Senior Editor
- FMA
- The Fabricator
- FABTECH
- Canadian Metalworking
Categories
- Additive Manufacturing
- Aluminum Welding
- Arc Welding
- Assembly and Joining
- Automation and Robotics
- Bending and Forming
- Consumables
- Cutting and Weld Prep
- Electric Vehicles
- En Español
- Finishing
- Hydroforming
- Laser Cutting
- Laser Welding
- Machining
- Manufacturing Software
- Materials Handling
- Metals/Materials
- Oxyfuel Cutting
- Plasma Cutting
- Power Tools
- Punching and Other Holemaking
- Roll Forming
- Safety
- Sawing
- Shearing
- Shop Management
- Testing and Measuring
- Tube and Pipe Fabrication
- Tube and Pipe Production
- Waterjet Cutting
Industry Directory
Webcasts
Podcasts
FAB 40
Advertise
Subscribe
Account Login
Search
A metal blanking company with safety at its core
Safety culture runs deep at Millennium Steel of Texas
- By Tim Heston
- March 3, 2020
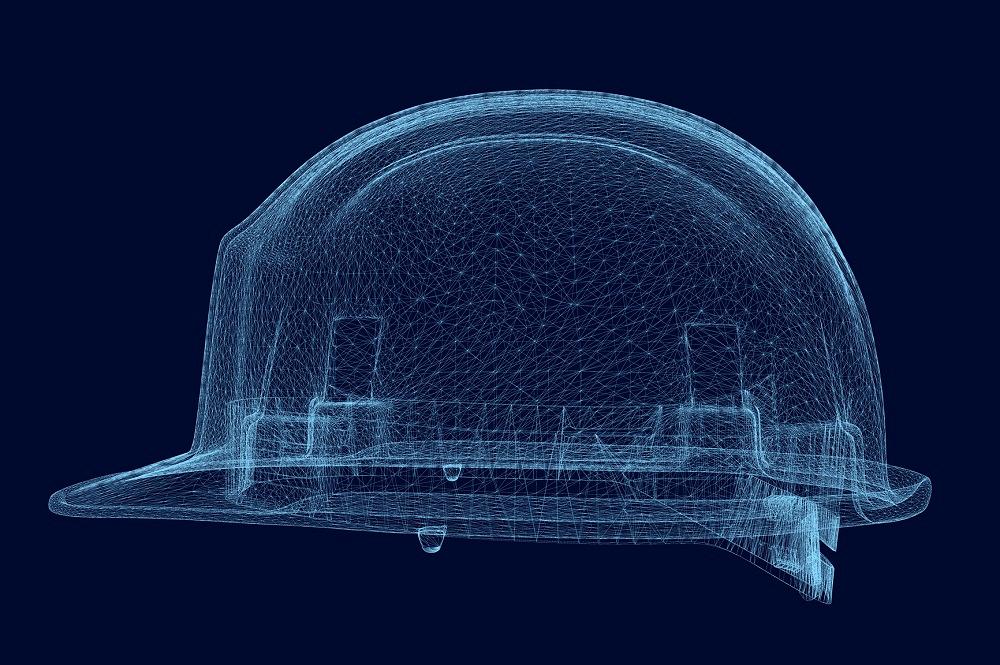
What could be more important for a metalworker than coming home, unscathed and unstrained, at the end of the day? That's front of mind for Millennium Steel in Texas. Getty Images
“Hello, my name is Mike, and my safety declaration is to stay safe for my family. Welcome to Millennium Steel.”
“Hello, my name is George, and my safety declaration is to lead through example.”
That’s just a sample of what I heard Tuesday morning during a tour of Millennium Steel of Texas, a blanking operation adjacent to the Toyota Tundra plant outside San Antonio, Texas, the locale for this year’s Fabricators & Manufacturers Association (FMA) Annual Meeting, and the tour Tuesday morning was a perfect kickoff, especially considering its focus on safety.
Every guide on the tour started with their name and their safety declaration before delving into the details about the work area. Business success matters, and so does quality, but safety towers above all else. The declarations help instill that safety culture, but they weren’t spoken vaguely or casually. They weren’t just following corporate policy. They really meant what they declared.
This probably had to do with the level of safety education workers receive. Down one side of the plant, adjacent to a marked walkway dubbed the “Green Mile,” are several so-called “safety dojos” set up to train workers on the risks of working in a coil handling and blanking facility—and how to make those risks as low as possible. They don’t just list proper safety procedures but instead actually show what can happen should someone make a hasty misjudgment. The “Green Mile” idiom might mean the march toward the inevitable, but in Millennium’s case, injuries aren’t inevitable, though risks are, which is why everyone works to minimize them as much as possible—hence the safety dojos.
For instance, one safety dojo showed a coil that looked tiny relative to the 22,000-pound coils in the adjacent inventory bay. But that seemingly tiny coil still was 800 lbs., quite enough to utterly crush an appendage, especially if tipped. The dojo setup, surrounded by the appropriate hard safeguards, simulated an inadvertent tipping, with the coil slamming down onto a slanted support with 4,000 lbs. of force. The aluminum can on that support was flattened beyond recognition. Employees watch that, learn best safety practices, and—perhaps most important, learn to take them to heart.
Modern manufacturing stands in stark contrast to the dark, dirty, dangerous plant floors of the past. And Millennium Steel is a prime example, with its clean floors, great lighting, and gleaming stamping presses. But you still can’t change physics. Metal is heavy and, if wielded with abandon, dangerous or even deadly. Millennium’s commitment to safety instills that engaged respect for the material, so employees come home at the end of the day unscathed and unstrained. Nothing is more important.
subscribe now
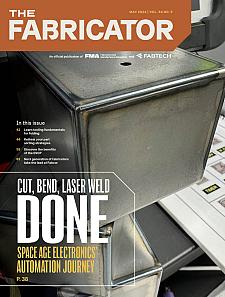
The Fabricator is North America's leading magazine for the metal forming and fabricating industry. The magazine delivers the news, technical articles, and case histories that enable fabricators to do their jobs more efficiently. The Fabricator has served the industry since 1970.
start your free subscriptionAbout the Author
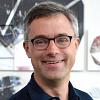
Tim Heston
2135 Point Blvd
Elgin, IL 60123
815-381-1314
Tim Heston, The Fabricator's senior editor, has covered the metal fabrication industry since 1998, starting his career at the American Welding Society's Welding Journal. Since then he has covered the full range of metal fabrication processes, from stamping, bending, and cutting to grinding and polishing. He joined The Fabricator's staff in October 2007.
- Stay connected from anywhere
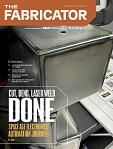
Easily access valuable industry resources now with full access to the digital edition of The Fabricator.
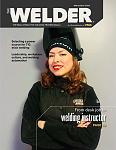
Easily access valuable industry resources now with full access to the digital edition of The Welder.
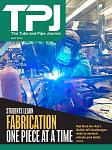
Easily access valuable industry resources now with full access to the digital edition of The Tube and Pipe Journal.
- Podcasting
- Podcast:
- The Fabricator Podcast
- Published:
- 04/16/2024
- Running Time:
- 63:29
In this episode of The Fabricator Podcast, Caleb Chamberlain, co-founder and CEO of OSH Cut, discusses his company’s...
- Trending Articles
Tips for creating sheet metal tubes with perforations
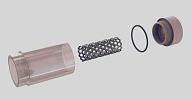
Supporting the metal fabricating industry through FMA
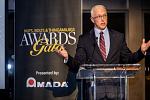
JM Steel triples capacity for solar energy projects at Pennsylvania facility
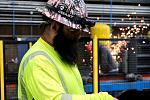
Are two heads better than one in fiber laser cutting?
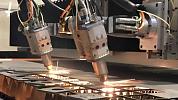
Fabricating favorite childhood memories
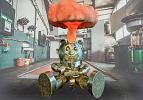
- Industry Events
16th Annual Safety Conference
- April 30 - May 1, 2024
- Elgin,
Pipe and Tube Conference
- May 21 - 22, 2024
- Omaha, NE
World-Class Roll Forming Workshop
- June 5 - 6, 2024
- Louisville, KY
Advanced Laser Application Workshop
- June 25 - 27, 2024
- Novi, MI