Editor-in-Chief
- FMA
- The Fabricator
- FABTECH
- Canadian Metalworking
Categories
- Additive Manufacturing
- Aluminum Welding
- Arc Welding
- Assembly and Joining
- Automation and Robotics
- Bending and Forming
- Consumables
- Cutting and Weld Prep
- Electric Vehicles
- En Español
- Finishing
- Hydroforming
- Laser Cutting
- Laser Welding
- Machining
- Manufacturing Software
- Materials Handling
- Metals/Materials
- Oxyfuel Cutting
- Plasma Cutting
- Power Tools
- Punching and Other Holemaking
- Roll Forming
- Safety
- Sawing
- Shearing
- Shop Management
- Testing and Measuring
- Tube and Pipe Fabrication
- Tube and Pipe Production
- Waterjet Cutting
Industry Directory
Webcasts
Podcasts
FAB 40
Advertise
Subscribe
Account Login
Search
Can cobots help shops make the most of their welding operations?
For those that can’t find qualified welders, collaborative robots might make sense
- By Dan Davis
- March 10, 2021
Much has been made about how manufacturing companies struggle to find qualified skilled labor to fill open positions in their facilities. In fact, in 2018 Deloitte and The Manufacturing Institute estimated that this skills gap could leave about 2.4 million manufacturing jobs unfilled in the ensuing decade.
Even with unemployment reaching 10.2% in July 2020 during the pandemic, manufacturers still complained about their inability to find the right talent. It’s an ongoing headache that many associations, companies, and communities are trying to ease at a grassroots level, but improving the image of manufacturing as an attractive career choice is a long-term project, the results of which might not be evident for years.
So, how have metal fabricators kept up with the business opportunities as the country emerges from the pandemic? Who is filling these jobs? The answer more than likely is a “what” instead of a “who.”
Collaborative robots have made an immediate impact on the welding scene over the past couple of years, and the adoption rate will only increase as people become more familiar with them. They are easy to program and quick to deploy—literally rolling them from one area to another—which makes automation possible even for the smallest of shops. (If you are interested in learning more about collaborative robots and welding, check out this webinar.)
The FABRICATOR wrote about PMI LLC, Bloomer, Wis., and its adoption of collaborative robots for welding. The company had been using the cobots for material handling in a stamping operations, so the potential to use them in a welding application was intriguing.
The company rented two packages from a welding automation integrator, which included a Universal Robots UR10e cobot arm, a connector to the cloud-based internet, a Miller Electric welding power source, a wire feeder, a robotic gas metal arc gun, a modular welding table, and an app and software to control the system. PMI provided the operator, gas, wire, and parts. Because collaborative robots do not require safety fencing like industrial robots do, they take up about the same amount of room as a manual welding cell.
PMI assigned someone from its stamping operation to learn the ropes of the welding automation, and he picked up on it right away. “When you watch them program one of these cobots, it’s move the arm, press a button, move the arm, press a button. You don’t need welding experience to get it working,” said Erik Larson, PMI’s vice president, operations.
After a summer of working with the cobots, Larson said that they improved the quality of welded parts because of their ability to deliver the same welds repeatedly, part after part. The cobots also allowed the shop to move its certified welders to larger and more complex work.
If you are interested in learning more about collaborative robots and how they are changing people’s thinking about welding automation, consider registering for an April 6 webinar by Universal Robots. Stuart “Stu” Shepherd, Universal Robots’ vertical development director for the Americas region, will cover the specifics of what type of welding processes collaborative robots can support, making the case for an investment in this type of automation, and real-world case study examples.
For more information, click here.
subscribe now
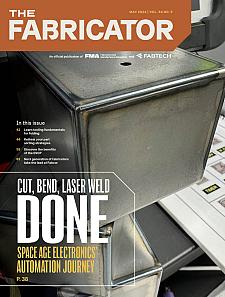
The Fabricator is North America's leading magazine for the metal forming and fabricating industry. The magazine delivers the news, technical articles, and case histories that enable fabricators to do their jobs more efficiently. The Fabricator has served the industry since 1970.
start your free subscriptionAbout the Author
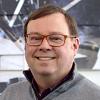
Dan Davis
2135 Point Blvd.
Elgin, IL 60123
815-227-8281
Dan Davis is editor-in-chief of The Fabricator, the industry's most widely circulated metal fabricating magazine, and its sister publications, The Tube & Pipe Journal and The Welder. He has been with the publications since April 2002.
Related Companies
- Stay connected from anywhere
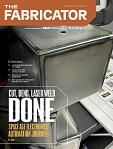
Easily access valuable industry resources now with full access to the digital edition of The Fabricator.
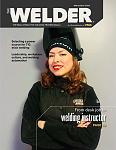
Easily access valuable industry resources now with full access to the digital edition of The Welder.
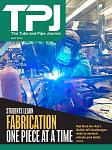
Easily access valuable industry resources now with full access to the digital edition of The Tube and Pipe Journal.
- Podcasting
- Podcast:
- The Fabricator Podcast
- Published:
- 04/16/2024
- Running Time:
- 63:29
In this episode of The Fabricator Podcast, Caleb Chamberlain, co-founder and CEO of OSH Cut, discusses his company’s...
- Trending Articles
Tips for creating sheet metal tubes with perforations
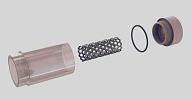
JM Steel triples capacity for solar energy projects at Pennsylvania facility
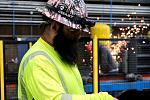
Are two heads better than one in fiber laser cutting?
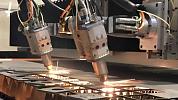
Supporting the metal fabricating industry through FMA
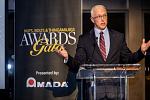
Omco Solar opens second Alabama manufacturing facility
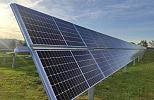
- Industry Events
16th Annual Safety Conference
- April 30 - May 1, 2024
- Elgin,
Pipe and Tube Conference
- May 21 - 22, 2024
- Omaha, NE
World-Class Roll Forming Workshop
- June 5 - 6, 2024
- Louisville, KY
Advanced Laser Application Workshop
- June 25 - 27, 2024
- Novi, MI