Editor-in-Chief
- FMA
- The Fabricator
- FABTECH
- Canadian Metalworking
Categories
- Additive Manufacturing
- Aluminum Welding
- Arc Welding
- Assembly and Joining
- Automation and Robotics
- Bending and Forming
- Consumables
- Cutting and Weld Prep
- Electric Vehicles
- En Español
- Finishing
- Hydroforming
- Laser Cutting
- Laser Welding
- Machining
- Manufacturing Software
- Materials Handling
- Metals/Materials
- Oxyfuel Cutting
- Plasma Cutting
- Power Tools
- Punching and Other Holemaking
- Roll Forming
- Safety
- Sawing
- Shearing
- Shop Management
- Testing and Measuring
- Tube and Pipe Fabrication
- Tube and Pipe Production
- Waterjet Cutting
Industry Directory
Webcasts
Podcasts
FAB 40
Advertise
Subscribe
Account Login
Search
Getting the most from your material handling efforts
When’s the last time your shop thought about how parts and assemblies are moved?
- By Dan Davis
- February 24, 2021
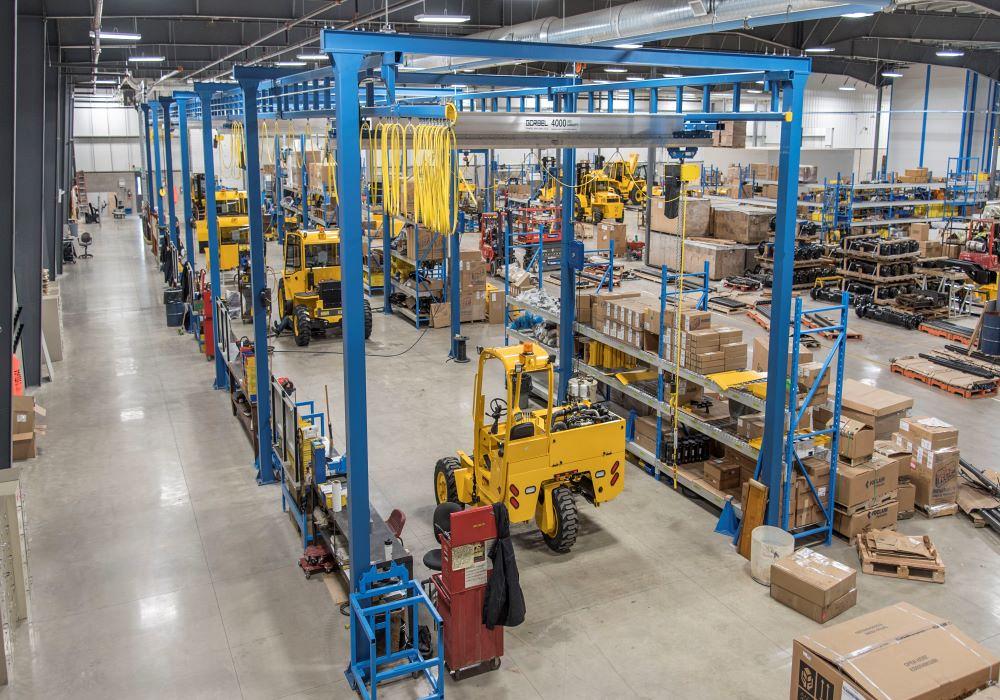
Enclosed track workstation cranes can help manufacturers improve productivity on the shop floor. Images: Gorbel Inc.
U.S. manufacturing is at an interesting point in early 2021. Although some sectors of the economy are still crawling out of a deep hole as a result of the pandemic, domestic manufacturers are still in expansion mode, according to the Feb. 1 report from the Institute for Supply Management. The PMI registered 58.7, which marked the eighth month in the row of economic expansion. (Anything over 50 indicates expansion, and anything below that mark is economic contraction.)
This puts metal fabricators in the awkward position of trying to keep up with current production orders while simultaneously preparing for future opportunities that come with a rebounding economy. Throw in the challenge of finding skilled labor interested in working in a manufacturing environment, and manufacturers have an uphill climb ahead of them.
These are the moments when owners and managers of metal fabricating companies need to ask themselves what they can do to help their employees work more efficiently. The best way to get more productivity out of a workforce is to work smarter, not necessarily harder.
Material handling is one area that a shop should look at, particularly when it comes to workstation material handling. Gorbel Inc., a manufacturer of cranes and material handling technology, suggests in a new e-book that implementation of enclosed track workstation cranes can make a huge difference in a fabricator’s productivity.
For example, these types of cranes, which can accommodate loads from 150 to 4,000 lbs., are much easier for workers to use. This is especially important in manufacturing as the workforce has a large share of people 50 and older in its ranks. The enclosed track design of this workstation crane keeps the tracks clear of dirt and debris, which reduces friction of the trolley’s running surface and makes the crane easier to move when compared to traditional heavy-duty cranes.
Also, this type of crane has a high strength-to-weight ratio that makes it easy to maneuver. To validate these points, Gorbel refers to a study by the Rochester Institute of Technology that found fewer than one in 10 men are able to safely handle a 4,000-lb. load using a manual I-beam crane. An enclosed track workstation model was found to be safely used by 99% of men.
The cranes also can be installed quickly and cost-effectively, according to Gorbel officials. Most facilities can use their existing foundations if they have standard reinforced concrete flooring. The crane’s footprint is small, which contributes to the fast installation.
To learn more about enclosed track workstation cranes, download the new Gorbel e-book.
Gorbel officials claim that these types of enclosed track systems can boost productivity by 28% or more when compared to the use of heavy-duty I-beam cranes. It’s something to explore as manufacturing comes to grips with an economy that is going to heat up in the second half of 2021.
subscribe now
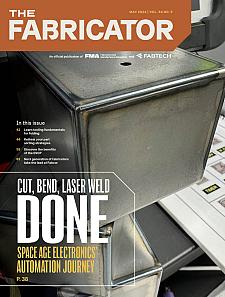
The Fabricator is North America's leading magazine for the metal forming and fabricating industry. The magazine delivers the news, technical articles, and case histories that enable fabricators to do their jobs more efficiently. The Fabricator has served the industry since 1970.
start your free subscriptionAbout the Author
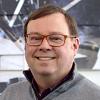
Dan Davis
2135 Point Blvd.
Elgin, IL 60123
815-227-8281
Dan Davis is editor-in-chief of The Fabricator, the industry's most widely circulated metal fabricating magazine, and its sister publications, The Tube & Pipe Journal and The Welder. He has been with the publications since April 2002.
Related Companies
- Stay connected from anywhere
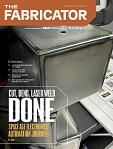
Easily access valuable industry resources now with full access to the digital edition of The Fabricator.
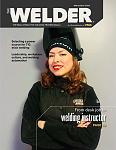
Easily access valuable industry resources now with full access to the digital edition of The Welder.
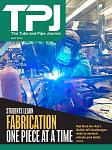
Easily access valuable industry resources now with full access to the digital edition of The Tube and Pipe Journal.
- Podcasting
- Podcast:
- The Fabricator Podcast
- Published:
- 04/16/2024
- Running Time:
- 63:29
In this episode of The Fabricator Podcast, Caleb Chamberlain, co-founder and CEO of OSH Cut, discusses his company’s...
- Trending Articles
Tips for creating sheet metal tubes with perforations
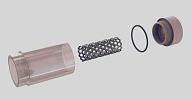
Supporting the metal fabricating industry through FMA
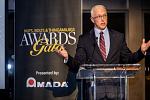
JM Steel triples capacity for solar energy projects at Pennsylvania facility
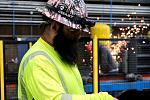
Are two heads better than one in fiber laser cutting?
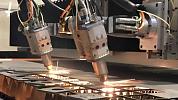
Fabricating favorite childhood memories
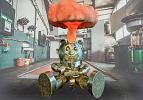
- Industry Events
16th Annual Safety Conference
- April 30 - May 1, 2024
- Elgin,
Pipe and Tube Conference
- May 21 - 22, 2024
- Omaha, NE
World-Class Roll Forming Workshop
- June 5 - 6, 2024
- Louisville, KY
Advanced Laser Application Workshop
- June 25 - 27, 2024
- Novi, MI