Editor-in-Chief
- FMA
- The Fabricator
- FABTECH
- Canadian Metalworking
Categories
- Additive Manufacturing
- Aluminum Welding
- Arc Welding
- Assembly and Joining
- Automation and Robotics
- Bending and Forming
- Consumables
- Cutting and Weld Prep
- Electric Vehicles
- En Español
- Finishing
- Hydroforming
- Laser Cutting
- Laser Welding
- Machining
- Manufacturing Software
- Materials Handling
- Metals/Materials
- Oxyfuel Cutting
- Plasma Cutting
- Power Tools
- Punching and Other Holemaking
- Roll Forming
- Safety
- Sawing
- Shearing
- Shop Management
- Testing and Measuring
- Tube and Pipe Fabrication
- Tube and Pipe Production
- Waterjet Cutting
Industry Directory
Webcasts
Podcasts
FAB 40
Advertise
Subscribe
Account Login
Search
Blue collar skills, white collar thinking
If welders want to boost their wages, they'll need to climb their own version of the corporate ladder
- By Dan Davis
- December 19, 2022
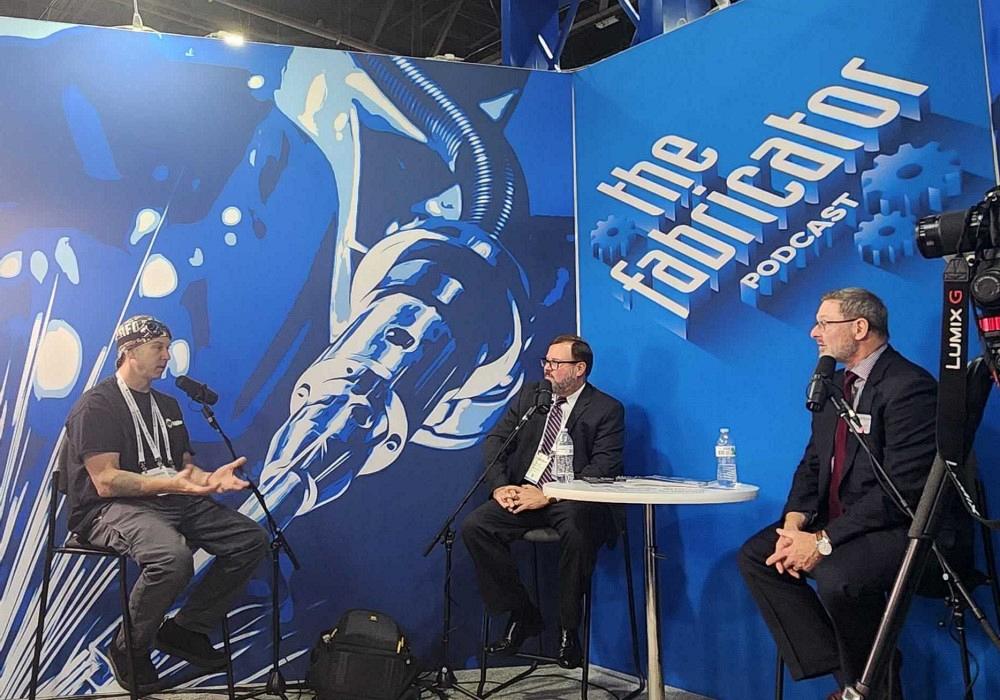
Michael Brandt of Garage Bound in Chattanooga, Tenn., talks with The Fabricator Podcast hosts Dan Davis and Jim Gorzek.
“Sometimes you have to be ready to go somewhere else.”
That’s what Sean Flottmann, who you might know as “Dabswellington” if you are one of his almost 50,000 followers on Instagram, recommended for welders who are not satisfied with their work situation or wages. Flottmann made the comment during a recording of The Fabricator Podcast at FABTECH in Atlanta in early November, and it was echoed by other welders we chatted with during the podcast recordings. They all have moved forward in their careers as they try to find out what makes them the happiest—and also happens to pay the bills. Rae Ripple of Big Spring, Texas, found art. Adam Heffner, Springfield, Tenn., started his own fabricating business. Tiffany Noel Orff, Salinas, Calif., entered welding education. All of these welders didn’t start off where they are today; they had to find it.
That’s a difficult thing for a young person to grasp, particularly in today’s world. Today’s high school and college students have grown up with access to the internet in the palm of their hand. They want instantaneous results. Real life can be painfully slow for Generation Z sometimes.
But that’s reality, and it can be vexing. That’s why young welders need to realize that they are in control of their welding career, not the employer. In some cases, if they want to grow their skills and their paychecks, these welders are going to have to hit the road.
Disclaimer: This doesn’t mean burning bridges. Leaving with noble intentions and with relationships intact is a mature and smart act. Just as leaving a job might be necessary to grow, coming back home is always a possibility as well, especially as family members grow older. A one-time employer easily can become a future employer as well.
Flottmann, who works in recruiting for American Welding Academy in Union, Mo., said that he has tried to pick up new skills wherever he’s worked. Even when he knew he wasn’t a good fit for a place, he did his best to make the most of it, learn what he could, and depart for greener pastures.
That type of focus on the future is necessary, and it’s part of frank conversations that parents, teachers, guidance counselors, and employers need to have with students. Without it, young welders have no perspective, and a terrible work experience early in a career can taint their welding passion. Honestly, early experiences on a shop floor can be intimidating and frustrating. These manufacturing rookies don’t have all the skills and likely don’t have any established relationships at their new places of employment. Of course, the welding work is going to be hard enough as well. That $47,010 annual salary or $22.60 hourly wage, the average median pay for a welder in 2021 according to the Bureau of Labor Statistics, might not be enough of an enticement for a young welder to stick around in a situation that’s not the right fit.
That’s where the white collar mindset makes sense. You don’t know of better horizons until you start looking for one.
Disclaimer: A welder should probably have a discussion with his or her employer about future opportunities or growth paths. While it can be difficult for small and medium-sized companies to accommodate growth opportunities for all of their employees because of lack of dynamic growth, sometimes the companies will make accommodations for talented employees. Just ask.
Where does a welder go? Anywhere because welding skills travel. It could be shipbuilding on the Atlantic Coast, agricultural equipment manufacturing in the Midwest, or aerospace manufacturing on the West Coast. Welders are needed everywhere, and recruiters can find a spot for the eager and talented ones.
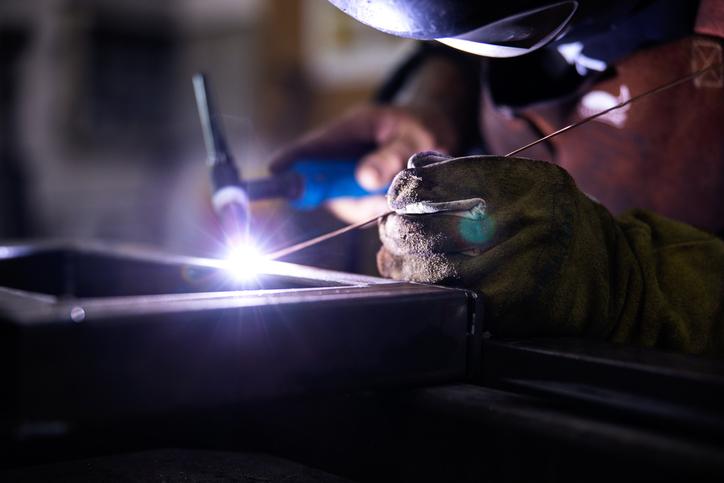
If welders want to maximize their skills development and earnings, they might need to hit the road to find those opportunities. skynesher/E+/Getty Images
Moving to a new location can be difficult, but it might be necessary. Earning and saving money buys options, and more options mean greater freedom. White collar workers figured this out a long time ago, and blue collar workers should recognize the same.
For those metal fabricating companies and owners that live in constant fear of training and possibly losing welders, know that companies that do right by their employees usually don’t worry a lot about losing employees. Open and honest communication can go a long way to keeping welders happy and production humming.
subscribe now
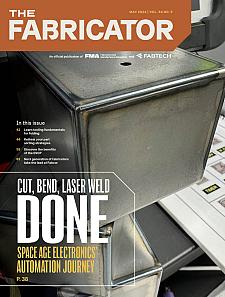
The Fabricator is North America's leading magazine for the metal forming and fabricating industry. The magazine delivers the news, technical articles, and case histories that enable fabricators to do their jobs more efficiently. The Fabricator has served the industry since 1970.
start your free subscriptionAbout the Author
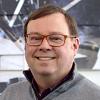
Dan Davis
2135 Point Blvd.
Elgin, IL 60123
815-227-8281
Dan Davis is editor-in-chief of The Fabricator, the industry's most widely circulated metal fabricating magazine, and its sister publications, The Tube & Pipe Journal and The Welder. He has been with the publications since April 2002.
- Stay connected from anywhere
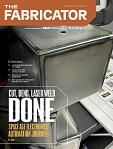
Easily access valuable industry resources now with full access to the digital edition of The Fabricator.
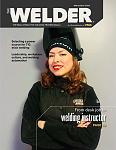
Easily access valuable industry resources now with full access to the digital edition of The Welder.
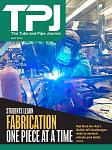
Easily access valuable industry resources now with full access to the digital edition of The Tube and Pipe Journal.
- Podcasting
- Podcast:
- The Fabricator Podcast
- Published:
- 04/16/2024
- Running Time:
- 63:29
In this episode of The Fabricator Podcast, Caleb Chamberlain, co-founder and CEO of OSH Cut, discusses his company’s...
- Trending Articles
Tips for creating sheet metal tubes with perforations
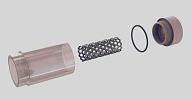
Are two heads better than one in fiber laser cutting?
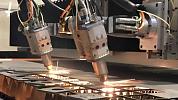
Supporting the metal fabricating industry through FMA
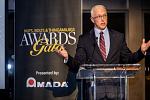
JM Steel triples capacity for solar energy projects at Pennsylvania facility
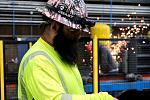
Omco Solar opens second Alabama manufacturing facility
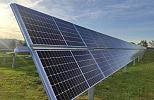
- Industry Events
16th Annual Safety Conference
- April 30 - May 1, 2024
- Elgin,
Pipe and Tube Conference
- May 21 - 22, 2024
- Omaha, NE
World-Class Roll Forming Workshop
- June 5 - 6, 2024
- Louisville, KY
Advanced Laser Application Workshop
- June 25 - 27, 2024
- Novi, MI