Senior Editor
- FMA
- The Fabricator
- FABTECH
- Canadian Metalworking
Categories
- Additive Manufacturing
- Aluminum Welding
- Arc Welding
- Assembly and Joining
- Automation and Robotics
- Bending and Forming
- Consumables
- Cutting and Weld Prep
- Electric Vehicles
- En Español
- Finishing
- Hydroforming
- Laser Cutting
- Laser Welding
- Machining
- Manufacturing Software
- Materials Handling
- Metals/Materials
- Oxyfuel Cutting
- Plasma Cutting
- Power Tools
- Punching and Other Holemaking
- Roll Forming
- Safety
- Sawing
- Shearing
- Shop Management
- Testing and Measuring
- Tube and Pipe Fabrication
- Tube and Pipe Production
- Waterjet Cutting
Industry Directory
Webcasts
Podcasts
FAB 40
Advertise
Subscribe
Account Login
Search
Employee engangement drives the manufacturing economy
Why companies with engaged employees stand apart
- By Tim Heston
- July 15, 2015
- Article
- Shop Management
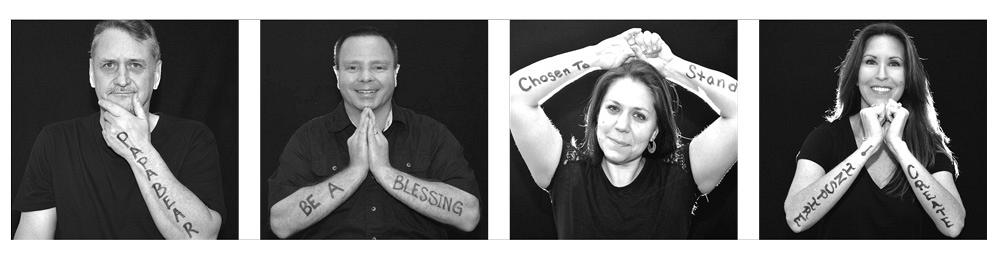
These photos, including one of General Manager David Bowes (aka, Papa Bear), and more are displayed in the lobby of Gap Partners Inc. (GPI). The words written on their forearms signify each person’s core values.
A Durham, N.C., tech company called Automated Insights wants to put me out of a job. OK, it doesn’t, really, but its product may shape a different kind of future for us writers of the world. The company’s technology basically automates the writing process. The computer struggles with metaphors and idioms, but it gets the job done extraordinarily quickly.
In a recent NPR story, the automation raced against Scott Horsley, one of the news organization’s quickest writers, to put together a simple news spot on Denny’s quarterly earnings. Horsley finished in seven minutes, lightning-fast for a typical news story. The computer didn’t even start until about a minute into the race, and it finished 60 seconds later. Ouch.
Concerns and fears over job-killing machines have been with us since the dawn of the Industrial Revolution. Whenever I talk to shop managers and ask them about new technology that allows fewer people to produce more, they usually tell me that they make sure they find a place for their best workers. If anything, they downsize through natural attrition. Of course, that means that ultimately these shops do employ fewer people, yet they’re also producing more than ever. At the same time, custom fabricators continue to scream for skilled people.
It’s a bit of a dichotomy. The industry needs good people, though not nearly as many people as it once did. Press brakes that change over automatically, combined with automatic angle measurement and compensation, are proving to have extremely high levels of throughput, even for jobs that are difficult to set up on a manual brake. More shops are programming welding robots offline and using welding automation even for low-volume jobs (thanks in part to efficient fixture development, like laser-cut components assembled in tab-and-slot fashion). Automated powder coat lines with quick color changes make painting more efficient. And laser cutting and punching have been highly automated for years.
Still, the industry needs more skilled people, and just knowing the business and technology isn’t enough. In May Jack Welch, the former CEO of GE and founder of the Jack Welch Management Institute, spoke in Nashville at Insights 2015, a software event for Epicor customers, and during the talk he described an employee evaluation chart with four quadrants. The left quadrants have good and bad performance, like good sales or production numbers; the right have good and bad behaviors, or how well these people represent the company culture and work with others. Behavior, he said, is just as important as performance. If people with bad behaviors but good performance (Welch, of course, used a more colorful description) are promoted, the company culture suffers—and in the long run, so does its financial performance.
Manufacturing automation does introduce another wrinkle of complexity. Sure, fabricators still need a few experts to run the equipment and manage the departments. When so few people are responsible for so much automated productivity, not finding the right people can really hurt. But it also means that many people don’t need to learn so much or be engaged to be productive. But without engagement, you get apathy.
“Lack of employee engagement is a serious problem in the United States,” Welch said, referring to a quarterly Gallup poll that measures employee engagement. “Since the recession in 2008, in every quarterly survey, employee engagement has yet to be more than 35 percent. Can you imagine working at a company where only 35 percent of employees are engaged?”
Welch should visit Gap Partners Inc. (GPI) in Rabun Gap, tucked away in the mountains of north Georgia. When entering, you see a flat-screen television playing a slideshow of the fabricator’s 100 employees, each wearing a black GPI shirt, and all with words written on their forearms, words that signify each person’s core values. Be a blessing. Inspire; create. Fun mom. Chosen to stand. Those photos line the conference room, too, where many customers have sat to watch GPI’s unique corporate video: not of machinery or arcs and sparks, but of people telling their stories, showing their silliness, and describing what drives them to do their best.
“Potential customers tell us that they were expecting another boring corporate video. They laugh, then they tell us they’re interested. That’s because we just showed them something that reflects the character of our people, and why we’re different.”
So said General Manager David Bowes, known at GPI as Papa Bear. A veteran of the automotive business, Bowes arrived at GPI two years ago. The company embraces lean manufacturing and other improvement tools wholeheartedly. It also has embraced modern technology.
But for Papa Bear and everyone else at GPI, all this is secondary. Modern technology is absolutely needed to compete, and so is lean manufacturing. But the same lean tools are available to any company, and the competition down the street theoretically can buy the same manufacturing technology. It’s the people and the ideas that set the company apart.
“Most tell about how they get their people to step up, unite, and work together to achieve a better result,” Bowes said. “That’s what you hear all the time, and frankly, that’s the most difficult part of the job.”
It’s a hackneyed phrase, but it really is the people who make the difference. At least that’s my hope. Now, if you’ll excuse me, I’m going to learn how to program those newfangled writing computers.
About the Author
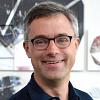
Tim Heston
2135 Point Blvd
Elgin, IL 60123
815-381-1314
Tim Heston, The Fabricator's senior editor, has covered the metal fabrication industry since 1998, starting his career at the American Welding Society's Welding Journal. Since then he has covered the full range of metal fabrication processes, from stamping, bending, and cutting to grinding and polishing. He joined The Fabricator's staff in October 2007.
subscribe now
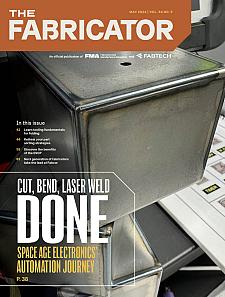
The Fabricator is North America's leading magazine for the metal forming and fabricating industry. The magazine delivers the news, technical articles, and case histories that enable fabricators to do their jobs more efficiently. The Fabricator has served the industry since 1970.
start your free subscription- Stay connected from anywhere
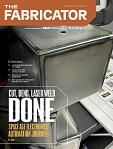
Easily access valuable industry resources now with full access to the digital edition of The Fabricator.
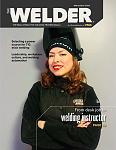
Easily access valuable industry resources now with full access to the digital edition of The Welder.
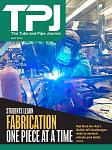
Easily access valuable industry resources now with full access to the digital edition of The Tube and Pipe Journal.
- Podcasting
- Podcast:
- The Fabricator Podcast
- Published:
- 04/16/2024
- Running Time:
- 63:29
In this episode of The Fabricator Podcast, Caleb Chamberlain, co-founder and CEO of OSH Cut, discusses his company’s...
- Trending Articles
Tips for creating sheet metal tubes with perforations
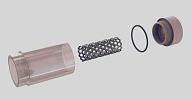
Are two heads better than one in fiber laser cutting?
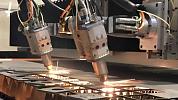
Supporting the metal fabricating industry through FMA
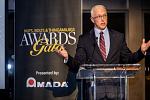
JM Steel triples capacity for solar energy projects at Pennsylvania facility
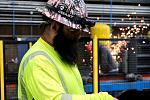
Omco Solar opens second Alabama manufacturing facility
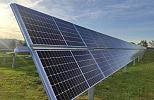
- Industry Events
16th Annual Safety Conference
- April 30 - May 1, 2024
- Elgin,
Pipe and Tube Conference
- May 21 - 22, 2024
- Omaha, NE
World-Class Roll Forming Workshop
- June 5 - 6, 2024
- Louisville, KY
Advanced Laser Application Workshop
- June 25 - 27, 2024
- Novi, MI