- FMA
- The Fabricator
- FABTECH
- Canadian Metalworking
Categories
- Additive Manufacturing
- Aluminum Welding
- Arc Welding
- Assembly and Joining
- Automation and Robotics
- Bending and Forming
- Consumables
- Cutting and Weld Prep
- Electric Vehicles
- En Español
- Finishing
- Hydroforming
- Laser Cutting
- Laser Welding
- Machining
- Manufacturing Software
- Materials Handling
- Metals/Materials
- Oxyfuel Cutting
- Plasma Cutting
- Power Tools
- Punching and Other Holemaking
- Roll Forming
- Safety
- Sawing
- Shearing
- Shop Management
- Testing and Measuring
- Tube and Pipe Fabrication
- Tube and Pipe Production
- Waterjet Cutting
Industry Directory
Webcasts
Podcasts
FAB 40
Advertise
Subscribe
Account Login
Search
TRUMPF celebrates the first anniversary of its Smart Factory
Visitors witness Industry 4.0 in action
- By Eric Lundin
- September 13, 2018
- Article
- Shop Management
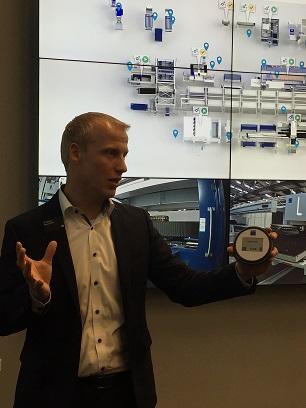
Figure 1. Tobias Reuther, director of TRUMPF’s Smart Factory, Hoffman Estates, Ill., discusses the company’s use of tracking devices, which can be affixed to essentially anything that the user wants to monitor as it makes its way through the shop. The display in the background shows a top view of the machine layout in the Smart Factory; the blue-colored indicators show the locations of the tracking devices.
Nearly a year after machine tool builder TRUMPF opened its showcase facility—dubbed Smart Factory—in the Chicago region, its running smoother than ever and doing more than before, benefiting from tweaks and improvements made since it opened on Sept. 12, 2017. A model of efficiency, the facility uses the principles of Industry 4.0—connectivity and transparency—to power a factory replete with automated material handling and machine tending, making parts with little human interaction.
“We encourage our customers to send drawings of parts, not the parts,” said Tobias Reuther, director of the Smart Factory. The company’s goal is to replicate the typical fabricator experience as faithfully as possible, from start to finish, relying heavily on digital technology; reverse-engineering a part isn’t in line with this goal.
A manufacturing laboratory and proving ground for modern technology, the facility uses automatic guided vehicles to retrieve raw material from storage and central storage towers to hold raw material and to serve as a work-in-process buffer between the cutting, punching, bending, and welding steps that turn flat sheet metal into useful intermediate parts. From March to June of this year, its slowest month was April, when it processed 67 tons of material; its busiest was March, when it processed 101 tons.
The potential of connectivity becomes clear when watching how parts flow through the factory (see Figure 1). Although many of the machines perform a single function, such as cutting, punching, or bending, they work in a seamless fashion, passing work from one to the next.
The transparency available with digital technology is evident when a customer with a computer, tablet, or cellphone logs into this sort of system, from essentially anywhere, to check an order’s status; when company employees log in from anywhere to check an order’s progress and equipment status; and when employees inside building receive alerts, sent directly to the Apple watches they wear, to alert them that a machine is unexpectedly idle and needs attention to resume operating.
Although processing a component through every step of the way, from a part drawing to a box of parts ready to ship, often requires several stages of operator involvement, the company’s TrueLaser Center 7030 is a highlight, showing how a single machine can handle an entire laser-cut part cycle.
“The company started to develop this machine in 2001,” Reuther said. “It was about 10 years on paper and six years of active development.”
The processing starts with the company’s TruTops Boost system, which develops the cutting path and directs the removal, sorting, and dispensing of the cut parts. The machine’s cutting dynamics are unusual in that the laser head’s motions are augmented by sheet motions; rather than slats, the sheet sits on a table of brushes, which prevents the cut parts from tipping or tilting; an ejector cylinder pushes parts out of the skeleton; and those parts are lifted out by a vacuum system that uses an array of small venturi nozzles that can handle nearly any part shape and size, up to 130 lbs. Slugs, scrap pieces, and small parts are directed downward. Slugs and scraps go into a slag bin, while the parts are sorted and directed into eight specific bin locations. Unloading the current sheet and loading the next sheet aren’t separate actions; the two overlap to save time.
The company also uses statistics, machine monitoring, and the knowledge it has on mean-time-to-failure rate for many machine components to analyze machine wear and suggest when to schedule a maintenance activity to replace a part before it breaks and causes an instance of unexpected downtime. No equipment builder can eliminate downtime, but TRUMPF is doing what it can to reduce unexpected downtime.
The facility is also a proving ground for new concepts, some of which relate to manual processes. For example, the company’s Sorting Assistant uses a vision system to monitor the parts on a sheet after they are cut. When part-picking personnel remove a part from the skeleton, the vision system detects it and, as envisioned by TRUMPF engineers, the system will provide instructions that pertain to that part—put into a particular bin headed to another workstation for a subsequent process or put it into another bin for packing and shipping, for example.
Another new wrinkle is the use of a real-time location system, a transmitter and receiver combo that uses small tracking devices that can be affixed to essentially anything—an automated guided vehicle, parts bin, or even a sheet of steel. Made by BeSpoon SAS, it uses an ultrawideband radio system—one that transmits on a frequency that isn’t commonly used by other industrial equipment, so interference is unlikely—to trace the trackers to any location in the building, within about 1 ft. of resolution.
“They can be used to track orders, find a bin’s position, or determine process flow,” Reuther said. In addition to common, day-to-day uses, they also can help management get a clear picture of how the shop handles priority situations.
“Some customers use them to track rush orders,” Reuther said.
Unlike a radio-frequency identification tag, which typically has to go through a gate for detection, these trackers can be detected nearly anywhere in a typical manufacturing environment.
By carefully tracking the times associated with every step needed to complete an order in a traditional, nonconnected, pre-Industry 4.0 shop, TRUMPF and others have found that direct processes—cutting, punching, bending, and welding sheet metal—account for about 20 percent of the time needed to complete an order. Indirect processes, such as order entry, material handling (see Figure 2), and idle time, account for 80 percent.
“Roadblocks include the quoting and order-entry process, which can take up to three days,” Reuther said. Other roadblocks include process chain inconsistency, a lack of integration among all the machines, inefficient in-house logistics, a lack of transparency in order tracking (and individual part tracking), and the inability to optimize production dynamically.
A connected fabrication shop, one set up to minimize handling and maximize processing, is intended to show that technology can reduce the indirect portion of the order completion cycle. In other words, it shows what a fabrication shop can accomplish when it gets rid of the conventional roadblocks.
About the Author
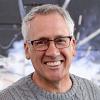
Eric Lundin
2135 Point Blvd
Elgin, IL 60123
815-227-8262
Eric Lundin worked on The Tube & Pipe Journal from 2000 to 2022.
Related Companies
subscribe now
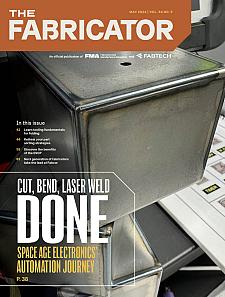
The Fabricator is North America's leading magazine for the metal forming and fabricating industry. The magazine delivers the news, technical articles, and case histories that enable fabricators to do their jobs more efficiently. The Fabricator has served the industry since 1970.
start your free subscription- Stay connected from anywhere
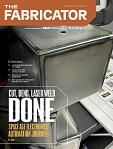
Easily access valuable industry resources now with full access to the digital edition of The Fabricator.
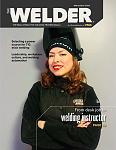
Easily access valuable industry resources now with full access to the digital edition of The Welder.
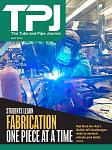
Easily access valuable industry resources now with full access to the digital edition of The Tube and Pipe Journal.
- Podcasting
- Podcast:
- The Fabricator Podcast
- Published:
- 04/16/2024
- Running Time:
- 63:29
In this episode of The Fabricator Podcast, Caleb Chamberlain, co-founder and CEO of OSH Cut, discusses his company’s...
- Trending Articles
Tips for creating sheet metal tubes with perforations
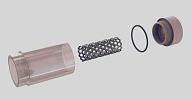
JM Steel triples capacity for solar energy projects at Pennsylvania facility
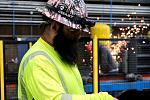
Are two heads better than one in fiber laser cutting?
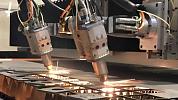
Supporting the metal fabricating industry through FMA
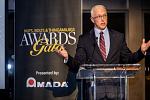
Omco Solar opens second Alabama manufacturing facility
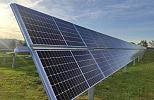
- Industry Events
16th Annual Safety Conference
- April 30 - May 1, 2024
- Elgin,
Pipe and Tube Conference
- May 21 - 22, 2024
- Omaha, NE
World-Class Roll Forming Workshop
- June 5 - 6, 2024
- Louisville, KY
Advanced Laser Application Workshop
- June 25 - 27, 2024
- Novi, MI