Senior Editor
- FMA
- The Fabricator
- FABTECH
- Canadian Metalworking
Categories
- Additive Manufacturing
- Aluminum Welding
- Arc Welding
- Assembly and Joining
- Automation and Robotics
- Bending and Forming
- Consumables
- Cutting and Weld Prep
- Electric Vehicles
- En Español
- Finishing
- Hydroforming
- Laser Cutting
- Laser Welding
- Machining
- Manufacturing Software
- Materials Handling
- Metals/Materials
- Oxyfuel Cutting
- Plasma Cutting
- Power Tools
- Punching and Other Holemaking
- Roll Forming
- Safety
- Sawing
- Shearing
- Shop Management
- Testing and Measuring
- Tube and Pipe Fabrication
- Tube and Pipe Production
- Waterjet Cutting
Industry Directory
Webcasts
Podcasts
FAB 40
Advertise
Subscribe
Account Login
Search
Boosting velocity in laser cutting even with disparate material thicknesses
Cutting technology, smart storage streamline flow at Tigmaster Precision Fabrication
- By Tim Heston
- December 20, 2021
- Article
- Materials Handling
Tigmaster Precision Fabrication exemplifies how metal fabrication job shops defy specialization. The 45-employee company in Baroda, Mich., cuts everything from the very thin to the extraordinarily thick. One day you might find the company’s precision plasma and oxyfuel table in action, flame cutting special stock that could be up to 13 in thick. Another day you might see underwater plasma cutting of 2-in.-thick stainless steel—material that wasn’t ordered for the job but instead pulled from stock left over from a previous job several months before.
And every day, you’ll see high-powered fiber lasers in action. The shop purchased an 8-kW fiber laser in 2016, and earlier this year it installed a 10-kW system complete with adaptive technology in the laser cutting head. Both machines slice through metal a few thousandths thin all the way up to 0.75 in. and occasionally even thicker.
Even before the latest laser addition earlier this year, Tigmaster had serious cutting capacity, which is why Casey Gibson, sales and manufacturing engineer, knew something was up when he opened a window in the enterprise resource planning (ERP) system. One laser had just cut a few shims out of gauge stock. According to clock-in and clock-out data in the system, the job took 50 minutes. It should have taken less than 10.
“We knew we weren’t spending all that time laser cutting. We were digging out material,” Gibson said.
Many in this business can probably relate to Tigmaster’s story. For years the fabricator had focused on increasing cutting capacity. That had been the shop’s claim to fame, after all. The job shop was one of the first operations in Michigan to buy a laser back in 1991, and the operation continues to push the laser cutting envelope. But a shop’s overall cutting capacity isn’t measured by the speed of the cutting head. It’s instead governed by the velocity of work as it travels from the first operation through its last.
When Is Cutting Finished?
Those clock-in-and-out numbers on the ERP weren’t entirely surprising. Gibson and other managers knew they had a material handling problem for some time. “We were double- and even triple-ordering material because we couldn’t find a skid of 7 gauge that we ordered six months ago,” Gibson said. “So we ordered the material again. We had so much excess material that we just shouldn’t have had, stacked four or five rows deep.”
Up until this point, managers had thought it was just the cost of doing business as a quick-response job shop with an extraordinarily high product mix. But as the shop continued to invest in high-powered fiber lasers, Gibson said that he and his team knew that its current material handling strategy really wasn’t sustainable.
“Back in 2016 we had just bought one of the fastest fiber lasers on the market,” Gibson said. “We knew we had to get organized to feed this thing, or we’d defeat the purpose of buying a new fiber laser.”
Soon the operation began to take a broader view of cutting capacity. Inches per minute is a piece of the puzzle, but it’s still just one piece. The true measure of a cutting operation starts as material is found and retrieved from raw stock, placed on the shuttle table, cut, denested, and transported to the next operation. If cut blanks aren’t ready to be processed at the next operation, the cutting operation really isn’t “finished.”
For years Tigmaster had perfected and minimized the use of microtabbing. Tabs, if they were used at all, were never thicker than they needed to be, and they were placed in ways such that cut blanks twisted free easily. From there, operators placed blanks on custom roller carts lined with carpet to ensure pieces weren’t scuffed or scratched. They placed small parts in the center of the cart and propped large blanks vertically on either side, then sent work to forming and beyond. The flow downstream to flat-part deburring (if needed), forming, and welding wasn’t an issue. The problem, managers knew, was upstream.
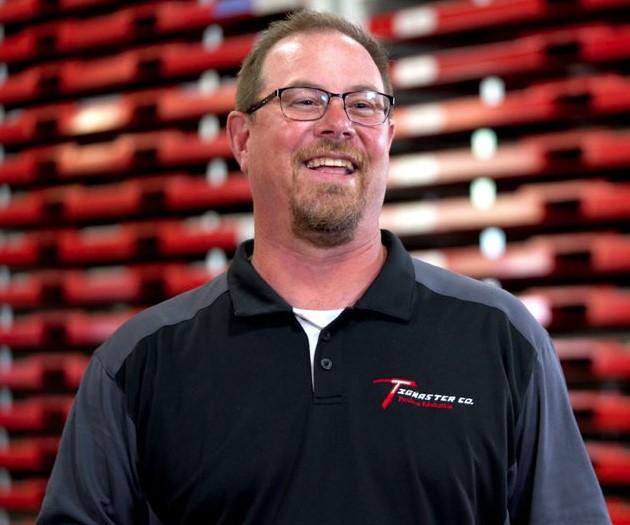
Casey Gibson, sales and manufacturing engineer at Tigmaster, recalls how employees had to dig through stacks of wooden pallets four rows deep.
Controlling WIP in a Job Shop
As a job shop, Tigmaster needs a healthy amount of raw stock to stay competitive, a reality that has become even more important when immediately receiving ordered material isn’t a guarantee (especially in 2021). Because of the product mix and space constraints, Tigmaster’s managers chose not to go with an automated tower system, but they knew they couldn’t continue with the status quo.
Conventional lean thinking would promote simply limiting raw material, then organizing what the shop has on conventional racking. After all, does a job shop really need so many different grades and thicknesses?
Gibson nodded yes, vigorously. Having material on hand could be seen as the keystone of Tigmaster’s business model. The company works diligently to minimize its work-in-process (WIP) by measuring its always-shifting bottlenecks, whether the WIP buffers grow. The greater those WIP buffers are, the longer Tigmaster’s lead time.
“Every two weeks we evaluate our bottlenecks,” Gibson said, adding that as the job mix changes, the scheduler releases work to the primary cutting process to “steady the flow through the shop and to ease our bottlenecks.”
Of course, it’s difficult to “steady the flow” through a laser process that isn’t predictable. To make the process rock-solid calls for reducing variability throughout every task occurring in and around the laser: material retrieval, nesting, cutting process quality, denesting, and remnant management. The cutting operation is a dance with a lot of moving parts, and the first step occurs in material storage.
Raw Stock Strategy for the Job Shop
A job shop like Tigmaster can’t rely on filler parts to complete a nest on a sheet. Yes, some customers might order a cutting job but not need it for several weeks. This gives the programmer the freedom to nest some parts ahead of time should he have space to fill on a sheet. That said, the cut blanks don’t sit as WIP for weeks; the company moves them downstream with everything else and delivers them early—which, of course, usually isn’t a problem for customers.
Even so, Tigmaster can’t control when those opportunities arise. The shop also wants to get as much out of the material as it can, especially if the material grade has long lead times (and these days, more grades fall into this category). The last thing the shop wants is to nest parts loosely on an oddball-grade sheet and, considering the labor involved handling remnants, just scrap what it doesn’t use. It needs to make good use of its remnants. And because of the variety of material Tigmaster uses, storing remnants randomly near the machine, or even organized in separate vertical racks, just isn’t practical. Depending on the job mix, operators would fill up those nearby racks in no time flat.
Tigmaster needed a high-density storage strategy that could handle both raw stock and remnants and do it in as little space as possible. And in early 2021 the job shop set that strategy in motion. Tigmaster purchased a high-density, cartridge-based storage system from Waukesha, Wis.-based Lean Manufacturing Products. Now, instead of hunting for hours among stacks of wooden pallets and conventional racking, a driver retrieves a work order, drives up to the rack and, after a glance, reads highly visible labels on the storage racks, laser-etched directly into the metal for durability.
Everything is organized logically by grade and thickness. Each holding up to 5,000 lbs., cartridges holding thicker material go below cartridges holding thinner material. It’s like a library card catalog; if the fork truck driver knows the number (grade and thickness), he needn’t spend time hunting.
The driver slides the forks neatly into the base of a metal cartridge and drives that to a staging table adjacent to the laser. When that cartridge arrives, the laser operator usually has a stack of full sheets to work with. Sometimes, though, he also has a sheet remnant, separated by a layer of cardboard (to prevent marring), stored on top of those full sheets.
That remnant isn’t a surprise. The shop’s ERP system tracks remnants in specific cartridges. It might, for instance, say it has 20.4 sheets of 16-ga. 304 stainless. That 0.4 is the remnant.
In these cases, the drag-and-drop functionality of modern laser controls comes into play. Programmers in the office create nests for full sheets, but they leave the programming of remnants to the shop floor. In fact, new control technology has made cut programming on remnants much less arduous than it used to be.
Earlier this year, the company purchased a Mitsubishi GX-F 10-kW fiber laser, which features cameras inside the work envelope. An operator loads the remnant, after which the machine positions the piece and activates the camera. With a view of the actual remnant on the machine control, the operator drags and drops parts (represented by blank outlines) directly onto the sheet—a huge time savings, especially for low-run or one-off work.
Laser Cutting Head Advancements
Once cutting commences, another camera is activated, this one integrated into the cutting head itself, along with various other sensors. “The laser has a cutting head driven by artificial intelligence,” Gibson said, adding that, like having the first laser in the 1990s and the first high-powered fiber laser in 2016, “we’re the first fabricator in Michigan to have this kind of AI-based technology.”
The sensors detect the cut quality by the look and sound of the cutting action, which can change depending on the quality of the plate. “So, if we’re cutting thick material like 0.75-in. stainless steel, the machine might run conventionally at 30 inches a minute,” Gibson explained, “but sometimes, when the conditions are just right, it can go up to 45 or 50 inches a minute. Conversely, it might slow to 20 inches per minute.”
The head optics and beam parameters work in concert with fine-tuned assist gases. This includes using nitrogen-oxygen mixes, which are particularly useful when piercing thick stainless. The system also offers a mode that incorporates an ultra-dried-shop-air shield around a column of nitrogen assist gas.
He added that, overall, the system’s increased use of shop air—both for applications using only shop air and in combination with nitrogen—has cut down the company’s bulk nitrogen use by nearly 70%.
For stainless cutting, the system uses a cutting assist gas strategy that incorporates a mix that includes high-pressure shop air. “The result looks like a nitrogen cut, but it’s twice as fast, there’s no burr, and it doesn’t change color,” Gibson said. He added that the greatest benefit isn’t the speed but the burr- and color-free cut edge. Finishing a cutting program in record time is great, but minimizing or eliminating secondary operations (like deburring and polishing) is even better.
About Adaptability
To avoid cross-contamination, Tigmaster segments its material into two areas: one dedicated to stainless and aluminum, another dedicated to carbon steel. One fiber laser cuts stainless and nonferrous, while the other handles the ferrous metals. The same segmentation applies to deburring, grinding, welding, and polishing.
Beyond this, Tigmaster’s shop is arranged for maximum flexibility. The most commonly used material sits in high-density racks near their point of use (one of the two fiber lasers), while less common stock—which the shop might run once or twice a month—is stored out of the way in one corner of the building.
Feed the Beasts
Tigmaster’s leaders have had differentiation top of mind for decades, a trait that has stayed with the company since it launched in 1981 as a tool and die repair shop. “At that time the town of Baroda probably had more tool and die shops than anywhere else per capita in Michigan,” Gibson said, “so launching a shop that welded and repaired dies just made sense.”
Of course, tool and die work isn’t what it was—a consequence of globalization, market forces, and companies failing to adapt and differentiate. The shop still performs repair work, including thermal stress relief. But most revenue now comes from cutting, bending, polishing, and welding sheet metal and plate.
The operation invested in technology early and often, moving to the CNC turret punch and then the laser shortly thereafter. The owner knew the shop could grow by selling cutting capacity and wanted more of it. That strategy continues to this day, but again, company leaders think about cutting capacity from a broad perspective, considering the velocity of material from storage through the laser and on to the next operation.
In August the company broke ground on an addition that will be dedicated to storage. Gibson paused and chuckled a bit. “Our last addition was for material storage, and we ended up instead putting a new laser in the space.”
He added, however, that this latest addition might be different. With fiber lasers becoming so powerful, just a few machines give an operation extraordinary capacity. A small amount of space can be highly productive—if, that is, the shop has material to feed the beasts.
About the Author
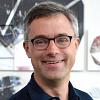
Tim Heston
2135 Point Blvd
Elgin, IL 60123
815-381-1314
Tim Heston, The Fabricator's senior editor, has covered the metal fabrication industry since 1998, starting his career at the American Welding Society's Welding Journal. Since then he has covered the full range of metal fabrication processes, from stamping, bending, and cutting to grinding and polishing. He joined The Fabricator's staff in October 2007.
Related Companies
subscribe now
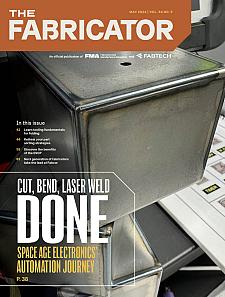
The Fabricator is North America's leading magazine for the metal forming and fabricating industry. The magazine delivers the news, technical articles, and case histories that enable fabricators to do their jobs more efficiently. The Fabricator has served the industry since 1970.
start your free subscription- Stay connected from anywhere
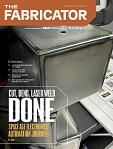
Easily access valuable industry resources now with full access to the digital edition of The Fabricator.
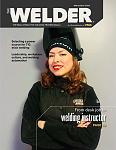
Easily access valuable industry resources now with full access to the digital edition of The Welder.
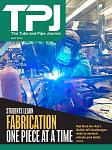
Easily access valuable industry resources now with full access to the digital edition of The Tube and Pipe Journal.
- Podcasting
- Podcast:
- The Fabricator Podcast
- Published:
- 04/16/2024
- Running Time:
- 63:29
In this episode of The Fabricator Podcast, Caleb Chamberlain, co-founder and CEO of OSH Cut, discusses his company’s...
- Trending Articles
Tips for creating sheet metal tubes with perforations
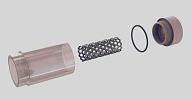
JM Steel triples capacity for solar energy projects at Pennsylvania facility
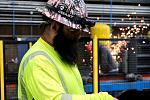
Are two heads better than one in fiber laser cutting?
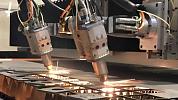
Supporting the metal fabricating industry through FMA
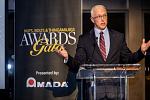
Omco Solar opens second Alabama manufacturing facility
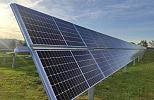
- Industry Events
16th Annual Safety Conference
- April 30 - May 1, 2024
- Elgin,
Pipe and Tube Conference
- May 21 - 22, 2024
- Omaha, NE
World-Class Roll Forming Workshop
- June 5 - 6, 2024
- Louisville, KY
Advanced Laser Application Workshop
- June 25 - 27, 2024
- Novi, MI