Senior Editor
- FMA
- The Fabricator
- FABTECH
- Canadian Metalworking
Categories
- Additive Manufacturing
- Aluminum Welding
- Arc Welding
- Assembly and Joining
- Automation and Robotics
- Bending and Forming
- Consumables
- Cutting and Weld Prep
- Electric Vehicles
- En Español
- Finishing
- Hydroforming
- Laser Cutting
- Laser Welding
- Machining
- Manufacturing Software
- Materials Handling
- Metals/Materials
- Oxyfuel Cutting
- Plasma Cutting
- Power Tools
- Punching and Other Holemaking
- Roll Forming
- Safety
- Sawing
- Shearing
- Shop Management
- Testing and Measuring
- Tube and Pipe Fabrication
- Tube and Pipe Production
- Waterjet Cutting
Industry Directory
Webcasts
Podcasts
FAB 40
Advertise
Subscribe
Account Login
Search
How automation affects manufacturing shop culture
Advancing technology can lift manufacturers and fabricators or leave some behind
- By Tim Heston
- March 25, 2021
- Article
- Shop Management
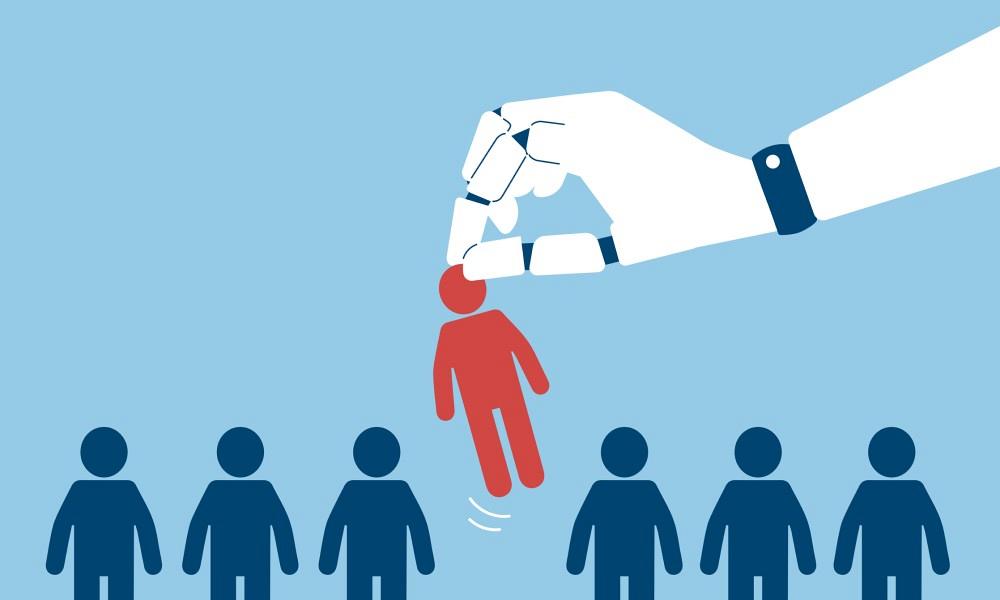
When automation reduces the need for skilled workers, what happens to shop culture in the manufacturing industry? Getty Images
In 2019 I chatted with Kurt Wollenberg, who several years before had sold a $10 million-plus fab shop he had built from nothing, mainly because he didn’t like the headache of running a 75-person company. When we spoke he had recently gotten back into the metal fabrication fray, launching Kaukauna, Wis.-based Metal Fab Solutions. Why? He missed people in the shop, his co-workers in the office, his wide network of longtime customers. He missed his friends.
About eight years ago, during a group tour of Lithonia, Ga.-based Southern Metalcraft, organized by the Fabricators & Manufacturers Association, Ken Williams pointed to pockmarks on a wall near the shop floor, marks his now-grown daughter had left practicing her softball game. No one on the tour asked why he hadn’t repaired the pockmarks. Everyone just smiled and nodded, knowingly.
Several years before that I visited Wyoming Machine in Stacy, Minn. (the shop launched in Wyoming, Minn., hence the name), a precision sheet metal shop run by two sisters, Lori and Traci Tapani. The Tapanis live a block apart, had their first children (both girls) about two weeks apart from each other, and finish each other’s sentences. These sisters are close; that much is obvious. But they’re also present, eager, curious, and excited about what the right people and technology can accomplish.
More than anything, the custom metal fabrication business is about relationships, be they with customers, fellow employees, suppliers, or anyone else within a fab shop’s sphere. It’s why the difficulty of finding good, skilled employees hits people emotionally. It’s also why there’s an underlying tension as technology transforms the business. Fabricators can’t ignore technology, but how will technology change those relationships? What will happen to what many consider to be the best thing about metal fabrication: its people?
Today’s shop leaders, many of them in their 40s and early 50s, entered the business at an opportune time. Computers and associated automation were starting to take over, but fab shops still employed people who learned how to fabricate before the PC, perhaps even before the CNC. In the 1980s, longtime press brake personnel might have performed bend calculations and manual layout, delving deep into trigonometry to form an incredibly complicated part. But in the office, the shop engineer was probably getting his first taste of computer-aided design.
There was something about those old brake gurus. They spent years learning their craft, had pride of ownership, and just got better and better over time. Now, with 3D CAD and simulation software, rookies can create some incredibly complicated parts in no time at all. Businesses can’t compete without such technology, but what happens to the people? Technology can lift people up or leave people behind; the progressive fab shop owner works to maximize the former and minimize the latter.
Whatever the case, technology marches on. The promises of Industry 4.0 introduce entirely new ways of doing business. Employees handle the exceptions, the oddball orders, the unusual or challenging machine problem, while automation handles the routine. All this sounds great, but again, what happens to people in this scenario? After all, with the routine automated, how do new employees learn? If they do learn, technology will lift them up. If they don’t, technology will leave them behind.
The left-behind scenario doesn’t bode well for the industry’s image. As fabricators become more automated, front-line operators become button-pushers. They clock in, produce, and clock out. Some might like the job’s predictability, especially if they’re just not career-focused and they find the working environment to be pleasant. But others who want more out of their workday might become frustrated and bored, especially if they work in a shop culture lacking trust.
Regardless, if shops automate simply to eliminate the need for skill, to be able to hire an easily replaceable warm body at a machine, then the working environment might not be that pleasant. Even those who do enjoy button-pushing workdays might jump ship. All this leaves the company with a core group of highly engaged, skilled, stressed people struggling to keep a host of front-line workers engaged and praying that the shop down the street isn’t offering 50 cents more an hour.
The lift-people-up scenario creates a new kind of shop altogether. While the technical guru of old learned the ropes over time, the entry-level employee of 2021 begins producing good parts immediately, but also continues learning. He or she might delve more into sheet metal design, how metal elongates during bending, how the laser creates a clean cut with no dross, or how welding technique minimizes distortion, but they probably won’t spend years perfecting a single craft. They might have an area of concentration, but they also see the big picture, how work flows from one end of the plant to the other. They collaborate with just about everyone. No one’s a stranger, and everyone is incentivized—financially and otherwise—to learn more.
Last year I spoke with Jonah Higgs, the technical services leader at Schofield, Wis.-based Applied Laser Technologies. He told me stories about how the shop’s technical leads work with operators on a challenging project, bouncing ideas back and forth about alternative ways to approach a particular problem. “We have fun, challenge each other’s solution on how we should solve a problem, and do high-fives when we’ve found a new way. Let me tell you, those are the good days.”
Such collaborative problem-solving is an ingredient for strong working relationships, even friendships. When the collaboration stops, shop culture suffers. When everyone participates in problem-solving, tackling those exceptions to routine that technology just can’t automate, those relationships—the building blocks of the metal fabrication business—get stronger.
About the Author
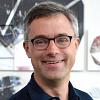
Tim Heston
2135 Point Blvd
Elgin, IL 60123
815-381-1314
Tim Heston, The Fabricator's senior editor, has covered the metal fabrication industry since 1998, starting his career at the American Welding Society's Welding Journal. Since then he has covered the full range of metal fabrication processes, from stamping, bending, and cutting to grinding and polishing. He joined The Fabricator's staff in October 2007.
Related Companies
subscribe now
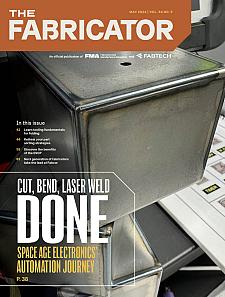
The Fabricator is North America's leading magazine for the metal forming and fabricating industry. The magazine delivers the news, technical articles, and case histories that enable fabricators to do their jobs more efficiently. The Fabricator has served the industry since 1970.
start your free subscription- Stay connected from anywhere
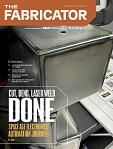
Easily access valuable industry resources now with full access to the digital edition of The Fabricator.
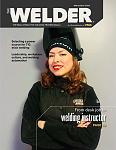
Easily access valuable industry resources now with full access to the digital edition of The Welder.
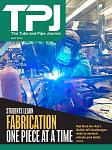
Easily access valuable industry resources now with full access to the digital edition of The Tube and Pipe Journal.
- Podcasting
- Podcast:
- The Fabricator Podcast
- Published:
- 04/16/2024
- Running Time:
- 63:29
In this episode of The Fabricator Podcast, Caleb Chamberlain, co-founder and CEO of OSH Cut, discusses his company’s...
- Trending Articles
Tips for creating sheet metal tubes with perforations
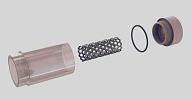
JM Steel triples capacity for solar energy projects at Pennsylvania facility
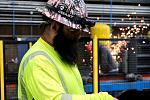
Are two heads better than one in fiber laser cutting?
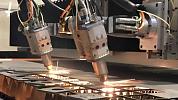
Supporting the metal fabricating industry through FMA
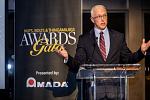
Omco Solar opens second Alabama manufacturing facility
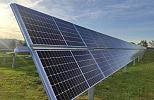
- Industry Events
16th Annual Safety Conference
- April 30 - May 1, 2024
- Elgin,
Pipe and Tube Conference
- May 21 - 22, 2024
- Omaha, NE
World-Class Roll Forming Workshop
- June 5 - 6, 2024
- Louisville, KY
Advanced Laser Application Workshop
- June 25 - 27, 2024
- Novi, MI