Senior Editor
- FMA
- The Fabricator
- FABTECH
- Canadian Metalworking
Categories
- Additive Manufacturing
- Aluminum Welding
- Arc Welding
- Assembly and Joining
- Automation and Robotics
- Bending and Forming
- Consumables
- Cutting and Weld Prep
- Electric Vehicles
- En Español
- Finishing
- Hydroforming
- Laser Cutting
- Laser Welding
- Machining
- Manufacturing Software
- Materials Handling
- Metals/Materials
- Oxyfuel Cutting
- Plasma Cutting
- Power Tools
- Punching and Other Holemaking
- Roll Forming
- Safety
- Sawing
- Shearing
- Shop Management
- Testing and Measuring
- Tube and Pipe Fabrication
- Tube and Pipe Production
- Waterjet Cutting
Industry Directory
Webcasts
Podcasts
FAB 40
Advertise
Subscribe
Account Login
Search
Spreading knowledge in metal fabrication for 50 years
Real, actionable knowledge sews the fabric of a healthy fab shop
- By Tim Heston
- January 20, 2020
- Article
- Shop Management
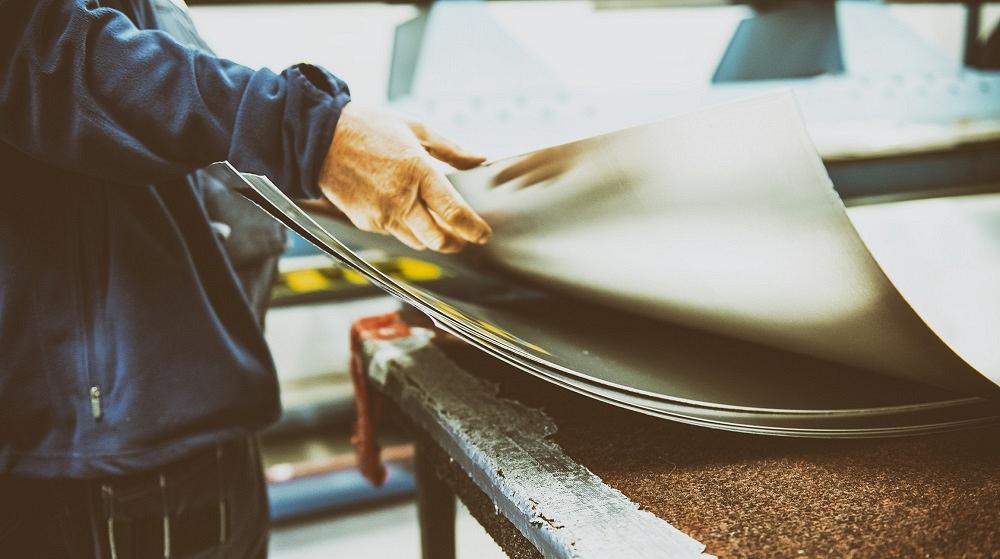
So much has changed in the metal fabrication and manufacturing industries since The FABRICATOR magazine launched 50 years ago, but one thing hasn’t: the need for real, actionable knowledge. Getty Images
When The FABRICATOR launched in January 1970, industry veterans at the time grew up in the pre-NC era, when a punch press operator had to turn hand cranks to move the sheet and initiate the punching cycle. Every hole and every part profile required complete and total operator intervention. Those were the days.
Today’s industry veterans never left home without their slide rules, and they knew their trigonometry. They used it to generate layouts of complex arcs, and typed the corresponding code into a Flexowriter, which generated the tape. Someone then would feed that tape into the punching machine, which would loop it continuously to run the program. The “controller” had no computer memory whatsoever. Those were the days.
Those entering the business today—people exposed mostly to touchscreens and 3D simulations—might hear this story and ask, “Code? What code?” When experienced technical gurus hear that, their ears perk up and the storytelling begins. Those remember-when stories, rooted in deep process knowledge, help define the metal fabrication business. They sew the fabric of fab shop culture.
It’s a culture built on solving concrete problems. Nothing’s ambiguous. The job is right in front of you. It either meets quality standards and ships on time, or it doesn’t. Case closed.
OK, the case isn’t closed. In fact, the case is rarely that simple, hence all The FABRICATOR’s articles on communication and management practices over the years. Regardless, people in metal fabrication tend to abhor buzzwords and, for that matter, any kind of sugarcoating in general. They tell it like it is.
This business is about getting sheet metal and plate from the raw stock to the shipping dock, adding value to it along the way. There’s nothing magical about it, and in many ways it keeps fabricators brutally honest. The technological cornucopia keeps growing with smarter software, more powerful lasers, more flexible and productive press brakes, and smarter welding systems.
Sure, a laser or punch program that produces greater material yield can have a financial impact. But in general, if a shop invests millions in equipment and the order-to-ship time doesn’t change—that is, if the job doesn’t move faster from raw stock to the shipping dock—cash flow stays much the same, customers don’t notice anything different, and nothing significant really changes.
This isn’t to say machines and software haven’t had profound effects. Most shops today can claim that they employ fewer people but produce more than ever. Technology adoption has reached new levels, and the reasons for it are pretty clear.
“Over the next decade, 3.5 million jobs are going to be needed, and 2 million are expected to go unfilled due to the skills gap.”
So said Matt Heerey, division president of the manufacturing division of ECI Software Solutions, presenting at the FABTECH conference in Chicago in November, during which he presented findings of a recent survey the company conducted. Almost 90% of the survey’s respondents said that they had increased technology spending over the past 12 to 18 months, and more than two-thirds said they made operational changes over the same period. Why? The labor shortage is part of it, but so is the generational shift.
The youngest shop owners today—many in their 30s, some even in their 20s—grew up in the internet age. And there’s excitement brewing among them as the industry moves from manual and automated operation to autonomous production, where artificial intelligence and machine learning boost productivity in the face of a severe labor shortage.
But there’s also growing unease that goes back to that technical guru telling stories of days gone by. To become gurus, they acquired knowledge—not fluff or BS (the world has enough)—but real, actionable knowledge. (My apologies for the corporate buzzword.)
Gurus became gurus because they knew trigonometry for manual layout and bend calculations. They knew the idiosyncrasies of cutting and punching, enough to realize that, for reliable operation, a microtab of this width and that geometry should go in that spot. Process-specific knowledge made their careers, and their curiosity made them who they are.
Ignorance is OK as long as it’s temporary and accompanied by curiosity. The ignorant who aren’t curious stay ignorant and, worst of all, apathetic. Problem is, the labor shortage is so acute, the apathetic ignorant can stay on at a shop, push buttons, and produce parts, with no knowledge, engagement, or skin in the game. The situation spreads the kind of apathy that tugs at the very fabric of fab shop culture.
But not all is lost. Consider one of my favorite letters printed in The FABRICATOR several years ago. It came from a onetime inmate. He read the magazine religiously and even cut out Steve Benson’s Bending Basics column every month and put them in a binder by his machine.
The actionable information in that column, combined with a healthy dose of curiosity and initiative, turned that onetime inmate into the shop’s top press brake operator, able to operate any machine brand no matter its age. When he sent his letter to us, he was applying for a press brake supervisor position. Real knowledge helped turn his life around.
Spreading knowledge in a way that spurs the curious to action is at the heart of a healthy fab shop. It’s why the Fabricators & Manufacturers Association decided to launch The FABRICATOR magazine 50 years ago this month. The industry’s longtime leaders and best technical gurus spread knowledge every day, and we at The FABRICATOR will continue to listen, learn, and spread the word.
About the Author
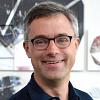
Tim Heston
2135 Point Blvd
Elgin, IL 60123
815-381-1314
Tim Heston, The Fabricator's senior editor, has covered the metal fabrication industry since 1998, starting his career at the American Welding Society's Welding Journal. Since then he has covered the full range of metal fabrication processes, from stamping, bending, and cutting to grinding and polishing. He joined The Fabricator's staff in October 2007.
subscribe now
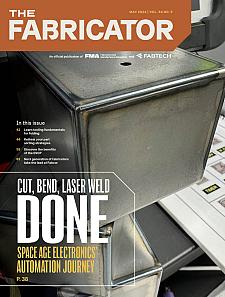
The Fabricator is North America's leading magazine for the metal forming and fabricating industry. The magazine delivers the news, technical articles, and case histories that enable fabricators to do their jobs more efficiently. The Fabricator has served the industry since 1970.
start your free subscription- Stay connected from anywhere
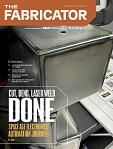
Easily access valuable industry resources now with full access to the digital edition of The Fabricator.
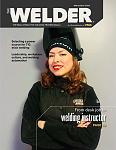
Easily access valuable industry resources now with full access to the digital edition of The Welder.
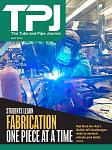
Easily access valuable industry resources now with full access to the digital edition of The Tube and Pipe Journal.
- Podcasting
- Podcast:
- The Fabricator Podcast
- Published:
- 04/16/2024
- Running Time:
- 63:29
In this episode of The Fabricator Podcast, Caleb Chamberlain, co-founder and CEO of OSH Cut, discusses his company’s...
- Trending Articles
Tips for creating sheet metal tubes with perforations
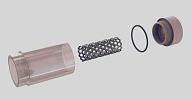
Supporting the metal fabricating industry through FMA
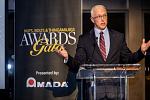
JM Steel triples capacity for solar energy projects at Pennsylvania facility
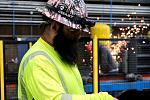
Are two heads better than one in fiber laser cutting?
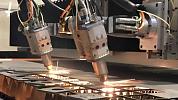
Fabricating favorite childhood memories
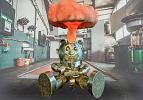
- Industry Events
16th Annual Safety Conference
- April 30 - May 1, 2024
- Elgin,
Pipe and Tube Conference
- May 21 - 22, 2024
- Omaha, NE
World-Class Roll Forming Workshop
- June 5 - 6, 2024
- Louisville, KY
Advanced Laser Application Workshop
- June 25 - 27, 2024
- Novi, MI