Editor-in-Chief
- FMA
- The Fabricator
- FABTECH
- Canadian Metalworking
Categories
- Additive Manufacturing
- Aluminum Welding
- Arc Welding
- Assembly and Joining
- Automation and Robotics
- Bending and Forming
- Consumables
- Cutting and Weld Prep
- Electric Vehicles
- En Español
- Finishing
- Hydroforming
- Laser Cutting
- Laser Welding
- Machining
- Manufacturing Software
- Materials Handling
- Metals/Materials
- Oxyfuel Cutting
- Plasma Cutting
- Power Tools
- Punching and Other Holemaking
- Roll Forming
- Safety
- Sawing
- Shearing
- Shop Management
- Testing and Measuring
- Tube and Pipe Fabrication
- Tube and Pipe Production
- Waterjet Cutting
Industry Directory
Webcasts
Podcasts
FAB 40
Advertise
Subscribe
Account Login
Search
Building the safety culture
FMA Safety Award winners remind other companies that a safety-first culture can’t be built overnight
- By Dan Davis
- April 27, 2017
- Article
- Shop Management
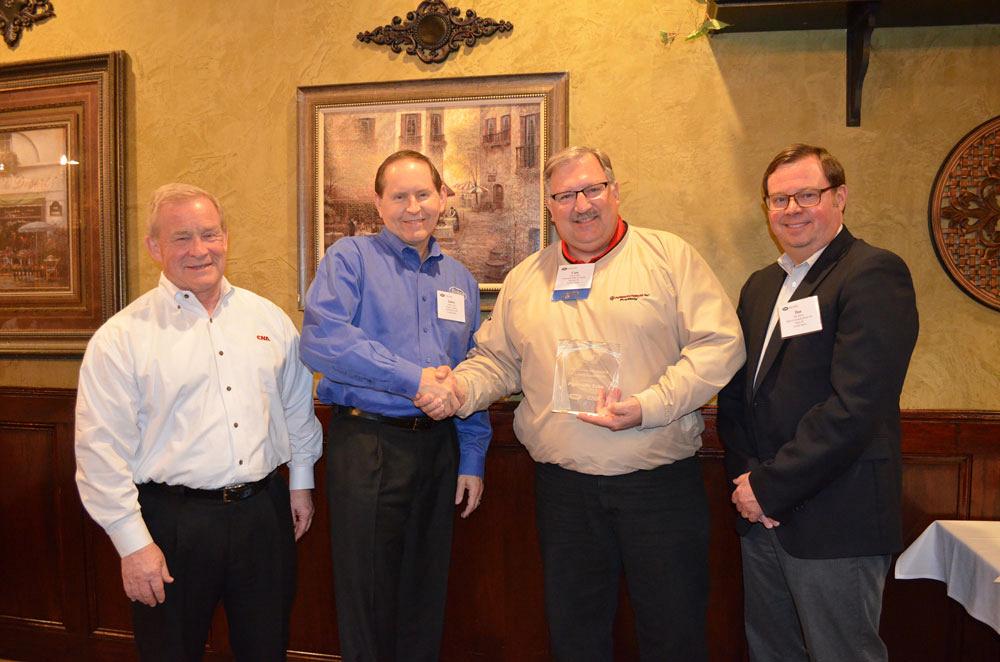
Figure 1
Cam Valle of Plymouth Tube holds the Rusty Demeules Award for Safety Excellence that was presented to him by Jim Vose of The Dupps Co., the 2015 winner of the award. Roger Wilson, a representative of CNA, the sponsor of the award, and FMA’s Dan Davis join in the award presentation.
Cam Valle, Plymouth Tube’s director of human resources, who also has oversight of safety efforts for the tube manufacturer’s nine locations, attended the Fabricators & Manufacturers Association’s (FMA) 2017 Safety Award program in Elgin, Ill., on April 19 for a good reason: Plymouth Tube’s Streator, Ill., facility was collecting its second consecutive Rusty Demeules Award for Safety Excellence (see Figure 1). That’s the kind of honor that follows a manufacturer with a firmly established safety culture.
The Streator mill produces cold-drawn seamless low-carbon and alloy steel tubing for primarily hydraulic and aerospace applications. It had achieved 1,145 consecutive days without a lost-time injury at the time it received the safety award, named after a metal fabricator who was a longtime volunteer leader with FMA and founder of the organization’s Safety Council.
Earlier in the day, Valle reminded conference attendees (see Figure 2) that such success didn’t happen overnight. It was slightly more than 10 years ago that the company was faced with $1.5 million in workers’ compensation claims. Safety rules were discussed even back then, but they weren’t taken seriously. That changed over the years, Valle explained during a panel session.
Valle, who prior to moving on to corporate activities for Plymouth Tube was the Streator facility plant manager, said managers made safety efforts visible and personal. Job safety analyses were done for almost every activity to determine potential hazards and find the safest way to do the job. Safety talks before shifts focused not only on safety on the job, but safety at home. Everyone was encouraged to participate in some way, and investments were made to demonstrate the company’s commitment to keeping everyone safe.
“The union employees came to us and said you always talked about safety, but now you believe in safety,” he said.
It Has to Start Somewhere
In a morning keynote address at the Safety Conference, Bob Tepe, president and CEO, Winergy Drive Systems Corp., and vice president, Mechanical Drives Business Unit, Siemens Industry, reminded conference attendees that all facilities, new and old, have to work to establish a culture where employees are engaged in keeping an eye out for each other. Winergy, an assembler and refurbisher of very large gearboxes for wind turbines and other applications, built its facility in Elgin, Ill., in 2009 and has seen its business grow with the expanding wind energy sector. As a result, new employees have been added at a steady pace over the years, which creates the need for increased vigilance with so many fresh faces walking around. Currently, about 180 employees work in the facility.Attendees got to see the challenge that Winergy faces on a daily basis during a tour on April 20. Workers move and manipulate gearbox assemblies that can weigh 40,000 to 90,000 lbs. Electric lift trucks, 60 cranes (see Figure 3), and more than 100 hooks are used for material handling. Extensive audits of the equipment and employee training keep injuries to an absolute minimum in the 170,000-sq.-ft. building, Tepe said.
So how is this done? Plant Manager Juan Carlos Rivera said it’s important to get everyone involved. It’s driven from the top of the organization, and the shop floor and front-office personnel all are involved in process improvement and reporting on positive and negative safety behavior.
A good example of this evolution was the introduction of a daily morning meeting covering environmental, health, and safety issues, Rivera said. Topics can range from discussing a potential hazard witnessed recently on the shop floor to a new Occupational Safety and Health Administration advisement regarding something like hot work. Rivera said that since these regular meetings have taken place, and with consistent employee training, the number of injuries has decreased. Last year the company had only one lost-time injury.
“That gives us something to work on,” Tepe said.
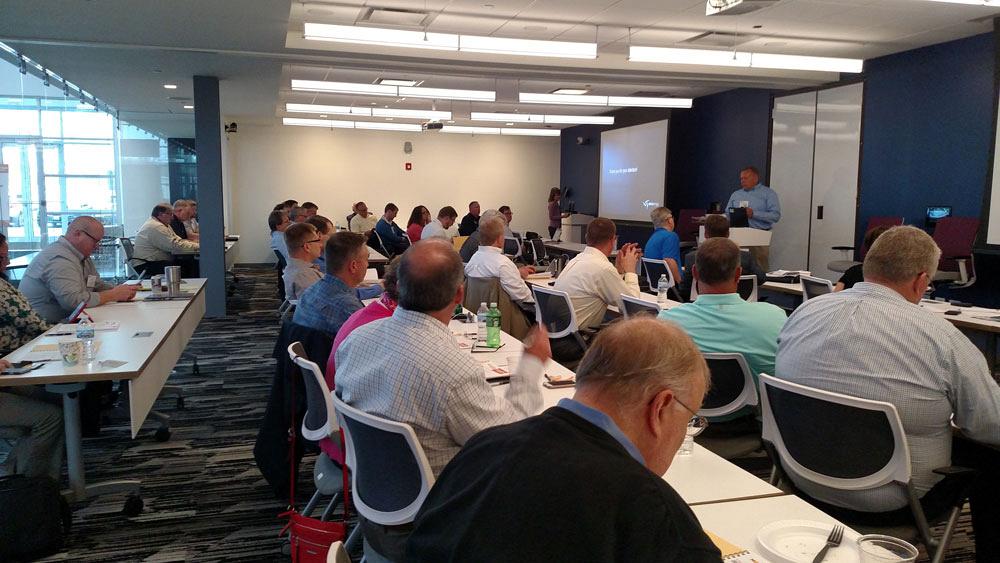
Figure 2
Darrel Shankles, safety manager, PlayCore, and member of the FMA Safety Council, reviews conference activities with attendees at the 2017 FMA Safety Conference, which was the first educational event to be held at FMA’s new Elgin, Ill., headquarters.
This is all part of the company’s Zero Harm Culture, Tepe added, that has helped to create this environment. Zero injuries is the goal, and no compromises, such as deadline and cost pressures, are allowed to interfere with that goal.
“I always tell our folks that I want them to go home in the same shape that they came into work,” Tepe said.
So what else can a fabricator do, in addition to training and involving everyone in safety observations, auditing, and resolution activity? Some of the safety professionals share some ideas during the conference:
- Steve Lehning, EHS manager, SPX Cooling Technologies, Overland Park, Kan., noted that while he was with Decatur, Ill.-based ADM Mechanical, a former winner of the Rusty Demeules Award, the company had an annual Family Safety Day at a nearby park. Employees had a chance to celebrate staying safe at work, but probably more important, according to Lehning, was that management had a chance to meet with workers’ families. This established personal relationships outside of the fabricating facility, and management used those connections to challenge employees to participate in safety improvement activities. What is a better motivator for a safe workplace than coming home safely to the family?
- Eric Larson, plant manager, Elgin Sweeper, Elgin, Ill., said supervisors pass out tokens, which can be used in the vending machines, to employees demonstrating good safety practices. For example, if a supervisor notices a welder wearing all of the required personal protective equipment, he or she can give a token to the welder. “It seems like in American society we don’t want to celebrate our successes,” Larson said. “We want to change that.”
- Jim Vose, human resources director, The Dupps Co., Germantown, Ohio, another former Rusty Demeules Award winner, offered a couple of suggestions tied to meals. He holds a monthly safety lunch with supervisors, who them turn around and share the luncheon topic discussion with the rest of the staff during weekly safety talks. Also, catered lunches are held to celebrate safety milestones, such as a full year without a lost-time injury. (The Dupps Co. had gone 8.5 years without a lost-time injury before one occurred early in 2016.)
Safety professionals or fabricators looking to boost their safety knowledge who might be interested in attending the 2018 FMA Safety Conference are encouraged to call 888-394-4362.
About the Author
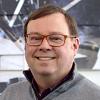
Dan Davis
2135 Point Blvd.
Elgin, IL 60123
815-227-8281
Dan Davis is editor-in-chief of The Fabricator, the industry's most widely circulated metal fabricating magazine, and its sister publications, The Tube & Pipe Journal and The Welder. He has been with the publications since April 2002.
subscribe now
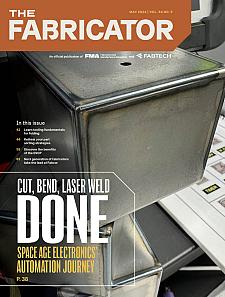
The Fabricator is North America's leading magazine for the metal forming and fabricating industry. The magazine delivers the news, technical articles, and case histories that enable fabricators to do their jobs more efficiently. The Fabricator has served the industry since 1970.
start your free subscription- Stay connected from anywhere
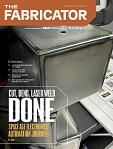
Easily access valuable industry resources now with full access to the digital edition of The Fabricator.
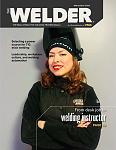
Easily access valuable industry resources now with full access to the digital edition of The Welder.
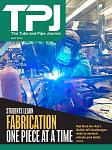
Easily access valuable industry resources now with full access to the digital edition of The Tube and Pipe Journal.
- Podcasting
- Podcast:
- The Fabricator Podcast
- Published:
- 04/16/2024
- Running Time:
- 63:29
In this episode of The Fabricator Podcast, Caleb Chamberlain, co-founder and CEO of OSH Cut, discusses his company’s...
- Trending Articles
Tips for creating sheet metal tubes with perforations
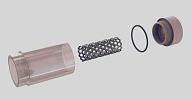
JM Steel triples capacity for solar energy projects at Pennsylvania facility
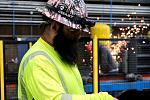
Are two heads better than one in fiber laser cutting?
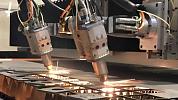
Supporting the metal fabricating industry through FMA
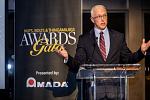
Omco Solar opens second Alabama manufacturing facility
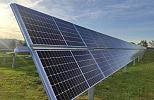
- Industry Events
16th Annual Safety Conference
- April 30 - May 1, 2024
- Elgin,
Pipe and Tube Conference
- May 21 - 22, 2024
- Omaha, NE
World-Class Roll Forming Workshop
- June 5 - 6, 2024
- Louisville, KY
Advanced Laser Application Workshop
- June 25 - 27, 2024
- Novi, MI