Global Products Manager, Donaldson Connected Solutions
- FMA
- The Fabricator
- FABTECH
- Canadian Metalworking
Categories
- Additive Manufacturing
- Aluminum Welding
- Arc Welding
- Assembly and Joining
- Automation and Robotics
- Bending and Forming
- Consumables
- Cutting and Weld Prep
- Electric Vehicles
- En Español
- Finishing
- Hydroforming
- Laser Cutting
- Laser Welding
- Machining
- Manufacturing Software
- Materials Handling
- Metals/Materials
- Oxyfuel Cutting
- Plasma Cutting
- Power Tools
- Punching and Other Holemaking
- Roll Forming
- Safety
- Sawing
- Shearing
- Shop Management
- Testing and Measuring
- Tube and Pipe Fabrication
- Tube and Pipe Production
- Waterjet Cutting
Industry Directory
Webcasts
Podcasts
FAB 40
Advertise
Subscribe
Account Login
Search
How the internet of things applies to industrial air filtration
Digital connectivity means always knowing how dust collection systems are operating
- By Brent Nelson
- May 3, 2021
- Article
- Safety
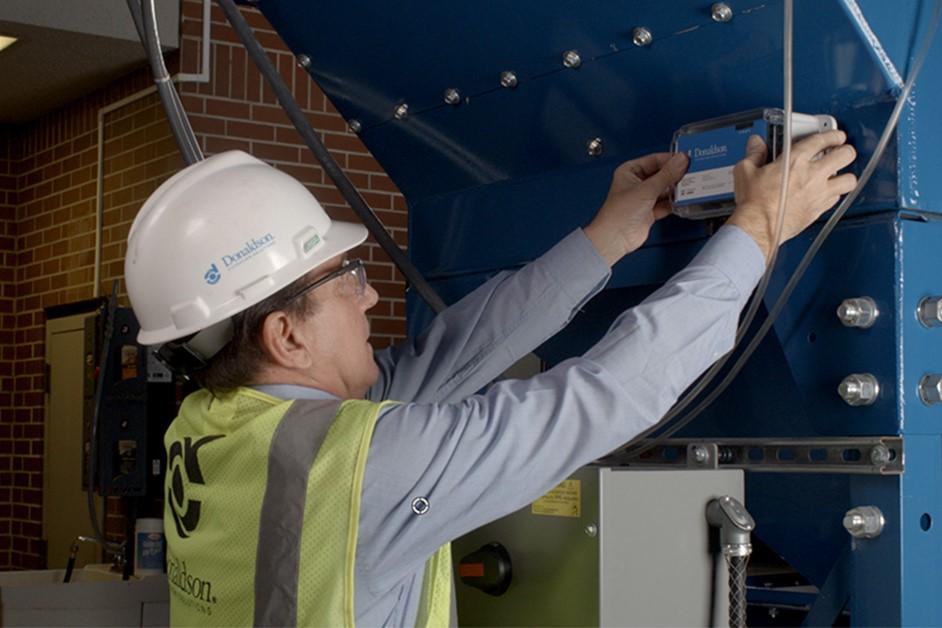
A technician connects a compact box on a facility dust collector to set up iCue, Donaldson’s remote filtration monitoring system. This device provides the means for the maintenance team to monitor the collector’s performance at all times.
The popular saying “If it ain’t broke, don’t fix it” seems to be the approach many companies are taking for their maintenance needs today. Of course, the majority do not wait until their equipment requires unplanned attention. Many are deploying preventive maintenance strategies, and an increasing number are going a step further by using remote equipment monitoring and performance data collection to better understand real-time system conditions.
This approach is more commonly referred to as condition-based maintenance (CBM), a strategy that uses indicators to flag decreasing equipment performance issues in real time for busy plant maintenance teams. With CBM, maintenance is performed only when the data shows that performance is decreasing, or if a critical maintenance action is needed, helping maintenance teams save time by eliminating some in-person review steps on the collector. In contrast, preventive maintenance kicks in only at predetermined, specified intervals, which means manufacturers might not discover problems at the moment they occur or may be acting before it is necessary.
CBM also can be more effective than preventive maintenance in avoiding unplanned repairs and downtime. The aging workforce, along with recent production slowdowns, distribution delays, and staffing shortages because of the pandemic, have accelerated the push for CBM, which has become a standard practice in recent years across many industrial environments to manage operational costs and prioritize staff time. Increasingly, however, manufacturers also are discovering additional benefits of connected monitoring services.
Remote Monitoring for Dust Collection
Dust collection plays an important supporting role in any manufacturing business, and for the metal fabrication industry in particular. And fabricators know all too well that monitoring a dust collection system usually means reading instrument panels, then recording the data manually and interpreting it. These are time-consuming tasks that might not provide all the information you need to make timely decisions. Data recorded manually only reflects a point in time, but connected monitoring is continuous, letting you see trends and spot deviations that are helpful for all stakeholder departments—operations; maintenance; and environmental, health, and safety (EHS).
A remote filtration monitoring service helps manage particulates in the air and stands apart from traditional filtration control systems because it relies on Internet of Things (IoT) technology to connect to a plant’s filtration system and monitor its performance. Thanks to IoT, this service gives manufacturers continuous visibility into their filtration operations, helping them better manage important processes that support primary manufacturing activities. The ultimate goal is to run without unplanned interruption, while simultaneously helping to manage compliance requirements.
Remote monitoring is an attractive option for facility teams looking to streamline their work flow and maintenance processes, optimize procedures to support EHS initiatives, and gain more valuable data and insights to help them stay ahead of potential challenges.
A 2020 survey of plant engineers and maintenance managers conducted by Donaldson confirms the need for reliable remote filtration monitoring services. More than half (56%) of respondents saw dust collection as critical to process, and 49% reported seeing a line shutdown based on a collector stoppage. Meanwhile, 60% of respondents reported facing at least one collector downtime event per year, while 14% said they faced at least one per month.
The good news is that remote filtration monitoring can become a natural part of a plant’s CBM process and overall crisis management plan. Here are three specific reasons manufacturers and job shops should consider adopting CBM and a connected filtration monitoring system across their operations:
1. Do more with less.Amid staffing disruptions related to quarantine periods, furloughs, and downsizing, many organizations have had to put a freeze on hiring additional maintenance managers and technicians during the last year. During these lean times, relying on remote monitoring systems to keep tabs on machines like dust collectors makes sense.
With CBM, you can significantly reduce the need for in-person inspections of your dust collectors, which frankly aren’t that good at preventing unplanned downtime anyway. CBM allows you to deploy your teams where and when they are needed and avoid unnecessary checks and physical walk-arounds to record data points.
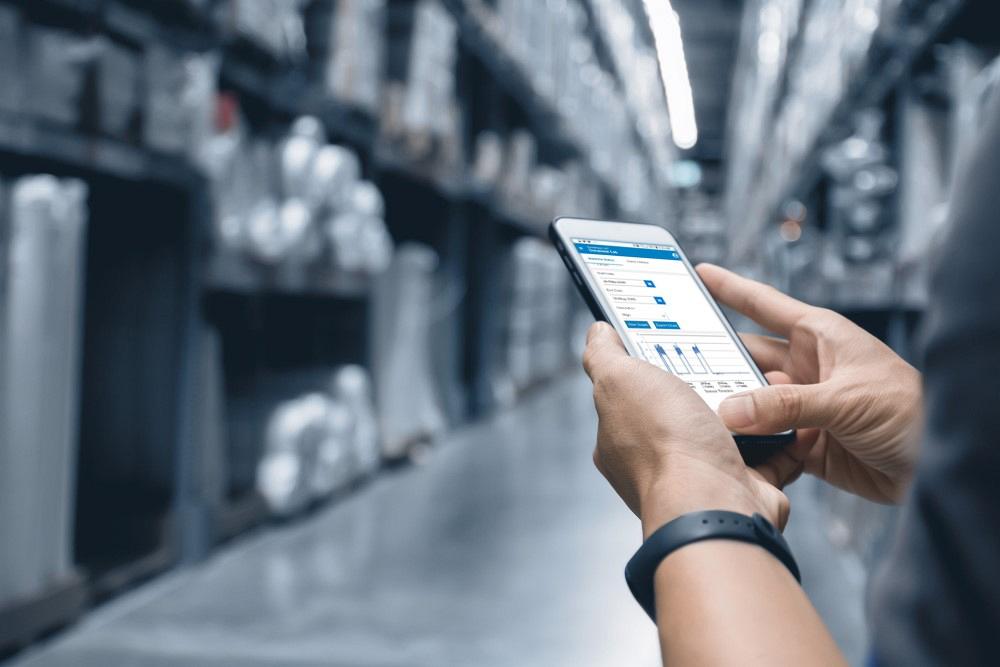
Remote monitoring of dust collection and filtration equipment can help those manufacturers and shops that are trying to streamline their maintenance processes.
For CBM, maintenance teams frequently use monitoring services that provide reliable and accurate data through a dashboard and receive timely notifications that flag maintenance tasks that may be coming or those that need immediate attention.
This approach to maintenance is not theoretical. For example, after a six-month trial period using a remote filtration monitoring service, a large industrial mineral plant in the southern U.S. anticipated it would slash its preventive maintenance time on its 23 dust collectors by roughly 900 hours per year. Now the plant’s workers have more time to devote to other important tasks.
This plant is not alone. Remote monitoring systems will continue to help fill staffing voids for maintenance managers who need to rebuild their teams after this unprecedented year, reprioritize workloads, and simply do more with less.
2. Keep production going. Remote system monitoring enables facility management teams both on- and off-site to proactively address time-sensitive equipment needs.
For example, using a remote monitoring filtration technology as part of your CBM approach can help maintenance staff proactively catch a rise in differential pressure (dP) in a dust collector, which likely means a filter is expired and needs to be changed. It can also read the particulate matter sensor in the exhaust of a collector and automatically send an alert when particulate levels are rising, so the team can prevent disruption and unplanned downtime.
Over time, recorded monitoring data is saved in a timeline that shows the historical performance through graphs and charts. These insights are shared in reports that help track scheduled and unexpected downtime and highlight trending issues that might require a longer, more time-intensive repair plan.
3. Manage, track, and stay compliant. Some states and local counties have regulations that require facilities to conduct in-person dust collector checks for two reasons: to manually record data like dP on a clipboard to meet air permit requirements, and to visually inspect the equipment for issues like particulate levels in the dust collector exhaust.
However, manual, in-person checks and visual monitoring are prone to human error, so it’s best to supplement them with a remote monitoring system that sends alerts when a function is out of your preset parameters. This enables a cross-check of manual findings with the system’s reporting analysis.
During times when the crew on the floor may be different every day, having a reliable, no-guesswork, connected monitoring system helps you make sure your standards are being met. The data collected, both in person and through the monitoring service, makes the completion of required compliance reports easier and more manageable for the maintenance and EHS teams.
Looking for the Right Monitoring-connected Filtration Service
Having remote monitoring of filtration equipment makes sense, but what should manufacturing companies look for when deploying such a maintenance plan? First and foremost, the remote monitoring system should be easy to deploy. One big advantage of IoT-based technology when compared to traditional control systems is that it is easy to set up and does not require specialized personnel. In addition, it works with all brands of dust collectors, new and existing, so manufacturers don’t need to replace their existing collector.
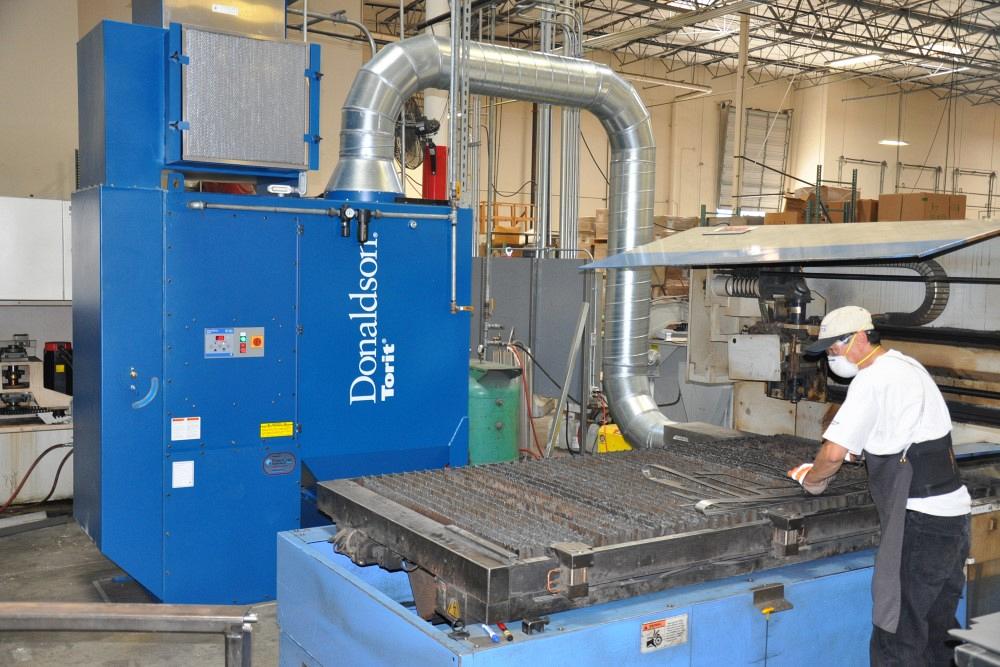
Dust collectors are important tools for keeping shop floor workers safe. The collectors, such as the one attached to this laser cutting machine, filter fine particulates out of the air, creating a safer work environment.
An IoT-based system also provides secure cloud communication, so your dust collector performance data is separate from your internal control systems and local Wi-Fi networks. This not only safeguards the security of the overall network, but it frees up IT to focus on other areas of the plant.
Second, make sure the system is designed specifically for dust collection. Some generic control systems are designed to manage production systems with extremely low latency. As a result, they are actually overdesigned and prove costly for monitoring a dust collector. Traditional control systems also can require the work of specialized engineers, often from outside the organization, to complete the integration process, which can be costly. You should look for a service that does not require any specialized resources—ideally one that connects to a web-based application in which the user only needs to log in to get the service running.
The challenges with a generic service don’t end there, though. In fact, some generic monitoring systems generate “nuisance alerts” that flag when a dust collector simply starts up or shuts down. You should look for an application that is intelligent enough to determine why a machine is shutting down or turning on, and generate alarms only when there is a performance issue that needs attention.
Third, make sure the monitoring-connected filtration service meets your technical requirements. It should offer:
- Various sensor options so you can track the performance metrics that are most critical to your operations.
- Real-time email alerts, so you can address issues before they escalate.
- Automated data capture and reporting, which simplifies compliance reporting.
- An online dashboard that’s easy to use and accessible to all necessary personnel.
- Analytics specific to dust collectors, like tracking pulse valve health.
Deploying a CBM strategy in combination with an IoT-based remote monitoring filtration service provides benefits too numerous for manufacturers to ignore. The service can help support EHS initiatives, maintain data for regulatory compliance, and streamline work flow. When choosing a remote monitoring filtration solution, focus on one that is easy to deploy, developed specifically for dust collectors, and meets all of your technical requirements.
By following these guidelines, you can avoid getting caught in situations where a critical dust collection system is suddenly “broke” and you have to “fix it.”
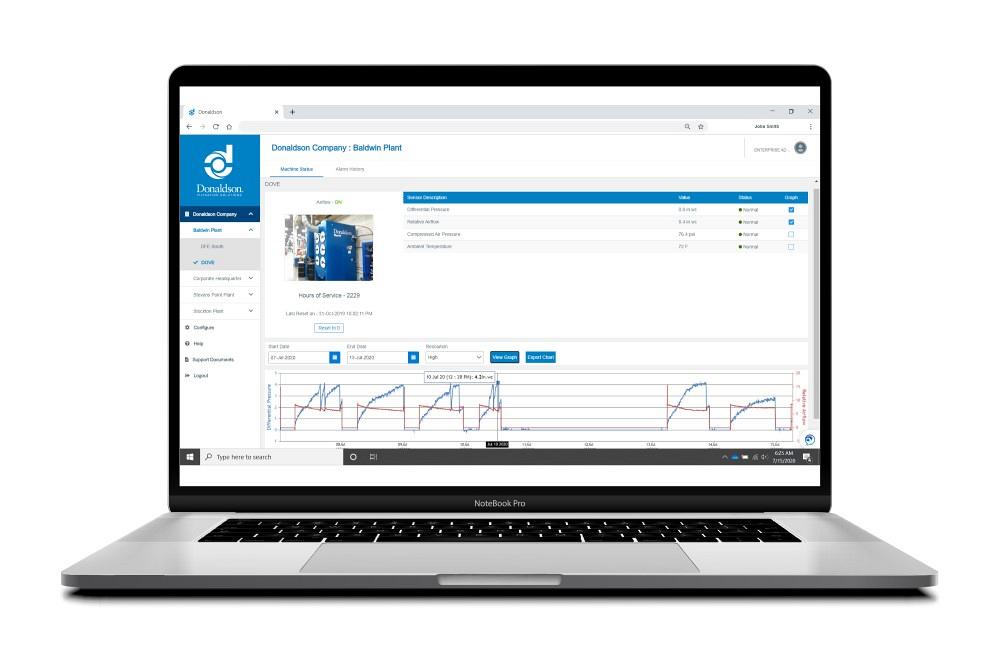
A filtration monitoring service records performance data from dust collectors and can display the information in easy-to-read forms in a dashboard view on a computer screen or mobile device. The insights allow a company to react quickly to any service needs that arise and keep their operations running efficiently.
About the Author
Brent Nelson
1400 W. 94th St.
Bloomington, MN 55431
833-310-0017
Related Companies
subscribe now
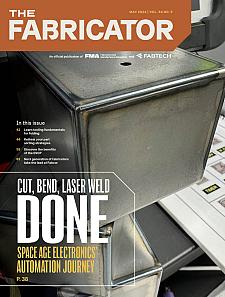
The Fabricator is North America's leading magazine for the metal forming and fabricating industry. The magazine delivers the news, technical articles, and case histories that enable fabricators to do their jobs more efficiently. The Fabricator has served the industry since 1970.
start your free subscription- Stay connected from anywhere
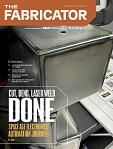
Easily access valuable industry resources now with full access to the digital edition of The Fabricator.
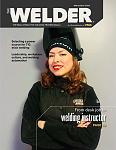
Easily access valuable industry resources now with full access to the digital edition of The Welder.
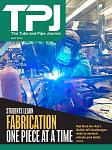
Easily access valuable industry resources now with full access to the digital edition of The Tube and Pipe Journal.
- Podcasting
- Podcast:
- The Fabricator Podcast
- Published:
- 04/16/2024
- Running Time:
- 63:29
In this episode of The Fabricator Podcast, Caleb Chamberlain, co-founder and CEO of OSH Cut, discusses his company’s...
- Trending Articles
Tips for creating sheet metal tubes with perforations
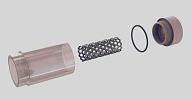
Are two heads better than one in fiber laser cutting?
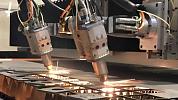
Supporting the metal fabricating industry through FMA
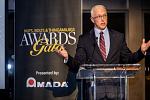
JM Steel triples capacity for solar energy projects at Pennsylvania facility
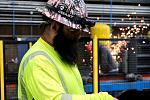
Omco Solar opens second Alabama manufacturing facility
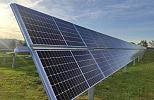
- Industry Events
16th Annual Safety Conference
- April 30 - May 1, 2024
- Elgin,
Pipe and Tube Conference
- May 21 - 22, 2024
- Omaha, NE
World-Class Roll Forming Workshop
- June 5 - 6, 2024
- Louisville, KY
Advanced Laser Application Workshop
- June 25 - 27, 2024
- Novi, MI