- FMA
- The Fabricator
- FABTECH
- Canadian Metalworking
Categories
- Additive Manufacturing
- Aluminum Welding
- Arc Welding
- Assembly and Joining
- Automation and Robotics
- Bending and Forming
- Consumables
- Cutting and Weld Prep
- Electric Vehicles
- En Español
- Finishing
- Hydroforming
- Laser Cutting
- Laser Welding
- Machining
- Manufacturing Software
- Materials Handling
- Metals/Materials
- Oxyfuel Cutting
- Plasma Cutting
- Power Tools
- Punching and Other Holemaking
- Roll Forming
- Safety
- Sawing
- Shearing
- Shop Management
- Testing and Measuring
- Tube and Pipe Fabrication
- Tube and Pipe Production
- Waterjet Cutting
Industry Directory
Webcasts
Podcasts
FAB 40
Advertise
Subscribe
Account Login
Search
Process automation meets oxyfuel cutting
How technological advances can change oxyfuel perceptions
- Updated October 2, 2019
- October 2, 2019
- Article
- Oxyfuel Cutting
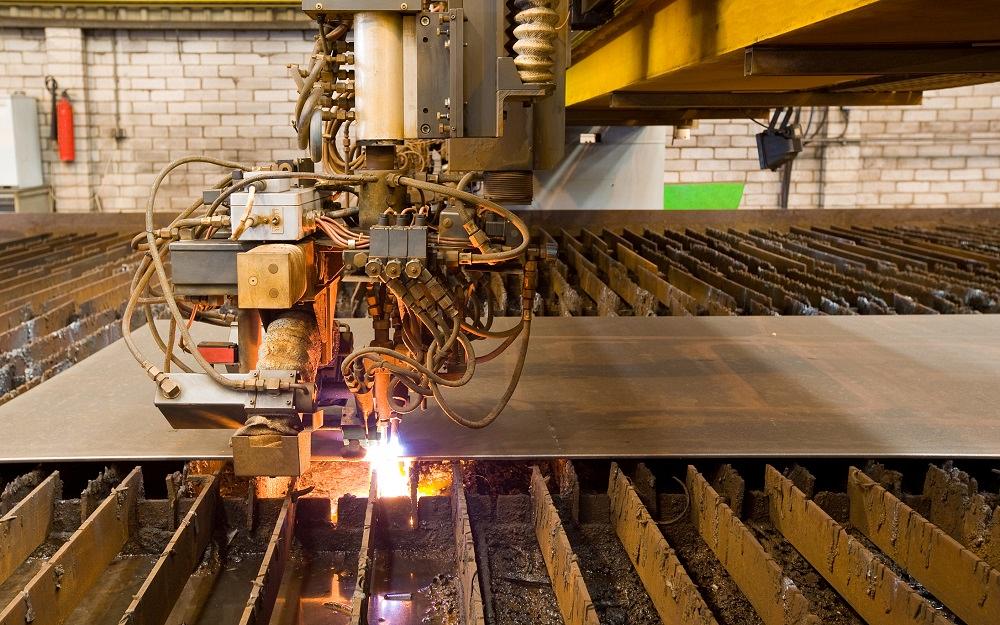
Oxyfuel cutting is often seen as old, boring, perhaps destined for extinction. Automation can change this perception entirely. Getty Images
Editor’s Note: This article is based partly on “Oxyfuel Cutting: What Is Required for a Fully Automated Process,” to by presented at FABTECH, Nov. 11-14, Chicago, by Kurt Nachbargauer, president, IHT Automation.
Of all the plate cutting technologies, oxyfuel cutting doesn’t have the best reputation. It’s the classic “heavy manufacturing” process, marketed through images of dark plant floors as a backdrop for bright sparks from rooster tails created by a row of torches. Ironically, all those spark plumes might be a sign of a less-than-ideal piercing process that’s quickly eating away torch consumables.
Regardless, the reputation drives a perception that has shifted the industry toward other processes. Ambitious youth don’t look to oxyfuel cutting but instead to the plasma and, especially, the laser—seemingly space-age compared to oxyfuel cutting, which has been around for more than a century.
So the ambitious youth avoids oxyfuel, making recruitment and (especially) training a challenge. Oxyfuel also happens to be the most manual of all thermal cutting options, so training is challenging even for the most ambitious and technically apt.
Because manufacturers have trouble recruiting good operators, they avoid the process and instead turn to more automated processes like plasma and, for material 1 in. and less, the laser. Operations end up pushing their plasma and lasers to the limits.
But what if oxyfuel cutting didn’t require so much operator attention? Today’s process automation can make this a reality. Doing so might eventually shift people’s perception of the process and, ultimately, its place in metal fabrication.
An Objective Look
Note that in the current context, “automation” refers not to material handling but simply the basic process settings—the tasks required between pulling up a cut program and initiating it. For most modern cutting processes, operators pull up a program on the CNC, check a few settings, then initiate cutting. Even without fully lights-out settings, one operator can run a host of laser cutting machines at once.
Although modern oxyfuel cutting machines do have a CNC that stores programs and controls torch motion, the process setup is different. Many operators still light flames manually. And when they adjust the oxygen and fuel gases—be they acetylene, propylene, or anything else—they adjust the flame to ensure the primary and secondary flames are just right for preheating.
The experienced operator “reads” the plate. Just as the metal reaches kindling temperature, the operator adjusts the settings again to commence piercing and cutting. It can take months or even years to learn all these intricacies. With few people looking at oxyfuel as a “technology of the future,” fewer people end up specializing in oxyfuel, so the industry has fewer people with experience than ever. And the vicious cycle continues.
Meanwhile, companies continue to watch the performance of their oxyfuel operations diminish. Having to learn a process that remains largely manual, new operators burn up consumables. Parts require an excessive amount of grinding. Productivity is abysmal, the process unpredictable, so it’s no wonder that fabricators seek alternatives. Oxyfuel is seen as an inherently slow process that makes sense only for applications where it isn’t cost-effective to invest in a more expensive cutting system. Other times the material is simply so thick that oxyfuel is the only thermal cutting option.
Oxyfuel Benefits
If you were to see a video that compared travel speeds of the most common thermal cutting processes for plate—oxyfuel, plasma, and increasingly the laser—the plasma and laser sources would of course speed ahead of the oxyfuel, particularly in thinner plate. As thickness grows, the speed advantage isn’t quite so pronounced.
What often isn’t considered in this equation is the batch size. If a shop processes a high mix of low-volume material and it’s looking for high cutting throughput, plasma and laser might fill the need perfectly.
But when volumes grow, and you’re cutting a nest full of identical pieces, the story changes. That’s because oxyfuel can have two, four, a half-dozen, or even more cutting torches working in tandem. In a one-on-one race between a plasma and oxyfuel torch, the plasma might win, depending on the material thickness, but six oxyfuel torches working in tandem would likely finish cutting the nest first.
Oxyfuel’s edge quality shouldn’t be taken for granted either. Oxyfuel is far hotter than waterjet cutting, of course, but it’s cooler than plasma cutting. The width of the heat-affected zone (HAZ) on either side of the kerf can be significant, but the metal itself doesn’t get as hot during oxyfuel cutting, so subsequent cooling doesn’t induce such a dramatic temperature change. This mitigates edge hardening, a fact especially appreciated by those in the welding department.
In fact, most of the energy from the oxyfuel flame itself is used during preheating and piercing. Once the torch starts moving down the cut line, upwards of 80 percent of the cutting energy comes from the chemical reaction between iron and oxygen.
Configured and operated correctly, oxyfuel cutting also offers tight perpendicularity or angularity tolerances, based on the ISO 9013 standard. The chemical reactions from the oxyfuel process should leave a smooth cut surface with minimal if any slag at the bottom.
Subtleties of Setting the Flame
Of course, all these benefits really can’t be realized if the oxyfuel operation is rife with quality and productivity problems. This goes back to oxyfuel being a largely manual process that isn’t easy to learn.
Imagine a problematic oxyfuel operation that continues to produce bad parts and continually falls behind schedule. This is a huge deal, considering a delay in the first manufacturing step dominoes into monumental delays in the shipping department. What’s going on?
When you observe the operation, you notice that preheat time is taking far too long for the material thickness. The piercing operation is generating far too much splash, and the resulting edge quality is subpar. The problem has to do with flame adjustment. Specifically, the flame isn’t efficiently heating the material and the pierce is inefficient.
An experienced operator should “read the flame” as it progresses through ignition, preheating, piercing, and cutting. As its name suggests, the ignition flame occurs when the operator ignites the flame, and the flame parameters (gas settings) should be less than or at most equal to the preheating parameters.
To achieve the proper preheating flame, the operator must adjust the gas values to achieve the optimal primary flame, which is a high-temperature mix of heating oxygen and fuel gas, and a secondary flame, which is a low-temperature mix of ambient air and fuel gas.
He first adjusts the heating oxygen and fuel gas pressure, fine-tuning to achieve the flame he needs—with a bright spot of the primary flame near the orifice of the torch, but not extending too far beyond that orifice. The secondary flame and oxygen jet should be narrow and compact, extending a few inches before quickly dissipating at the flame edge.
Next comes the transition from the preheating flame to the cutting flame. Specifically, the heating oxygen and fuel gas pressure stay constant, while the operator adds the cutting oxygen. When cutting, the flame’s primary cone looks bright near the torch orifice, and a concentrated jet extends beyond.
Gas settings are critical. A primary cone that extends too far beyond the orifice, broadening the secondary flame and jet, often means the fuel gas pressure is too high. An experienced operator will see this and hear this as the “hiss” of the flame descends in pitch. A primary cone that’s dim or invisible, with the bright spot seemingly shrinking back into the orifice in front of a diminishing secondary flame, means the fuel gas pressure is too low. Accordingly, the gas flow will sound thin and constricted.
If the operator sees a bright primary flame but a wide, long, and diffuse secondary flame, the heating oxygen pressure is set too high. If the secondary flame dims and the primary flame becomes slightly less compact, the heating oxygen pressure is set too low.
Flame adjustment is really just one oxyfuel cutting parameter. The experienced operator needs to know optimal preheat time too before edge-starting or piercing into the plate. If he continually loses the cut, chances are the preheat time was too short or the preheat flame wasn’t set correctly. If burnt, black, difficult-to-clean slag hangs off the bottom surface of the kerf, chances are the preheat was too long or, again, the flame was set incorrectly.
Then there’s the cutting speed to consider and the right gas pressure for that speed; and the effects of cutting around sharp corners versus a straight line. Then there’s the height settings as the torch transitions from preheating to piercing to cutting. Get too close during piercing and the splash destroys consumables in a hurry. Too far away and you have an inefficient pierce.
The variables go on and on, and each intertwines with the others. For instance, preheating time relates directly to the preheating flame. The operator needs enough energy to penetrate the material as effectively and quickly as possible. A flame that is too hot will induce so much energy (and chemical reactions between oxygen and iron) into the pierce hole that you’ll end up with a large pierce hole with excessive slag. Similar problems occur if the preheat time is too long.
Even worse, because setting the flame and numerous other variables are all manual, tribal knowledge dominates the industry—and that knowledge might vary from one tribe (one shop floor) to the next. Visit a half-dozen shops and you’ll see a half-dozen operators adjust the oxygen in different ways as they transition from preheating to piercing to cutting. Some add a lot more cutting oxygen, some might not add enough, some might increase the flow of cutting. Best practices vary, which in turn makes the process less reliable.
Enter Automation
Why does oxyfuel cutting remain manual? Part of it has to do with the machinery market. If fabricators want a turnkey laser or plasma system, they have options. Being complete systems, these machines come with factory settings with tech tables full of time-tested cutting parameters.
If fabricators want a turnkey oxyfuel cutting system, they have fewer options. Quite often the gas delivery system (valves and plumbing) comes from one supplier, the torch from another supplier, the table from another. Sometimes the fabricator ends up integrating the entire system in-house.
Another reason the process isn’t automated is that it stands apart from cutting processes like plasma. A plasma arc is either on or off; there’s no middle ground. Cutting with an arc gives the process electrical characteristics like amps and volts, which can be sensed in real time and adjusted for.
Oxyfuel cutting is largely a chemical process; again, most of the cutting occurs thanks to the reaction between oxygen and iron. Also, a flame isn’t binary—meaning it isn’t just on or off—so adapting it to the ones and zeros, the “digital guts” of modern factory automation, can be a challenge. That said, the ideal flame for the application does have certain aspects that can be sensed and translated to the language of automation.
Running an oxyfuel system with automation, the operator wouldn’t undergo so many manual steps to initiate a cutting process. He would instead pull up the cutting program on the control, ensure the material and torch are clean and ready, then initiate the cutting cycle. The torch ignites automatically, and the system sets the flame and adjusts automatically as piercing and cutting commence.
The torch can detect conditions ripe for flashback and, through a direct connection to the CNC, can shut the gas off before flashback occurs and communicate that fact to the operator.
Height sensing and control are central to this. Height for piercing and cutting can be set based off a cutting database. Capacitive sensing also helps the torch avoid obstacles like surface slag and ensure proper clearance during bevel cutting.
This and similar automation change the equation when it comes to choosing the best cutting process for an application. It makes it more than just about material thickness. For instance, say a factory has to cut 0.75-in.-thick carbon steel. Plasma cutting would be the conventional choice, but a fabricator might choose an automated oxyfuel process.
The inherent qualities of the oxyfuel process meet the application’s part geometry and throughput requirements. The only reason the fabricator would have gone to plasma cutting would have had to do with process repeatability: that is, the ability for an oxyfuel cutting operator to consistently produce parts in what is considered (at least for oxyfuel) thin material. Automating the process settings mitigates this concern.
Automation Builds a Foundation
At present many still view oxyfuel cutting as the dinosaur of the heavy fab shop floor—understandably so, considering the technology’s roots go back to the 1850s. But just because a technology has deep roots doesn’t mean it’s rooted in place and forever static.
It’s an old debate: Do manufacturers seek out automation because they can’t find skilled operators? Or is automation simply more efficient? In the short term it’s probably the former, but in the long term it’s probably the latter. In one sense, automation is part of the natural evolution of most manufacturing technologies. If it can be automated in a cost-effective way, it should be. However, automation should not eliminate operator education. The combination generates the best results.
For oxyfuel cutting in particular, automation can help break the vicious cycle and attract more people to the cutting process. It shouldn’t take operators years to learn the automated process, which helps make these new employees more productive earlier in their careers. They climb the ladder, learn to use automation to perfect oxyfuel cutting, and use the process in new ways. In this sense, process automation builds the foundation for technological development.
subscribe now
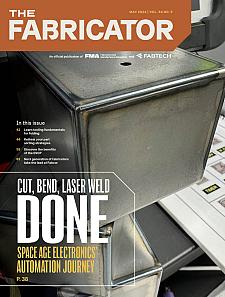
The Fabricator is North America's leading magazine for the metal forming and fabricating industry. The magazine delivers the news, technical articles, and case histories that enable fabricators to do their jobs more efficiently. The Fabricator has served the industry since 1970.
start your free subscription- Stay connected from anywhere
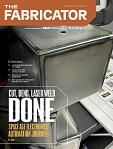
Easily access valuable industry resources now with full access to the digital edition of The Fabricator.
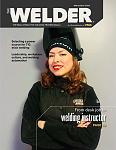
Easily access valuable industry resources now with full access to the digital edition of The Welder.
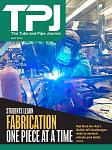
Easily access valuable industry resources now with full access to the digital edition of The Tube and Pipe Journal.
- Podcasting
- Podcast:
- The Fabricator Podcast
- Published:
- 04/16/2024
- Running Time:
- 63:29
In this episode of The Fabricator Podcast, Caleb Chamberlain, co-founder and CEO of OSH Cut, discusses his company’s...
- Trending Articles
Tips for creating sheet metal tubes with perforations
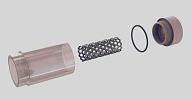
JM Steel triples capacity for solar energy projects at Pennsylvania facility
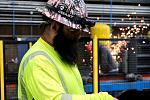
Are two heads better than one in fiber laser cutting?
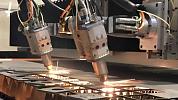
Supporting the metal fabricating industry through FMA
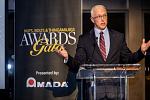
Omco Solar opens second Alabama manufacturing facility
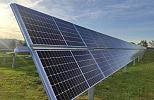
- Industry Events
16th Annual Safety Conference
- April 30 - May 1, 2024
- Elgin,
Pipe and Tube Conference
- May 21 - 22, 2024
- Omaha, NE
World-Class Roll Forming Workshop
- June 5 - 6, 2024
- Louisville, KY
Advanced Laser Application Workshop
- June 25 - 27, 2024
- Novi, MI