Senior Editor
- FMA
- The Fabricator
- FABTECH
- Canadian Metalworking
Categories
- Additive Manufacturing
- Aluminum Welding
- Arc Welding
- Assembly and Joining
- Automation and Robotics
- Bending and Forming
- Consumables
- Cutting and Weld Prep
- Electric Vehicles
- En Español
- Finishing
- Hydroforming
- Laser Cutting
- Laser Welding
- Machining
- Manufacturing Software
- Materials Handling
- Metals/Materials
- Oxyfuel Cutting
- Plasma Cutting
- Power Tools
- Punching and Other Holemaking
- Roll Forming
- Safety
- Sawing
- Shearing
- Shop Management
- Testing and Measuring
- Tube and Pipe Fabrication
- Tube and Pipe Production
- Waterjet Cutting
Industry Directory
Webcasts
Podcasts
FAB 40
Advertise
Subscribe
Account Login
Search
Technology Spotlight: The potential of self-driving vehicles in metal fabrication
Oxide coating application proves SDVs’ potential
- By Tim Heston
- August 17, 2017
- Article
- Materials Handling
Metal fabrication automation has come a long way in recent decades. Sheet storage towers send parts to laser cutting or punching. Then you have part offloading automation, which can take parts out of the nest and stack them. This technology can make sense for some applications, depending on the nest, production schedule, and available labor. On some punch presses, parts also can be sent down a chute for retrieval.
And therein lies the challenge—parts sent “for retrieval.” Despite advances in cutting, bending, and welding automation, people still move parts from one fabrication process to the next with fork trucks, carts, and other manual methods. You do find creative uses of conveyors in some cases. But for the most part, the act of moving jobs between operations remains almost entirely manual.
A material handling application at Hirotec America, through a partnership with self-driving vehicle supplier OTTO™ Motors, mounted with a dual-arm Motoman robot from Yaskawa America, shows how this situation might change.
Hirotec America provides weld assembly equipment for OEMs including GM, Fiat Chrysler, Ford, Toyota, and BMW. The division provides more than $200 million of Hirotec’s $1.6 billion worldwide sales.
The company has a long history of continuous improvement, and to that end it has scrutinized many of its processes, including a black oxide coating operation.
“We now have a mobile robot that can run from the machine shop to the black oxide tanks,” Krus said. “The robot brings the parts [in a basket] down to the workstation, loads the parts, runs it through the [black oxide] system, and then brings the parts to the next step in the process, without a human having to run back and forth.”
The robot does not move when the vehicle is in motion. But when the vehicle is stationary, the robot can move, and sensors mounted on the system ensure that if anyone gets within 3 feet of the robot arm, the robot shuts down.
The program operates by a set routine, and the robot operates with machine vision so that it can locate elements in its surroundings, including the basket of parts it needs to retrieve as well as the various stages of the black oxide dipping process.
An operator in the machine shop loads a basket with parts. The mobile robot then goes to the basket, picks it up and transfers it to the black oxide, where it dips the basket, washes the parts, then runs them through a salt bath and dries them. The robot is programmed to perform dipping motions so that it performs each step properly.
The self-driving vehicle came from OTTO Motors, a division of Clearpath Robotics based in Kitchener, Ont. The company differentiates the terms self-driving vehicle, or SDV, and automated guided vehicle. AGVs are, as their name suggests, physically guided in some way, such as with magnetic tape, beacons, bar codes, or by some other mechanism. They travel on fixed paths in a controlled space.
SDVs sense the world around them, using laser-based or similar technology, and use algorithms to navigate their own way through facilities. They adapt, learn, and, ideally, become more efficient and accurate over time. They also don’t require tapes, beacons, or other physical infrastructure to operate in a factory.
OTTO’s SDV in use at Hirotec can carry up to 3,400 pounds. “It uses the same foundational technology that’s used in the Google driverless car,” said Meghan Hennessey, marketing communications manager at OTTO Motors. Specifically, it uses sensors called LIDAR, or light detection and ranging. The technology works like sonar, with waves bouncing off objects to provide an image; but instead of sound, LIDAR uses light.
“It uses perception and mapping software capability, and doesn’t require any cables, tracks, or magnetic strips,” Hennessey explained, “and so no additional infrastructure is required when implementing the system.”
System management occurs through a software platform that communicates with the SDV via wifi. The SDV operates as a self-contained unit. The only element not on the vehicle is the battery charger. The vehicle even drives itself to the charging dock, plugs in, and starts charging automatically.
Krus said he next plans for the robot to be used to make parts for another Hirotec product line. These are products the company currently outsources to local suppliers, but by automating the process, Krus said he will be able to lower costs enough so that it makes sense to produce those products in-house.
“A lot of the suppliers actually have these parts shipped in from China before they sell them to us,” Krus said. “I’d rather make them in the U.S.”
Once this last phase is validated, the mobile robot will not only be working on its current black oxide operation, but it will also be changing fixtures and loading parts into a specific workcell, then taking the parts and delivering them to the next stage of production. “The next project will have the robot operate two cells,” Krus explained, “the first being the black oxide and the second being a [gas metal arc] welding cell. At the second cell, the robot will remove flexible fixture units and place them in storage; pick up new units and install them to the fixture; then pick up parts to be loaded to the fixture. Once the part is welded together, it will be removed and the process will be repeated.”
Where else could Hirotec implement this technology? “Anywhere you have a repetitive act,” Krus said. “If we have a lot of variation, we’ll need extensive machine vision. Essentially, I see it taking on these jobs to free up our talented workforce to do more important things.”
Could versions of this technology apply to material handling in sheet metal fabrication? Krus reiterated that it depends on how repetitive and repeatable the task is—loading one part or part family time after time in a welding cell, carrying blanks from a laser to the press brake. As always, it will depend on the application specifics. But down the road, SDVs could help a fabricator get more work-in-process parts on the move.
Photos courtesy of OTTO Motors, 844-733-6886, www.ottomotors.com.
About the Author
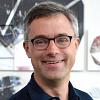
Tim Heston
2135 Point Blvd
Elgin, IL 60123
815-381-1314
Tim Heston, The Fabricator's senior editor, has covered the metal fabrication industry since 1998, starting his career at the American Welding Society's Welding Journal. Since then he has covered the full range of metal fabrication processes, from stamping, bending, and cutting to grinding and polishing. He joined The Fabricator's staff in October 2007.
subscribe now
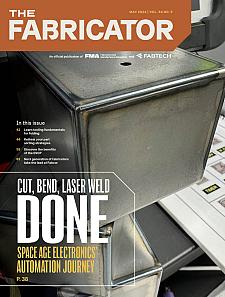
The Fabricator is North America's leading magazine for the metal forming and fabricating industry. The magazine delivers the news, technical articles, and case histories that enable fabricators to do their jobs more efficiently. The Fabricator has served the industry since 1970.
start your free subscription- Stay connected from anywhere
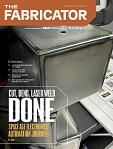
Easily access valuable industry resources now with full access to the digital edition of The Fabricator.
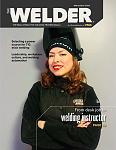
Easily access valuable industry resources now with full access to the digital edition of The Welder.
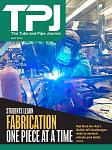
Easily access valuable industry resources now with full access to the digital edition of The Tube and Pipe Journal.
- Podcasting
- Podcast:
- The Fabricator Podcast
- Published:
- 04/16/2024
- Running Time:
- 63:29
In this episode of The Fabricator Podcast, Caleb Chamberlain, co-founder and CEO of OSH Cut, discusses his company’s...
- Trending Articles
Tips for creating sheet metal tubes with perforations
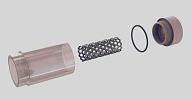
Are two heads better than one in fiber laser cutting?
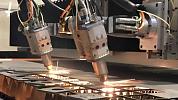
Supporting the metal fabricating industry through FMA
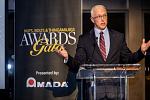
JM Steel triples capacity for solar energy projects at Pennsylvania facility
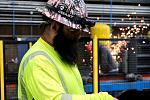
Omco Solar opens second Alabama manufacturing facility
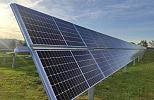
- Industry Events
16th Annual Safety Conference
- April 30 - May 1, 2024
- Elgin,
Pipe and Tube Conference
- May 21 - 22, 2024
- Omaha, NE
World-Class Roll Forming Workshop
- June 5 - 6, 2024
- Louisville, KY
Advanced Laser Application Workshop
- June 25 - 27, 2024
- Novi, MI