Senior Editor
- FMA
- The Fabricator
- FABTECH
- Canadian Metalworking
Categories
- Additive Manufacturing
- Aluminum Welding
- Arc Welding
- Assembly and Joining
- Automation and Robotics
- Bending and Forming
- Consumables
- Cutting and Weld Prep
- Electric Vehicles
- En Español
- Finishing
- Hydroforming
- Laser Cutting
- Laser Welding
- Machining
- Manufacturing Software
- Materials Handling
- Metals/Materials
- Oxyfuel Cutting
- Plasma Cutting
- Power Tools
- Punching and Other Holemaking
- Roll Forming
- Safety
- Sawing
- Shearing
- Shop Management
- Testing and Measuring
- Tube and Pipe Fabrication
- Tube and Pipe Production
- Waterjet Cutting
Industry Directory
Webcasts
Podcasts
FAB 40
Advertise
Subscribe
Account Login
Search
Five years of rapid change at Industrial Sheet Metal
A tour of a sheet metal shop undergoing a transformation towards advanced manufacturing
- By Tim Heston
- March 1, 2022
ISM hosted a tour that opened the Fabricators & Manufacturers Association Annual Meeting, held March 1-3 in Miami.
Five years ago the people at Industrial Sheet Metal, Hialeah, Fla., were immersed in old-school sheet metal fab, wielding metal snips and performing layout by hand. The job shop served local weld shops as well as the metal roofing space, and it did so with an old shear, a metal folder, and some other basic machines.
Today the 20-employee shop has utterly transformed. It has modern TRUMPF fiber lasers and press brakes, even a handheld IPG fiber laser welder. It also has a team of engineers versed in SolidWorks, and not all of them work locally—a feat that rose many eyebrows this morning, when the company hosted a tour that opened this week’s Fabricators & Manufacturers Association (FMA) Annual Meeting, being held in Miami March 1-3. The tour group gathered around a sleek room near the front of the shop. On one side, two designers worked on wide-screen monitors that were adjacent to a bank of screens on the wall, each showing a remote engineer’s computer screen in action.
Only about 20% of ISM’s customer’s have a 3-D CAD file. Most come with paper drawings, sometimes with just an idea in their head—hence the need for in-house engineering. But those remote engineers do more than just draw in SolidWorks. They also work in offline bend simulation software. During this morning’s visit, I witnessed one engineer tweak a backgauge position for forming a complex part, complete with contoured edges and multiple bends at unusual angles—no simple 90-degree bend to be found. Those screens help remote employees collaborate with on-site personnel.
Soon after I saw a similarly complex part being formed on the company’s press brake. It’s the kind of part you look at and as, OK, how do I gauge this thing? The backgauge fingers looked far too simple to take the complex contours. Would this thing need a side gauge? Not at all, as it turned out. The operator bent the odd flanges one after the other with little hesitation, and with each bend a new, secure gauging point revealed itself. It was a sight to see for a sheet metal geek like me.
The shop’s transformation isn’t over. In recent months the shop hired a software engineer to develop a custom enterprise resource planning (ERP) system tailored for the company’s needs, reducing the shop’s reliance on paper travelers and other communication inefficiencies.
That’s a high aim for any shop, but the company’s rapid five-year transformation makes that software initiative even more impressive. ISM’s Russell Murton, our tour guide, told us that the fact that so many at the company have roots in old-school layout, and that the shop’s most experienced people know the intricacies of sheet metal design and fabrication, made the transition to modern machines and software all the more powerful.
”We wouldn’t have it any other way,” Murton said, adding that the machines make those who know sheet metal even more effective and efficient.
ISM’s Diego Idarraga added that such knowledge is paramount for shop employees and, especially, those working remotely. Those remote engineers don’t visit the shop floor, but they do know sheet metal. In fact, all of them have worked in sheet metal for years.
Both in their 30s, Murton and Idarraga appreciate the need to know how things are made, how the tool shapes sheet metal. Most important, they both appreciate the time they spent in their 20s, learning the old-school way, observing how sheet metal forms, folding and unfolding blanks in their heads. And they recognize the importance of legacy processes. The shop performs hand laser welding—a novel process if ever there was one—in an area directly adjacent to a soldering station, one of the oldest metalworking process out there. It’s old, but it’s still the best way to get the job done.
Like many family fab shops, ISM is undergoing a generational transition, and that new generation is making its mark in a big way. Considering the changes the shop made just in the past five years, just imagine what the next five years will hold.
subscribe now
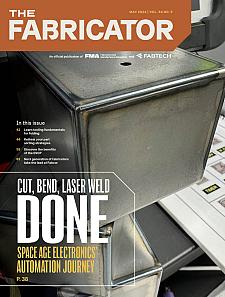
The Fabricator is North America's leading magazine for the metal forming and fabricating industry. The magazine delivers the news, technical articles, and case histories that enable fabricators to do their jobs more efficiently. The Fabricator has served the industry since 1970.
start your free subscriptionAbout the Author
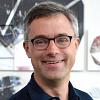
Tim Heston
2135 Point Blvd
Elgin, IL 60123
815-381-1314
Tim Heston, The Fabricator's senior editor, has covered the metal fabrication industry since 1998, starting his career at the American Welding Society's Welding Journal. Since then he has covered the full range of metal fabrication processes, from stamping, bending, and cutting to grinding and polishing. He joined The Fabricator's staff in October 2007.
Related Companies
- Stay connected from anywhere
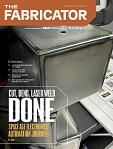
Easily access valuable industry resources now with full access to the digital edition of The Fabricator.
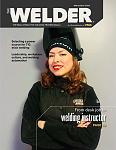
Easily access valuable industry resources now with full access to the digital edition of The Welder.
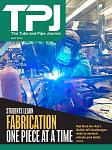
Easily access valuable industry resources now with full access to the digital edition of The Tube and Pipe Journal.
- Podcasting
- Podcast:
- The Fabricator Podcast
- Published:
- 04/16/2024
- Running Time:
- 63:29
In this episode of The Fabricator Podcast, Caleb Chamberlain, co-founder and CEO of OSH Cut, discusses his company’s...
- Trending Articles
Tips for creating sheet metal tubes with perforations
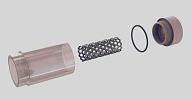
JM Steel triples capacity for solar energy projects at Pennsylvania facility
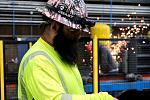
Are two heads better than one in fiber laser cutting?
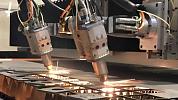
Supporting the metal fabricating industry through FMA
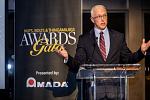
Omco Solar opens second Alabama manufacturing facility
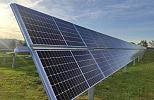
- Industry Events
16th Annual Safety Conference
- April 30 - May 1, 2024
- Elgin,
Pipe and Tube Conference
- May 21 - 22, 2024
- Omaha, NE
World-Class Roll Forming Workshop
- June 5 - 6, 2024
- Louisville, KY
Advanced Laser Application Workshop
- June 25 - 27, 2024
- Novi, MI