Senior Editor
- FMA
- The Fabricator
- FABTECH
- Canadian Metalworking
Categories
- Additive Manufacturing
- Aluminum Welding
- Arc Welding
- Assembly and Joining
- Automation and Robotics
- Bending and Forming
- Consumables
- Cutting and Weld Prep
- Electric Vehicles
- En Español
- Finishing
- Hydroforming
- Laser Cutting
- Laser Welding
- Machining
- Manufacturing Software
- Materials Handling
- Metals/Materials
- Oxyfuel Cutting
- Plasma Cutting
- Power Tools
- Punching and Other Holemaking
- Roll Forming
- Safety
- Sawing
- Shearing
- Shop Management
- Testing and Measuring
- Tube and Pipe Fabrication
- Tube and Pipe Production
- Waterjet Cutting
Industry Directory
Webcasts
Podcasts
FAB 40
Advertise
Subscribe
Account Login
Search
Capturing metal fabrication knowledge at FABTECH
Technology aims to make the most out of available talent for the industry
- By Tim Heston
- October 12, 2023
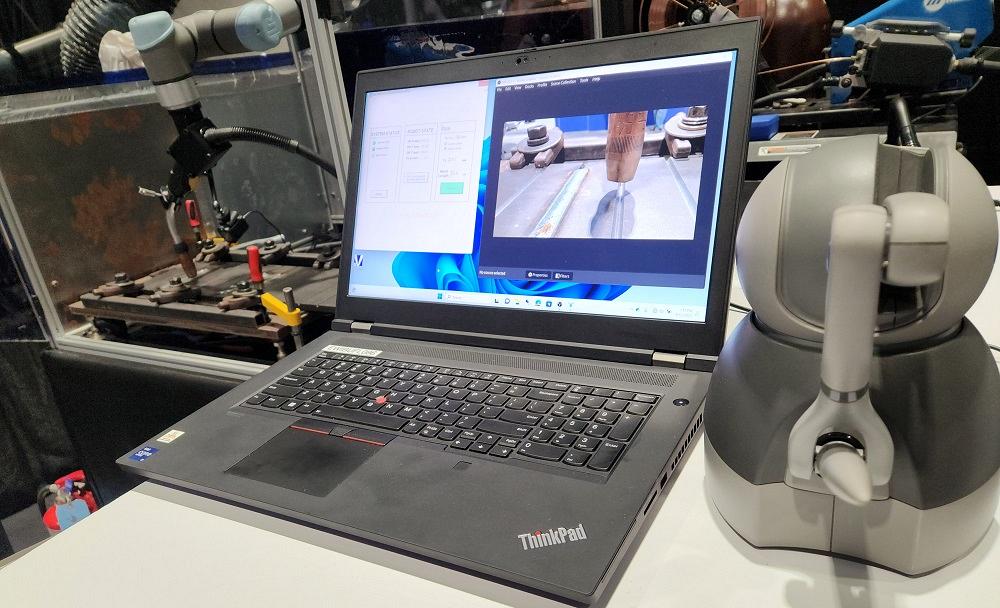
At EWI’s booth showing the potential of tele-welding, a joystick (right) gives haptic feedback for those operating a welding cobot (far left) at a distance.
This year’s Chicago FABTECH was the busiest in years. Crowds resembled those seen before COVID-19 made headlines and the world changed. And for good reason. The official attendance number came in at 40,505—a 67% increase from the 2021 show. FABTECH, it’s safe to say, is back. The industry stands at a kind of technological inflection point. Fundamentals of precision sheet metal and plate fabrication haven’t changed, but just about everything else has. Some worry about all this change; others couldn’t be more excited.
Those who worry think back to a time when jobs seemed secure and people worked for one corporation their entire lives—a common theme that underlies the rise in labor unions and the current labor strikes. They also might see technological innovation as a way for those in charge to get their way and grab more of the pie for themselves. Those excited about the future (and this includes yours truly) sometimes wish folks would open their eyes to all the possibilities—and many were on display Sept. 11-14 at McCormick Place. This year’s FABTECH showcased the potential of ultrahigh-powered laser cutting, technology that could change the nature of the plate fabrication market.
This also was the year of the cobot, with an unprecedented number showcasing various automation possibilities: wire welding, plasma cutting, painting, grinding. Although all those cobots at the show don’t directly equate to market share or rates of technology adoption, they do reveal just how important collaboration has become between all industry stakeholders. In truth, it’s the only way fabricators will make the ideals behind Industry 4.0 a reality.
All that said, if someone doesn’t know how to bend a flange, wield a welding gun, or program or operate a laser cutting machine, a fabricator is in trouble no matter what. New technology drives the industry forward, yet peoples’ lack of knowledge and experience holds the industry back. At a bending event at FABTECH attended by about two dozen people, the host asked how many operators had more than two years of experience in front of the press brake. No one raised their hand.
One technology at FABTECH in particular illustrated how the skills landscape could change in the coming years: a tele-welding and -grinding setup on display at EWI’s booth.
“This was developed initially as a research project for a national shipbuilding project,” said James Logan McNeil, EWI project engineer. “Only certain welders are qualified to do certain things. And in certain situations, you want to remove the operator from the location but still have operator input into that process.”
The technology allows an experienced welder or grinder to wield a joystick that gives haptic feedback as a robot welds or grinds, often when it’s performing a dangerous or dirty task, while maintaining full control of the process, including feeds and speeds of the welding gun or angle and pressure of the grinder. It was developed for shipbuilding but could be used anywhere that relies on the experience and dexterity of skilled workers. It’s being presented as a technology that gets the most out of talented people, no matter where they happen to be.
You could look at it as the ultimate tool to teach someone how to do a manual task—or as an alternative for someone who is willing to learn how to operate a robot but doesn’t necessarily want to spend all day with a right-angle grinder. It could be a tool that prevents good people from staying the course and climbing the ranks.
As an industry reporter, I talk to so many people who entered the industry on a serendipitous path. Some of a fabricator’s best (and best-paid) people didn’t have to accumulate years of education and the debt that goes with that. In this sense, metal fabrication epitomizes meritocracy. If you work hard and embrace change, you can go far.
General media outlets usually focus on the underpaid and overworked, and I’ve seen plenty of that. There are good and bad companies out there, and the fab industry is no exception. But I’ve also seen so many who’ve made a good career in a manufacturing sector that’s hungry for curious people.
Change can be uncomfortable and sometimes outright unfair—hence the news of strikes, the broader rise of unionization, and general unhappiness of so many workers. Some make too much money; others don’t make enough. But at least for me, it’s far more exciting and productive to stay curious, question everything, and assume what’s true today won’t necessarily be true tomorrow.
subscribe now
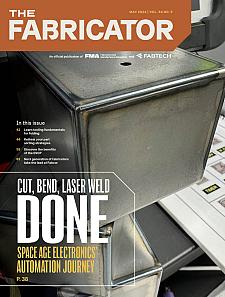
The Fabricator is North America's leading magazine for the metal forming and fabricating industry. The magazine delivers the news, technical articles, and case histories that enable fabricators to do their jobs more efficiently. The Fabricator has served the industry since 1970.
start your free subscriptionAbout the Author
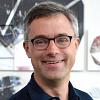
Tim Heston
2135 Point Blvd
Elgin, IL 60123
815-381-1314
Tim Heston, The Fabricator's senior editor, has covered the metal fabrication industry since 1998, starting his career at the American Welding Society's Welding Journal. Since then he has covered the full range of metal fabrication processes, from stamping, bending, and cutting to grinding and polishing. He joined The Fabricator's staff in October 2007.
Related Companies
- Stay connected from anywhere
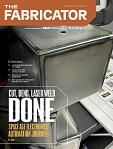
Easily access valuable industry resources now with full access to the digital edition of The Fabricator.
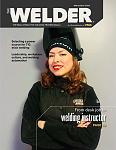
Easily access valuable industry resources now with full access to the digital edition of The Welder.
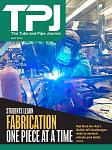
Easily access valuable industry resources now with full access to the digital edition of The Tube and Pipe Journal.
- Podcasting
- Podcast:
- The Fabricator Podcast
- Published:
- 04/16/2024
- Running Time:
- 63:29
In this episode of The Fabricator Podcast, Caleb Chamberlain, co-founder and CEO of OSH Cut, discusses his company’s...
- Trending Articles
Tips for creating sheet metal tubes with perforations
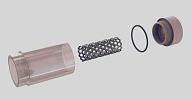
JM Steel triples capacity for solar energy projects at Pennsylvania facility
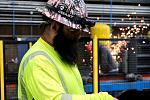
Are two heads better than one in fiber laser cutting?
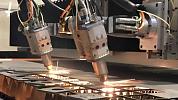
Supporting the metal fabricating industry through FMA
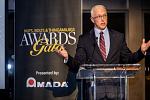
Omco Solar opens second Alabama manufacturing facility
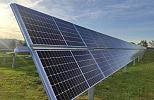
- Industry Events
16th Annual Safety Conference
- April 30 - May 1, 2024
- Elgin,
Pipe and Tube Conference
- May 21 - 22, 2024
- Omaha, NE
World-Class Roll Forming Workshop
- June 5 - 6, 2024
- Louisville, KY
Advanced Laser Application Workshop
- June 25 - 27, 2024
- Novi, MI