Editor-in-Chief
- FMA
- The Fabricator
- FABTECH
- Canadian Metalworking
Categories
- Additive Manufacturing
- Aluminum Welding
- Arc Welding
- Assembly and Joining
- Automation and Robotics
- Bending and Forming
- Consumables
- Cutting and Weld Prep
- Electric Vehicles
- En Español
- Finishing
- Hydroforming
- Laser Cutting
- Laser Welding
- Machining
- Manufacturing Software
- Materials Handling
- Metals/Materials
- Oxyfuel Cutting
- Plasma Cutting
- Power Tools
- Punching and Other Holemaking
- Roll Forming
- Safety
- Sawing
- Shearing
- Shop Management
- Testing and Measuring
- Tube and Pipe Fabrication
- Tube and Pipe Production
- Waterjet Cutting
Industry Directory
Webcasts
Podcasts
FAB 40
Advertise
Subscribe
Account Login
Search
Making a metal fabricator proud
The Brixius family wants to grow their namesake company to honor its founder
- By Dan Davis
- June 28, 2021
- Article
- Plasma Cutting
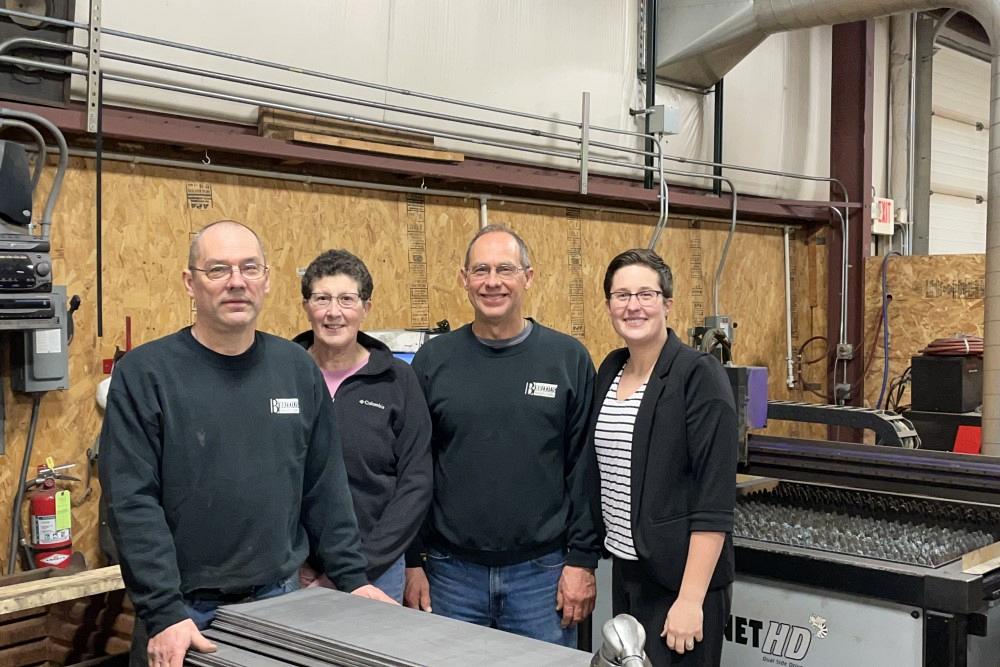
(From left) Tom, Peggy, Mike, and Abby Brixius of Brixius Manufacturing, Manitowoc, Wis., stand near one of the company’s recent capital equipment investments, a Hornet Cutting Systems plasma table. Images: Brixius Manufacturing
You could argue that metal fabricating is in the blood of the Brixius family of Manitowoc, Wis., but is metal fabricating in the family’s future?
Spoiler alert: It is. But the details are still being worked out. As Brixius Manufacturing celebrates 76 years in business—the pandemic kind of put a damper on any possible 75th anniversary celebration—the small family company is figuring out how the third generation might get involved. It’s not a transition that will occur without some hiccups, but that doesn’t mean it won’t occur. In fact, the transition of the family’s metal fabricating business from the first generation to the second suggests that sometimes patience is the best medicine for these situations. When the family name is not only on the business cards but also on the business itself, family members have a hard time walking away from the memories—and the possibilities.
From Subs to Battleships to Railings
Like many of his time, Harold Brixius didn’t think anything about taking trades-related classes while in high school. Everyone did it, and everyone was fine learning about wood- and metalworking. It was expected.
Brixius was first introduced to welding during this time and found that he liked it. That interest led to a degree in welding from the local technical school and later to a job with Manitowoc Shipbuilding Co., which started building submarines for the U.S. Navy in the 1940s. (According to the Wisconsin Maritime Museum in Manitowoc, the shipbuilding company built 28 submarines from 1940 to 1945, and 25 saw action during World War II, sinking 132 Japanese ships.)
Uncle Sam called soon thereafter, and Brixius joined the war effort. He put his welding skills to use during this time as a shipfitter and diver serving aboard the battleship USS Pennsylvania (BB-38).
When he returned, Brixius decided he wanted to work for himself and started Manitowoc Designers of Steel in 1945. The business was housed in a Quonset-style building, which today is still a part of the company’s structure.
The early days of the business were focused mostly on railings and awnings. Sales were good enough over the ensuing years to help raise a family of seven children.
In the 1970s the company got its first taste of some manufacturing work outside of railings and awnings. A local business reached out to see if Brixius could help with the fabricating of cabinets for Oral Roberts University in Tulsa, Okla. This led to a decade or so of more typical job shop work.
“My dad retired in the mid-1980s, and none of us were really into the business yet,” recalled Tom Brixius, Harold’s son. “But he still continued to dabble with things, working part-time. We would help in the evenings.”
Anybody who grew up in a family metal fabricating shop might identify with Tom’s childhood. There was a lot of sweeping. But he also twisted a lot of spokes for railings and assisted elsewhere when his dad needed an extra pair of hands.
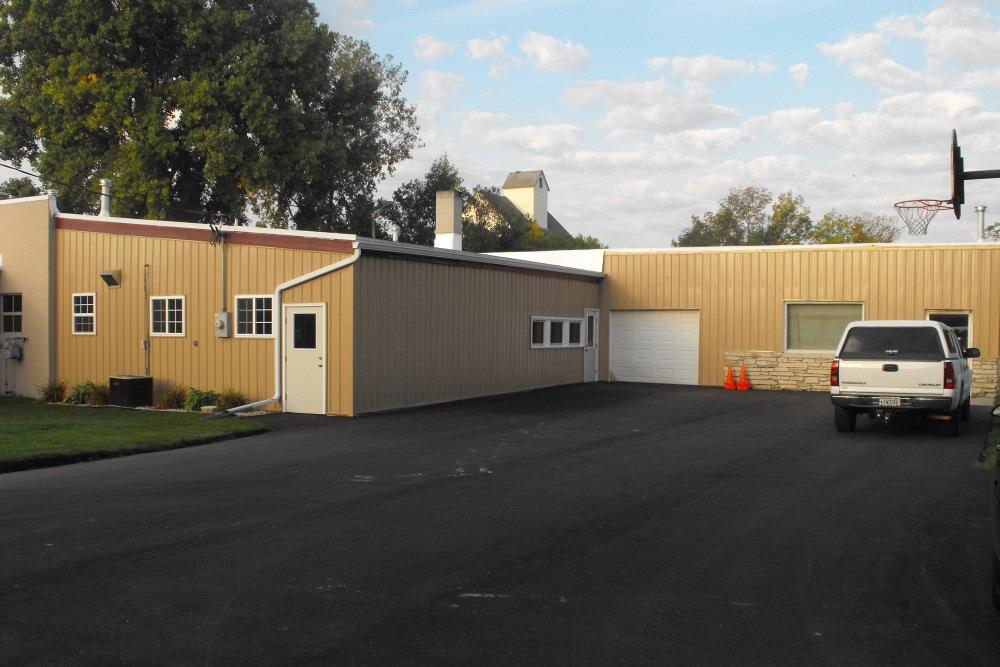
The Brixius Manufacturing facility was expanded from the original Quonset-style building in which the company began.
“We all worked out there, doing one thing or another, whether it was punching holes, drilling, bending stuff, or just cleaning up,” Tom said. “We’d always build the stuff during the week and install them on the weekends.”
Time to Take on the Family Business
That exposure to the family fabricating business influenced Tom enough that in the early 1980s he attended Lakeshore Technical College to study mechanical design. He earned his associate degree in 1983.
But he didn’t go to work for the family business right away. He sought experience with another company to see how things were done elsewhere.
Tom said that after about 10 years he had had enough. He wanted to go out on his own. Luckily, he knew a guy.
In 1995 he formally joined the company that was now named Brixius Manufacturing. He progressed to vice president and eventually to the president’s role with the death of Harold in 2006.
When Tom joined the family company, it primarily fabricated railings and awnings. It’s what the company was mostly known for, and there were really no other shops in the area that could offer the services Brixius could.
Today railings account for about 10% of the company’s overall sales revenues, and the awnings 25%. Most of its railing installations are in the Manitowoc area. The awnings, however, have a nationwide market. Tom said that the business has 60 dealers that sell the awnings, mostly focused on the Midwest and East Coast.
“It’s nice having the railings and awnings business because you have different venues for cash flow. You know that the railings and awnings business is always going to be busy in the summer and busy right before winter,” he said.
Tom pointed out that his dad started out with railings when he started the shop and then added awnings in the 1950s. The additional manufacturing jobs didn’t come until the 1970s. That type of gradual transition showed that growth could be managed without tremendous stress on the business.
If only that was the case today.
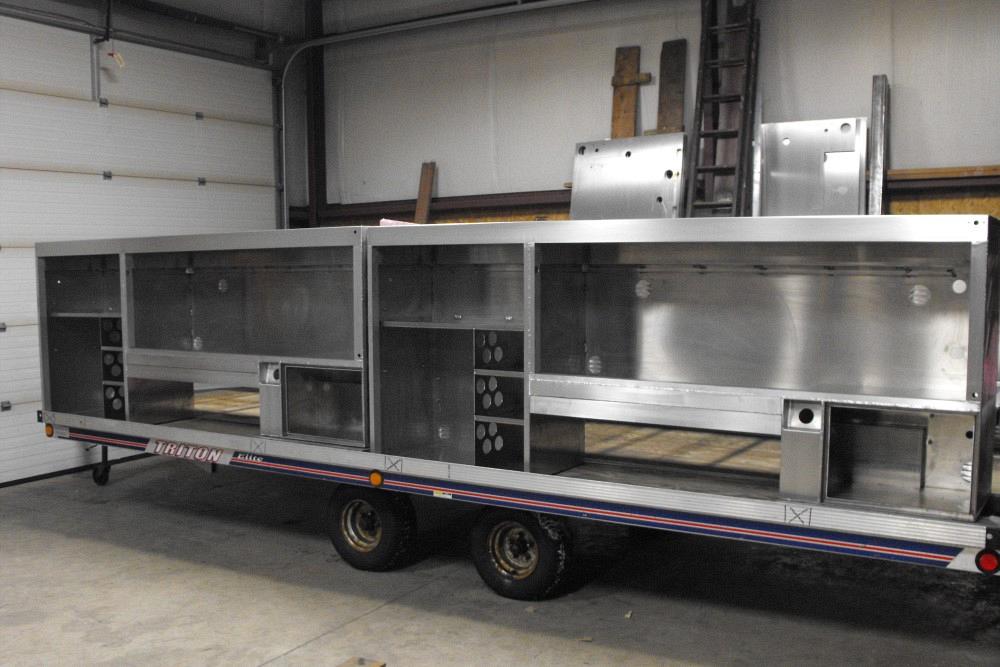
This stainless steel work is an example of some of the large projects that Brixius Manufacturing does for its industrial customers.
“We’re booming right now,” Tom said. “Even before last year, we had really big years. But this year, we’re up around 200% over those years.” He declined to share the company’s annual revenue.
Probably the biggest shift that has occurred during Tom’s tenure is the increase in the “job shop work,” as he called it. That’s anything from a big contract from the Wisconsin Department of Natural Resources to fabricate the frames and the sheet metal panel work for truck bodies to be used to respond to emergencies deep into wooded areas to cookware that is sprayed with heavy-duty, heat-resistant powder coatings. Agricultural jobs, such as building carts and wagons for small farms and greenhouses; stamping small parts; and punching holes into sheet metal panels represent some of the other work. All of these miscellaneous jobs account for about 65% of the company’s overall revenue.
Even with business booming, Tom said that the company is always looking for more long-run production jobs for the company’s turret punch and plasma cutting machine. Brixius Manufacturing has 12,000 sq. ft. of manufacturing space. About 1,800 sq. ft. is dedicated to fabrication of railings and 2,500 sq. ft. to awnings. The rest is set aside for the general industrial work.
While space may be limited, Brixius Manufacturing does have a full suite of capabilities to offer its customers. It can punch holes with its Murata/Wiedemann Centrum 2000, a Strippit 30/30 single-station punch, and a couple of OBI presses. It can cut with its horizontal and vertical band saws and a cold-cutting saw. It has a 10-ft., 120-ton press brake; a 0.25-in. by 10-ft. shear; a tube bender; and sheet and tube rollers. It can drill and machine parts if needed. (Its latest equipment purchase was a 30-in. Clausing lathe.)
The shop also upped its metal cutting game with the addition of a 4- by 4-ft. plasma cutting table from Hornet Cutting Systems. Tom had been looking for such a table about four years ago when someone let him know that they were looking to sell this table. Tom said he needed a smaller unit because the typical 5- by 10-ft. table wouldn’t fit into his shop; this smaller table was designed to be moved easily from tradeshows with a lift truck.
Tom said he liked what he saw, so he bought the system. It came with a 130-amp Hypertherm power source, and Brixius Manufacturing typically cuts steel 0.25 in. and thinner with it. Tom admitted that he has cut plate as thick as 0.75 in. and was pleased with the results. (“The angle on the edge of that was half a degree. It really cuts nice,” he said.)
Assisting Tom are his brother Mike and five other employees. Three are semiretired fabricators who still enjoy coming into a shop and taking on the day’s new challenges. The sixth is a new hire in his late 20s who is a trained welder and looking to learn the metal fabricating business.
Flexibility in a workforce helps any small shop, and Brixius Manufacturing is no different. The shop has three welders who know the gas metal arc and gas tungsten arc welding processes for use on aluminum, steel, and stainless steel. One of the welders works on railings when it’s that time of year. Mike works on awnings full-time when that season rolls around and is able to help out with the industrial jobs when the awning work slows. “A couple of us float around and work on everything,” Tom said.
“I think my dad would be pretty proud. We’ve taken the business pretty far since he died in 2006. And that’s what he wanted. He just wanted to see it grow,” Tom said.
Time for the Third Generation?
Just as Tom didn’t immediately work for his dad right out of school, Tom’s own children are doing the same. His daughter Abby is a dean of students at a nearby elementary school, Amber is a police officer, and Angie is a graphic designer. “Maybe they’ll be looking for a change of pace down the road,” he mused.
Abby said that she has had some discussions with her dad about joining the family business at some time. She also has fond memories of doing odd jobs around the shop, hanging out on the truck tailgate while a railing was being installed, and having her grandfather, Harold, pick her up from school and drive her to the shop. But she also wanted to strike out on her own, and she found a passion in educational leadership, later earning a master’s degree in administrative leadership.
“I told my dad that when we do something with the shop, I’d probably like to do something in the leadership realm. I’m probably never going to be a tradesman like he was, because I have no desire to do that,” Abby said. “But as we’re growing, we’re finding that we do need somebody to do the marketing, to help with sales, and do some of the HR work. That might be a better fit for me.”
Abby has been helping with some of those marketing tasks and played an important role in building the company website. She said she sees her dad spending time preparing all of the quotes and following up on sales, which makes her believe that she can help free up some of his time to go back to the technical work he enjoys and excels at.
She said her professional background has trained her to handle multiple projects simultaneously and deal with the most passionate of people, which is a common occurrence when it comes to tackling issues involving children. She thinks that strongly translates into the ability to satisfy customers and to ensure that employees are happy with their jobs.
“This shop has huge potential,” Abby said. “My grandpa started it, and he built this really strong core. My dad came in and brought more fabrication work in. And now I’m thinking about what I can add. What isn’t being tapped into? What can we do that other places can’t maybe? It’s a real neat opportunity.”
Tom, Abby, and perhaps other family members will join the conversation about how Brixius Manufacturing might look in the future. With the family name on the sign out front, everyone does feel some responsibility to do what they can to keep the business going. Tom agrees that keeping the family company going is much more preferable than trying to start from scratch. For that, he’ll always be grateful to his father.
Youthful energy can be a definite positive. Good shops find a way to embrace it and channel it in a positive direction. It sounds like Brixius Manufacturing has a good family project to tackle in the coming years.
About the Author
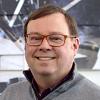
Dan Davis
2135 Point Blvd.
Elgin, IL 60123
815-227-8281
Dan Davis is editor-in-chief of The Fabricator, the industry's most widely circulated metal fabricating magazine, and its sister publications, The Tube & Pipe Journal and The Welder. He has been with the publications since April 2002.
Related Companies
subscribe now
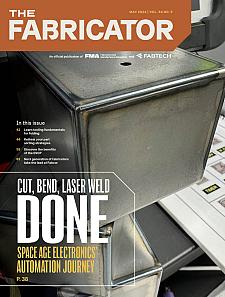
The Fabricator is North America's leading magazine for the metal forming and fabricating industry. The magazine delivers the news, technical articles, and case histories that enable fabricators to do their jobs more efficiently. The Fabricator has served the industry since 1970.
start your free subscription- Stay connected from anywhere
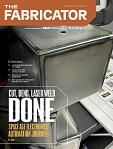
Easily access valuable industry resources now with full access to the digital edition of The Fabricator.
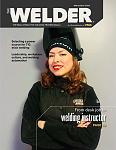
Easily access valuable industry resources now with full access to the digital edition of The Welder.
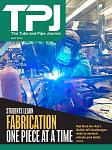
Easily access valuable industry resources now with full access to the digital edition of The Tube and Pipe Journal.
- Podcasting
- Podcast:
- The Fabricator Podcast
- Published:
- 04/16/2024
- Running Time:
- 63:29
In this episode of The Fabricator Podcast, Caleb Chamberlain, co-founder and CEO of OSH Cut, discusses his company’s...
- Trending Articles
Tips for creating sheet metal tubes with perforations
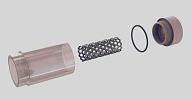
Are two heads better than one in fiber laser cutting?
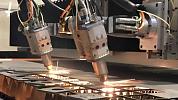
Supporting the metal fabricating industry through FMA
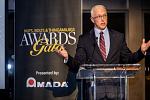
JM Steel triples capacity for solar energy projects at Pennsylvania facility
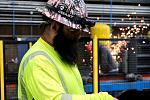
Omco Solar opens second Alabama manufacturing facility
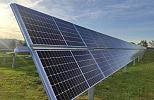
- Industry Events
16th Annual Safety Conference
- April 30 - May 1, 2024
- Elgin,
Pipe and Tube Conference
- May 21 - 22, 2024
- Omaha, NE
World-Class Roll Forming Workshop
- June 5 - 6, 2024
- Louisville, KY
Advanced Laser Application Workshop
- June 25 - 27, 2024
- Novi, MI