Director of Sales
- FMA
- The Fabricator
- FABTECH
- Canadian Metalworking
Categories
- Additive Manufacturing
- Aluminum Welding
- Arc Welding
- Assembly and Joining
- Automation and Robotics
- Bending and Forming
- Consumables
- Cutting and Weld Prep
- Electric Vehicles
- En Español
- Finishing
- Hydroforming
- Laser Cutting
- Laser Welding
- Machining
- Manufacturing Software
- Materials Handling
- Metals/Materials
- Oxyfuel Cutting
- Plasma Cutting
- Power Tools
- Punching and Other Holemaking
- Roll Forming
- Safety
- Sawing
- Shearing
- Shop Management
- Testing and Measuring
- Tube and Pipe Fabrication
- Tube and Pipe Production
- Waterjet Cutting
Industry Directory
Webcasts
Podcasts
FAB 40
Advertise
Subscribe
Account Login
Search
Magnetic tooling helps grip challenging parts in automated processes
Magnetic force vacuum cup holds on tight when other tooling cannot
- By Collins McGeorge
- October 9, 2019
- Article
- Punching and Other Holemaking
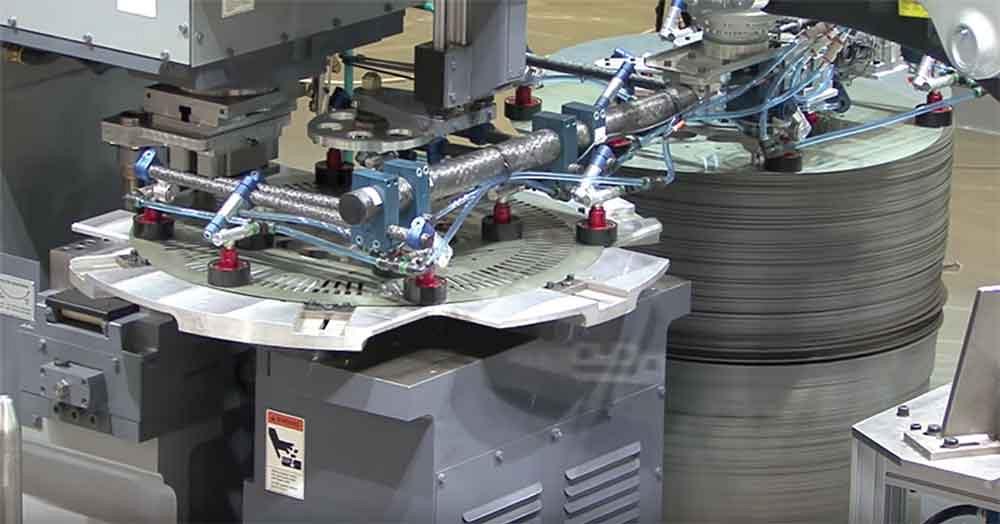
Magnetic tooling can come to the rescue in transporting parts with slots, holes, cutouts, and irregular surfaces.
The efficient transfer of steel parts or blanks in automated station-to-station, press-to-press, or robotic pick-and-place applications can be hindered by various features of the part.
Part Features, Conditions
Certain characteristics of a part, such as perforations or uneven surfaces, can present a challenge when securing it for transfer.
A part may have holes, slots, or cutouts that would prevent a vacuum cup from creating the necessary suction to hold it. Ridges, ribs, and bends on the part can also decrease the surface area needed to create a strong suction.
In addition, oils and lubricants on the steel’s surface can have an adverse effect, making it challenging for transfer tooling to separate, grasp, or retain the steel blank or part in the correct position.
Magnetic Transporters
Magnetic transporters are strong, permanent magnets that can resolve most of the problems that irregular, perforated, and uneven surfaces may cause in material handling. Magnetic end-of-arm tooling will attract and hold a blank or part securely even if it is not perfectly solid or flat, and if the part offers only a small contact surface area. They are designed to directly replace vacuum cups on an arm or boom with only minor tooling adjustments.
The transporters are encased in a low-profile housing that can be turned on or off with a quick blast of shop air.
Reduce Tooling Changes. Magnetic transporters often are used in applications in which a stamping manufacturer is trying to reduce the number of tooling changes required when running multiple parts on the same line.
For example, if a stamper runs one part on a station-to-station press line early in the day but wants to run a different part later in the day, alternative tooling configurations (or multiple tooling arms) usually are required to handle the different dimensions and pickup points on the two parts.
Typically, the entire tooling boom will have to be changed out at each station and a new boom installed to handle the new part. This not only increases downtime on the line, but necessitates investing in multiple booms, tooling, storage requirements, and so forth. Magnetic tooling eliminates the need for the stamper to invest in these additional items because the same tooling boom can work for both parts. If the transporter has a set pickup point, it doesn’t matter if the first part’s location is solid and the second part’s location has slots or holes. The magnet will still grasp and hold the steel securely, thereby offering a wider range of pickup points for the parts being transferred.
A magnetic transporter can reduce tooling requirements in robotic pick-and-place applications when a robot needs to perform multiple operations at a single station. Let’s say the robot’s end-of-arm tooling grabs a circular steel blank to place it in a notching press. Then, once the surface of the part has been notched all the way around, the same tooling needs to grab the completed inner and outer perforated rings from the press, move them, and drop them separately at their designated stacking stations.
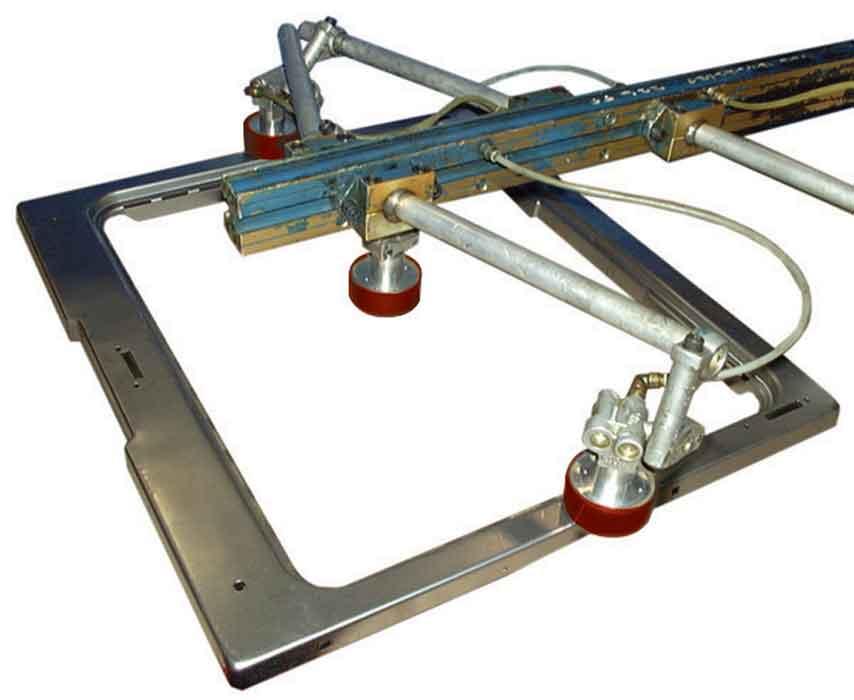
Magnetic tooling also can aid in applications where the pickup point options become narrower as a part moves through a press line, such as after it has been bent.
The same magnetic tooling can handle both the blank and the finished part, regardless of the part’s surface integrity. As a result, this can reduce tooling costs and increase cell efficiency.
Consume Less Shop Air. Besides allowing more flexibility in pickup points and cutting down on tooling requirements, transporters also offer a savings in shop air consumption. Because they require only a short blast of air to switch the magnet between the on (grip) and off (release) position, air requirements are minimal compared with other tooling technology.
In addition, fast cycle times are possible because the magnet is on and ready to hold the part prior to its arrival at the part pickup point.
Work During Power Loss. Magnetic transporters also work in the event of a power or air pressure loss. Since the magnet positively holds the part, it won’t inadvertently drop it if power or air is temporarily lost.
Nonferrous Metals Need Not Apply
Of course, magnetic technology is limited to ferrous metal blanks and parts, so it won’t work on nonferrous material. But for processes involving steel, magnetic transporters can save the day in situations that would be difficult or impossible for other types of transfer tooling.
Case Example: Steel Bathtubs
Magnetic tooling also can aid in applications where the pickup point options become narrower as a part moves through a press line.
A stamping manufacturer of bathtubs was having difficulty moving steel blanks on an automated press-to-press line. When the blank was at the first press station, there was plenty of surface area for the vacuum cup to grasp and handle the sheet. But as it progressed through each press and the blank was drawn increasingly deeper, it became more and more difficult for the vacuum cup to find a surface area large and flat enough to pick up and move the part.
The manufacturer installed magnetic transporters onto its existing tooling. The magnets were able to attract and hold on to the narrow flange of the tub while still handling the weight of the part. In fact, it didn’t matter that the surface area of the magnet overhung the flange because that did not compromise the magnet’s holding power or ability to grip. It still provided additional flexibility to the tooling setup.
Collins McGeorge is director of sales for Industrial Magnetics Inc., 1385 S. M-75, Boyne City, MI 49712, 800-662-4638, cmc
george@magnetics.com, www.magnetics.com.
About the Author
Collins McGeorge
800-662-4638
Related Companies
subscribe now
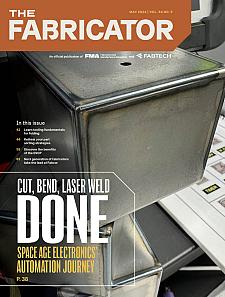
The Fabricator is North America's leading magazine for the metal forming and fabricating industry. The magazine delivers the news, technical articles, and case histories that enable fabricators to do their jobs more efficiently. The Fabricator has served the industry since 1970.
start your free subscription- Stay connected from anywhere
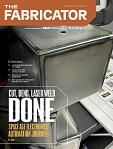
Easily access valuable industry resources now with full access to the digital edition of The Fabricator.
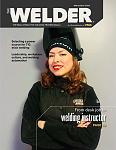
Easily access valuable industry resources now with full access to the digital edition of The Welder.
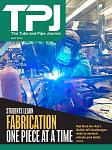
Easily access valuable industry resources now with full access to the digital edition of The Tube and Pipe Journal.
- Podcasting
- Podcast:
- The Fabricator Podcast
- Published:
- 04/16/2024
- Running Time:
- 63:29
In this episode of The Fabricator Podcast, Caleb Chamberlain, co-founder and CEO of OSH Cut, discusses his company’s...
- Trending Articles
Tips for creating sheet metal tubes with perforations
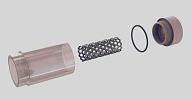
JM Steel triples capacity for solar energy projects at Pennsylvania facility
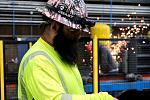
Are two heads better than one in fiber laser cutting?
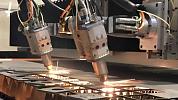
Supporting the metal fabricating industry through FMA
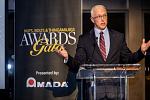
Omco Solar opens second Alabama manufacturing facility
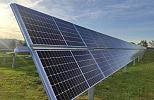
- Industry Events
16th Annual Safety Conference
- April 30 - May 1, 2024
- Elgin,
Pipe and Tube Conference
- May 21 - 22, 2024
- Omaha, NE
World-Class Roll Forming Workshop
- June 5 - 6, 2024
- Louisville, KY
Advanced Laser Application Workshop
- June 25 - 27, 2024
- Novi, MI