Director of Business Development
- FMA
- The Fabricator
- FABTECH
- Canadian Metalworking
Categories
- Additive Manufacturing
- Aluminum Welding
- Arc Welding
- Assembly and Joining
- Automation and Robotics
- Bending and Forming
- Consumables
- Cutting and Weld Prep
- Electric Vehicles
- En Español
- Finishing
- Hydroforming
- Laser Cutting
- Laser Welding
- Machining
- Manufacturing Software
- Materials Handling
- Metals/Materials
- Oxyfuel Cutting
- Plasma Cutting
- Power Tools
- Punching and Other Holemaking
- Roll Forming
- Safety
- Sawing
- Shearing
- Shop Management
- Testing and Measuring
- Tube and Pipe Fabrication
- Tube and Pipe Production
- Waterjet Cutting
Industry Directory
Webcasts
Podcasts
FAB 40
Advertise
Subscribe
Account Login
Search
Inline process auditing
Moving beyond random sampling
- By Bruce Johnson
- June 12, 2003
- Article
- Shop Management
![]() |
Sound familiar? What are the options?
Today's Audit
Today the most widely accepted practice for checking part or process quality is random or, at best, controlled sampling. With these types of sampling, you hope those four parts you checked from 70 are enough to catch a major disaster. In truth, however, they typically are not enough to catch potentially many minidisasters that may be part of even a controlled process.
Random sampling can catch the occasional catastrophe once it has started. Unfortunately, by that time you may already have sent many bad parts out the door.
Controlled sampling gives a better picture of quality than random sampling, but even if you are using the statistical tools on the floor as best as you can, the control charts still may indicate that parts have been made in and out of specification all day, so several bad parts could be on their way out the door.
What is the alternative? Time and cost do not allow checking each part by pulling it off the line, clamping it into a fixture, checking it with a jig or touchprobe, and bringing it back to the line.
Inline Auditing
![]() |
Figure 1 One hundred percent noncontact, inline process auditing audits parts and assemblies while providing the necessary tools and data to help reduce variation in the process. |
A new trend that addresses these problems is 100 percent noncontact, inline process auditing (see Figure 1). This process audits parts and assemblies and provides the tools and data to help reduce process variation.
Noncontact, inline auditing can be performed several ways.
Robot-based Scanning. A robot-based system works directly inline with the process and consists of multiaxis robots, laser scanners, feature analysis and comparison software, and a statistical package designed for the quality control inspector and the shop floor (see Figure 2).
Robots and sensors come in many varieties and sizes. Systems can work in up to eight different axes for scanning flexibility and can be anchored, powered up, and calibrated in less than a day. Parts can be located online through visual or mathematical fixturing.
More than 250 different parts or scan processes can be programmed for each drive, and industrial computer screens show operators the scan trends and variations for monitoring on the floor. Data then can be archived for future review and, through bar coding or optical character recognition, matched to the part throughout its working life.
Repeatability typically ranges from 0.002 to 0.004 inch. Systems can be installed and programmed quickly to run continuously.
Moving Linear or Radial-based Scanning
![]() |
Figure 2 A robot scanner scans a rear floor trim panel and mounting brackets (left). The scanned image showing the laser path coverage appears on the operator's monitor (right). |
These systems are designed to move around specific areas of the same or similar parts in the assembly or on the floor. Scanners mounted to linear rails moving in the X, Y, or Z axis or radial servo arms rotating about an object scan specific areas or features and perform comparisons and validations.
These systems may still be tied to the process so that parts or assemblies can be measured at specific stations or on-the-fly as needed. Semifixed systems tend to be less flexible but work in tighter spaces and often can obtain even higher repeatability and accuracy.
Fixed Linear or Radial-based Scanning
These systems are designed for batch operations. Sensors are mounted to linear rails or radial arms and move in specific programmed paths about a stationary part. Scanning is completed and then compared and validated as with the other systems, but the flexibility is reduced.
This method is appropriate for applications in which a few parts of similar size are produced. Its repeatability and accuracy tend to be high, and the process moves very quickly while remaining noncontact.
Auditing for Advantage
Many forms of part or process auditing exist today. With new capabilities for 100 percent measurement of parts or assemblies using thousands of points inline and at process speeds, many companies now not only can reduce product variation, but also implement the Six Sigma process (see Sidebar). Operational and inventory savings, as well as producing to tight quality specifications, can be a competitive advantage for companies today and in the future.
Bruce Johnson is director of business development for MERILab Inc., 2390 S. Tejon St., Englewood, CO 80110, 303-922-3775, fax 303-936-1480, b.johnson@merilab.com, www.merilab.com.
You can't improve what you can't measure.
But how do you measure a process?
Six Sigma is a management philosophy developed by Motorola that emphasizes setting extremely high objectives, collecting data, and analyzing results to a fine degree as a way to reduce defects in products and processes. The Greek letter sigma sometimes is used to denote variation from a standard. The philosophy behind Six Sigma is that if you measure how many defects are in a process, you can determine how to eliminate them systematically and get as close as possible to perfection.
The foundation of Six Sigma is the customer's wants and needs. Three key program points are:
- Critical to quality (CTQ). Areas that are important to the customer
- Quality defects. Product flaws that result from not meeting the customer's requirements
- Overall process capability. Repeatability of the process, variations in the process, such as out-of-specification parts and product delivery delays, can prevent the product from meeting a customer's wants or needs.
Implementing Six Sigma requires five steps:
- Define the problem.
- Measure the problem.
- Analyze the causes of variation.
- Improve the process by eliminating the variation.
- Control the improvement by errorproofing or using alarm go/no-go feedback.
Inline process auditing may be able to help you complete some of these steps by defining, measuring, and controlling the defect or process variation. Bottom-line savings may come in the form of reduced rework and scrap, reduced inspection labor, reduced operation cycle time, and tighter specifications and higher quality.
About the Author
Bruce Johnson
2390 S. Tejon St.
Englewood, CO 80110
303-922-3775
subscribe now
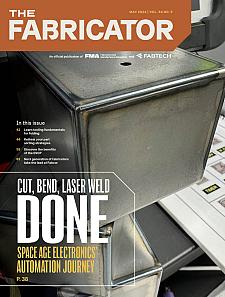
The Fabricator is North America's leading magazine for the metal forming and fabricating industry. The magazine delivers the news, technical articles, and case histories that enable fabricators to do their jobs more efficiently. The Fabricator has served the industry since 1970.
start your free subscription- Stay connected from anywhere
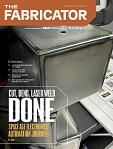
Easily access valuable industry resources now with full access to the digital edition of The Fabricator.
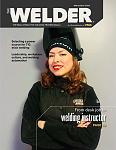
Easily access valuable industry resources now with full access to the digital edition of The Welder.
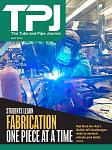
Easily access valuable industry resources now with full access to the digital edition of The Tube and Pipe Journal.
- Podcasting
- Podcast:
- The Fabricator Podcast
- Published:
- 04/16/2024
- Running Time:
- 63:29
In this episode of The Fabricator Podcast, Caleb Chamberlain, co-founder and CEO of OSH Cut, discusses his company’s...
- Trending Articles
Tips for creating sheet metal tubes with perforations
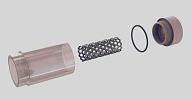
JM Steel triples capacity for solar energy projects at Pennsylvania facility
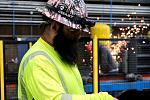
Are two heads better than one in fiber laser cutting?
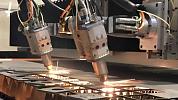
Supporting the metal fabricating industry through FMA
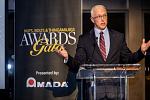
Omco Solar opens second Alabama manufacturing facility
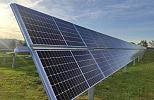
- Industry Events
16th Annual Safety Conference
- April 30 - May 1, 2024
- Elgin,
Pipe and Tube Conference
- May 21 - 22, 2024
- Omaha, NE
World-Class Roll Forming Workshop
- June 5 - 6, 2024
- Louisville, KY
Advanced Laser Application Workshop
- June 25 - 27, 2024
- Novi, MI