- FMA
- The Fabricator
- FABTECH
- Canadian Metalworking
Categories
- Additive Manufacturing
- Aluminum Welding
- Arc Welding
- Assembly and Joining
- Automation and Robotics
- Bending and Forming
- Consumables
- Cutting and Weld Prep
- Electric Vehicles
- En Español
- Finishing
- Hydroforming
- Laser Cutting
- Laser Welding
- Machining
- Manufacturing Software
- Materials Handling
- Metals/Materials
- Oxyfuel Cutting
- Plasma Cutting
- Power Tools
- Punching and Other Holemaking
- Roll Forming
- Safety
- Sawing
- Shearing
- Shop Management
- Testing and Measuring
- Tube and Pipe Fabrication
- Tube and Pipe Production
- Waterjet Cutting
Industry Directory
Webcasts
Podcasts
FAB 40
Advertise
Subscribe
Account Login
Search
Sawing, storage system specialist Kasto opens Chicago-area facility
Open house provides opportunity to introduce new storage system for tube, pipe, and bar
- By Eric Lundin
- September 14, 2018
- Article
- Materials Handling
Steel service centers and fabricators can see Kasto Inc.'s automated material storage and retrieval systems at its new facility in Schaumburg, Ill.
For modern service centers, running the business successfully requires making innumerable complex decisions, nearly all of which affect other decisions—how much floor space to dedicate to inventory, how much inventory to carry, and how varied an inventory to have; how much space to dedicate to equipment, how many fabrication processes to offer, how many machines to invest in, and when to upgrade them. Day-to-day operations and related decisions are a little easier, but again, each affects the others and has an influence on managing the day’s order volume, handling production contingencies, ordering raw material, compensating for staffing shortfalls, and so on and so forth, all day long.
Thankfully, some decisions are more straightforward, especially when considering equipment to retrieve material from inventory or equipment to cut it.
“It comes down to reducing cost per pick and cost per cut,” said Kasto Inc.’s Vice President Nikolis Wasynczuk, speaking at the company’s grand opening of its new facili-ty, showroom, and demo center in Schaumburg, Ill., near Chicago. The company’s automated storage and retrieval systems—systems designed and built to hold standard material sizes, yet customizable to suit each customer’s needs—uses tower structures to store material vertically, maximizing storage density while providing a way to keep material organized and inventoried, and makes the retrieval fast and streamlined.
A typical program for reducing cost per cut—by increasing the speed per cut—is Kastorespond, a program that provides dynamic cutting. After the operator enters workpiece parameters, the software determines the blade speed and feed rates. The machine monitors the cutting parameters as the job progresses and increases the cutting speed when possible—for example, cutting at normal speed when entering or exiting a tube, and cutting at a faster rate in the middle of a tube.
“It can increase the band speed by 50 percent,” Wasynczuk said.
Taking a stake in the future of additive manufacturing (AM), the company developed Kastowin amc (additive manufacturing cutting). Designed and built to separate components from base plates, the saw is equipped with a turning device to rotate parts upside-down for cutting. This orientation allows most of the chips to fall away from the cutting channel, rather than entering the cutting channel, which reduces blade wear. Another critical feature is its ability to capture most of the dust generated by cutting parts made by AM.
“The particulates generated when cutting such parts are less than 40 microns in diameter,” said Managing Partner Armin Stoltzer, identifying a potential health hazard.
The company is no stranger to the digital revolution, having built its first CNC band saw in 1980. The company’s recent work in the digital realm allows it to use augmented reality to determine how a proposed storage rack would fit into a customer’s facility, allowing the customer to make an informed decision before committing to an installation. Kasto also can work out the details of integrating a storage system into the customer’s existing work flow to determine production targets.
Its enterprise resource planning integration capability isn’t a proprietary system, but an open platform. For example, the company’s equipment and software are set up so that its storage systems can interface with other manufacturers’ machines. Its retrieval systems can deliver sheet material to a laser or plasma cutting system or punch press. The company’s storage algorithms use historical data and other information to maximize storage efficiency when returning drop sheets to storage. Another capability analyzes the inventory and historical work flow and works overnight to stage material to be as close as possible to the appropriate machines, setting up the following day for maximum productivity.
Fitting with the introduction of its new location, the company had a second introduction: its latest model, the KASTOecostore bar stock, a storage system designed and built for tube, pipe, bar, and other long products. Similar to the company’s other offerings, it uses standardized dimensions for the storage area. For example, rather than 5 by 10 ft. or 5 by 13 ft. for the X and Y dimensions, which are common for sheet metal storage, these racks measure approximately 3 by 22 ft. The height of each storage location is selectable and available in five heights, from 8 to 40 in. Each pallet holds a maximum of 1.2 or 3 tons, depending on the specific system, and system heights can be configured from 10 to 26 ft. high.
About the Author
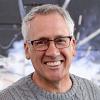
Eric Lundin
2135 Point Blvd
Elgin, IL 60123
815-227-8262
Eric Lundin worked on The Tube & Pipe Journal from 2000 to 2022.
Related Companies
subscribe now
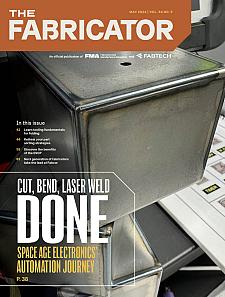
The Fabricator is North America's leading magazine for the metal forming and fabricating industry. The magazine delivers the news, technical articles, and case histories that enable fabricators to do their jobs more efficiently. The Fabricator has served the industry since 1970.
start your free subscription- Stay connected from anywhere
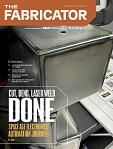
Easily access valuable industry resources now with full access to the digital edition of The Fabricator.
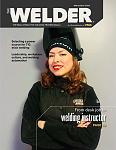
Easily access valuable industry resources now with full access to the digital edition of The Welder.
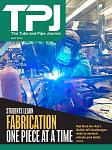
Easily access valuable industry resources now with full access to the digital edition of The Tube and Pipe Journal.
- Podcasting
- Podcast:
- The Fabricator Podcast
- Published:
- 04/16/2024
- Running Time:
- 63:29
In this episode of The Fabricator Podcast, Caleb Chamberlain, co-founder and CEO of OSH Cut, discusses his company’s...
- Trending Articles
Tips for creating sheet metal tubes with perforations
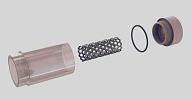
JM Steel triples capacity for solar energy projects at Pennsylvania facility
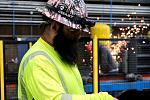
Are two heads better than one in fiber laser cutting?
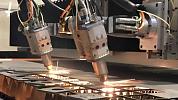
Supporting the metal fabricating industry through FMA
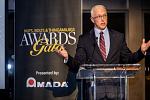
Omco Solar opens second Alabama manufacturing facility
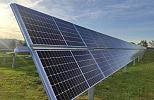
- Industry Events
16th Annual Safety Conference
- April 30 - May 1, 2024
- Elgin,
Pipe and Tube Conference
- May 21 - 22, 2024
- Omaha, NE
World-Class Roll Forming Workshop
- June 5 - 6, 2024
- Louisville, KY
Advanced Laser Application Workshop
- June 25 - 27, 2024
- Novi, MI