Editor-in-Chief
- FMA
- The Fabricator
- FABTECH
- Canadian Metalworking
Categories
- Additive Manufacturing
- Aluminum Welding
- Arc Welding
- Assembly and Joining
- Automation and Robotics
- Bending and Forming
- Consumables
- Cutting and Weld Prep
- Electric Vehicles
- En Español
- Finishing
- Hydroforming
- Laser Cutting
- Laser Welding
- Machining
- Manufacturing Software
- Materials Handling
- Metals/Materials
- Oxyfuel Cutting
- Plasma Cutting
- Power Tools
- Punching and Other Holemaking
- Roll Forming
- Safety
- Sawing
- Shearing
- Shop Management
- Testing and Measuring
- Tube and Pipe Fabrication
- Tube and Pipe Production
- Waterjet Cutting
Industry Directory
Webcasts
Podcasts
FAB 40
Advertise
Subscribe
Account Login
Search
Technology Spotlight - Knowledge is power when it comes to power tools
The interconnected world helps to keep the fabrication project going
- By Dan Davis
- December 5, 2017
- Article
- Shop Management
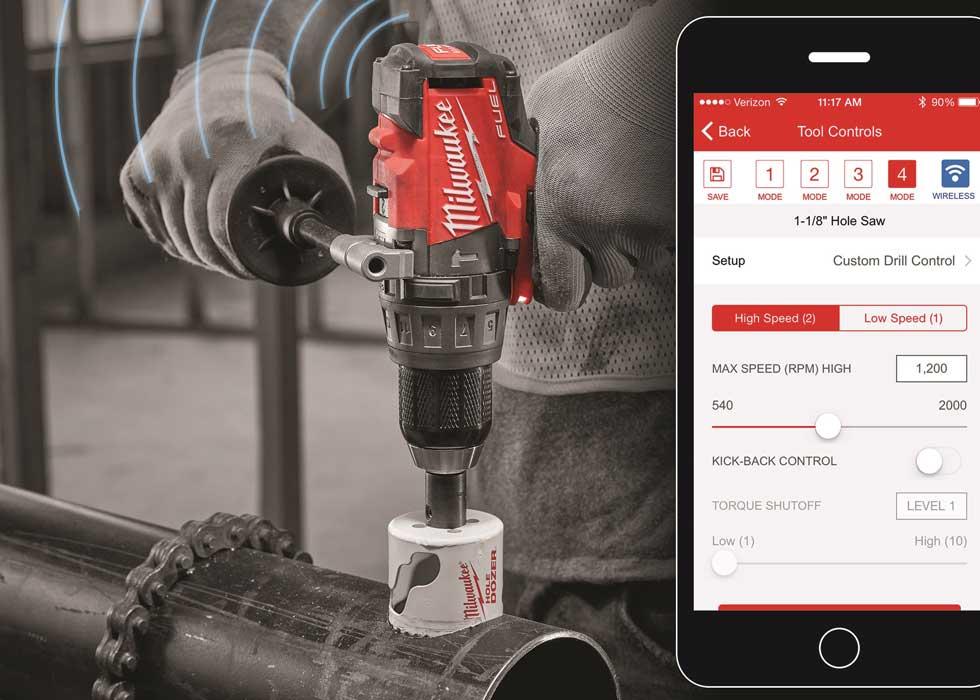
Figure 1
With Wi-Fi connectivity between a Milwaukee Tool control application and a smart power tool, a person can adjust settings on the power tool, even from a remote location.
High-powered fiber laser cutting machines, high-precision press brakes, and robotic welding cells come to mind when a fabricator thinks of cutting-edge machine tools. Power tools are taken for granted, as they sit to the side in a toolroom or a cabinet until they are needed. Fabricators may be missing some real potential for shop floor efficiency, however, if they continue to think of their power tools in the same manner.
Just think about how much has changed for power tools over the last decade. Many folks now work with cordless tools, thanks to a shift from AC to DC power sources. This transition was hastened as battery technology evolved from nickel-cadmium to the longer-lived lithium-ion platform.
As these cordless tools moved to brushless motor technology, fabricators and tradespeople got more power in their hands. Simultaneously, a power tool manufacturer started to realize that because its tools now had electronically controlled motors, it had the potential to add “intelligence” to the tool and communicate with it.
That realization led Milwaukee Tool to develop its ONE-KEY™ digital platform, which debuted in late 2015.
“ONE-KEY is the program that allows users to interact with their tools and manage their tools better,” said Steve Matson, a senior product manager with Milwaukee Tool.
The initial push for the ONE-KEY product centered around its inventory management and configuration capabilities. With the application downloaded on a smartphone, tablet, or computer, an individual can keep tabs on all ONE-KEY-enabled tools. A person can look up a tool’s purchase information, status, performance history, and maintenance schedule. From a configuration standpoint, the user can adjust the tool’s parameters, such as run-time and power, to optimize consumable usage or to ensure consistent tool settings for repetitive jobs done by multiple employees (see Figure 1).
The tool also can be assigned to a person, work site, or vehicle. This action helps to create a digital home for the tool. This is important, Matson said, because the latest generation of cordless tools were very likely to go missing from a work site or a large facility.
“It got to the point where this was commonly heard from our tools’ users so we really had to take a hard look at it,” he said. “When you are a company that is aligned with helping people be more productive, you need to get the tools in their hands. If they don’t have those tools, they can’t be productive.”
Using the same app, tool owners can now track their ONE-KEY-enabled devices on their smartphones, which also act as the main tool in this “Bluetooth, crowd-sourced” tracking effort, Matson said. People’s smartphones, with the ONE-KEY app downloaded, act as beacons on the job site or manufacturing facility. When a phone comes within 100 feet of the smart power tool, it updates the app as to where that tool is located (see Figure 2).
This theoretically could be helpful if a piece of equipment has been stolen. If someone with a ONE-KEY-enabled smartphone is walking around a pawn shop or a swap meet, that person’s phone could connect with the stolen piece of equipment. “That’s an example of the 250,000 users in the system who are all helping to track your stuff down,” Matson said.
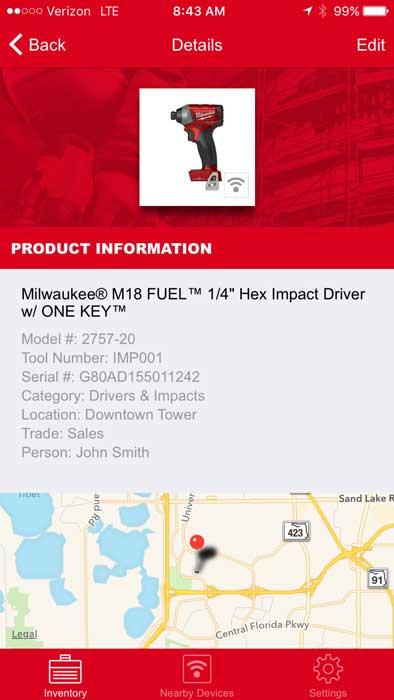
Figure 2
Milwaukee Tool’s ONE-KEY tool-tracking capability lets a power tool owner know where the tool is on a job site or in the manufacturing facility.
If a smart tool goes missing, the user can mark it as missing within the app. The next time that missing tool comes within range of a ONE-KEY-enabled phone, the user is notified about the location of that once-lost tool. The user can even choose to shut down the tool remotely through the app.
“It will be turned into a paperweight,” Matson said.
For equipment such as generators and welding power sources that don’t have the same smart capabilities embedded within them, Milwaukee Tool product developers came up with the TICK™ tool and equipment tracker. The tracker, which can be affixed to equipment with adhesives, plastic ties, or screws, interacts with the ONE-KEY network just like the company’s smart products do (see Figure 3). Just as it does with the smart power tools, the app automatically stores the location of a TICK and the equipment it’s attached to the last time it was within 100 ft. of a ONE-KEY-enabled phone. This location is updated as other phones come in range of the TICK. A user can check the app to pinpoint the last seen date, time, and location.
“The whole idea for all of this is to eliminate the need to have skilled labor look for stuff,” Matson said.
Matson added that this new connectivity between the company and its power tools has gotten people excited. Large contractors and manufacturing companies understand how money can be saved just by keeping track of tools and not losing them. Smaller companies realize they have an instant inventory log of power tools, which is great for insurance or reference purposes, as they are connected to the inventory management system. Businesses of all sizes like the idea that their tools can be modernized with an upgrade that is sent over a Bluetooth connection.
“The stuff that we can do with tracking is really just the beginning of what we can deliver to the user,” Matson said.
“The next logical step is to start analyzing what’s going on with the tool,” he continued. “Is it being used at all? Is it being misused? Does it need service?”
Milwaukee Tool, 800-729-3878, www.milwaukeetool.com
About the Author
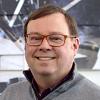
Dan Davis
2135 Point Blvd.
Elgin, IL 60123
815-227-8281
Dan Davis is editor-in-chief of The Fabricator, the industry's most widely circulated metal fabricating magazine, and its sister publications, The Tube & Pipe Journal and The Welder. He has been with the publications since April 2002.
subscribe now
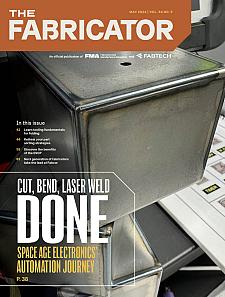
The Fabricator is North America's leading magazine for the metal forming and fabricating industry. The magazine delivers the news, technical articles, and case histories that enable fabricators to do their jobs more efficiently. The Fabricator has served the industry since 1970.
start your free subscription- Stay connected from anywhere
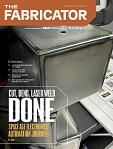
Easily access valuable industry resources now with full access to the digital edition of The Fabricator.
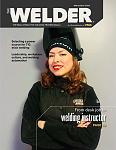
Easily access valuable industry resources now with full access to the digital edition of The Welder.
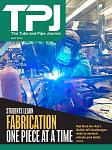
Easily access valuable industry resources now with full access to the digital edition of The Tube and Pipe Journal.
- Podcasting
- Podcast:
- The Fabricator Podcast
- Published:
- 04/16/2024
- Running Time:
- 63:29
In this episode of The Fabricator Podcast, Caleb Chamberlain, co-founder and CEO of OSH Cut, discusses his company’s...
- Industry Events
16th Annual Safety Conference
- April 30 - May 1, 2024
- Elgin,
Pipe and Tube Conference
- May 21 - 22, 2024
- Omaha, NE
World-Class Roll Forming Workshop
- June 5 - 6, 2024
- Louisville, KY
Advanced Laser Application Workshop
- June 25 - 27, 2024
- Novi, MI