Editor-in-Chief
- FMA
- The Fabricator
- FABTECH
- Canadian Metalworking
Categories
- Additive Manufacturing
- Aluminum Welding
- Arc Welding
- Assembly and Joining
- Automation and Robotics
- Bending and Forming
- Consumables
- Cutting and Weld Prep
- Electric Vehicles
- En Español
- Finishing
- Hydroforming
- Laser Cutting
- Laser Welding
- Machining
- Manufacturing Software
- Materials Handling
- Metals/Materials
- Oxyfuel Cutting
- Plasma Cutting
- Power Tools
- Punching and Other Holemaking
- Roll Forming
- Safety
- Sawing
- Shearing
- Shop Management
- Testing and Measuring
- Tube and Pipe Fabrication
- Tube and Pipe Production
- Waterjet Cutting
Industry Directory
Webcasts
Podcasts
FAB 40
Advertise
Subscribe
Account Login
Search
Rethinking safety for novice press brake operators
Safety devices have to evolve with the new generation of manufacturing workers
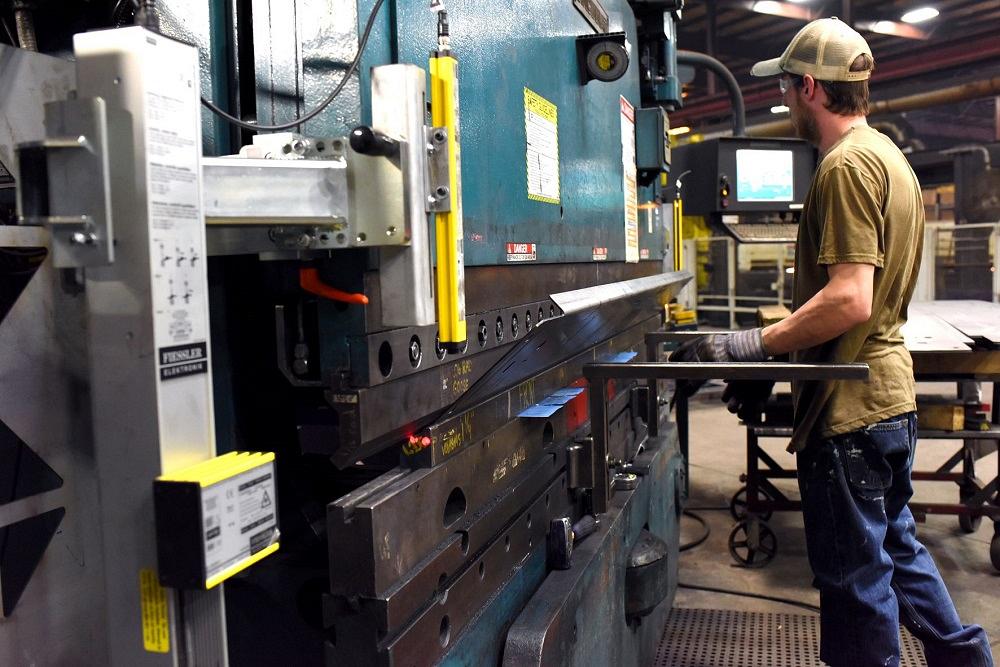
A light curtain protects the crush zone, the area of the ram above the tooling where an operator might get his fingers or hand caught if holding the workpiece wrong, and a laser ensures the point of contact between the punch and the workpiece is clear. Images: Press Brake Safety
A lot has been said about the inability of metal fabricators to find workers to take the place of the baby boomers who have left the shop floor in recent years. While much of that conversation has focused on welders, fab shops are desperate for press brake operators as well.
Industry and local educational systems have come together to reinvest in vocational skills development across the U.S. For instance, many communities are building larger and sophisticated welding training facilities that rival the most modern manufacturing settings. But when it comes to press brake operation, metal fabricating companies are pretty much having to shoulder the full responsibility of training. No one is building new wings of a school dedicated to the science of metal forming.
Larger fabricating companies might have a formal training program that allows an inexperienced person the time to learn the art of bending, exploring the basics of metal forming and how the tools and brakes are used to bring 3D models to life. At smaller shops, however, a press brake rookie might get to shadow a company veteran for a week or so before being placed in front of a machine to work without direct supervision.
The latter scenario isn’t necessarily a horrible one, but it does increase the chance of injury. No matter how far modern press brakes have come with advanced safety devices, these machines still can be dangerous.
Eliminating the Crush Zone
New press brakes sold to manufacturing companies today are supposed to include some sort of safety system per Occupational Safety and Health Administration regulations. In most instances, that means an active opto-electronic protection device (AOPD), most often referred to as a “laser” on which the safety mechanism is based, or a light curtain.
Light curtains, probably most often used in a fabrication facility for guarding an area, also can safeguard point-of-operation hazards in press brakes. With an LED transmitter and receiver set up on each side of the bending window, covering the area between the die opening and the bottom of the punch tooling, any interruption of the plane of light by an object larger than the minimum size allowed by the safety system causes the press brake to stop. A hand or a finger in the bending window can put a halt to bending activity.
Light curtains are very useful, but they can be cumbersome because they restrict access to the operator’s hands to inside the bending window. Operators sometimes need to handle small parts close to the press brake tooling, and light curtains make that hard to do.
That’s where laser devices have emerged as an attractive alternative to light curtains on the press brake. These devices allow for the operator’s hands to hold parts close to the tooling. The biggest advantage of AOPD is that operators can hand-hold parts close to the dies without worrying about the machine stopping when the ram is engaged.
While injuries still occur because fingers and hands get caught between the punch and die, for the most part, light curtains and laser devices have helped to reduce the risk of injury for press brake operators. But that’s not the only area that should be of concern to the manager of a metal fabricating company or supervisor of a bending department.
For years, Press Brake Safety President Jason Boyer had heard about operators injured when they held material during the bending process and then had their fingers or hands slammed against the ram as the flange sprung up as a result of the punch driving into the workpiece and the bottom die. In fact, a manufacturer of transportation equipment asked for help in addressing these types of injuries after three such incidents occurred in its own facility over a short period of time.
Boyer said the manufacturer knew that Press Brake Safety dealt with safety tools that mitigate risk related to press brake pinch points, but it was looking for something else.
“My dad [Douglas Boyer, CEO of Press Brake Safety] said we should try and put a light curtain in that area. So that’s what we did,” Boyer said.
The resulting patented technology development, the Reverse Flange Crush Zone protection device, comprises two light curtains positioned on each side of the ram. It prohibits the closing movement of the ram when an obstruction other than the material is detected within the crush zone, which Boyer defines as the area of the ram where an operator’s hand or fingers could be pinned by the workpiece. The safety system releases the ram when the obstruction has been removed or the operator intentionally requests the system to be overridden, which sometimes might be required for the handling of large and awkward parts.
The light curtains have what Boyer calls a “muted status floating area” of about 0.5 in., which provides coverage of the typical workpiece thickness that would be of concern in these types of applications. Anything more than 0.5 in., such as the presence of fingers on the flange heading toward the ram, causes the system to shut down the bending process.
The light curtains are connected to an external indicator lamp, also attached to the ram, which illuminates if an obstruction has been detected. This acts as a visual reminder for the brake operator to alter his support of the part, such as moving the hand to under the part or to the side instead of having a finger or thumb above the workpiece.
Another tap of the foot pedal engages the ram and overrides the stoppage. This causes the same light to flash.
The safety device can be adjusted to accommodate different workpiece sizes and tooling lengths. By adjusting a couple screws on the support for each light curtain, they can be slid up or down to provide coverage anywhere on the ram—and even the tooling when the resulting flange is not that big.
The injuries related to this sort of accident are much more serious than simple bruises, according to Boyer.
“Depending on the part, it could take a finger off,” he said.
The manufacturer of transportation equipment that originally asked for some sort of safety device to protect workers from injuries in the crush zone now has the devices on its nine press brakes, and the results have been positive, Boyer said. His company now has 42 installations of these devices in metal fabricating facilities in the U.S.
A safety foot pedal can offer an operator more control of the press brake ram, especially if the operator has experienced a hand injury at the brake.
Additional Safety Devices to Think About
Again, inexperienced operators bring additional worries for any supervisor or safety professional overseeing press brakes at a company. But sometimes even experienced people zone out, and press brakes can be unforgiving.
Boyer recounted the story of a press brake operator who engaged the foot pedal control but leaned into it as she did that and stumbled forward into the bending area. Because the foot pedal control had engaged the ram, her hand got caught in the tooling, resulting in an injury.
A traditional pedestal e-stop doesn’t do an operator much good in a situation like that because the operator’s hand is likely injured, or the pedestal is out of reach.
“ANSI B11.3 [international safety standard] says you should have a safety foot pedal all of the time for press brakes,” Boyer said.
With the new generation of safety foot pedals, Boyer described the device’s active positions:
- While at rest, the ram doesn’t move.
- When the operator presses the pedal down to its first resistant catch, the ram is activated and starts its closing action.
- When the operator presses the pedal down beyond the first resistant catch until it reaches the absolute bottom, the ram reverses movement and returns to its resting position.
Other items that Boyer said could help minimize injury risk on the press brake include light curtains surrounding the backgauge system and safety blocks. Again, light curtains can ensure that fingers are on the backside of the part as it is about to engage with the backgauge, preventing a painful pinch. Meanwhile, safety blocks, commonly used to support the ram during press brake maintenance, help to extend the useful life of the brake when it’s not in use, taking the pressure off of the cylinders during those off hours.
In the end, press brake safety devices are good tools to help prevent injuries, but they don’t act as a guarantee for an accident-free bending department. That’s a constant battle and one that is much harder with very green operators joining the manufacturing fold.
“Money well spent would be creating an in-house training program for new press brake operators,” Boyer said. “Training on the press bake that they will use daily would be valuable to the operator and the company.”
About the Author
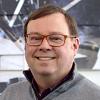
Dan Davis
2135 Point Blvd.
Elgin, IL 60123
815-227-8281
Dan Davis is editor-in-chief of The Fabricator, the industry's most widely circulated metal fabricating magazine, and its sister publications, The Tube & Pipe Journal and The Welder. He has been with the publications since April 2002.
Related Companies
subscribe now
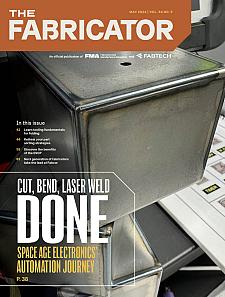
The Fabricator is North America's leading magazine for the metal forming and fabricating industry. The magazine delivers the news, technical articles, and case histories that enable fabricators to do their jobs more efficiently. The Fabricator has served the industry since 1970.
start your free subscription- Stay connected from anywhere
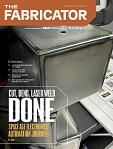
Easily access valuable industry resources now with full access to the digital edition of The Fabricator.
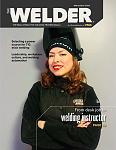
Easily access valuable industry resources now with full access to the digital edition of The Welder.
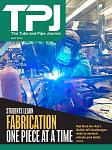
Easily access valuable industry resources now with full access to the digital edition of The Tube and Pipe Journal.
- Podcasting
- Podcast:
- The Fabricator Podcast
- Published:
- 04/16/2024
- Running Time:
- 63:29
In this episode of The Fabricator Podcast, Caleb Chamberlain, co-founder and CEO of OSH Cut, discusses his company’s...
- Trending Articles
Tips for creating sheet metal tubes with perforations
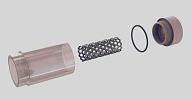
Are two heads better than one in fiber laser cutting?
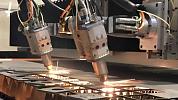
Supporting the metal fabricating industry through FMA
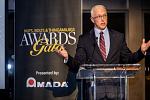
JM Steel triples capacity for solar energy projects at Pennsylvania facility
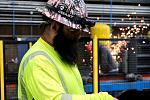
Omco Solar opens second Alabama manufacturing facility
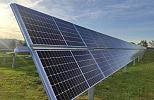
- Industry Events
16th Annual Safety Conference
- April 30 - May 1, 2024
- Elgin,
Pipe and Tube Conference
- May 21 - 22, 2024
- Omaha, NE
World-Class Roll Forming Workshop
- June 5 - 6, 2024
- Louisville, KY
Advanced Laser Application Workshop
- June 25 - 27, 2024
- Novi, MI