Vice President of Sales
- FMA
- The Fabricator
- FABTECH
- Canadian Metalworking
Categories
- Additive Manufacturing
- Aluminum Welding
- Arc Welding
- Assembly and Joining
- Automation and Robotics
- Bending and Forming
- Consumables
- Cutting and Weld Prep
- Electric Vehicles
- En Español
- Finishing
- Hydroforming
- Laser Cutting
- Laser Welding
- Machining
- Manufacturing Software
- Materials Handling
- Metals/Materials
- Oxyfuel Cutting
- Plasma Cutting
- Power Tools
- Punching and Other Holemaking
- Roll Forming
- Safety
- Sawing
- Shearing
- Shop Management
- Testing and Measuring
- Tube and Pipe Fabrication
- Tube and Pipe Production
- Waterjet Cutting
Industry Directory
Webcasts
Podcasts
FAB 40
Advertise
Subscribe
Account Login
Search
The rise of the multifunctional plate processing table
The metal manufacturing industry is changing, and plate processors are changing with it
- By Ben Morrall
- January 29, 2022
- Article
- Plasma Cutting
Parts with threaded holes, holes with diameters that are two times smaller than the diameter of the material thickness, and beveled edges can be made on the same piece of equipment. Shops that specialize in heavy fabrications, structural steel fabricators, and service centers are finding these multiprocess tables attractive as they look to add fabricating capacity.
An interesting trend is occurring in metal manufacturing in the U.S. today. Shops specializing in heavy-duty fabrications, structural steel fabricators, and service centers are looking for extra capacity, but they aren’t approaching capital investment in the same way. Instead of just adding a plasma cutting table or a milling center, they are interested in adding a multifunctional metal processing table.
After a quick glance, a fabricator might think these tables are nothing more than plasma cutting tables. They have a large cutting bed, some extending almost 100 ft. to accommodate cutting on one end and removal of parts from skeletons on the other, and a gantry with the plasma cutting torch attached. But a closer look reveals other heads dedicated to drilling and milling. These are combination machines that are new to many metal processors.
New motivations, however, have changed the thought process as it relates to this type of multiprocess machine. Owners and business managers recognize that they are only getting paid to add value to the metal parts that they are producing. They don’t get paid to move metal around on their shop floors. As a result, anything that can be done to minimize material handling is a good thing. Being able not only to cut, but also bevel, drill, and mill on the same table avoids secondary processing. That eliminates nonvalue-added material handling activities.
Of course, moving heavy plate is always a safety concern for employees. Anything that can be done to avoid additional handling of the plate and the resulting parts helps to reduce the risk of injury for shop floor workers.
Additionally, shops looking for extra capacity don’t necessarily have the shop floor space to add multiple machines. They need something that will accentuate the company’s current fabricating services and be flexible enough to process complex parts, which helps to minimize work-in-process and keep parts flowing to the shipping area.
A Change in Thinking About Plate Processing
As mentioned, a multiprocess machine looks like a plasma cutting machine. In most instances, it’ll have high-definition cutting capabilities and be able to handle material up to 2 in. thick. (Oxyfuel cutting torches are another option on these tables if the company is going to be cutting materials thicker than 2 in. regularly.) But because these multifunctional machines have other capabilities, they need to be approached differently.
For instance, if a shop needs 3-in. plate to be cut for a rush job and the table with the oxyfuel capability is busy with another job, a multiprocess table with plasma cutting capabilities can still do it. The drill can make three pierce holes deep enough that allow the plasma torch to complete the job.
Multifunctional machines require a change in the way parts are processed on the shop floor. For many companies with large plasma tables, an operator typically creates the nest at the machine. One nest for one process is not too complicated. Additional processes, however, complicate the approach to a nest.
That’s why it’s best to move programming of these multiprocess tables to the front office. Offline programming using modern software takes the guesswork out of nesting; produces better material utilization rates; and offers tracking of remnants, which is important given the high price of steel.
This also creates the situation where an operator might be able to run multiple machines on the shop floor. Without the duties associated with programming, a machine operator can set up the material, check to see that the job has started appropriately, and then tend to other responsibilities. The programmed job has a designated completion time, and the machine operator can check back in when the job is complete.
Having drilling and plasma cutting capabilities on the same machine gives a metals processor a lot of flexibility for holemaking. Generally speaking, plasma cutting small holes increases processing time, while drilling small-diameter holes can decrease the time it takes to produce parts. But for thick materials, thermal cutting is typically the process of choice for creating large hole diameters.
Advanced software controls now allow these multiprocess tables to run unattended even when processing different thicknesses. For instance, if 0.25-, 0.50-, and 2-in. blanks are all set up on the same bed, the machine can be programmed to drill holes in each of those material pieces.
Particularly in today’s tight labor climate, metal processors are always interested in adding production capacity without adding labor costs. They just need to be cognizant that adding a piece of equipment with multiple capabilities might also require rethinking the way that parts are produced and how machines are programmed to make the most of the capital equipment investment.
Additional Training Required
Odds are that a machine operator that has been running a plasma cutting table doesn’t know a whole lot about milling. That’s probably the one area that any operator new to a multifunctional machine might need to get up to speed on.
Now, this type of equipment will never be a replacement for a milling center. Milling centers can tackle a part from four sides, but that’s not possible with a part sitting on a table. Also, parts that require intricate features, such as internally milled features inside a hole or a cutout, are a better fit for mills than a multifunctional table.
This type of equipment is great for other milled features, however. A precise hole that has to have a depressed bearing fit snugly inside it is one example. Counter boring and blind holes are additional examples.
The operator needs to get used to these new applications that the machine’s milling capabilities make possible. The individual also needs to learn about different tooling available for these milling activities and the relationship between them and feed rates for different types of materials.
Drilling doesn’t require as much training. Multifunctional machines likely come with a set of drilling tools, and software controls help to determine how the drills run once parameters are plugged in. Milling, on the other hand, is a discipline that requires engaged shop personnel.
Multiprocess Impact
Beveling capabilities on plasma cutting machines have been explored in the pages of The FABRICATOR for years. Having said that, fabricators should know that software control advances have progressed far enough that engaging the beveling functions on these machines is much more user-friendly than equipment from 10 years ago. It’s not as simple as a straight plasma cut, but machine operators don’t have to do much to set up these machines to bevel plate.
In fact, a lot has changed over a decade. Multiprocess tables were available back then as well, but some metal processors might have been turned off by the excessive costs. Today the machines cost less than half of what they did then, and the user-friendliness of the machines has improved greatly.
Adding extra capacity, eliminating nonvalue material handling, maximizing the labor required to stay on top of the new capacity—all are factors that make these multifunctional devices the machines of the moment for metal processors.
About the Author
Related Companies
subscribe now
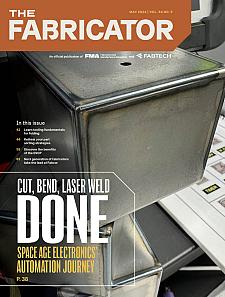
The Fabricator is North America's leading magazine for the metal forming and fabricating industry. The magazine delivers the news, technical articles, and case histories that enable fabricators to do their jobs more efficiently. The Fabricator has served the industry since 1970.
start your free subscription- Stay connected from anywhere
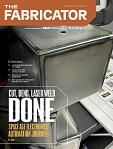
Easily access valuable industry resources now with full access to the digital edition of The Fabricator.
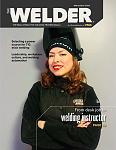
Easily access valuable industry resources now with full access to the digital edition of The Welder.
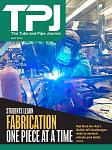
Easily access valuable industry resources now with full access to the digital edition of The Tube and Pipe Journal.
- Podcasting
- Podcast:
- The Fabricator Podcast
- Published:
- 04/16/2024
- Running Time:
- 63:29
In this episode of The Fabricator Podcast, Caleb Chamberlain, co-founder and CEO of OSH Cut, discusses his company’s...
- Trending Articles
Tips for creating sheet metal tubes with perforations
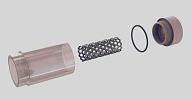
JM Steel triples capacity for solar energy projects at Pennsylvania facility
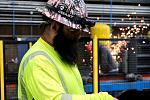
Are two heads better than one in fiber laser cutting?
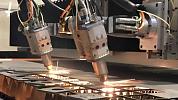
Supporting the metal fabricating industry through FMA
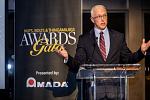
Omco Solar opens second Alabama manufacturing facility
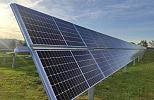
- Industry Events
16th Annual Safety Conference
- April 30 - May 1, 2024
- Elgin,
Pipe and Tube Conference
- May 21 - 22, 2024
- Omaha, NE
World-Class Roll Forming Workshop
- June 5 - 6, 2024
- Louisville, KY
Advanced Laser Application Workshop
- June 25 - 27, 2024
- Novi, MI