Editor-in-Chief
- FMA
- The Fabricator
- FABTECH
- Canadian Metalworking
Categories
- Additive Manufacturing
- Aluminum Welding
- Arc Welding
- Assembly and Joining
- Automation and Robotics
- Bending and Forming
- Consumables
- Cutting and Weld Prep
- Electric Vehicles
- En Español
- Finishing
- Hydroforming
- Laser Cutting
- Laser Welding
- Machining
- Manufacturing Software
- Materials Handling
- Metals/Materials
- Oxyfuel Cutting
- Plasma Cutting
- Power Tools
- Punching and Other Holemaking
- Roll Forming
- Safety
- Sawing
- Shearing
- Shop Management
- Testing and Measuring
- Tube and Pipe Fabrication
- Tube and Pipe Production
- Waterjet Cutting
Industry Directory
Webcasts
Podcasts
FAB 40
Advertise
Subscribe
Account Login
Search
Automation energizes structural steel fab operation
Stehl Corp. takes a step to keep up with growth opportunities
- By Dan Davis
- May 5, 2018
- Article
- Plasma Cutting
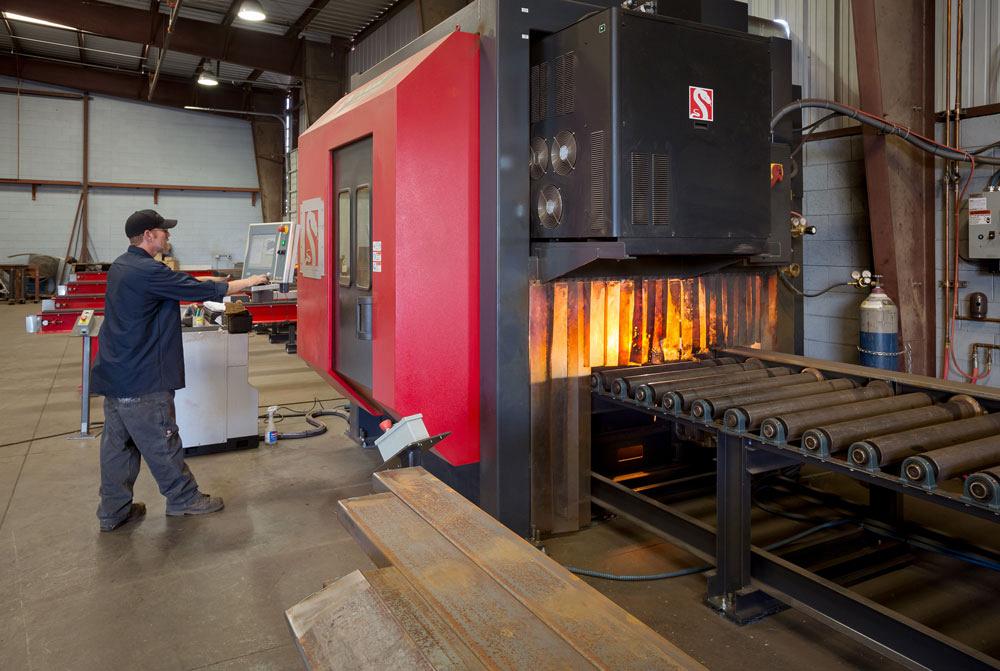
Figure 1
A new PythonX beam processing line has helped Stehl Corp. increase its production capacity, which has helped the company to grow its business.
Sometimes a fabricator needs a sign to know when to make that jump in an attempt to get to the next level of growth.
Paul Stehl, who has been around construction and welding for almost 30 years, said he has always had his sights on the future, even during the earliest days of his Phoenix business, now known as Stehl Corp. He struck out on his own in 1999 after having worked for a structural steel fabricator for several years. In those days, the company was a basic miscellaneous and architectural metals fabricator, taking on whatever projects were available, such as side yard gates for little old ladies, Stehl said. While establishing a steady stream of work to act as a foundation for the business, Stehl was still focused on the future.It started with small structural steel projects like a parking structure and ultimately led to large jobs. Stehl was comfortable enough with the company’s growth in 2003 that he relocated to accommodate larger projects; only about three years later he moved again for the same reason.
In 2009 Stehl Corp. acquired property next to its existing facility to take on even more structural steel work. This was no longer a shop waiting on a phone call for fence fabrication or repair.
Around this time, Stehl said he knew that more opportunity awaited. The metropolitan Phoenix area was booming from the influx of retirees, corporate investment, and growth connected to Arizona State University. To take advantage, however, Stehl Corp. realized that it needed to automate some fabricating activities so that it could push through more volume.
In 2015 Stehl and his management team began investigating beam processing equipment that might work in their facility. This was no easy purchase, though.
“These things are pretty high-end pieces of equipment,” he said. “That makes it tough to write a check for it.”
A conversation with another fabricator reframed his thinking about the investment. On his way to FABTECH® in Chicago in 2015, Stehl said he was seated next to a vice president from the company where he was once general manager before starting his own firm. During the conversation, the other fabricator described how gaining automated beam processing capabilities was a game-changer for his company. He encouraged Stehl to follow through on the same plan.
That conversation provided the motivation to take that next step. The fact that he was going to a major tradeshow with the latest fabricating technology on display made the final decision even easier.
With assurances that the equipment could be installed quickly in early 2016, Stehl Corp. committed to purchasing a PythonX® beam fabrication system from Lincoln Electric. It turns out that Stehl got some pretty good advice on that plane ride (see Figure 1).
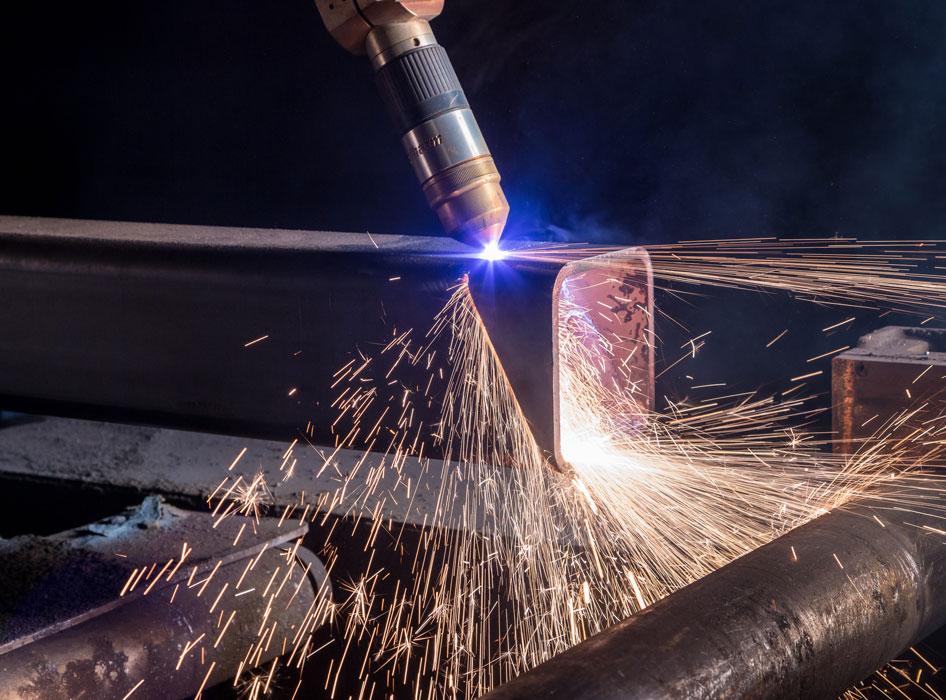
Figure 2
The beam processing equipment can make specialty cuts in a matter of seconds, whereas manual cuts of this nature would take longer.
Automation Changes the Fab Shop
Today Stehl Corp. has 80,000 square feet dedicated to fabrication. It had annual sales of $16.5 million last year and hopes to hit $18 million in 2018. The beam processing equipment played a huge role in this growth.
“I mean, just our ability to take on larger projects and be more confident and comfortable in taking on these jobs was huge,” Stehl said.
Almost all beams, columns, and structural shapes are fed through the PythonX equipment. A lot of that work involves plasma cutting holes for typical structural connections and preparing the structural members for full-penetration welds. Early on Stehl discovered that the equipment devoured metal like the shop floor had never seen before.
“It would knock out the pieces for a big stair job in no time at all,” Stehl said. “What might take us several days before to process now is being done in a matter of a few hours.”
That left additional time for more work, and Stehl Corp. has been aggressive in chasing that down. But, even running with two shifts, the steel fabricator has capacity to accommodate work from other fab shops.
Stehl Corp.’s beam processing system is somewhat unique in that it was purchased with automated material handling. In many instances, structural steel shops that are hesitant to spend a lot of money on automated equipment are downright petrified to spend additional dollars to remove manual material handling from the fabrication process. Stehl said he didn’t want to make that mistake, particularly as he wanted to create as much fabricating capacity as he could with the new equipment.“Far too often in our world, you get something and you go marginal with it. Then you invariably wish you had more to it. You wish that you would have done something more with it,” Stehl said.
Stehl wasn’t going to starve the new equipment as it waited for delivery of structural steel via lift truck or crane. That’s why the system is outfitted with both infeed and outfeed cross-transfers, as well as an infeed conveyor.
“I’m so glad we did that. It literally makes such a big difference for loading up,” Stehl added. “You can load up so much more stuff and have it staged and ready to go. It’s just more efficient that way.”
While Stehl Corp. has been able to boost its production efficiency, it also has reduced the need for rework. The new equipment is an important piece of the digitization of the manufacturing effort, which means the opportunity for human errors is minimized. All structural steel parts destined for the shop floor come from the building information model. The model provides the exact details for the shop drawings and the information that creates the CNC program for the PythonX. If the drawing is correct, the equipment will put the holes, the copes, the bevels, and the markings where they are supposed to be (see Figure 2).
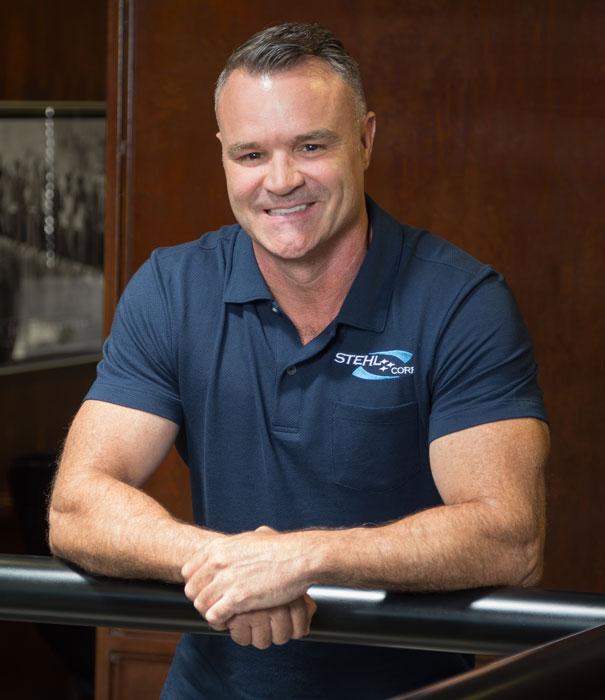
“It would knock out the pieces for a big stair job in no time at all. What might take us several days before to process now is being done in a matter of a few hours.” —Paul Stehl, Stehl Corp
“Even the greatest fabricator has an off day, and that can get very expensive,” Stehl said.
The Human Reaction
Most people might see this type of automation as a threat to jobs. After all, only one person is really needed to run the highly productive and accurate beam processing line at Stehl Corp. (Three people are trained to run the equipment: one for each of the two shifts and a backup.) But the opposite appears to be reality for Stehl. The equipment has enabled the company to take on more jobs, keeping fabricators busy with the filled pipeline of work.
“We’ve added more fabricators since the equipment was installed, and the plan is to add even more yet,” Stehl said.
He added that the machine has made fabricating work easier as well, taking some of the pressure off the jobs. For instance, one of the hardest parts of setting up a stair stringer is getting the very first running dimension reference point set. Well, the equipment automatically cuts and marks that point. From there the fabricator can measure and mark out the treads quickly.
Stehl knows that the equipment has positioned his company for future growth, and he believes his team is proud to be part of the steps being taken to prepare for future opportunities. So once again, he’s faced with a familiar question: Is it time to invest in more production capacity?
“We’re having conversations about that right now,” Stehl said. Gathering input to make informed decisions has proved fruitful for Stehl in the past, so it makes sense to follow that approach again. It’ll also be interesting to see who he sits next to on his next flight to FABTECH.
Stehl Corp., www.stehlcorp.com
Lincoln Electric, www.lincolnelectric.com
About the Author
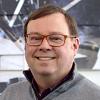
Dan Davis
2135 Point Blvd.
Elgin, IL 60123
815-227-8281
Dan Davis is editor-in-chief of The Fabricator, the industry's most widely circulated metal fabricating magazine, and its sister publications, The Tube & Pipe Journal and The Welder. He has been with the publications since April 2002.
subscribe now
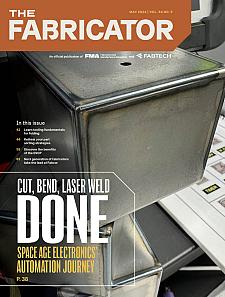
The Fabricator is North America's leading magazine for the metal forming and fabricating industry. The magazine delivers the news, technical articles, and case histories that enable fabricators to do their jobs more efficiently. The Fabricator has served the industry since 1970.
start your free subscription- Stay connected from anywhere
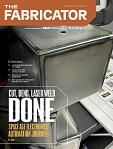
Easily access valuable industry resources now with full access to the digital edition of The Fabricator.
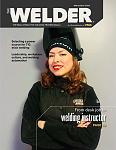
Easily access valuable industry resources now with full access to the digital edition of The Welder.
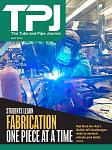
Easily access valuable industry resources now with full access to the digital edition of The Tube and Pipe Journal.
- Podcasting
- Podcast:
- The Fabricator Podcast
- Published:
- 04/16/2024
- Running Time:
- 63:29
In this episode of The Fabricator Podcast, Caleb Chamberlain, co-founder and CEO of OSH Cut, discusses his company’s...
- Trending Articles
Tips for creating sheet metal tubes with perforations
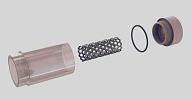
Are two heads better than one in fiber laser cutting?
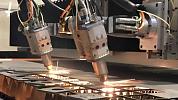
Supporting the metal fabricating industry through FMA
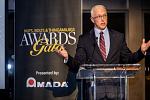
JM Steel triples capacity for solar energy projects at Pennsylvania facility
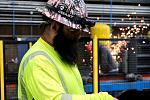
Omco Solar opens second Alabama manufacturing facility
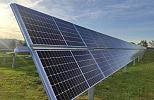
- Industry Events
16th Annual Safety Conference
- April 30 - May 1, 2024
- Elgin,
Pipe and Tube Conference
- May 21 - 22, 2024
- Omaha, NE
World-Class Roll Forming Workshop
- June 5 - 6, 2024
- Louisville, KY
Advanced Laser Application Workshop
- June 25 - 27, 2024
- Novi, MI