Principal
- FMA
- The Fabricator
- FABTECH
- Canadian Metalworking
Categories
- Additive Manufacturing
- Aluminum Welding
- Arc Welding
- Assembly and Joining
- Automation and Robotics
- Bending and Forming
- Consumables
- Cutting and Weld Prep
- Electric Vehicles
- En Español
- Finishing
- Hydroforming
- Laser Cutting
- Laser Welding
- Machining
- Manufacturing Software
- Materials Handling
- Metals/Materials
- Oxyfuel Cutting
- Plasma Cutting
- Power Tools
- Punching and Other Holemaking
- Roll Forming
- Safety
- Sawing
- Shearing
- Shop Management
- Testing and Measuring
- Tube and Pipe Fabrication
- Tube and Pipe Production
- Waterjet Cutting
Industry Directory
Webcasts
Podcasts
FAB 40
Advertise
Subscribe
Account Login
Search
Lean manufacturing in metal fabrication: How about some visual cues?
The right visual cues can bring rhythm to the fab shop
- By Jeff Sipes
- December 1, 2017
- Article
- Shop Management
Next time you go on a gemba walk, put yourself in the shoes of the machine operator, the welder, and the press brake operator. If they are cherry-picking the next job based on what is easiest, has the least changeover, or has the loosest standards, then they might be running what you don’t need and not running what you do need. Put yourself in their shoes. In the absence of better direction, can you be critical of the choices they make?
If you were doing their job, how would you know what to do, how to do it, and what comes next? If the answers aren’t obvious, then their work areas might be candidates for some visual cues.
The Traditional Work Area
Let’s visit Fred, a welder in the fab shop. Fred has been around for a lot of years and knows the job as well as anybody. His work area is like many others in the fab shop. The parts to be welded are placed in any open space in the general area and are expected to be welded into assemblies sometime soon. At best, Fred’s supervisor might come around and tell him to run a certain hot job next.
But overall, Fred has little in the way of a forward-looking schedule. So Fred needs to decide which job to run next. Maybe he sees that another order for the parts he just ran is scheduled for two weeks from now and he can use the same setup. Or maybe he knows that one of the jobs in the pile is easy to run and has a large batch size. Or he could hunt down the supervisor to get some input on priorities. In all these cases, the heat is on Fred to figure it out … and he will. The question is, will he run what is really needed?
This scenario sounds a bit harsh. Can an operation really be that loose? Do we really expect Fred to make these important decisions without giving him enough information, ground rules, and guidance to know the answers? If you are willing to take an honest and objective inward look, you might be surprised. What do we do to improve the situation and help Fred be more effective? How about some visual cues?
Visual cues and signals help employees perform their jobs and, ultimately, make their workday easier. Cues and signals can be simple and yet extremely effective. In the lean body of knowledge, we refer to these visual cues or signals as visual controls. Typical visual controls in the fab shop include:
Aisle floor markings. If you do not have aisle markings on your floors, how can you expect people (employees, vendors, customers, and other visitors) to know where it is safe to walk? How do you know what the traffic flow for materials is supposed to be? I never cease to be amazed at the power of a piece of yellow tape on the floor. That tape helps define space and instill discipline.
Incoming and outgoing material floor markings. Floor markings at the workcell can define how space is intended to be used. If incoming materials arrive on skids or in totes, mark the space where material handlers should drop the material so employees know the status of incoming work. The same applies to outgoing material. Mark the floor so that, after a quick glance, everyone can tell the status of materials in the area.
Andon signals. Used to indicate status, an andon signal communicates that either some action is required or that everything is OK. The signal can be visual or audio. If the signal is based on lights, then the green light means all is OK, blue might mean material handling is needed, and red might indicate an equipment issue that requires maintenance. As long as employees can see or hear those signals, they have an effective way to communicate with their support resources.
Production control visual board. Posted at an individual work center or at the department level, the production control visual board shows information about schedules, quality issues, safety priorities, and customer feedback, plus whatever else is important in your operation. You can tailor the content to meet your needs. These boards are most effective when used with daily standup meetings to reinforce priorities.
Red and green replenishment signals. These help employees stay on top of incoming components. For instance, consider corrugated material in your shipping department. If corrugated sheets lie flat on the floor against the wall, you could use the wall as part of your replenishment signal. Determine the maximum number of corrugated sheets you should hold, as well as the number of sheets you should have at the point you send the replenishment signal to your vendor. Now stack that number of corrugated sheets and mark the height of the stack on the wall. Paint the wall red from the floor to that mark. Then paint the wall green from the replenishment height to the height of the maximum number of sheets. When you pull a sheet for use, as long as the wall is still green, all is OK. The moment you pull a sheet and red appears, then send the replenishment signal. This is about as simple and effective a replenishment system as you could possibly have.
Container pitch signal. The pitch is the amount of time it takes to fill a container, move it downstream, and retrieve another container to keep producing. One client used a container sized to hold 30 minutes’ worth of product—that is, a 30-minute pitch. This created a predictable, easy rhythm in the operation. Both the operator and the supervisor could assess the state of product with a quick glance.
This is only a sampling of possible visual cues, but it at least gives you some ideas to get started. One word of caution: Be sure to take before-and-after pictures, because it is so easy to forget the old way.
The Contemporary Work Area
Let’s revisit Fred. He is looking ahead to what jobs he needs to work on in his weld cell. The plant is well on its way to implementing lean methods and techniques. The plant leadership has invested in education and awareness for all the employees … and more important, the employees are involved in making changes.
What does this have to do with Fred getting ready for his next job in the weld cell? Thanks to visual cues, Fred knows exactly what to work on next. He simply refers to a dispatch list on the production control board.
Material for the next job is queued in a spot that’s labeled with floor markings in Fred’s work area. He can expect the material to be ready in the same place every time, because this is part of the standard process for material flow.
Fred does not need to chase down the supervisor to get this answer. There is no scrambling or disruption, no dropping everything to look for material for the next job. The entire operation, including Fred’s weld cell, has a smooth, predictable rhythm to it.
Make It Easy
When you go to gemba, look at the operation with visual cues in mind. If you visit a supplier or customer plant, the same thing applies. See how effective the visual communications are.
Put yourself in Fred’s shoes. Have you done enough to make it easy for Fred, the supervisor, and the material handler to do their jobs? Visual cues help create clarity and alignment in your fab shop. The more you can minimize disruptions, the better the environment will be for Fred and all his colleagues to produce consistently, effectively, and safely.
Jeff Sipes is principal of Back2Basics LLC, 317-439-7960, www.back2basics-lean.com. If you have improvement ideas you’d like to read about, contact him at jwsipes@back2basics-lean.com or Senior Editor Tim Heston at timh@thefabricator.com.About the Author
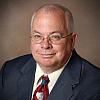
Jeff Sipes
9250 Eagle Meadow Dr.
Indianapolis, IN 46234
(317) 439-7960
subscribe now
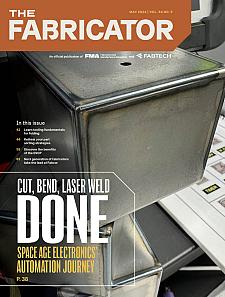
The Fabricator is North America's leading magazine for the metal forming and fabricating industry. The magazine delivers the news, technical articles, and case histories that enable fabricators to do their jobs more efficiently. The Fabricator has served the industry since 1970.
start your free subscription- Stay connected from anywhere
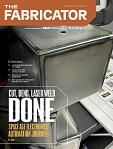
Easily access valuable industry resources now with full access to the digital edition of The Fabricator.
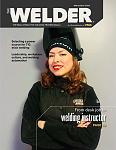
Easily access valuable industry resources now with full access to the digital edition of The Welder.
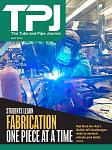
Easily access valuable industry resources now with full access to the digital edition of The Tube and Pipe Journal.
- Podcasting
- Podcast:
- The Fabricator Podcast
- Published:
- 04/16/2024
- Running Time:
- 63:29
In this episode of The Fabricator Podcast, Caleb Chamberlain, co-founder and CEO of OSH Cut, discusses his company’s...
- Trending Articles
Tips for creating sheet metal tubes with perforations
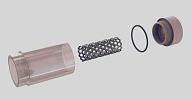
Supporting the metal fabricating industry through FMA
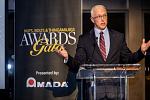
JM Steel triples capacity for solar energy projects at Pennsylvania facility
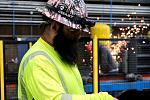
Fabricating favorite childhood memories
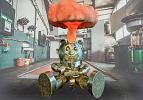
Omco Solar opens second Alabama manufacturing facility
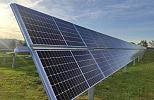
- Industry Events
16th Annual Safety Conference
- April 30 - May 1, 2024
- Elgin,
Pipe and Tube Conference
- May 21 - 22, 2024
- Omaha, NE
World-Class Roll Forming Workshop
- June 5 - 6, 2024
- Louisville, KY
Advanced Laser Application Workshop
- June 25 - 27, 2024
- Novi, MI