- FMA
- The Fabricator
- FABTECH
- Canadian Metalworking
Categories
- Additive Manufacturing
- Aluminum Welding
- Arc Welding
- Assembly and Joining
- Automation and Robotics
- Bending and Forming
- Consumables
- Cutting and Weld Prep
- Electric Vehicles
- En Español
- Finishing
- Hydroforming
- Laser Cutting
- Laser Welding
- Machining
- Manufacturing Software
- Materials Handling
- Metals/Materials
- Oxyfuel Cutting
- Plasma Cutting
- Power Tools
- Punching and Other Holemaking
- Roll Forming
- Safety
- Sawing
- Shearing
- Shop Management
- Testing and Measuring
- Tube and Pipe Fabrication
- Tube and Pipe Production
- Waterjet Cutting
Industry Directory
Webcasts
Podcasts
FAB 40
Advertise
Subscribe
Account Login
Search
Top 5 in 365—Articles about finishing
- By Vicki Bell
- August 15, 2018
The last installment of “Top 5 in 365” showcased the five most-popular articles on thefabricator.com published within the last year about cutting and weld prep. Previous installments have focused on bending and folding, laser cutting, arc welding, assembly and joining, automation and robotics, and consumables. This post is about the finishing category on the website. How do you achieve the desired and often specified finish? Does it require contracting the process out or adding to your existing processes and equipment? Finishing comes with many important considerations. Here are the top five most-read articles in the past year that discuss this important aspect of most fabricating jobs.
5. A powder coating primer for metal fabricators
It’s a common story. A fabricator analyzes how much time parts spend in each process. Laser cutting, bending, welding—these and other in-house departments usually can be measured in minutes and hours. But send parts to outside subcontractors, and the time is usually measured in days, sometimes weeks. No wonder so many fabricators choose to bring many services in-house, including powder coating.
When a fab shop launches a powder coating department, equipment is important, but most important of all is process knowledge. A coating operation can’t be effective without it.
4. Rethinking the coating and pretreatment relationship
While other coating and pretreatment suppliers look for new compounds that can replicate the performance of old compounds now outlawed because of environmental regulations, others saw an opportunity to pursue a new approach to parts cleaning and painting. That’s how Rugged Coatings brought Intuitive Coatings and CleanWirx together.
3. Automating powder coat system, adding IR curing accelerate productivity
Matthews Industries offers fabricating, welding, coating, and assembly services in the manufacture of compressed air systems, food service equipment, HVAC/refrigeration components, cabinets and electrical enclosures, industrial valves, and consumer products. Company leadership realized efficiencies in its finishing line and eliminated bottlenecks by installing automated powder coating application and an electric infrared preheating system, thereby doubling line speed and output.
2. Engineering expertise drives growth at Royal Welding
Good engineering practice drives everything at Royal Welding & Fabricating, a custom fabricator in California. It can be seen in the design of some of its tanks and vessels, as well as its manufacturing processes on the floor—including grinding and polishing.
1. 4 reasons automated deburring might be the right choice for your shop
With the extensive variety of deburring systems available, it can be exceptionally challenging to determine which one will work best for your specific production requirements. Each part profile, finish, thickness, and type of material can introduce unique challenges, expenses, and constraints to your cutting and smoothing efforts, which complicates the decision even further.
In many cases, professional metalworkers manually deburr parts while their machine works away at the next plate. However, regardless of how skilled you are at manual deburring, it’s impossible to match the speed and consistency of automated deburring systems. In fact, hand grinding could be hampering the overall productivity and profitability of your organization.
Next up? Manufacturing software.
subscribe now
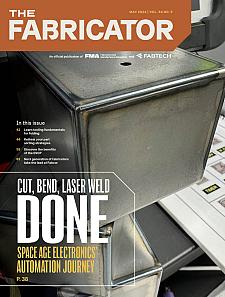
The Fabricator is North America's leading magazine for the metal forming and fabricating industry. The magazine delivers the news, technical articles, and case histories that enable fabricators to do their jobs more efficiently. The Fabricator has served the industry since 1970.
start your free subscriptionAbout the Author
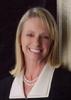
Vicki Bell
2135 Point Blvd
Elgin, IL 60123
815-227-8209
- Stay connected from anywhere
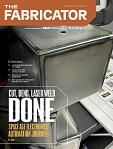
Easily access valuable industry resources now with full access to the digital edition of The Fabricator.
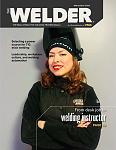
Easily access valuable industry resources now with full access to the digital edition of The Welder.
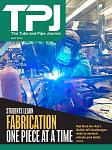
Easily access valuable industry resources now with full access to the digital edition of The Tube and Pipe Journal.
- Podcasting
- Podcast:
- The Fabricator Podcast
- Published:
- 04/16/2024
- Running Time:
- 63:29
In this episode of The Fabricator Podcast, Caleb Chamberlain, co-founder and CEO of OSH Cut, discusses his company’s...
- Trending Articles
Tips for creating sheet metal tubes with perforations
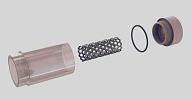
JM Steel triples capacity for solar energy projects at Pennsylvania facility
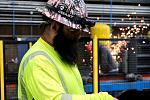
Are two heads better than one in fiber laser cutting?
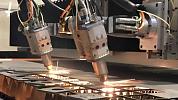
Supporting the metal fabricating industry through FMA
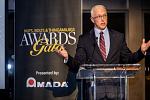
Omco Solar opens second Alabama manufacturing facility
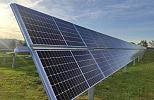
- Industry Events
16th Annual Safety Conference
- April 30 - May 1, 2024
- Elgin,
Pipe and Tube Conference
- May 21 - 22, 2024
- Omaha, NE
World-Class Roll Forming Workshop
- June 5 - 6, 2024
- Louisville, KY
Advanced Laser Application Workshop
- June 25 - 27, 2024
- Novi, MI