficiently. The Fabricator has served the industry since 1970.
start your free subscription- Stay connected from anywhere
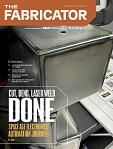
Easily access valuable industry resources now with full access to the digital edition of The Fabricator.
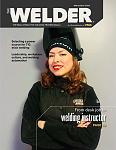
Easily access valuable industry resources now with full access to the digital edition of The Welder.
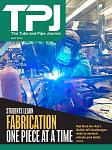
Easily access valuable industry resources now with full access to the digital edition of The Tube and Pipe Journal.
- Podcasting
- Podcast:
- The Fabricator Podcast
- Published:
- 04/16/2024
- Running Time:
- 63:29
In this episode of The Fabricator Podcast, Caleb Chamberlain, co-founder and CEO of OSH Cut, discusses his company’s...
- Trending Articles
Tips for creating sheet metal tubes with perforations
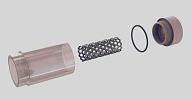
Are two heads better than one in fiber laser cutting?
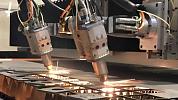
Supporting the metal fabricating industry through FMA
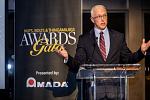
JM Steel triples capacity for solar energy projects at Pennsylvania facility
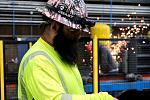
Omco Solar opens second Alabama manufacturing facility
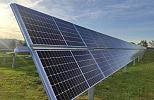
- Industry Events
16th Annual Safety Conference
- April 30 - May 1, 2024
- Elgin,
Pipe and Tube Conference
- May 21 - 22, 2024
- Omaha, NE
World-Class Roll Forming Workshop
- June 5 - 6, 2024
- Louisville, KY
Advanced Laser Application Workshop
- June 25 - 27, 2024
- Novi, MI