Editor-in-Chief
- FMA
- The Fabricator
- FABTECH
- Canadian Metalworking
Categories
- Additive Manufacturing
- Aluminum Welding
- Arc Welding
- Assembly and Joining
- Automation and Robotics
- Bending and Forming
- Consumables
- Cutting and Weld Prep
- Electric Vehicles
- En Español
- Finishing
- Hydroforming
- Laser Cutting
- Laser Welding
- Machining
- Manufacturing Software
- Materials Handling
- Metals/Materials
- Oxyfuel Cutting
- Plasma Cutting
- Power Tools
- Punching and Other Holemaking
- Roll Forming
- Safety
- Sawing
- Shearing
- Shop Management
- Testing and Measuring
- Tube and Pipe Fabrication
- Tube and Pipe Production
- Waterjet Cutting
Industry Directory
Webcasts
Podcasts
FAB 40
Advertise
Subscribe
Account Login
Search
Sassy Engines fires up plasma cutter to stay on top of production needs
Outsourcing of fabricated parts caused too many delays
- By Dan Davis
- February 2, 2018
- Article
- Shop Management
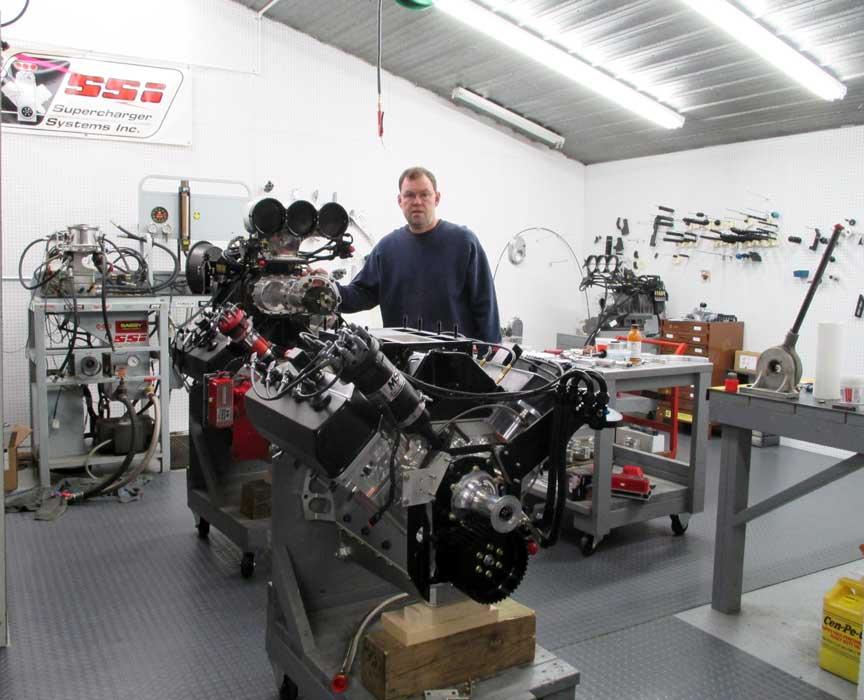
Figure 1
Brian Knox, owner and president, Sassy Engines Inc., poses with one of the company’s supercharged Hemi engines that will end up in modified tractors pulling sleds that could weigh up to 65,000 pounds.
Someone describing Sassy Engines Inc., Weare, N.H., as a simple engine maker is trying to pull a fast one. The company makes the engines for the leading modified tractors in the National Tractor Pullers Association (NTPA) circuit. In fact, it has been a part of more than 40 NTPA championships over the last couple of decades. These are no simple engines.
Now motorsports enthusiasts might know of engine shops that specialize in drag racing, but they will struggle to find a similar shop with as much expertise in tractor pulling as Sassy Engines (see Figure 1). The company has been at it full-time since 1998, and before that the Knox family, the Sassy Engines founders, were pulling themselves. A family affair evolved into a commercial endeavor that has a loyal following not just in the U.S., but in Europe.
“The biggest reason that people buy engines and parts here is that we can tell them how to use it,” said Brian Knox. “We know what’s the right part. We sell the right combination to people. It all fits.”
If the company struggled in any area with its business, it was in getting fabricated parts back from a local shop in a timely manner. Sassy Engines prides itself on being knowledgeable and prompt with orders, but sometimes the fab shop might need several weeks to supply those parts, which in many instances were small in size but a very large part of the engine packages sold to customers.
In early 2017 Sassy Engines took control of its fabrication needs. It purchased a 4- by 8-foot mechanized plasma cutting table, and it’s changed the nature of its parts fabrication and delivery business. It controls its own destiny now.
Building an Engine-building Business
In a way it should be no surprise that Sassy Engines has jumped into fabrication. Most of the eight company employees have some connection to racing and pulling, and these sports demand that the driver and crew be self-reliant. You are only as good as your ride, and that ride is only as good as those that work on it and drive it.
The Knox family got started racing in the late 1960s. John Knox would compete in the men’s classifications, and because she happened to be hanging around and showed some interest, his wife Rodalyn started participating in the “powder puff” class for women. Being observant, Knox noticed that his wife’s times were better than his own, so he convinced her to race against the men. That proved to be fortuitous advice.
Rodalyn worked her way up the ranks in the ensuing year until she was competing against the best in top Funny Car races in New England. The late 1970s were a time of memorable drag racers, and people likely remember Knox’s ride with “Country Girl” emblazoned on the side (Figure 2). It also was a dangerous time, as the Knox family actually witnessed someone dying on the track toward the end of 1978. The family liked the sport, but they liked the idea of living normal lives as well. Rodalyn stepped out from behind the wheel, at least for the time being.
John Knox still wanted to be involved in some sort of racing, and he found a kindred soul in a family friend that suggested tractor pulling. The friend said he’d buy a frame if Knox applied his engine-making skills to the ride. A partnership was born.
By the mid-1980s, the friend had grown tired of the commitments involved in traveling to races and the time needed to prep the rig to run. Knox now needed a new driver.
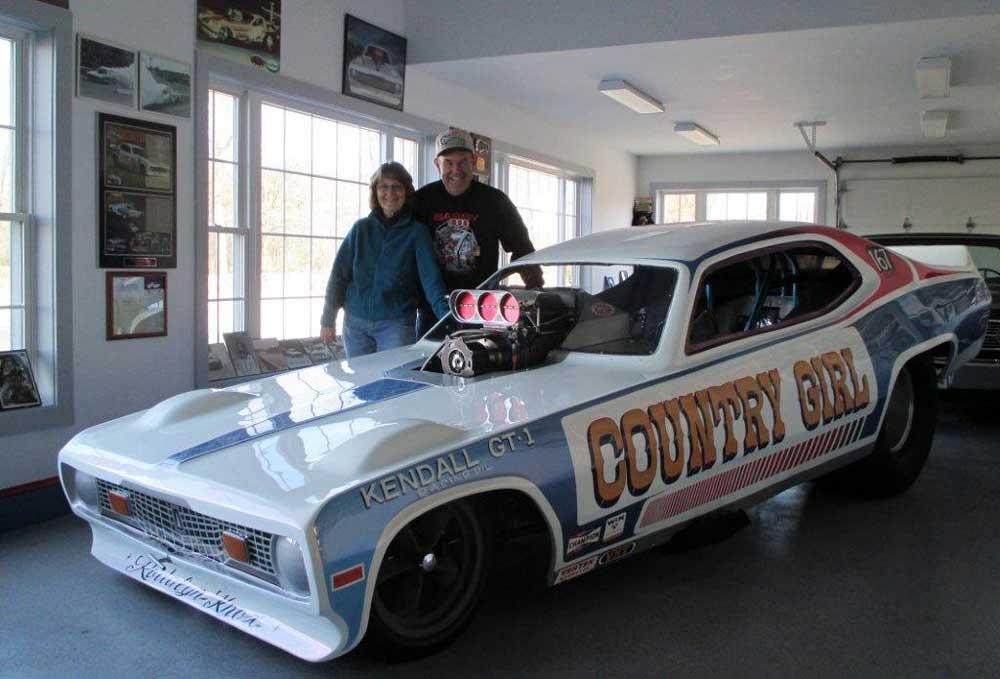
Figure 2
Rodalyn and John Knox pose with the Country Girl Funny Car that Rodalyn drove to fame in the 1970s and that John built and maintained. The couple left drag racing, and John jumped into tractor pulling in the 1980s. With Rodalyn driving the tractors in the 1990s, the Knox family dominated the pulling scene, winning several championships along the way.
From 1985 to 1989, Knox went through three drivers. Luckily, he knew someone with driving experience that might prove to be more of a long-term solution.
“We convinced my mom that it was safe and wouldn’t get her killed,” Brian Knox said. “She took over driving in 1989.”
The timing was perfect because now Brian was heavily involved as part of the crew. It also didn’t hurt that Rodalyn’s skill as a drag racer carried over to tractor pulling. As the driver of Brian’s four- and six-engine unlimited modified tractors, Rodalyn and the team dominated the 1990s. She won three unlimited modified NTPA Grand National titles and also had a second-place finish and two thirds. She was named to the NTPA Hall of Fame in 2008.
John Knox was so energized with the family’s early success in tractor pulling that he sold his business in 1990 and committed to the pulling lifestyle full-time. That also got him more involved in not only maintaining his own pulling engines, but building engines for others.
The fuel systems and cams are different on a pulling engine because the load put on them is much greater than what is asked of a drag racing engine. While a drag racing engine is designed to generate short bursts of power, pulling engines need greater torque to generate the power to tug sleds that could weigh up to 65,000 pounds.
This type of experience is hard to match. It literally is a lifetime’s worth, and Knox knows that helps his supercharged Hemi engine-making and parts business to be unique.
“I’m kind of the only one that specializes in this area,” he said.
Expanding Into Fabrication
Fabrication, however, wasn’t a specialized area for Sassy Engines. It was primarily doing what fabrication it needed by hand and relying on a local machine shop to handle more of the custom work. That put them at the mercy of the machine shop, which made project scheduling a bit more difficult.
“One of the problems that we have had in the last four or five years is getting stuff like brackets and other little parts made when we need them,” Knox said. “I could design it, but when the machine shop got the order, it might take two to three weeks or even a month to get it done.”
With a spike in engine-making and parts building, the manual approach to fabrication was taking entirely too long as well.
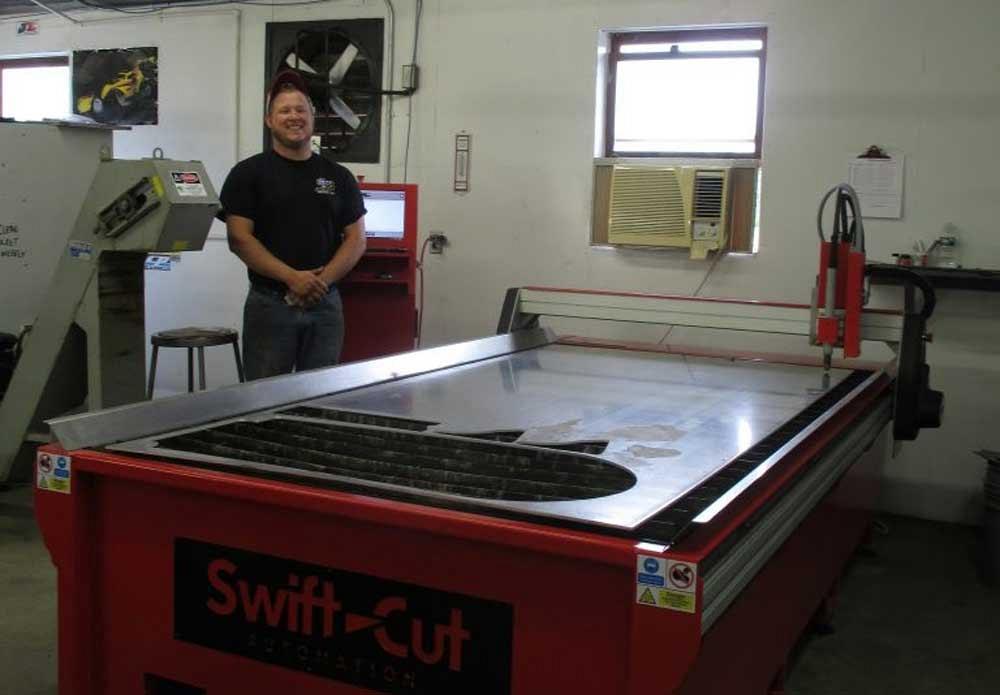
Figure 3
Joe Bosworth, who had no real previous experience with CNC equipment, was running jobs on the Swift-Cut plasma cutting machine after just a week.
That led Knox and his business partner John Card, who also is vice president of operations and a drag racer on the side, to purchase a plasma cutting table. They installed a Swift-Cut Pro Plasma 48 table in early 2017 (see Figure 3).
Joe Bosworth, another self-described “car guy,” is the point man on the plasma cutting table. His only “fabricating” experience was manually working with manual tools, such as a hand lathe, and the shop’s Bridgeport mill. He had no experience working with a CNC machine tool before his introduction to the equipment’s PC-based controller.
“That was a big leap for me not having done this before,” Bosworth said. “I had to transfer what I knew I needed to do into the computer and design it the right way. Then I had to learn to tidy the drawings up.”
Within a week, Bosworth said he was comfortable running the table and setting up jobs that were set up with the help of the Swift-Cut support team. Getting used to putting together clean programs himself took about another month. Since then, production of parts hasn’t been the same.
“It’s a completely different world over here now,” Bosworth said.
Prior to the installation of the plasma cutting table, to produce a part Bosworth had to draw the outline of part on a piece of wood or cardboard, transfer that to a piece of aluminum (which most of the parts are made of), and manually cut out the outline. A 36- by 44-in. engine plate made of 0.375-in. aluminum would take 12 to 14 hours to draw, cut, and then mill. With the help of the Swift-Cut table, that same part takes no more than four hours, according to Bosworth. The real time savings comes from the plasma cutting capability.
“Now in 20 minutes it’s roughed out on the plasma table,” Bosworth said. “I just throw it on the Bridgeport to clean up all of the holes and to get nice milled edges.”
It’s also changed the nature of the shop’s production and parts inventory business. Bosworth said they can produce parts when needed and actually build multiple parts to help fill something like an anodizing order or to replenish parts that have been sent out to fulfill customer orders. There’s no more waiting. They control their own manufacturing destiny , especially after acquiring a Haas CNC lathe and a Fadal 3-axis mill.
So now Knox and the Sassy Engines team are running a full-blown manufacturing operation, even sometimes doing work for customers outside the pulling world, such as cutting plate to repair a tractor bucket. Sassy Engines is more than pulling its weight as a small business.
Nowadays Knox attends pulling events with other teams. He gets to be near the action, but he doesn’t have to be wed to it. He’s slowing down in his own way.
“I joke around with people that I work only half-days now,” he said. “I work 12 hours a day.”Sassy Engines Inc., www.sassyracingengines.com
Swift-Cut Automation USA Inc., www.swift-cut.us
About the Author
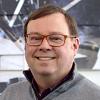
Dan Davis
2135 Point Blvd.
Elgin, IL 60123
815-227-8281
Dan Davis is editor-in-chief of The Fabricator, the industry's most widely circulated metal fabricating magazine, and its sister publications, The Tube & Pipe Journal and The Welder. He has been with the publications since April 2002.
subscribe now
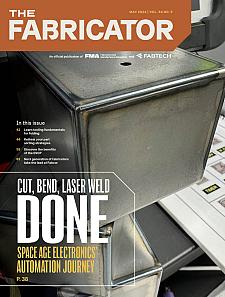
The Fabricator is North America's leading magazine for the metal forming and fabricating industry. The magazine delivers the news, technical articles, and case histories that enable fabricators to do their jobs more efficiently. The Fabricator has served the industry since 1970.
start your free subscription- Stay connected from anywhere
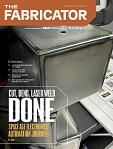
Easily access valuable industry resources now with full access to the digital edition of The Fabricator.
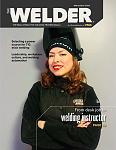
Easily access valuable industry resources now with full access to the digital edition of The Welder.
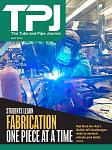
Easily access valuable industry resources now with full access to the digital edition of The Tube and Pipe Journal.
- Podcasting
- Podcast:
- The Fabricator Podcast
- Published:
- 04/16/2024
- Running Time:
- 63:29
In this episode of The Fabricator Podcast, Caleb Chamberlain, co-founder and CEO of OSH Cut, discusses his company’s...
- Trending Articles
Tips for creating sheet metal tubes with perforations
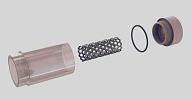
JM Steel triples capacity for solar energy projects at Pennsylvania facility
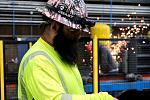
Are two heads better than one in fiber laser cutting?
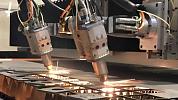
Supporting the metal fabricating industry through FMA
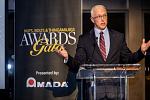
Omco Solar opens second Alabama manufacturing facility
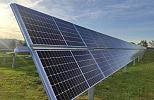
- Industry Events
16th Annual Safety Conference
- April 30 - May 1, 2024
- Elgin,
Pipe and Tube Conference
- May 21 - 22, 2024
- Omaha, NE
World-Class Roll Forming Workshop
- June 5 - 6, 2024
- Louisville, KY
Advanced Laser Application Workshop
- June 25 - 27, 2024
- Novi, MI