Editor
- FMA
- The Fabricator
- FABTECH
- Canadian Metalworking
Categories
- Additive Manufacturing
- Aluminum Welding
- Arc Welding
- Assembly and Joining
- Automation and Robotics
- Bending and Forming
- Consumables
- Cutting and Weld Prep
- Electric Vehicles
- En Español
- Finishing
- Hydroforming
- Laser Cutting
- Laser Welding
- Machining
- Manufacturing Software
- Materials Handling
- Metals/Materials
- Oxyfuel Cutting
- Plasma Cutting
- Power Tools
- Punching and Other Holemaking
- Roll Forming
- Safety
- Sawing
- Shearing
- Shop Management
- Testing and Measuring
- Tube and Pipe Fabrication
- Tube and Pipe Production
- Waterjet Cutting
Industry Directory
Webcasts
Podcasts
FAB 40
Advertise
Subscribe
Account Login
Search
Tube laser positions fabricator for future growth
Michigan-based River City Metals invests in new machinery to open up markets
- By Lincoln Brunner
- March 15, 2024
- Article
- Tube and Pipe Fabrication
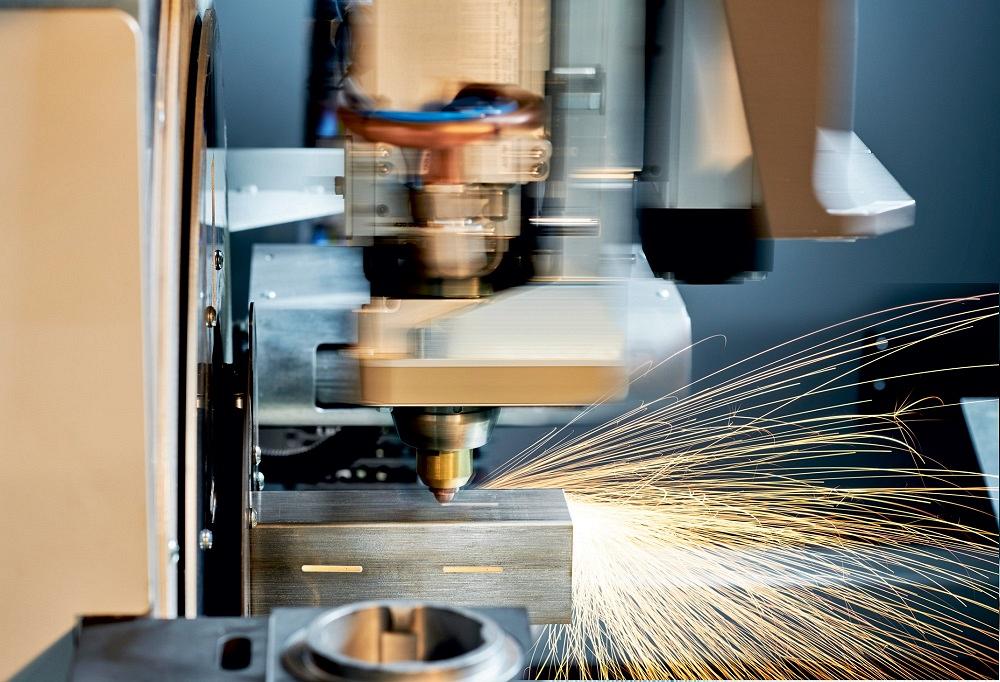
Tube fabrication at River City Metal Products, Grand Rapids, Mich., changed forever after it added a 3-kW Bystronic ByTube Star 130 laser tube cutting system to the shop floor in late 2022. Images: Bystronic
It’s amazing how adding just one machine can make a shop entirely rethink a major facet of its operation.
When River City Metal Products in Grand Rapids, Mich., began looking for a way to decrease the time required to cut tubes for its storage racks, the company knew that it needed something superior to what it was using. It landed on a 3-kW Bystronic ByTube Star 130 laser tube cutting system, which it purchased in September 2022 and installed a few months later.
With a crew of 40 welders working across two shifts, the company has created a growing roster of customers for its signature product: automotive part racks. The ByTube laser’s 28-ft. loading capacity is optimal for River City’s typical raw stock, a huge portion of which is round and square tubes.
The machine can accommodate tubes up to 5 in. OD. River City’s tubing usually runs up to 4 in. OD and ¼ in. thick, but the laser can cut 3/8-in.-thick material on closed profiles, such as round and box tubes, and up to ½-in. material on open profiles like angle iron and channels. River City uses nitrogen as the assist gas for thinner materials and oxygen for thicker ones, Operations Manager Daniel Rietema noted.
Simplify to Speed Up
Before the laser tube cutter arrived, River City used three band saws to make initial cuts on the tubes and then cut holes with a flat laser, a plasma cutter, or a drill. But now, because the new laser has a chuck that can rotate the tube 360 degrees underneath the cutting head, the unit relieves operators from having to handle workpieces that they once needed to move from machine to machine while maintaining tolerances throughout part runs.
“It’s replaced sometimes two or three steps in processing with just one, where we just go from the raw tube immediately to the finished part,” Rietema said. “It’s definitely helped our quality control because [of] having one less step in there. You don’t have to worry about stops on your drill press maybe sliding a little bit.”
That was the main idea from the outset of the company’s decision to purchase the laser tube cutting system—to achieve the productivity of two machines (a band saw and a drill) with just one while improving quality. That enables operators to focus on other tasks and also reduces or eliminates the need for secondary operations.
“In addition to this productivity, their idea was also to increase the quality per part because every time you saw-cut, there is always some burr you need to clean off,” said Gabriele Rebessi, Bystronic’s tube laser product manager. “On the laser, that is no longer required.”
Rietema noted that the laser replaced one of the band saws that the company was using and that it also added speed and a host of capabilities that the company simply didn’t have before, including the software controls that run it. In fact, installing the laser changed the way the company thinks about its capacity.
“The racks can vary quite a bit in complexity, but generally the relationship between how much tubing should be cut and how much time they will take to weld seems to stay pretty constant,” Rietema said. “So, when we would start to get business, it wasn’t too hard to add some more hours to welding. We have 40 welders, some of whom love working a lot of overtime. But in the saw department, we only [had] three large band saws, and we’re running two shifts, so it was hard to add any more capacity.
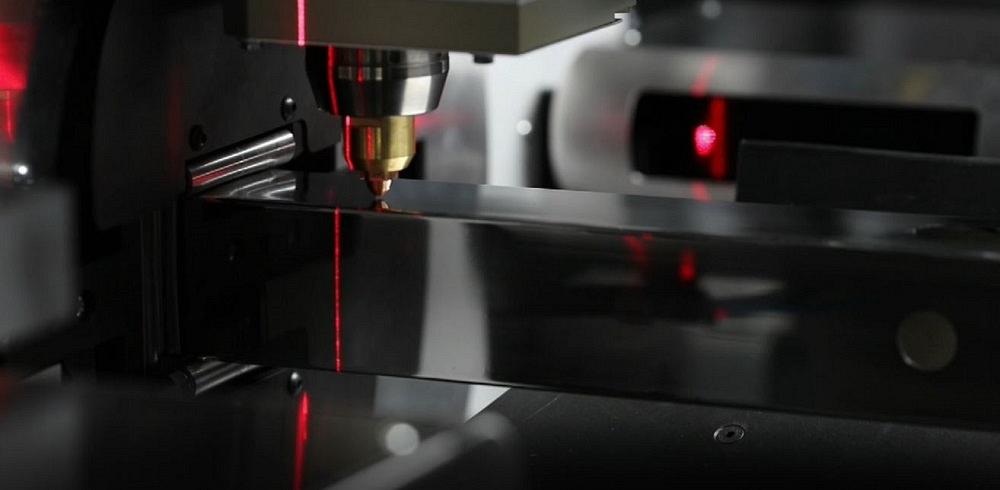
River City’s new laser tube cutting system has a laser scanning feature that detects twists in the tube’s OD, so that the machine can take that into account when cutting.
“But with … the two band saws and the laser, we actually have extra capacity,” he said. “So, [we’ll] start bidding some other projects, a little bit of contract work. We haven’t done a lot of that yet, but just not … being worried about being able to cut enough tubes in order to get something done in time has really been a big help for me in terms of scheduling.”
The results for River City, at times, have been noteworthy.
Before it acquired the laser, the company got an order for 300 racks from one customer, which subsequently ordered 800 more of the same rack in the second quarter of 2023. River City was able to fabricate and assemble the 800 in the same amount of time that it did the original 300.
While not every part that River City makes has seen a productivity leap of that magnitude, Rietema estimates that on many of the company’s parts, it has reduced its tube cutting time by 50%.
“It’s just really, really fast,” Rietema said. “For most thicknesses of tube, even on straight cuts, it’s significantly faster than our large bundle-cutting band saw on a per-piece basis.”
Changing cutting technologies was partly responsible for that increase in speed, but so was the way that the unit handles the tubing itself.
With an automatic loading system that Bystronic calls a Bundle Loader, the laser can store up to 9,900 lbs. of tubing and then automatically load it tube by tube into the chuck with no operator assistance. With this system, the laser keeps the process time for loading each tube to about 18 seconds.
“The preparation is in hidden time, so when the machine is processing one tube, it’s already preparing the next one,” Rebessi said. “The loading process is done while the machine is cutting.”
Quality Patrol
Of course, for River City, speed was one thing; achieving quality cuts was another. The company has found both have increased with the laser, especially its ability to compensate for less-than-perfect raw material. That’s the purview of the unit’s Laserscan feature, which detects twists in the OD that make a square tube not quite square, for example, and uses servomotors to adjust the piece under the cutting head.
Rebessi pointed out that the manipulators that load tubes from the bundle loader to the center of the axis also keep tubes straight all through the cutting process. Supports within the machine move up or down to hold tubes steady and avoid vibration, minimizing both mistakes and mechanical stress in the machine itself.
“The servos themselves are accurate enough that, really, the only kind of variable is what the actual size of the tube is and the squareness of it,” Rietema said. “It has some features that are able to compensate if a tube is rolled slightly off square. It scans the tube as it goes so they can see when it’s shifted off square.
“Primarily what we do with it is [locate] through-holes for bolts. It’s always important to me to make sure that the holes on one side line up with the holes on the other. If a tube is kind of rolled in more of a trapezoid shape, it will automatically move the two holes to align with each other.”
Frank Arteaga, regional director of marketing for Bystronic, noted that the unit’s laser scanning ability can help users maintain accuracy from one cutting side to the other, especially on materials like rectangular tubing. In addition, the available weld seam camera and multiple supports for the workpieces throughout the machine can help maintain quality even when no one is around to check.
“All the supports … help with the accuracy, as well,” Arteaga said. “When you have a 28-ft.-long tube, every little motion that you make on any side of the tube affects the cutting side, so you have to support it really well in order to maintain those accuracies.”
Widening the Net
In addition to the time savings that the laser affords River City, Rietema again alluded to the unexpected avenues that the machine has opened up as perhaps the chief yield of the investment.
“I think the No. 1 thing is it’s given me the option to quote more jobs that I would’ve stayed away from in the past that just had a lot of holes in them,” Rietema said. “There’s just not a really fast way to put a lot of holes into a steel tube, especially at the kind of volume that we’re doing.”
The machine’s software allows the company to modify parts, such as adding connections between them, which helps to reduce the required time to assemble and weld the rack. Not only has it simplified the daily work of welders, but it also has increased production efficiency because it takes less time to place the material correctly on the welding table.
Rietema added that the software also helps with estimating jobs. While it’s difficult to look at a new product and accurately estimate the cost to produce it as compared to one of the company’s current products, the system’s software is designed to determine how long each component of a given product will take to cut.
“When I’m doing a job, if I’m unsure about how long I think it will take to process all the parts, I take my models of the different parts that are in there, plug them into the tube laser software, and it will spit out a really accurate number—this is how long it will take to cut these parts on the laser, then adding in a little factor for downtime and moving bundles around,” Rietema said. “That’s the No. 1 thing: It has given me more confidence with complex assemblies to know exactly how long the tube processing is going to take [and be] confident in my quote.”
About the Author
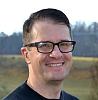
Lincoln Brunner
2135 Point Blvd.
Elgin, IL 60123
(815)-227-8243
Lincoln Brunner is editor of The Tube & Pipe Journal. This is his second stint at TPJ, where he served as an editor for two years before helping launch thefabricator.com as FMA's first web content manager. After that very rewarding experience, he worked for 17 years as an international journalist and communications director in the nonprofit sector. He is a published author and has written extensively about all facets of the metal fabrication industry.
Related Companies
subscribe now
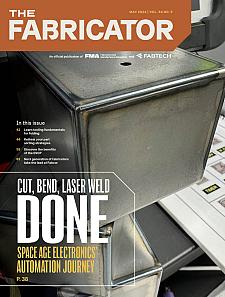
The Fabricator is North America's leading magazine for the metal forming and fabricating industry. The magazine delivers the news, technical articles, and case histories that enable fabricators to do their jobs more efficiently. The Fabricator has served the industry since 1970.
start your free subscription- Stay connected from anywhere
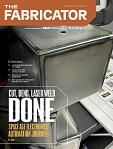
Easily access valuable industry resources now with full access to the digital edition of The Fabricator.
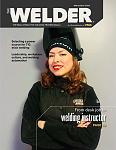
Easily access valuable industry resources now with full access to the digital edition of The Welder.
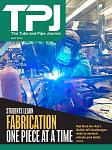
Easily access valuable industry resources now with full access to the digital edition of The Tube and Pipe Journal.
- Podcasting
- Podcast:
- The Fabricator Podcast
- Published:
- 04/16/2024
- Running Time:
- 63:29
In this episode of The Fabricator Podcast, Caleb Chamberlain, co-founder and CEO of OSH Cut, discusses his company’s...
- Trending Articles
Tips for creating sheet metal tubes with perforations
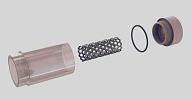
Are two heads better than one in fiber laser cutting?
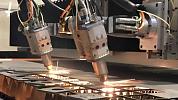
Supporting the metal fabricating industry through FMA
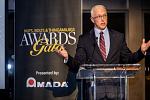
JM Steel triples capacity for solar energy projects at Pennsylvania facility
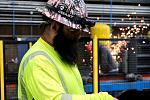
Omco Solar opens second Alabama manufacturing facility
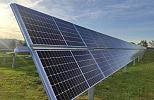
- Industry Events
16th Annual Safety Conference
- April 30 - May 1, 2024
- Elgin,
Pipe and Tube Conference
- May 21 - 22, 2024
- Omaha, NE
World-Class Roll Forming Workshop
- June 5 - 6, 2024
- Louisville, KY
Advanced Laser Application Workshop
- June 25 - 27, 2024
- Novi, MI