Editor-in-Chief
- FMA
- The Fabricator
- FABTECH
- Canadian Metalworking
Categories
- Additive Manufacturing
- Aluminum Welding
- Arc Welding
- Assembly and Joining
- Automation and Robotics
- Bending and Forming
- Consumables
- Cutting and Weld Prep
- Electric Vehicles
- En Español
- Finishing
- Hydroforming
- Laser Cutting
- Laser Welding
- Machining
- Manufacturing Software
- Materials Handling
- Metals/Materials
- Oxyfuel Cutting
- Plasma Cutting
- Power Tools
- Punching and Other Holemaking
- Roll Forming
- Safety
- Sawing
- Shearing
- Shop Management
- Testing and Measuring
- Tube and Pipe Fabrication
- Tube and Pipe Production
- Waterjet Cutting
Industry Directory
Webcasts
Podcasts
FAB 40
Advertise
Subscribe
Account Login
Search
Take steps to become the “employer of choice” in your own community
Follow the footsteps of JWF Industries and get involved
- By Dan Davis
- October 30, 2023
The need for workers to fill open positions within metal fabricating companies is an ongoing saga, and the situation has been exacerbated in recent years with baby boomers retiring and other segments of the economy becoming as desperate for workers as the manufacturing sector.
In fact, a recent study by the Manufacturing Institute, the workforce development and education affiliate of the National Association of Manufacturers, revealed just how important manufacturers thought having an intelligent and resilient workforce was in this modern economy. When study organizers asked those leaders of manufacturing companies this past summer about their top priorities for current investment dollars, nearly 74% of them replied that they viewed building a robust and trained workforce as a key area. That garnered more support than investing in new technology or improving current processes or operations.
“As manufacturers continue to evolve, the nature of work and skills must adapt to meet the needs of the changing industry,” said Chad Moutray, the National Association of Manufacturers’ chief economist and director of the Center for Manufacturing Research.
Some metal fabricating companies are not only recognizing the need for the best and the brightest to help them cope with increased customer demands and incorporating the right automation tools to meet those expectations, but they are also taking steps to attract that talent. JWF Industries President/CEO William Polacek described it as becoming the “employer of choice” in “Formalizing a feeder system for welding talent," the cover story in the November 2023 issue of The Fabricator. JWF Industries and others like it aren’t sitting on the sidelines, complaining about the state of the world and asking for pity. These such companies are taking steps to ensure that students, teachers, guidance counselors, administrators, and parents recognize manufacturing as the home of good, well-paying careers and that their own businesses are the best examples of those manufacturing companies.
Now, JWF Industries’ Polacek was pretty savvy in hiring the former superintendent of the local school district as the company’s workforce development coordinator. Ed Bowser knew a lot of the players in the local community, but he also had a perspective that any other applicant for the job might have been hard pressed to match. Bowser was a former teacher at vocational school, which gave him a great perspective of where he needed to start in terms of building up JWF’s talent pipeline.
“You have to start at the ground level,” Bowser said. “When I was superintendent, I had Bill [Polacek] come and visit sixth graders, and he would do presentations about welding and opportunities at JWF. So you have to start young and engage these students.”
Those presentations didn’t end with the sixth graders. JWF representatives went wherever they could—middle schools, high schools, vocational training institutions, and community colleges—talking about the career options available to the students. They could start out as a welder and move into project management, training, estimating, and leadership roles, to name a few. Bowser said he would even talk to autobody repair classes in the hopes of maybe convincing some students to try out painting at JWF.
Bowser said another key strategy was to get involved with bodies that can help support the mission to promote job opportunities at JWF and elsewhere. That meant communicating with local teachers and instructors and even acting as a trustee for a local community college. It also involved reaching out to the local economic development agency, JARI (Johnstown Area Regional Industries), and having them act as a source to rally other manufacturers to the cause. (Agencies such as JARI also might be helpful in investigating possible workforce development grants that could help fund training initiatives at a manufacturing company.)
“The next big thing is once you get the individuals in, you have to set up the proper training programs,” Bowser said. There’s no point in investing so much time in recruitment if an organization is not prepared to foster the growth of an employee once they join the fold. In some communities, bad word-of-mouth can easily sabotage any sort of outreach efforts very quickly.
For the record, JWF Industries is a large manufacturer compared to most companies in the metal fabricating space. They have the resources to dedicate to these efforts. The lesson, however, is still applicable to businesses of all sizes. If you make something a priority and commit to following through, real change is possible.
Pick up the phone or send an email to the local education institution to talk to an administrator or a teacher. Find out how you can help them. That will create a connection that soon won’t be forgotten.
Reach out to a local trade organization or economic development agency and see if they have meetings involving other manufacturers. There is strength in numbers, and voices calling for change are more likely to be heard if more voices join the effort.
Change doesn’t come by airing a complaint on social media or participating in an industry survey. Metal fabricators can shape their future just by reaching out beyond the shop.
subscribe now
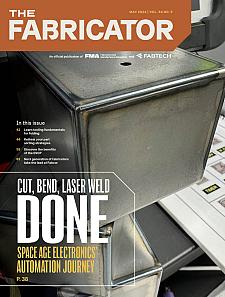
The Fabricator is North America's leading magazine for the metal forming and fabricating industry. The magazine delivers the news, technical articles, and case histories that enable fabricators to do their jobs more efficiently. The Fabricator has served the industry since 1970.
start your free subscriptionAbout the Author
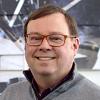
Dan Davis
2135 Point Blvd.
Elgin, IL 60123
815-227-8281
Dan Davis is editor-in-chief of The Fabricator, the industry's most widely circulated metal fabricating magazine, and its sister publications, The Tube & Pipe Journal and The Welder. He has been with the publications since April 2002.
- Stay connected from anywhere
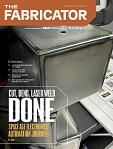
Easily access valuable industry resources now with full access to the digital edition of The Fabricator.
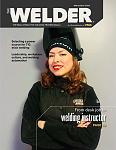
Easily access valuable industry resources now with full access to the digital edition of The Welder.
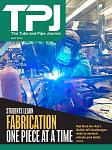
Easily access valuable industry resources now with full access to the digital edition of The Tube and Pipe Journal.
- Podcasting
- Podcast:
- The Fabricator Podcast
- Published:
- 04/16/2024
- Running Time:
- 63:29
In this episode of The Fabricator Podcast, Caleb Chamberlain, co-founder and CEO of OSH Cut, discusses his company’s...
- Industry Events
16th Annual Safety Conference
- April 30 - May 1, 2024
- Elgin,
Pipe and Tube Conference
- May 21 - 22, 2024
- Omaha, NE
World-Class Roll Forming Workshop
- June 5 - 6, 2024
- Louisville, KY
Advanced Laser Application Workshop
- June 25 - 27, 2024
- Novi, MI