Senior Editor
- FMA
- The Fabricator
- FABTECH
- Canadian Metalworking
Categories
- Additive Manufacturing
- Aluminum Welding
- Arc Welding
- Assembly and Joining
- Automation and Robotics
- Bending and Forming
- Consumables
- Cutting and Weld Prep
- Electric Vehicles
- En Español
- Finishing
- Hydroforming
- Laser Cutting
- Laser Welding
- Machining
- Manufacturing Software
- Materials Handling
- Metals/Materials
- Oxyfuel Cutting
- Plasma Cutting
- Power Tools
- Punching and Other Holemaking
- Roll Forming
- Safety
- Sawing
- Shearing
- Shop Management
- Testing and Measuring
- Tube and Pipe Fabrication
- Tube and Pipe Production
- Waterjet Cutting
Industry Directory
Webcasts
Podcasts
FAB 40
Advertise
Subscribe
Account Login
Search
Technology Spotlight: Will beam shaping shape laser welding’s future?
Manufacturers have another tool for refining the laser welding process
- By Tim Heston
- September 7, 2020
- Article
- Laser Welding
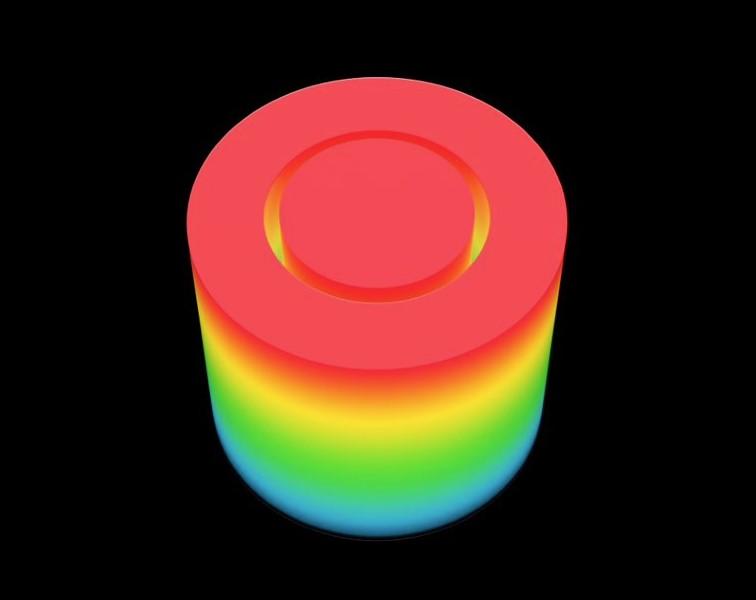
Changing the energy distribution of the profile in beam shaping that has helped move powertrain applications, and now many others, into the fiber laser welding arena.
Lasers have welded automotive powertrains for years, first with CO2 lasers, then with solid-state YAG as the equipment became competitive on price.
“But they weren’t competitive [on] performance. They would produce a lot more spatter than the CO2 lasers. Still, fiber lasers were never implemented for these powertrain laser welding applications. Only now, with the advent of beam shaping, have fiber lasers entered the powertrain welding arena.”
So said Brian Victor, director of industrial applications at nLIGHT, Vancouver, Wash. Beam shaping has been used to describe both changing the shape of the laser spot through the use of optics (as in beam oscillation) as well as changing the energy distribution (or mode) of the beam profile. It’s this last kind of beam shaping that has helped move those powertrain applications, and now many others, into the fiber laser welding arena.
Donut Versus Gaussian
Changing the energy profile in a laser beam is nothing new. A donut, or ring, mode concentrates the energy toward the beam perimeter, while Gaussian focuses the energy toward the center. CO2 lasers have offered this for years. In fact, the ability to switch between donut and Gaussian modes for different operations—cutting, welding, heat treating—has been one of the CO2 laser’s greatest advantages.
“Trying to do the same thing in a fiber has been tricky for a long time,” Victor said.
But beam-shaping options for fiber lasers have emerged within the past few years. With nLIGHT’s approach, now tuning the beam’s energy distribution is occurring within the delivery fiber of the laser itself.
Keyhole and Conduction Welding
When it comes to conventional sheet metal, plate, and other industrial applications, manufacturers generally use a laser to perform one of two types of joining with the fiber laser: conduction welding and keyhole welding.
Traditionally, conduction welding has used limited penetration and slow travel speeds. “You’re making a wide, shallow weld pool, and you’re not creating a lot of vaporization,” Victor said, adding that the goal usually is to create a clean, cosmetically appealing weld. Welds generally are wider than they are deep, and the slower travel gives time for the heat to “conduct” into the part.
Conduction welding often uses a so-called “flat top” beam. “A typical spot size is 600 microns or larger,” Victor said. “But to weld in conduction mode, even 600 microns is too small, so often the process engineer moves the beam out of focus to achieve a diffuse beam shape.” A laser focus point centers around the beam’s waist, its narrowest point. Move the focus away from the material, and a wider beam hits the surface.
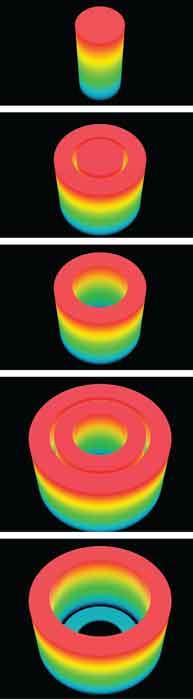
Tuning the laser beam, from a concentrated core to a wide ring mode, can adapt to the needs of various metals processing applications.
“In these cases, only a portion of the beam actually does any work on the material,” Victor said. “The rest is just wasted heat reflected off the material, because it didn’t couple [with the base metal] and create melting.”
Keyhole welding uses a more intense fiber laser beam to create a deep vaporization cavity, known as a keyhole, in the weld pool. This small, intense laser spot produces welds with deep, narrow penetration and the fastest travel speeds.
“Here you might have a beam with a 100-micron core that creates a narrow keyhole, which is great for penetration and speed,” Victor said, “but the narrow keyhole can become unstable, generate spatter, and generate surface irregularities, depending on the alloy you’re welding.”
If you see a laser weld with excessive spatter created with the keyhole process, it’s highly likely the spatter came from an unstable keyhole. Liquid metal around the keyhole edge collapses inward, nearly closing the keyhole (and reducing the penetration) before the laser’s energy forces it open again; metal vaporizes, and a keyhole again forms. The liquid metal that almost collapsed the keyhole ejects outward and results in an unstable weld with spatter and inconsistent penetration.
The Beam Takes a New Shape
For years engineers have tweaked welding parameters through speed and the use of optics. But now beam shaping—through changing the energy distribution of the beam profile—is playing an increasing role.
In nLIGHT’s approach, through its Corona programmable fiber laser system, a cross section of the delivery fiber has three regions: an inner core surrounded by intermediate and outer sections. That central core has a 100-micron diameter, while the two outer regions allow the beam diameter to be tuned up to 350 microns. Oversimplified, the delivery fiber has two inner sheaths that redistribute the energy emerging from the fiber laser source.
In essence, these regions allow the laser to tune its energy profile to meet the needs of the application. According to Victor, such tuning allows the laser to conduction-weld without defocusing. Yes, the resulting beam diameter (up to 350 microns) is smaller than the typical defocused flat top beam, but because it’s in focus, more of the beam energy goes into actually making the weld. With energy distributed not only in the core but also in the intermediate and outer sections of the beam, the beam produces the smooth bead and shallow penetration that conduction welding requires.
For keyhole welding, varying beam energy profiles (or beam “shapes”) helps stabilize the keyhole, and the exact shape needed can depend on the application, including the material’s melting characteristics and the viscosity of the molten metal. Molten metal of a certain viscosity might flow in just the right way to be able to maintain the keyhole wall, even with a Gaussian beam. A metal that melts to more fluid molten material might form a less stable keyhole wall using a laser with the same beam characteristics.
But if more beam energy is distributed to its intermediate and outer sections (closer to the donut mode), the keyhole diameter grows, and the story changes. The keyhole becomes more stable, and the surrounding liquid metal either vaporizes or flows smoothly around the keyhole.
Such beam shaping provides dozens of different beam profiles, each of which is suited for different applications. A beam welding certain stainless alloys that exhibit stable keyholes might have 90% of its energy in the core and only 10% in the outer rings. That creates a narrow keyhole, deep penetration, and fast welding speed.
But what if the next setup involves aluminum or copper, both of which melt into very fluid molten material that can wreak havoc on keyhole integrity? In this case, the setup might use a beam with 80% of its energy in the core and 20% in the outer rings.
Controlled digitally, the beam profile can change mid-operation. So a weld’s lead-in and lead-out might have different beam profiles and laser power than the beam used in the middle of the welding cycle. The beam shape also can shift from one weld to the next. For instance, one workpiece might require both a keyhole and a conduction weld. In the past, this might have required an entirely new setup. Now, though, the beam can make the keyhole weld, then shift immediately to conduction mode and weld the next feature.
The technology also helps bridge weld gaps.
“By having a tunable beam shape, you do add extra capability in gap bridging,” Victor said. “But there’s a theoretical limit. What’s been successful for decades in laser welding is still true.” As always, better fit-up leads to better results.
Even so, such beam shaping gives welding engineers another variable to control, which in turn opens up more processing options. Say a welding cell undergoes a major application changeover involving a different material, joint geometry, and welding speed requirements.
“If you’re developing a process with a fixed fiber dimension and a fixed welding head, historically the only variables you had left to tweak were speed and power,” Victor said. “[With beam shaping,] you have another variable to test, and you might not need to redesign the entire hardware setup of the welding cell.”
Beam shaping in general is gaining major traction in a variety of metal processing sectors. Various forms of beam shaping are in use in the cutting arena. Fiber lasers now cut cleaner in thicker material (such as using a donut mode when oxygen cutting) and cut faster than ever in thinner stock. The technology has also been used in heat treating and even metal additive manufacturing.
“This really is what makes beam shaping for the fiber laser so exciting,” Victor said. “It’s opening up a host of applications that we wouldn’t have dreamed of tackling just 10 years ago.”
About the Author
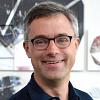
Tim Heston
2135 Point Blvd
Elgin, IL 60123
815-381-1314
Tim Heston, The Fabricator's senior editor, has covered the metal fabrication industry since 1998, starting his career at the American Welding Society's Welding Journal. Since then he has covered the full range of metal fabrication processes, from stamping, bending, and cutting to grinding and polishing. He joined The Fabricator's staff in October 2007.
subscribe now
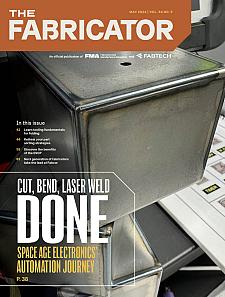
The Fabricator is North America's leading magazine for the metal forming and fabricating industry. The magazine delivers the news, technical articles, and case histories that enable fabricators to do their jobs more efficiently. The Fabricator has served the industry since 1970.
start your free subscription- Stay connected from anywhere
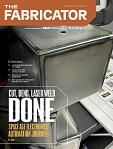
Easily access valuable industry resources now with full access to the digital edition of The Fabricator.
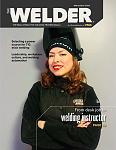
Easily access valuable industry resources now with full access to the digital edition of The Welder.
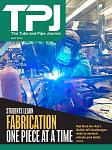
Easily access valuable industry resources now with full access to the digital edition of The Tube and Pipe Journal.
- Podcasting
- Podcast:
- The Fabricator Podcast
- Published:
- 04/16/2024
- Running Time:
- 63:29
In this episode of The Fabricator Podcast, Caleb Chamberlain, co-founder and CEO of OSH Cut, discusses his company’s...
- Trending Articles
Tips for creating sheet metal tubes with perforations
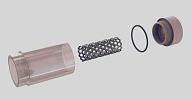
JM Steel triples capacity for solar energy projects at Pennsylvania facility
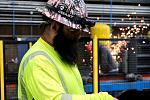
Are two heads better than one in fiber laser cutting?
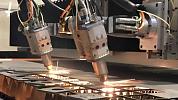
Supporting the metal fabricating industry through FMA
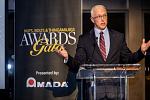
Omco Solar opens second Alabama manufacturing facility
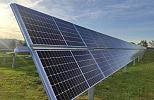
- Industry Events
16th Annual Safety Conference
- April 30 - May 1, 2024
- Elgin,
Pipe and Tube Conference
- May 21 - 22, 2024
- Omaha, NE
World-Class Roll Forming Workshop
- June 5 - 6, 2024
- Louisville, KY
Advanced Laser Application Workshop
- June 25 - 27, 2024
- Novi, MI