Senior Editor
- FMA
- The Fabricator
- FABTECH
- Canadian Metalworking
Categories
- Additive Manufacturing
- Aluminum Welding
- Arc Welding
- Assembly and Joining
- Automation and Robotics
- Bending and Forming
- Consumables
- Cutting and Weld Prep
- Electric Vehicles
- En Español
- Finishing
- Hydroforming
- Laser Cutting
- Laser Welding
- Machining
- Manufacturing Software
- Materials Handling
- Metals/Materials
- Oxyfuel Cutting
- Plasma Cutting
- Power Tools
- Punching and Other Holemaking
- Roll Forming
- Safety
- Sawing
- Shearing
- Shop Management
- Testing and Measuring
- Tube and Pipe Fabrication
- Tube and Pipe Production
- Waterjet Cutting
Industry Directory
Webcasts
Podcasts
FAB 40
Advertise
Subscribe
Account Login
Search
How small batches simplify metal fabrication
- By Tim Heston
- September 14, 2015
Material handling carts are a thing of beauty in metal fabrication, and I saw plenty of them just before the Labor Day holiday. That’s when I spent a week in Belgium and Holland on a press tour organized by LVD.
We’ll be covering the trip in detail in a future issue of the magazine, but much of the tour focused on LVD’s ToolCell. It’s a press brake with automated tool change that, when combined with adaptive bending technology, effectively shortens changeovers to minutes. Automatic tool change in the press brake arena has been a hot topic of late, both in manual and robotic systems. When you’re forming, the ability to change between jobs quickly can do wonders to overall throughput.
Still, no matter how quickly a machine can change over from job to job, you run into trouble when you don’t have an efficient way to move blanks to the brake or a good method to identify the work in process. And what if there’s a revision change? All this becomes even more important when you have dozens or even hundreds of short-run jobs on the floor at any one time.
A shop could install fancy monitors to show what jobs or where, or opt for a paperless system in which operators scan move tickets that bring up the latest and greatest information for a job.
But one job shop supervisor in Holland gave me some perspective. I saw that his shop had a single paper attached to each job, with a simple print drawing. A 3-D drawing of the part, and all the related information, was downloaded to the touch-screen machine controller, so the brake operator had no shortage of information.
Regardless, the supervisor told me that, when the overall manufacturing cycle time occurs in a matter of hours, the operator really doesn’t need that much information. He told me that fancy monitors and other shop information systems were just a Band-Aid that covered up a larger problem: weeks-long lead times and all the WIP they create.
The shop had automated a lot of engineering with custom software on the front end. It employed logic-based systems that automated the quoting for jobs that required cutting and forming. So jobs that used to take a dozen days to make their way through the front office now took less than an hour, if that.
If a job is processed in mere hours, from the initial order to the final shipment, there’s not much chance for the customer to send a part revision. There’s also very little WIP on the floor, so it doesn’t take much to sort jobs. This simplifies everything, and when things are simple, you don’t need comprehensive information management systems on the floor. For those in the job shop world, this makes life a lot simpler.
The greatest sorting challenge occurs after the laser or punch. But when you only have a single sheet to sort, it doesn’t take long for someone to organize the cut blanks on carts and send it on to the brake. When parts are on carts, they’re moving. And when parts are moving, they’re getting closer to shipping. When parts ship, the shop gets paid. That’s why the simple, small-batch material handling cart is a thing of beauty.
subscribe now
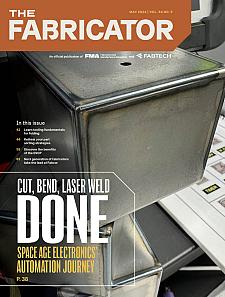
The Fabricator is North America's leading magazine for the metal forming and fabricating industry. The magazine delivers the news, technical articles, and case histories that enable fabricators to do their jobs more efficiently. The Fabricator has served the industry since 1970.
start your free subscriptionAbout the Author
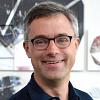
Tim Heston
2135 Point Blvd
Elgin, IL 60123
815-381-1314
Tim Heston, The Fabricator's senior editor, has covered the metal fabrication industry since 1998, starting his career at the American Welding Society's Welding Journal. Since then he has covered the full range of metal fabrication processes, from stamping, bending, and cutting to grinding and polishing. He joined The Fabricator's staff in October 2007.
Related Companies
- Stay connected from anywhere
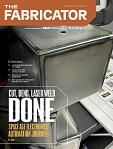
Easily access valuable industry resources now with full access to the digital edition of The Fabricator.
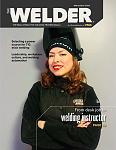
Easily access valuable industry resources now with full access to the digital edition of The Welder.
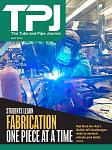
Easily access valuable industry resources now with full access to the digital edition of The Tube and Pipe Journal.
- Podcasting
- Podcast:
- The Fabricator Podcast
- Published:
- 04/16/2024
- Running Time:
- 63:29
In this episode of The Fabricator Podcast, Caleb Chamberlain, co-founder and CEO of OSH Cut, discusses his company’s...
- Trending Articles
Tips for creating sheet metal tubes with perforations
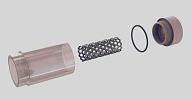
JM Steel triples capacity for solar energy projects at Pennsylvania facility
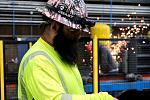
Are two heads better than one in fiber laser cutting?
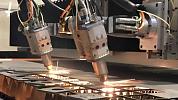
Supporting the metal fabricating industry through FMA
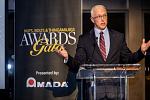
Omco Solar opens second Alabama manufacturing facility
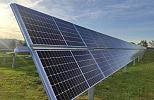
- Industry Events
16th Annual Safety Conference
- April 30 - May 1, 2024
- Elgin,
Pipe and Tube Conference
- May 21 - 22, 2024
- Omaha, NE
World-Class Roll Forming Workshop
- June 5 - 6, 2024
- Louisville, KY
Advanced Laser Application Workshop
- June 25 - 27, 2024
- Novi, MI