President
- FMA
- The Fabricator
- FABTECH
- Canadian Metalworking
Categories
- Additive Manufacturing
- Aluminum Welding
- Arc Welding
- Assembly and Joining
- Automation and Robotics
- Bending and Forming
- Consumables
- Cutting and Weld Prep
- Electric Vehicles
- En Español
- Finishing
- Hydroforming
- Laser Cutting
- Laser Welding
- Machining
- Manufacturing Software
- Materials Handling
- Metals/Materials
- Oxyfuel Cutting
- Plasma Cutting
- Power Tools
- Punching and Other Holemaking
- Roll Forming
- Safety
- Sawing
- Shearing
- Shop Management
- Testing and Measuring
- Tube and Pipe Fabrication
- Tube and Pipe Production
- Waterjet Cutting
Industry Directory
Webcasts
Podcasts
FAB 40
Advertise
Subscribe
Account Login
Search
IoT technologies help to create agile manufacturers
Metal fabricators and formers need to recognize potential of digital manufacturing so they won’t become a relic
- By Bill Frahm
- June 12, 2020
- Article
- Shop Management
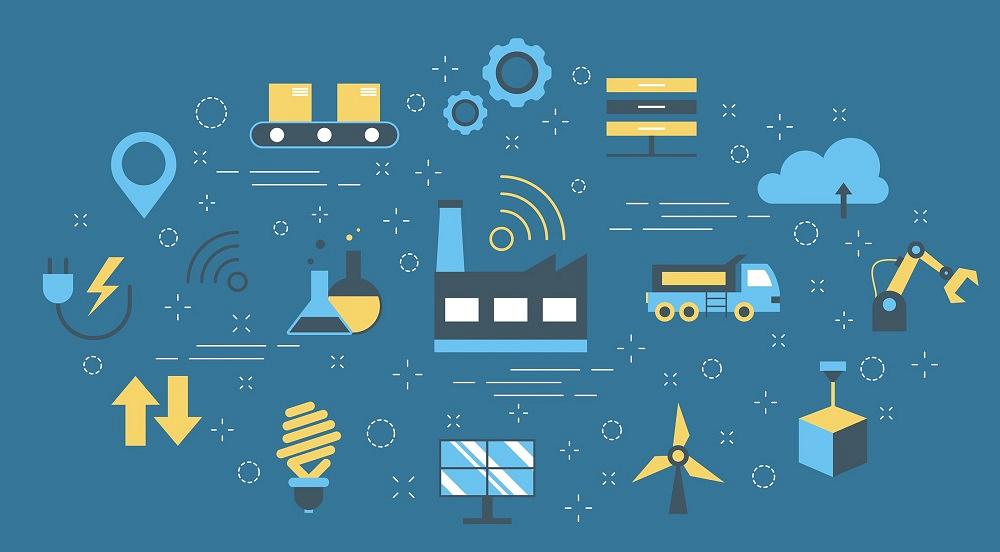
Without the instantaneous information gathering and analysis made possible by internet of things (IoT) technologies, metal fabricators and other manufacturers can’t make the best decisions. Getty Images
We’ve all heard others talk about how the world has become smaller. That actually is addressed by a social/economic theory called Space-Time Compression. This theory is based on the observation that as technologies like transportation, communication, and machinery evolve, humankind becomes increasingly interconnected, regardless of geography. Likewise, the speed at which we work and connect increases as these same technologies improve.
Probably the greatest impact of the internet of things (IoT) will be the compression of the time it takes for us to identify and respond to events in our business that require attention. Continued success and business growth require you to anticipate markets and adapt to meet the changes of new technologies. Evolution in technology, communication, and transportation influence your market both today and in the future. In sheet metal fabricating and forming, new production technologies and materials will continue to change your customers’ expectations while opening opportunities for those willing to invest in planning and training to meet evolving demands.
IoT isn’t revolutionary, as much as it is a step-function in the availability and immediacy of information supporting rapid decision-making. IoT represents a significant increase in our decision-making capabilities. The availability of affordable and reliable technologies increases our ability to collect, store, and analyze information quickly and easily.
With our new opportunities also come new liabilities and responsibilities. Decision-making will become more distributed. Faster decisions demand deeper knowledge. The integrity of information must be tightly controlled. We must keep our monitoring devices clean and calibrated to prevent false readings and poor decisions. Our manufacturing, management, and marketing processes must adapt to our new reality. Keep in mind that failure to act on a reported issue resulting in injury or loss becomes a documented corporate liability. As technical agility expands, so must employee agility.
Probably the best analogy of new technology viewed wrong is the history of the Eastman Kodak Co. Kodak was the leader in film photography throughout the 20th century. Founder, George Eastman, was a pioneer in introducing dry plates in the mid-19th century. Dry plates replaced wet plates that required photographers to carry carts of chemicals with them.
Kodak went on to develop the commonly used films and cartridges loved by amateur and professional photographers during the 20th century. The Brownie camera, introduced in 1900, was a small portable film camera that first brought photography to anyone.
Throughout the twentieth century, Kodak film and cameras were a phenomenon. We even talked of “Kodak moments,” thanks to effective advertising. Paul Simon even sang a popular song about Kodachrome film. Then, in 1975, Kodak engineer Steven Sasson developed the first portable digital camera.
Kodak’s unfortunate response was to suppress the camera because it didn’t support Kodak’s film business. Digital cameras began entering the market during the 1980s. Kodak followed the digital market, but was no longer a leader. Even when the company was the first to market (such as its introduction of the first wi-fi enabled camera), itfailed to take advantage of the opportunity. Kodak’s consumer photography strategy focused heavily on printing and digital frames. Kodak’s failure to anticipate the digital market and take a leadership position ended with company filing for bankruptcy protection in January 2012.
Part of what Kodak failed to recognize was a step-function reduction in the lifecycle of a photograph that digital photography introduced. In the days of film, the time from capture of an image through sharing could often be measured in months. The normal process involved:
- Load a 24- or 36-image film cartridge in the camera.
- Decide if the image is worth capturing, because you had a very limited amount of available exposures.
- Capture the photo.
- Return home with your exposed film cartridges.
- Send your cartridges to a processor.
- Wait hours to days for your prints.
- Show your prints to family and friends during gatherings and holidays over the course of the following year.
Compare that to today’s digital process that only takes a few short minutes:
- Load a storage device in your camera, or not if using your phone. By the way, you can store hundreds of images.
- Capture your image.
- Immediately post your image to your social media of choice.
- Friends and family everywhere can now see your new image.
IoT promises the same compression of time from event to notification. Where we once had to order analysis reports from IT, we now can collect immediate analytical information. Information that once required hours or days now can be on your monitor as events are happening. This offers the advantage of allowing operators to correct errors before they become production issues. It also alerts us to potential maintenance issues before they create quality problems and production down-time.
Learning and understanding materials and production offer your best opportunity to become a truly responsive and agile operation. Your knowledge and a robust maintenance schedule for IoT components are also your best defense against bad information and the drift away from data accuracy.
If you plan to adopt IoT, now is a great time to reinforce good maintenance behaviors and support employee development in materials, processes, and technologies. Production staff must understand the opportunities and limitations of IoT and data analysis. Also, your data analysts must understand how your materials and forming operations work and the impact of their analyses on your daily and long-term activities.
IoT also requires that you learn to look to the future and anticipate the many changes coming to your decision-making capabilities and responsibilities.
About the Author
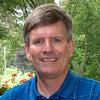
Bill Frahm
P.O. Box 71191
Rochester Hills, MI 48307
248-506-5873
subscribe now
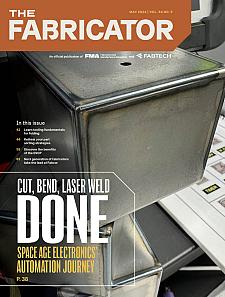
The Fabricator is North America's leading magazine for the metal forming and fabricating industry. The magazine delivers the news, technical articles, and case histories that enable fabricators to do their jobs more efficiently. The Fabricator has served the industry since 1970.
start your free subscription- Stay connected from anywhere
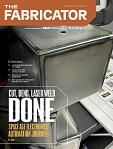
Easily access valuable industry resources now with full access to the digital edition of The Fabricator.
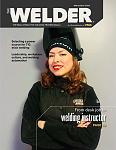
Easily access valuable industry resources now with full access to the digital edition of The Welder.
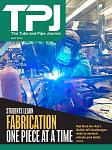
Easily access valuable industry resources now with full access to the digital edition of The Tube and Pipe Journal.
- Podcasting
- Podcast:
- The Fabricator Podcast
- Published:
- 04/16/2024
- Running Time:
- 63:29
In this episode of The Fabricator Podcast, Caleb Chamberlain, co-founder and CEO of OSH Cut, discusses his company’s...
- Trending Articles
Tips for creating sheet metal tubes with perforations
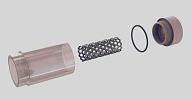
Are two heads better than one in fiber laser cutting?
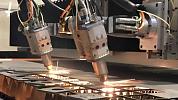
Supporting the metal fabricating industry through FMA
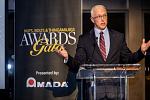
JM Steel triples capacity for solar energy projects at Pennsylvania facility
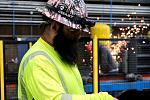
Omco Solar opens second Alabama manufacturing facility
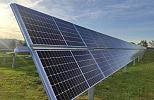
- Industry Events
16th Annual Safety Conference
- April 30 - May 1, 2024
- Elgin,
Pipe and Tube Conference
- May 21 - 22, 2024
- Omaha, NE
World-Class Roll Forming Workshop
- June 5 - 6, 2024
- Louisville, KY
Advanced Laser Application Workshop
- June 25 - 27, 2024
- Novi, MI