Senior Editor
- FMA
- The Fabricator
- FABTECH
- Canadian Metalworking
Categories
- Additive Manufacturing
- Aluminum Welding
- Arc Welding
- Assembly and Joining
- Automation and Robotics
- Bending and Forming
- Consumables
- Cutting and Weld Prep
- Electric Vehicles
- En Español
- Finishing
- Hydroforming
- Laser Cutting
- Laser Welding
- Machining
- Manufacturing Software
- Materials Handling
- Metals/Materials
- Oxyfuel Cutting
- Plasma Cutting
- Power Tools
- Punching and Other Holemaking
- Roll Forming
- Safety
- Sawing
- Shearing
- Shop Management
- Testing and Measuring
- Tube and Pipe Fabrication
- Tube and Pipe Production
- Waterjet Cutting
Industry Directory
Webcasts
Podcasts
FAB 40
Advertise
Subscribe
Account Login
Search
Teaching English on the metal fabrication shop floor
The story of a fabricator in the melting pot of …. Nebraska?
- By Tim Heston
- December 6, 2018
- Article
- Shop Management
Carrie Knapp recalled seeing one of her English-as-a-second-language students show her the press brake he was operating at TMCO Inc., a custom fabricator in Lincoln, Neb.
“I like students to show me their work, and he was bending pieces of metal that I thought couldn’t be bent,” Knapp said. “I was just dumbfounded. Still, I grew up on a farm, and my dad was very mechanically adept, has done welding, and so I had a lot of the background vocabulary already. So I could draw on that to help my students get the English words.”
Her student was a refugee from Burma (now Myanmar) in Southeast Asia, one of many refugees working at the fabricator. She worked one-on-one with him, using flashcards of common tools, like calipers, micrometers, squares, and hammers, and how to communicate basic units of measurement.
TMCO’s story shows that talent can come from anywhere; one just has to recognize it and tap it. Consider the story of Anwar Rida, who grew up in Iraq, Iran, and Syria (where he went to law school). When he arrived at TMCO he took a job running punch presses. Six years later he became manager of the entire fabrication department. By 2012 he was project manager, and in 2016 he became company president.
That’s not a bad career path, and it exemplifies a culture of opportunity at TMCO Inc. set in motion by longtime CEO Roland Temme, who began hiring refugees decades ago. The company’s first refugee, from Burma (not yet Myanmar), recently retired from the company after 30 years of service.
TMCO doesn’t hire refugees just to get a warm body to push buttons in front of a machine. As Rida told me earlier this year, “Your qualifications to do the work are what determines whether we hire you or not.”
Knapp’s anecdotes are proof of that. She was one of TMCO’s English teachers the fabricator hired on a contract basis through a local group called Lincoln Literacy. Working with employees one-on-one and in a group setting, she’s seen helpers and material handlers become machine operators and department supervisors.
The fabricator offers English-language training free to its employees. Most significant, this training (which isn’t mandatory) occurs not after hours, but during the workday. In all practicality, employees get paid to learn English.
Knapp has since moved on to another job. Today Lincoln Literacy’s Rik Minnick is coordinating the language program with TMCO and teaching some beginning-level classes. Reading is part of the curriculum, but focusing solely on reading can lead to problems. People can read English and not entirely grasp what they’re reading. So instead, “we really focus on interpretation. Overall, we try to take an approach that involves all facets of language,” Minnick said, “including understanding, speaking, reading, and writing.”
All this investment in employee education goes against the stereotype when it comes to immigrant employment. The popular perception is that companies hire immigrants to take on work that people born in the U.S. wouldn’t want, be it because of low pay, harsh working conditions, or both. That argument doesn’t sit well for many, of course. In an ideal world, no job should be so bad or pay so little that only someone with no viable alternative is willing to take it.
Most progressive fabricators require more than just warm bodies to push buttons. Granted, many specific jobs probably aren’t that fulfilling for most. Few probably want to spend a lifetime moving material, shaking parts out of sheets, heaving sheet metal skeletons into scrap bins. But at most fabrication operations, especially the small ones, people don’t spend their entire day on one mundane task. A person may need to heave a sheet metal skeleton into a scrap bin, but that same person may review a nest and manage a sophisticated laser cutting machine.
TMCO’s immigrant employees are refugees from the surrounding Lincoln community, an area that for the past few decades has quietly become one of the most vibrant refugee communities in the U.S. Why, exactly?
“It’s really hard to say,” Knapp said. “We do have a few churches here that help with refugee resettlement. Whenever I’ve asked my language learners about how they like it here, they tell me, ‘I like it because it’s quiet.’ It’s a polite town, a good place for people of all sorts of different colors and backgrounds. We have a little melting pot right here in the middle of the company.”
Knapp recalled working with one of her first TMCO students, also from Burma. Her lessons began like they always had; she started by asking questions, building rapport and trust. His initial responses gave her an idea of his current English-language capability and hinted at his style of learning.
After weeks of talking, the two got to know one another. “I eventually learned that, back in Burma, he had made a radio that was actually water-powered,” assembled together with what was available in his home village. Knapp immediately could see the man had mechanical aptitude and an insatiable curiosity, both of which have opened doors for him in metal fabrication.
The melting pot, both at TMCO and in greater Lincoln, brings with it a certain richness of experience. As the news headlines tell us too often, diversity can bring out the worst in us—including racism, sexism, and the worst kind of hatred and violence—but it can also bring out the best.
After talking with Knapp, I imagined the conversations she and other English teachers at TMCO have had. They’re building relationships with refugees who don’t have “just a job,” but instead are enjoying a real career in metal fabrication. It helps them build a fulfilling, quiet life in the American heartland. If that doesn’t show metal fabrication at its best, I don’t know what does.
Lincoln Literacy, www.lincolnliteracy.org
TMCO Inc., www.tmcoinc.com
About the Author
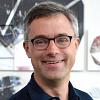
Tim Heston
2135 Point Blvd
Elgin, IL 60123
815-381-1314
Tim Heston, The Fabricator's senior editor, has covered the metal fabrication industry since 1998, starting his career at the American Welding Society's Welding Journal. Since then he has covered the full range of metal fabrication processes, from stamping, bending, and cutting to grinding and polishing. He joined The Fabricator's staff in October 2007.
Related Companies
subscribe now
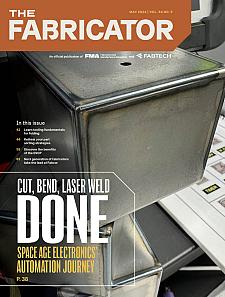
The Fabricator is North America's leading magazine for the metal forming and fabricating industry. The magazine delivers the news, technical articles, and case histories that enable fabricators to do their jobs more efficiently. The Fabricator has served the industry since 1970.
start your free subscription- Stay connected from anywhere
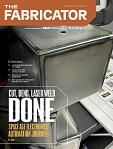
Easily access valuable industry resources now with full access to the digital edition of The Fabricator.
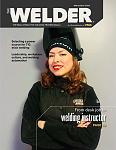
Easily access valuable industry resources now with full access to the digital edition of The Welder.
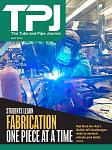
Easily access valuable industry resources now with full access to the digital edition of The Tube and Pipe Journal.
- Podcasting
- Podcast:
- The Fabricator Podcast
- Published:
- 04/16/2024
- Running Time:
- 63:29
In this episode of The Fabricator Podcast, Caleb Chamberlain, co-founder and CEO of OSH Cut, discusses his company’s...
- Trending Articles
Tips for creating sheet metal tubes with perforations
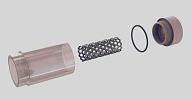
Supporting the metal fabricating industry through FMA
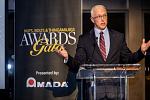
JM Steel triples capacity for solar energy projects at Pennsylvania facility
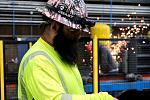
Are two heads better than one in fiber laser cutting?
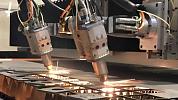
Fabricating favorite childhood memories
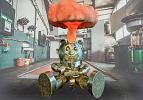
- Industry Events
16th Annual Safety Conference
- April 30 - May 1, 2024
- Elgin,
Pipe and Tube Conference
- May 21 - 22, 2024
- Omaha, NE
World-Class Roll Forming Workshop
- June 5 - 6, 2024
- Louisville, KY
Advanced Laser Application Workshop
- June 25 - 27, 2024
- Novi, MI