- FMA
- The Fabricator
- FABTECH
- Canadian Metalworking
Categories
- Additive Manufacturing
- Aluminum Welding
- Arc Welding
- Assembly and Joining
- Automation and Robotics
- Bending and Forming
- Consumables
- Cutting and Weld Prep
- Electric Vehicles
- En Español
- Finishing
- Hydroforming
- Laser Cutting
- Laser Welding
- Machining
- Manufacturing Software
- Materials Handling
- Metals/Materials
- Oxyfuel Cutting
- Plasma Cutting
- Power Tools
- Punching and Other Holemaking
- Roll Forming
- Safety
- Sawing
- Shearing
- Shop Management
- Testing and Measuring
- Tube and Pipe Fabrication
- Tube and Pipe Production
- Waterjet Cutting
Industry Directory
Webcasts
Podcasts
FAB 40
Advertise
Subscribe
Account Login
Search
Improve your fabrication shop's plasma consumables management
Modern technology helps the operator make the right changes at the right time
- October 3, 2022
- Article
- Plasma Cutting
One of the best ways to maintain uptime while plasma cutting is to recognize when plasma cutting consumables should or should not be replaced. Voortman Steel Machinery
Editor’s Note: This feature was adapted from a Voortman Steel Machinery and Hypertherm webinar, “How to improve your plasma consumable management,” on June 23. Speakers included Joey Schreur, business unit manager, plates, Voortman; Stef Rohaan, product manager, plates, Voortman; and Timo Lecher, consumable sales manager, Hypertherm.
Most companies running plasma cutting machinery feel like their shop floor team is doing well when it comes to replacing consumables. They trust that their operators are getting the most out of the plasma cutting machinery, optimizing equipment performance without sacrificing quality.
While these companies likely have every reason to believe in their machine operators, they also might want to check the used consumables box. That’s where the truth is evident: Sometimes people just have bad habits.
A great example of a bad choice is a plasma cutting machine operator changing consumables before a new job because they don’t want the consumables to wear out in the midst of the cutting job. This type of consumables changeout might occur even though the electrode, nozzle, and shield cap still are usable.
Some other operators swear they can track consumables life by sound. They believe until the frequency changes dramatically that all is well. Unfortunately, the human ear is not a precise measurement tool. By the time an experienced operator believes he has heard something that suggests a consumables changeout is necessary, the plasma torch might have poorly cut several parts, running the risk that they might need to be scrapped.
Modern CAM software has made it so that operators of all experience levels can make the right consumable changes at the right time when it comes to plasma cutting. The software tracks the starts/stops and cutting distance, uses that data to determine the wear of the torch, and notifies the operator when the torch’s consumables have exceeded their limits. As a result, the responsibility doesn’t have to rest solely on the shoulders of machine operators.
Choose the Right Sequence
A plasma cutting machine operator working on a modern table has the luxury of knowing plenty of details about the work that awaits. He can start the day by seeing the job list, looking over the nests, and making adjustments as needed.
Many operators do not have the luxury of focusing on one machine for an entire shift. They have responsibilities elsewhere. That’s why it’s important that the operator can adjust the sequencing of the job.
The sequencing function on the most advanced plate cutting machines provides the operator with the ability to see what nests use the same consumables, which allows him to bunch them in a job that can be left to run unattended for a set amount of time. This control function also gives him the information about the consumable life. Will any consumable changes be necessary during the stretch of unattended operation? If certain consumables need to be replaced in the midst of the unattended run, how does the operator adjust the sequence to get as much unattended operation as possible without sacrificing plasma cutting performance?
A modern control gives the operator all the information he needs to know to keep production quality and throughput up, while also getting the most out of the plasma cutting consumables.
The electrode, nozzle, and shield are the consumables that are changed the most, and they are usually changed at the same time because they wear at the same rate. Hypertherm
Know What’s Being Cut
It’s no secret to people who have operated plasma cutting tables that working with different material thicknesses requires different torches. Thick sheet metals require high amperages and different consumables than are necessary to cut thin sheet. In plasma cutting, one size does not fit all.
In the days before modern controls, operators relied on cut charts provided by the plasma power source manufacturer to pick which consumables would be right for the job. Today, that information is incorporated into the machine programming software.
But the parameters used to guide the plasma cutting process go beyond simple sheet thickness and material type. Operators can select the optimal cutting parameters for highest edge quality or some variation that weighs overall cut quality against cutting speed.
The truth is that some shops don’t really care about the edge quality of the plasma-cut parts they receive. If that’s the case, the metal fabricating company is probably going to focus on streamlining the cutting process in an effort to meet or beat delivery deadlines. For those shops more interested in edge quality, the plasma cutting process can be adjusted to deliver these optimal results.
This is where the nesting and machine programming software point the machine operator in the right direction. By the time he calls up the job, the correct power source amperage and appropriate consumables have been designated for the job. This helps to ensure that the operator makes the right choice and prevents unwanted mistakes.
About That Arc Length …
The pre-cut process of the torch touching the top of the material surface ensures that the plasma cutting machine maintains the optimal distance between the material and bottom of the torch. But that’s not where the measuring ends.
After the initial pierce and the start of the cutting process, modern plasma cutting machinery measures the arc voltage. (By measuring the arc voltage, the length of the arc from the electrode to the plate can be determined.) It maintains this monitoring over the entire electrode lifespan, ensuring that the torch remains at the same cut height even as the electrode wears and the hafnium emitter inside becomes shorter, and when the distance between the torch and material changes because of height deviations in the sheet.
This height control is important as a plasma arc is not perfectly square. The arc is tapered at the ends, similarly to a candle flame. To achieve the best cut quality and consumable life, the squarest part of the arc—that is the middle—needs to make contact with the plate.
In the past, as the hafnium emitter within the electrode whittled away, the torch might move closer to the material to maintain the arc, even as it might become more unstable. The lack of the steady arc, as a result, could affecting piercing and lead-in cuts.
By maintaining a steady arc and the correct cutting height, the plasma torch is able to deliver a clean pierce, shorter lead-in, and no rippling during the subsequent cutting process since the squarest portion of the arc would maintain contact with the workpiece. The consumables are going to last longer as well.
Avoid System Stresses
Sensors in the power supply are going to help metal fabricators avoid the headache of short-lived consumables and even blowing up the torch.
Today’s technology can sense the onset of a catastrophic electrode blowout. (Imagine water creeping into the plasma cutting torch from a compressed air hose and the blowout that would occur as a result. That’s what could occur if an electrode is near the end of its life and it’s pushed beyond its limits.) As sensors notice dramatic changes in current and an erratic arc voltage, the control shuts down the system right away. This prevents torch failure and avoids lengthy downtime associated with cleaning up after a blowout.
Sensors also are used to prevent the considerable stress placed on consumables when the plasma cut is about to end in an uncontrolled manner, like when the plasma cutting process continues even after the torch exits the cut on the material’s edge. This stretches the arc, which wants to maintain connection to the metal, and places great strain on the torch consumables.
In this case, the sensors notice an abrupt increase in the arc voltage as the arc stretches to maintain contact with the metal. It correctly senses that the arc is about to terminate and initiates a controlled ramp down of the current. This type of controlled shutdown gives the hafnium within the electrode the time it needs to resolidify, which leads to a major increase in consumable life.
Be Vigilant
For those machine operators that were engaged in consumable changeout cycles before the days of modern controls, they probably watched one key performance metric closely. It might have been the number of pierces or feet of material cut. (These metrics are still used by the software to determine consumable wear!) No matter what it was, the operator knew what they needed to track to keep the plasma torch cutting as expected.
The emergence of modern controls formalized the tracking of consumable wear, taking some of the responsibility off the shoulders of operators, but the machine itself can’t remove consumables if they need to be changed. Operators still need to be engaged.
That’s why the combination of an engaged operator and advanced controls on plasma cutting systems are so powerful. For example, machine software can calculate where in a nest a consumable change is necessary; the machine then can inform the operator when he has to be at the machine to perform that changeout. When working in unison, the plasma cutting system and the operator can deliver maximum machine uptime and high-quality cutting results.
But life in a metal fabricating facility is constantly marked by change, and that means both humans and machinery have to be flexible. If a rush job interrupts the production schedule, that change is going to alter not only the subsequent timing of subsequent jobs, but also the lifespan of the consumables.
Machines are designed to provide reliable data. The operator needs to find out just how fresh the data is.Drill It
Obviously, not everyone has a multiprocess machine, where one machine can provide milling, cutting, drilling, and marking. But for those that do, they have a nice alternative when it comes to holemaking in thick materials. Instead of piercing through the material, which runs the risk of spraying up slag into the torch and possibly damaging the consumables, machine operators can elect to drill the initial part of the hole as a pre-piercing step or the entire hole.
Related Companies
subscribe now
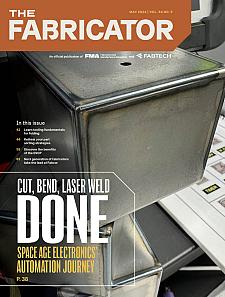
The Fabricator is North America's leading magazine for the metal forming and fabricating industry. The magazine delivers the news, technical articles, and case histories that enable fabricators to do their jobs more efficiently. The Fabricator has served the industry since 1970.
start your free subscription- Stay connected from anywhere
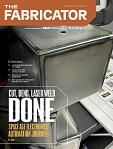
Easily access valuable industry resources now with full access to the digital edition of The Fabricator.
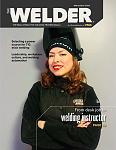
Easily access valuable industry resources now with full access to the digital edition of The Welder.
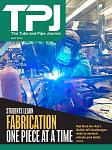
Easily access valuable industry resources now with full access to the digital edition of The Tube and Pipe Journal.
- Podcasting
- Podcast:
- The Fabricator Podcast
- Published:
- 04/16/2024
- Running Time:
- 63:29
In this episode of The Fabricator Podcast, Caleb Chamberlain, co-founder and CEO of OSH Cut, discusses his company’s...
- Trending Articles
Tips for creating sheet metal tubes with perforations
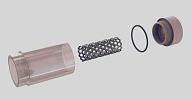
Are two heads better than one in fiber laser cutting?
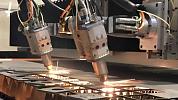
Supporting the metal fabricating industry through FMA
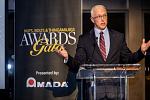
JM Steel triples capacity for solar energy projects at Pennsylvania facility
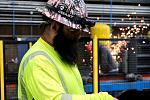
Omco Solar opens second Alabama manufacturing facility
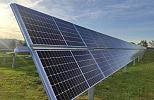
- Industry Events
16th Annual Safety Conference
- April 30 - May 1, 2024
- Elgin,
Pipe and Tube Conference
- May 21 - 22, 2024
- Omaha, NE
World-Class Roll Forming Workshop
- June 5 - 6, 2024
- Louisville, KY
Advanced Laser Application Workshop
- June 25 - 27, 2024
- Novi, MI